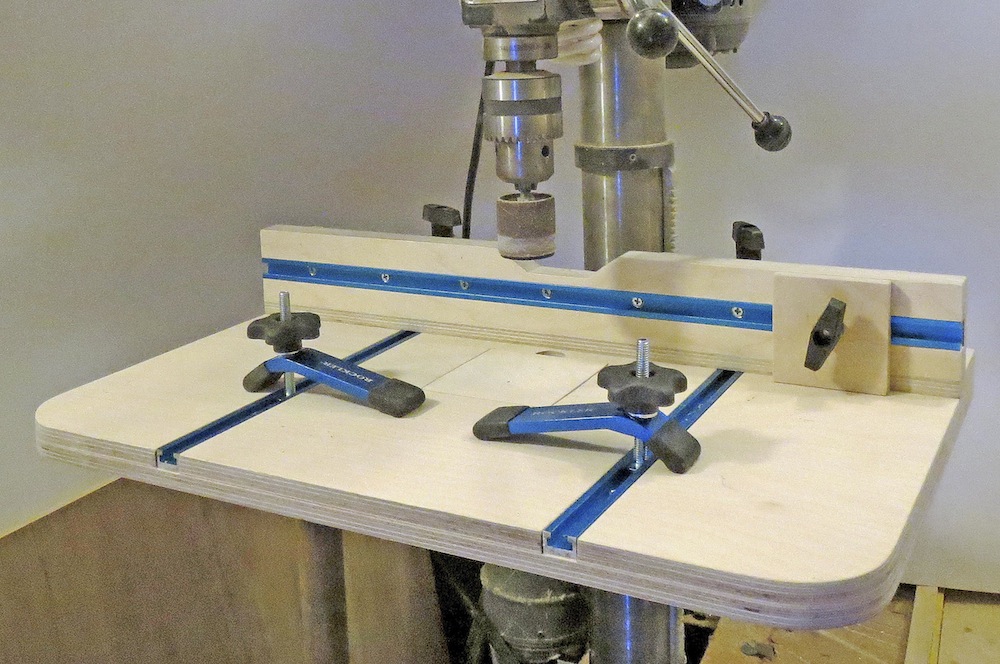
This is a shop fixture that’s worth getting started on immediately. Stationary drill presses are definitely not set up for DIY woodworking. The cast round table below the chuck isn’t woodworker friendly or even metalworking friendly. Once you build this fixture you’ll love its adjustable fence for drilling equally centered holes and the stop block that lets you make repeatable drilling operations in conjunction with the fence. The hold-downs are great for holding items still for delicate or precise hole drilling. Best yet, this jig is a project you can work on in your spare time over a couple days and complete for less than $50. The most expensive items are the T-track and the hold-downs. Follow the step-by-step drill press table plans for details to build your own.
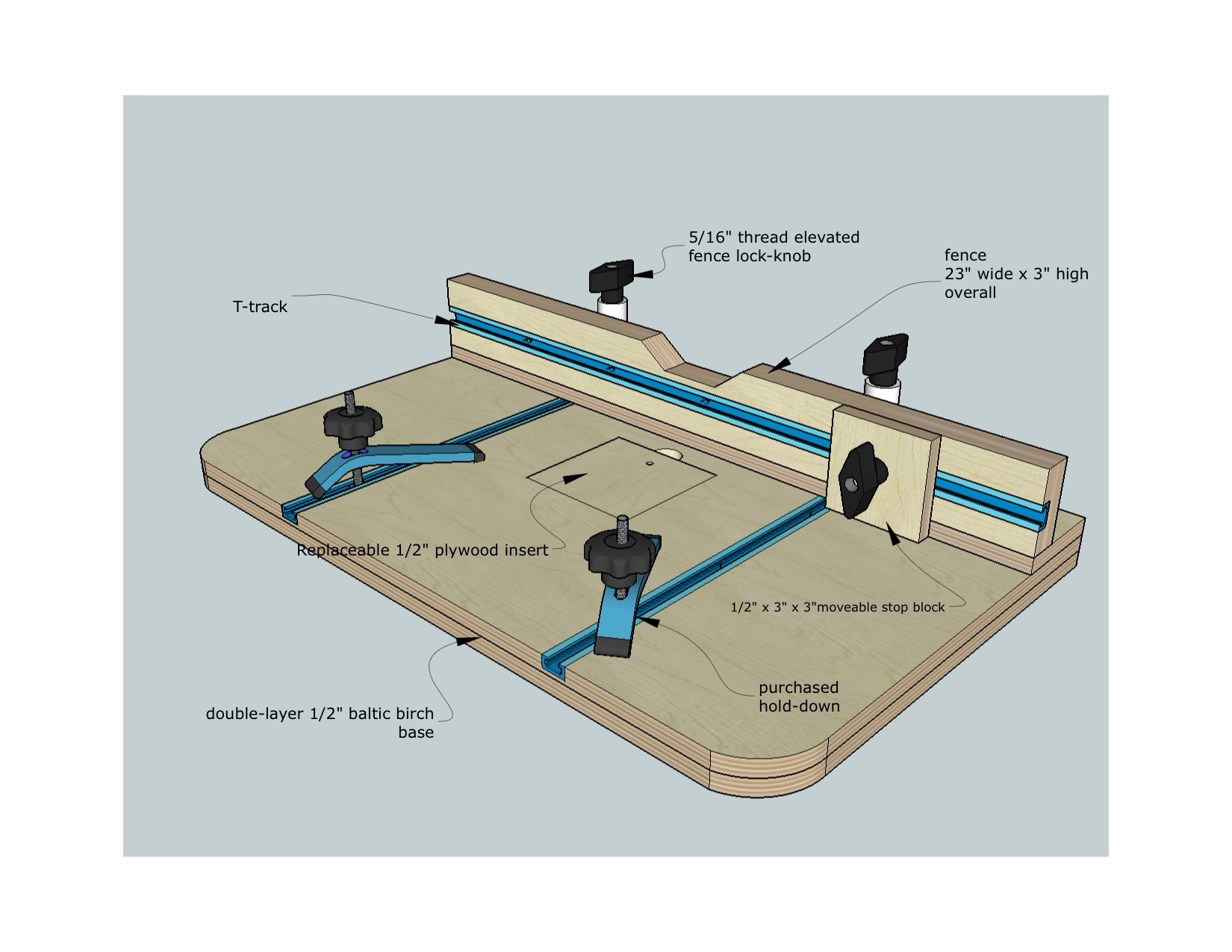
Figure A – Here is the construction of the drill press table. The base and fence are made from two layers of Baltic Birch plywood for rigidity.
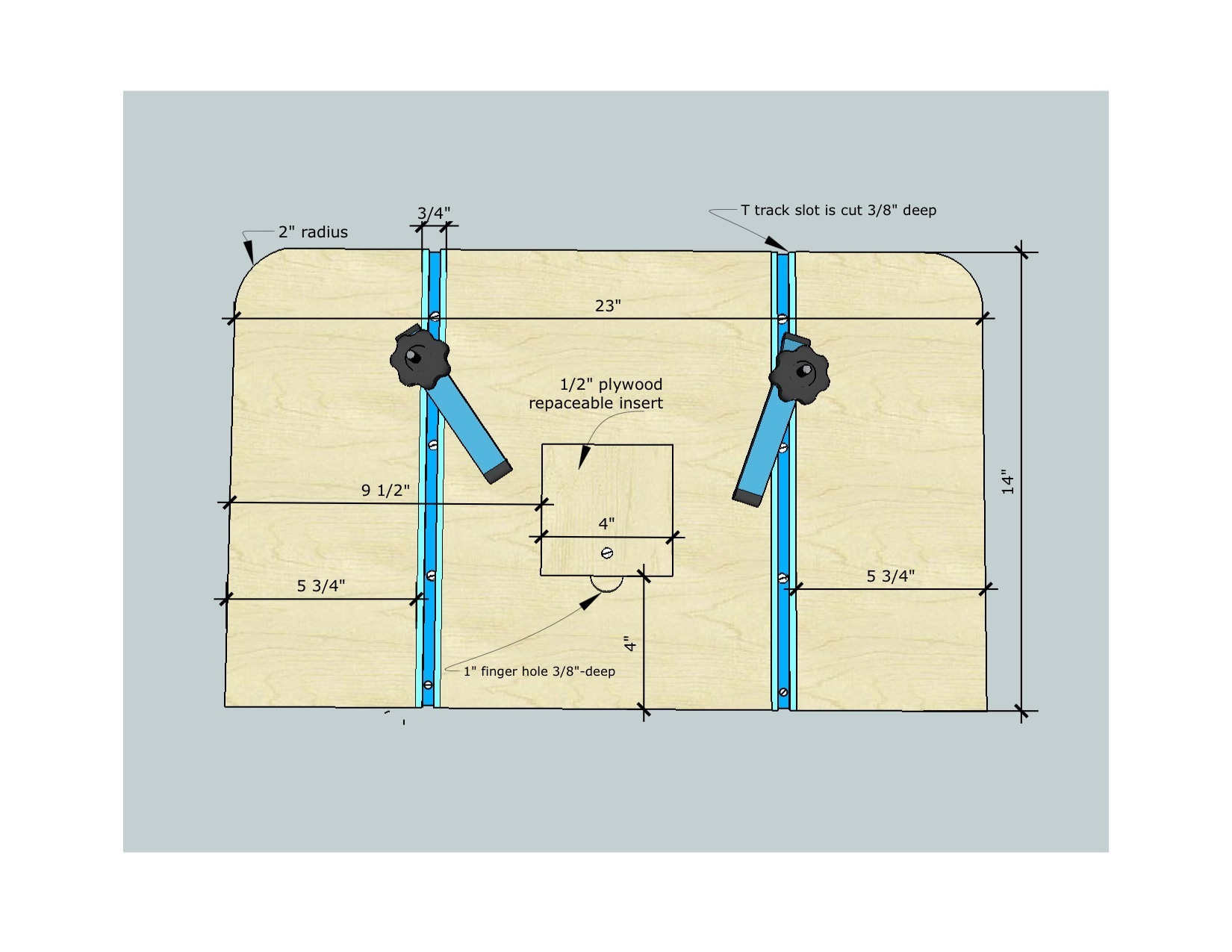
Figure B – Drill press table dimensions
Layout the drill press table with your framing square
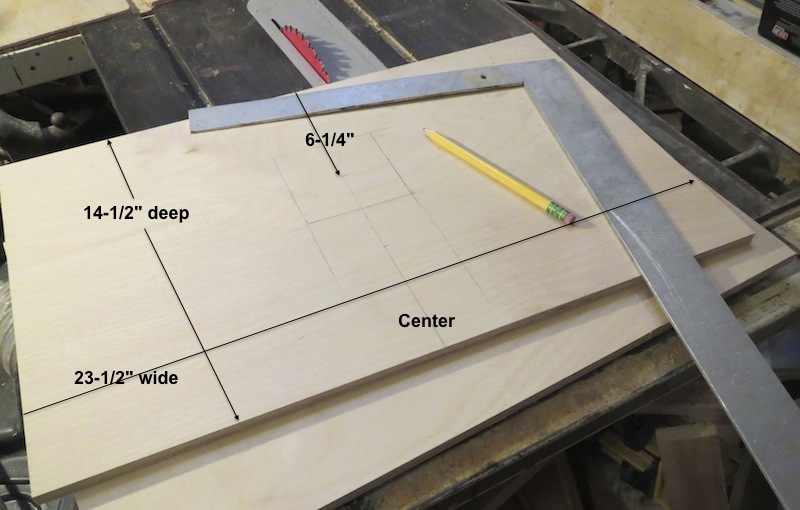
Start by cutting two pieces of 1/2″ Baltic birch plywood at least 1/2″ larger than the finished dimension of the table as shown. This will enable you to trim the piece