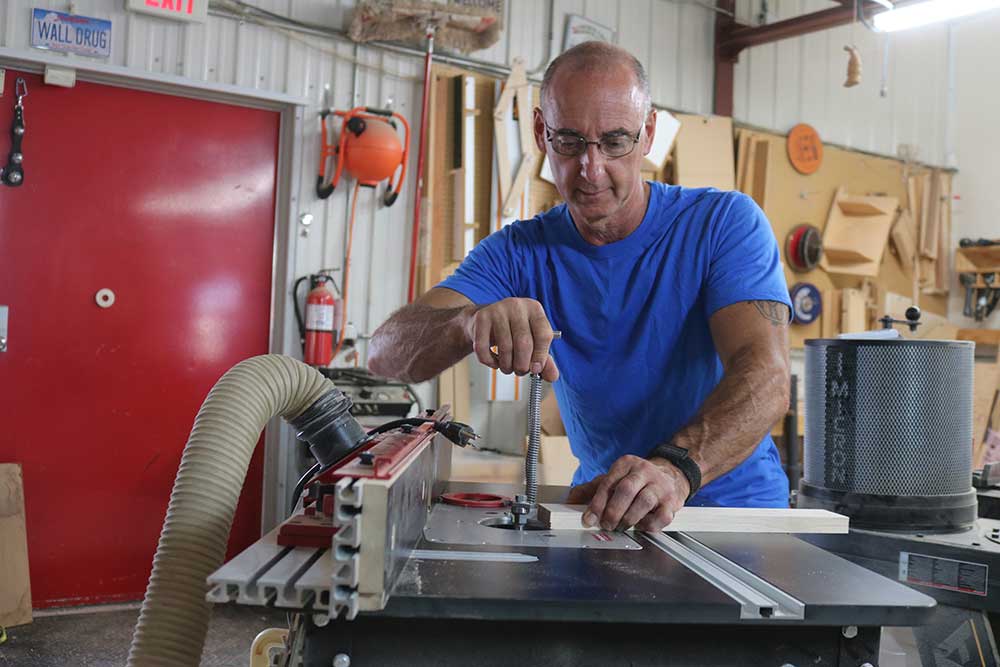
Choosing the Correct Screw Pocket Screw
George VondriskaWhen it comes to assembling woodworking projects seamlessly, few methods match the efficiency and durability of screw pockets. However, the success of your woodworking venture heavily relies on the precise selection of screw pocket screws. These screws aren’t mere components; they possess distinct characteristics that render them tailor-made.
Screw Material Matters
Selecting the right screw material is the cornerstone of a robust screw pocket assembly. Stainless steel screws, for instance, offer corrosion resistance, making them an excellent choice for outdoor projects. On the other hand, hardened steel screws provide exceptional strength, ideal for heavy-duty applications. Understanding the nuances of screw material empowers you to choose screws that stand the test of time.
Sizing Up the Situation: Length and Diameter
Screw pocket screws come in various lengths and diameters. Precision in sizing ensures a secure and reliable connection between the joined pieces. Opt for screws that provide ample engagement with the adjoining materials, promoting structural integrity. The versatility of screw pocket screws lies in their adaptability to projects of diverse scales and scopes.
Crucial Thread Considerations
Beyond screw selection, the thread type is a pivotal aspect of screw pocket assembly. Threads determine the grip, stability, and load-bearing capacity of the joint. Navigating the labyrinth of thread choices requires attention to detail and a comprehensive understanding of project requirements.
Fine Threads vs. Coarse Threads
Fine threads offer increased thread engagement, resulting in heightened grip and resistance to loosening. These threads excel in hardwood applications, where the material density demands a secure hold. Conversely, coarse threads are suitable for softer woods and plywood, providing quick and efficient penetration.
Tapping into Self-Tapping Threads
Self-tapping threads simplify the assembly process by creating their path as they’re driven into the material. This reduces the need for pre-drilling, enhancing efficiency. However, matching the thread type with the material is essential to ensure optimal results.
Other Screw Content
If you enjoyed this video tutorial on pickin the perect screw pocket screw,check out these other informative videos on screws. These videos offer a wealth of information and tips to help you improve your woodworking skills and achieve better project results.
