Ever get to an auction or flea market and stare lovingly, but in despair, at a hand plane that you’d love to own, but are going to pass on because it’s too rusty? There’s a solution for this problem. Electrolysis. It’s crazy cool, and easy to do. Here’s the overview; submerge the tool in a solution of baking soda and water, connect a battery charger, and let it sit overnight. By the next day the rust will have sloughed off.
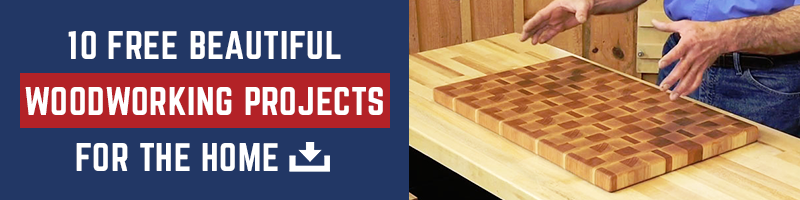
The beauty of using electrolysis for rust removal is that you’re not abrading the tool and removing metal. It’s better for the tool, especially if you’re concerned about its value, if you don’t hit it with sandpaper or a wire wheel. This, and the ease of doing it, makes electrolysis the perfect answer for restoring old tools. Electrolysis provides a very easy way to get rust out of a tool’s nooks and crannies.
I picked up the plane in this story cheap. You’ll see it go through the rust removal process here and, in future stories, get to follow along as it’s restored and tuned up.
Follow These Electrolysis Rust Removal Steps
Here’s a Bailey #4 hand plane I picked up for $25. Last patent date on the body is April 1910. It’s sound, but has a lot of surface rust on it, and is unusable in its current condition. I’ll remove all the parts from the body and use electrolysis to remove the rust.
Gather your electrolysis supplies together –
An electrolysis vat that is non-conductive. A plastic five-gallon bucket works well for most tools.
An anode (I’m using a coffee can)
Auto battery charger
Baking soda or washing powder
Measuring spoon
Scotch Brite pad and soft bristle brush
Wire leads
Rubber gloves
Prep. Wash the tool you’ll be treating. Make sure there isn’t any oil or wax on it that will prevent the electrolysis process from working. Give it a good bath with soap and water.
Make an anode. You need some kind of sacrificial steel for this. It’s best if the anode surrounds the tool so the electrolysis can happen from all sides. The anode will get eaten up by the electrolysis process, and will need to be replaced after being used a few times.
Connect one of the wire leads to the anode. Make sure you have a good, solid connection and that the lead is long enough to connect to the battery charger outside of the bucket.
Connect a lead to the tool. You’ve got to have a good connection or the process won’t work well. This can be challenging with a rusty tool. You may have to clean a small section of the tool with sandpaper to make certain you have contact.
Make up the electrolyte solution. You need enough water to completely submerge the tool. Add one tablespoon of baking soda or washing powder (either one will work) per gallon of water. Mix the solution to dissolve the powder.
Suspend the tool in the vat and check the set up. Try to arrange the anode so it surrounds the tool, but don’t let the tool and anode touch each other.
Start Removing Rust. Connect the clips from the battery charger to the leads on the tool and anode. Make sure you get this right. With the charger unplugged connect the positive to the anode and the negative to the tool. If you do this backwards your tool will become the sacrificial anode. Set the charger on a 2-amp charge and plug it in. Don’t let the connections from the charger touch the electrolyte solution.
Within minutes of plugging in the charger you should see bubbles rising from the tool. Allow the tool to “cook” for 15-20 hours.
Results. After some time the top of the vat will be covered with sludge. This is a good thing. The sludge is the rust coming off the tool.
Unplug and disconnect the charger and remove the tool from the solution. It won’t look like much now. It’ll need some cleaning.
Wearing rubber gloves, use a fine Scotch Brite pad to remove the sludge from the tool. It doesn’t take much elbow grease, just some wiping.
Use a soft bristle brush to get into the spots you can’t reach with the pad. Wipe the tool clean using a paper towel.
The result? A tool that’s clean of rust. If only I could make a vat large enough for my 1959 Farmall tractor to fit into…
The vat of electrolyte solution is pretty benign stuff, but will burn your lawn if you dump it all in one spot. It’s best to dilute the liquid before disposing of it.
Now that the rust is gone from the plane body it’s time to do some shopping!
Photos By Author
Related video: Removing Rust with Electrolysis
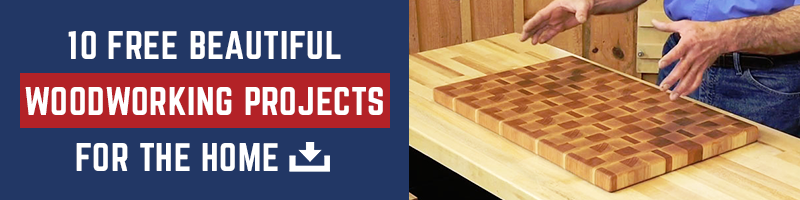
A very interesting article. I will try it
What would happen if I used 2 chargers? I’m trying this on a 48” mower deck and I’m not getting the response (bubbling action) from the washing soda solution (4 cups for 75 gallons) as I thought I would. my containment is made of 2x4, 3’x5’x8” with 6mil plastic sheeting inside for the tub. This is a large surface to cover. The amp draw looks like 3 amps on the charger
Do you suppose one could use a plastic colander to insulate the part from a close anode like you had?
Have you thought about putting the farmall in a swimming pool take the carb off don’t want water in that lol
Baking soda is incorrect. Washing soda can be used to increase electrical conductivity of water to speed electrolysis. It is not necessary, plain water can be used. But baking soda does not speed the process. Doubt me, look it up.
I've read all the discussions with great interest and am ready to try de-rusting an old Plane,but, I couldn't find anywhere how much Washing Soda to use per Gallon of water. What do you recommend? Thanks Russ
Use washing soda instead of baking soda so you do not release flammable/explosive hydrogen gas...
I have used this method a few times and while the rust I gone the tool is still dirty in some areas.
where is the next installment? I am trying to find a 9/32 left hand stud for a bench plane.
Thanks a lot for taking the time to do this; going through the process and recording/photographing/documenting it each step of the way. Saves us the trouble of doing the same. Keep up the awesome work! Cheers. :)