This is a two-part story. The focus is on drawers with mechanical slides. In this installment I will explain how a half-blind dovetail router jig works, calculating drawer parts sizes, and where to locate drawer bottoms for drawers with side-mount slides or undermount slides. Part two will be about using a dovetail router jig, and assembling dovetailed drawers.
For the longest time I resisted making dovetail drawers. I was under the misconception that making them took a lot of time and was a lot of work. Today I can’t imagine using any other type of drawer joinery. Dovetailed drawers look great, they scream out quality, and they are super strong. The dovetail joint is interlocking and well suited for drawers since it will not allow the drawer front to be pulled away from the sides. Routing half-blind dovetail joints is fairly easy if you know the tricks. I’ll show you what I have learned over my many years of making dovetail drawers.
Having a really good jig is essential. I use a Woodhaven 7600 jig (see Sources). It’s rock solid, simple to use, fast, and produces consistently perfect half-blind dovetails. It comes with a bearing piloted dovetail bit so there’s no need to use a template bushing with your router. This eliminates all concentricity issues related to a misaligned router base.
Drawer Construction Details. I make my drawer sides, fronts, and backs 1/2″ thick. The widths of my drawer sides, fronts, and backs are based on the dovetail tail spacing my jig cuts, and so I get a half dovetail pin at the top and bottom of the drawer front (see Half-blind dovetail anatomy below). I forego having a half-pin at the bottom if I’m using undermount drawer slides (see the photo Undermount drawer slides below). I make false “drawer faces” that I attach to my drawer fronts with screws, and I slide my drawer bottoms in from the back and screw them to the bottom edge of the drawer back.
Drawer faces are attached with screws. Drawers mounted with mechanical slides require false fronts to hide the slides. I call these false fronts “drawer faces”. Attach them to the drawer fronts with low profile washer head screws through 5/16″ dia. holes. The oversized holes allow for minor adjustments of the drawer face.
Half-blind dovetail anatomy. Admittedly, half-blind dovetail terminology is confusing. My solution for keeping the parts straight is to look for the board face with the “fish tails” at the ends. That’s the tailboard! Drawers with a half-pin at the top and bottom look best. The joint is called half-blind because when assembled the ends of the tails are hidden inside the joint, and only half of the joint is visible.
Equally spaced half-blind dovetails are routed in the jig with a single pass. A dovetail router bit is used to cut the joints. The tailboard (drawer side) and pinboard (drawer front or back) are clamped to the jig with their inside faces out. The jig’s stop is factory set to offset the parts the proper distance so both tails and sockets are cut with one pass of the router. When the joint is assembled the top and bottom edges of the boards are aligned flush to each other.
Adjusting the fit of a half-blind dovetail that’s cut with a single pass is accomplished by raising or lowering the dovetail bit in your router. You’ll need to make test cuts to get the fit correct. If the joint is loose, raise the bit. If the joint is tight, lower the bit.
Here are some wood species that make good drawers. All are closed-grain so they tear out less when routed, and they are all relatively inexpensive. I use white birch most often. It makes very nice drawers.
Optimal drawer heights are based on placing a half-pin at the top and bottom of the drawer front. My jig cuts dovetails spaced 7/8″ on center, so I make my drawers heights some multiple of 7/8″. I used the jig to cut dovetail sockets in a wide board, and I use that board as a guide to choose the drawer height that best fits my cabinet’s drawer opening.
Drawer backs are cut full width to start. Remember, I slide my drawer bottom in from the back after the drawer is assembled. The dovetails are cut on full widths drawer backs, and then the backs are cut to their finished width later when the drawer bottom grooves are cut in the sides and front. Doing this has many advantages, which become apparent when you start routing parts in the jig.
The drawer bottom grooves are cut so they are buried in the bottom tail and socket connection. This is done so the grooves are hidden from the outside when the drawers are assembled.
Undermount drawer slides require a 1/2″ space under the drawer. The way I deal with this is I add 3/16″ of height to these drawers, I modify the setup of my dovetail jig (next photo), and I forego having a half-pin at the bottom of the drawer.
Dovetailing drawers that use undermount slides requires both stops be repositioned outward 3/16″ more than their half-pin setting. The drawer parts are oriented bottom edges out and against the stops. Both sides of the jig are used (there will be more about this in Part 2). As you can see by the setup, the bottom pin is 3/16″ wider than the standard setup. That makes room so the bottom can be set 1/2″ up, and the bottom’s groove can still be hidden in the bottom tail/socket connection.
The overall length of a drawer should be equal to the length of the drawer slide you use. This is true for both side-mount and undermount slides.
The actual length of a drawer side is the drawer’s overall length minus 2 times the remaining wood at the bottom of the routed pinboard sockets.
The initial length of drawer fronts and backs is the actual length plus 1/32″. You’ll need to setup your dovetail jig so when the joint is assembled 1/64″ of pinboard endgrain protrudes past the tailboard. This overhang is sanded away after the drawers are assembled. That finishes the endgrain for a nice look.
Part 1 wrap-up. Now you know how the drawer parts need to be sized, and how the jig makes the dovetail joints. Next time I’ll show you the steps to cut the joints, and assemble and finish the drawers.
Photos By Author
Sources:
Related Video:Dovetail Buying Advice
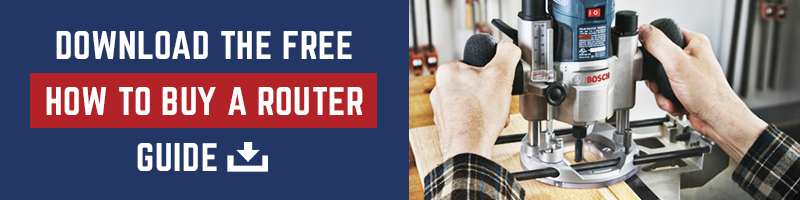
Thank you most interesting
"Adjusting the fit of a half-blind dovetail that’s cut with a single pass is accomplished by raising or lowering the dovetail bit in your router. You’ll need to make test cuts to get the fit correct. If the joint is loose, raise the bit. If the joint is tight, lower the bit." I thought George's instructional video was just the opposite: "too tight, too deep" and the solution is to raise the bit.