Some friends of mine have a cabin in the north woods with an out building for extra overnight guests to bunk up for the evening. It’s a great place to fall asleep on a moonlit night listening to the cooing owls and the foxes rustling through the brush. Both friends have a Swedish heritage so by committee we came up with a name for the bunkhouse and decided it needed a sign.
I got out a pen and paper, sketched several ideas, and came up with the sign you see here. I transferred my idea to a drawing program on the computer and enlarged it, and printed it out in two pages on a large printer. You can also print oversize images by going to Staples, uploading your design, and they’ll print it for you.
Another alternative, you can go a local print shop for help.
When you have your design printed, mount it to your wood blank with a spray adhesive. I bought a cedar deck board, cut it to shorter lengths, and then ripped the rounded edges off with my tablesaw. Once the edges were jointed I glued and clamped the boards to make up the panel.
To start routing, it’s a good idea to drill a 3/16” diameter hole the depth that you’re going to rout. This will let you drop your router into the hole without stressing the fragile bit. I’d do it this way even if I were using a plunge router. These 1/8” bits will only rout to a depth of 3/16” but I found that to be the perfect depth for this sign. Once you start routing, hold the router handles firmly and rest your forearms on the workpiece to stabilize the router. Move it slowly along the edge of your design. If you push it too fast, you’ll end up breaking the bit or burning the wood and overheating the bit.
Use the 1/8” cutter only to define the shapes, not to remove all the waste. It took me about 30 minutes and two bits to rout around all the lettering and the shapes in this design. Then install the 1/4″ bit to remove more material faster. Be sure to set the depth of the bit to exactly the same depth as the 1/8” cutter.
Routing with the 1/4″ bit goes much faster but you’ll still need to keep your forearms on the workpiece to stabilize the router to keep it from wandering during a climb cut. Go slow and steady to widen the area and work your way into the background of the design. I finished the routing using the ¼” straight bit, but you could also switch to a 3/4″ diameter bit if you have a lot of background to remove. Just remember to plan ahead and leave enough unrouted material to keep the router base stable. An upcut spiral router bit will work well for this project. Have a shop vacuum handy to clean up the debris from time to time.
When the routing is complete, go back and check for any spots you might have missed. We’ll be using a Dremel tool later to clean up any rough edges.
Removing the remaining paper is easy. Just soak the paper with acetone or lacquer thinner and peel it off with an old chisel or putty knife. Let the wood dry before the next step.
Cut the outer oval shape with your jigsaw or band saw. Clean up the edges of the lettering with a Dremel rotary tool outfitted with a small drum sander. You’ll also need to do a little hand sanding in tight areas.
After the initial painting, I decided to give the background a unifying texture with a burr bit (Dremel #134) in horizontal strokes. The effect left a more “hand-carved” appearance.
I gave the foreground of the design a second coat of enamel paint. I purchased small amounts of paint from a local hobby store.
To make the sign larger and give it a rustic feel, I glued up another panel made from 3/4″ thick cedar boards. I cut the edges to simulate a roughhewn look and then textured the cedar with a stiff wire wheel attached to the drill. The bristles wear away the early wood and leave a very weathered aged look to the surface. Once that was complete, I screwed the main sign to the backer from behind and then gave the whole sign two coats of spar varnish over the painted and unpainted parts. The spar varnish will seal it and protect it from moisture and UV rays.
You can rout keyholes on the back or just screw some picture hanging hardware on the backside to mount it to a wall or hang it with rope or chain from above.
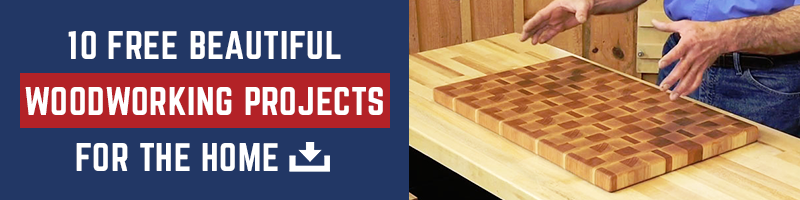
is cedar the only wood for making signs
thanks i needed this.
Neat little project.....Question, I'm a big (GF) General Finishes fan. In your opinion if you both the spar varnish and GF zexterior 450 which one would you recommend/use? And why? Thanks.....btw I ask because I live in Western NC its almost like a rain forest here particularly come summer.
That is awesome!
All you guys touting cnc..."o I could do it in 30min on my cnc" Great good for you...what a craftsman you are!!
very well done!!! inspiring to me and I feel confident to take on a sign job if it comes my way now. Thanks for also conveying the heart behind this project- what a gift!
Ya know the feeling you get when you make something with your hands..................well as you start up the ladder from hand tools, to power, to CNC I believed your satisfaction level decreases. Also the cost of a CNC is extreme if you are not going to make signs commercially...........................Just Saying
Without getting into the "CNC isn't real woodworking" argument, for those of you wanting to try this at home (without a CNC)... you can get a better initial outline cut with a 20 or 30-degree "pointed" bit vs. a straight cut, and you won't have to use two of them. With practice, you can easily make signs of this type that rival a CNC. I highly recommend joining the Facebook page "Hand Routed Carvings 4 Newbies" and checking out Dave and Eric Rhoten's YouTube channel and web page (makeawoodsign.com). Sure, a CNC can make a perfect sign, but there's nothing like knowing your own hands did this. Even better when someone asks you what kind of CNC you used! Carve on!!
I really like this project
Looking forward to lots of ideas with my membership