Free Videos:
- Using Screw Pockets and Screw Pocket Jigs
- Understanding Different Types of Screws
- What’s the Deal with Screw Pocket Joinery?
- Easy Pocket Hole Joint Assembly
Member Videos:
Unlock Your Woodworking Potential!
Sign up for our newsletter for endless woodworking inspiration! Become a member today and gain access to a world of craftsmanship.
If you're using screw pockets for joinery in your shop, eventually you're gonna have to put those joints together. When you do so, I really recommend you stick with screw pocket screws as opposed to trying to substitute something else in. And there are some real distinct reasons for doing so. Here on the bench I've got some screws laid out. Some are screws you should use, some are screws you should not use.
Let's talk about the screw pocket screws first and their attributes. When we look at this silver screw, this is a screw pocket screw. It's got fine threads down here at the bottom. It's got a thread cutting tip. So part of the deal with that is that when we put screw pockets together, you don't drill into the mating piece, you just drive the screw.
So we wanna make sure we're using a screw with it's own thread cutter on the tip so that it can thread its way into that mating piece. Especially true in hardwoods. Now in the screw next to it, we've got another screw pocket screw. The only difference is that it's a different color. Additionally, it's a coarse thread screw.
It's still got that thread cutting tip at the bottom. So there'll be different occasions where we'll use coarse versus fine, talk about that in a second. What I don't want you to use are screws like this. These are called bugle head screws. The problem with these is that the bottoms of these heads look just like a splitting wedge.
So you can imagine that if we took this shape or the flathead shape, like we've got on this screw over here, still wedge shaped, when that hits the bottom of our screw pocket, it's gonna have a tendency to act like a wedge and split the material. So there's a big difference between the two heads. On the screw pocket screws we've got pan heads and on these more conventional woodworking screws, we've got bugle or flat heads, and those have that wedge shape to them and they're gonna cause the splitting. Now the deal with coarse thread, fine thread is manmade materials versus natural and hardwoods versus softwoods. So as a general rule of thumb, what you'll wanna do is stick with the fine thread screws anytime you're assembling anything in hardwood using screw pockets.
So that would be oak, walnut, maple, cherry, a lot of the North American woods, a lot of the tropical woods. If you're assembling manmade materials, so that would be plywood, particle board, MDF, or softwoods like pine, then you'd wanna go with the screw that's got the more coarse threads in it. Again, making sure that you stick with those pan head screw pocket specific screws. Now let's just do one more thing and look at the heads of the screws. Very commonly, these are square drive screws, and because of the angle at which we're driving them, remember those screw pockets go in at about 15 degrees, using a square drive on the square drive head screw just makes it a lot easier to run at an angle like that.
And make sure that the tip of the driver stays in contact, stays engaged, with the head of the screw. So the lesson out of all of this is there's a very good reason why screw pocket screws go with screw pocket joinery. The other thing to think about is make sure you're matching the length of the screw to the thickness of the wood that you're working with so that, by running the screw in at an angle, it doesn't accidentally come out the joining face. So make sure you're loading your shop up with screw pocket screws so that you're ready to assemble those screw pockets using the right tool for the right job.
Any idea why Kreg went to the zinc coated screws instead of the black oxide ones?
The other thing that's obvious with the "do not use" screws is that the threads go too far up the shank, inhibiting the drawing of the joint together. Just another reason not to use them. "Friends don't let friends use drywall screws in furniture."
George, I assembled a Hickory table top using pocket holes. One problem I ran into was the screw heads breaking off once they were driven into the adjoining board. I then used a lubricant and although less screw heads broke off , I was still breaking them. I tried an impact driver and also a cordless screwdriver with a clutch with the same results. My question is that with a wood as hard as hickory is there a way to pre drill the adjoining board at the proper angle to match the pocket hole? I plan on using some Ipe lumber on my next project using pocket holes but I'm afraid it may be even more difficult. I used Kreg brand fine thread screws in the hickory table project.. and advise is greatly appreciated and thanks for all the informative videos. Paul G