to final dimensions after gluing. Mark the center and then mark the cutout for the replaceable drilling square. Check your drill press for the dimensions from the column of the drill press to the center of the chuck. Mine is about 6 -1/4”. It’s nothing to get too precise about, a 1/4” difference one way or the other will still be fine. If the plywood has a slight warp, check out the text below for how to deal with it.
Create a finger hole for the replaceable drilling square
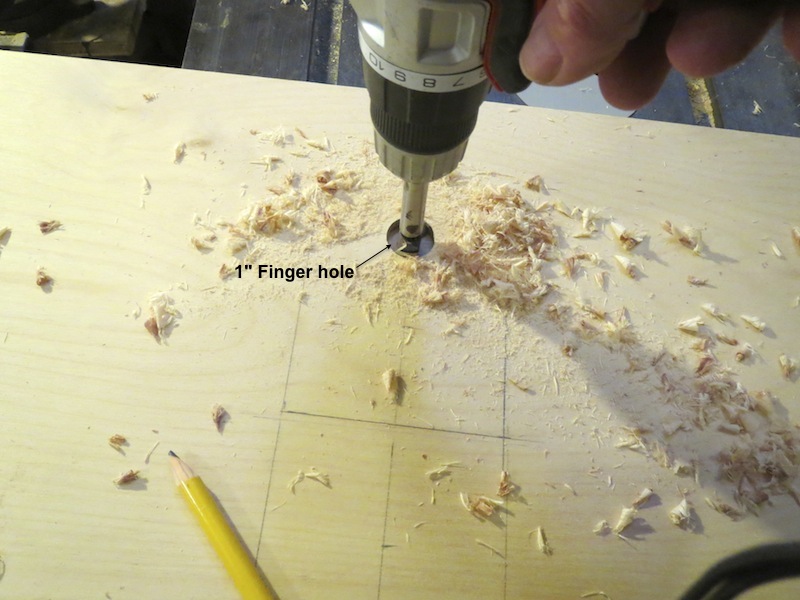
Drill a 1” hole 3/8” deep into the upper base layer to provide a finger hole to help remove the drilling square.
Cut through the plywood with a jigsaw
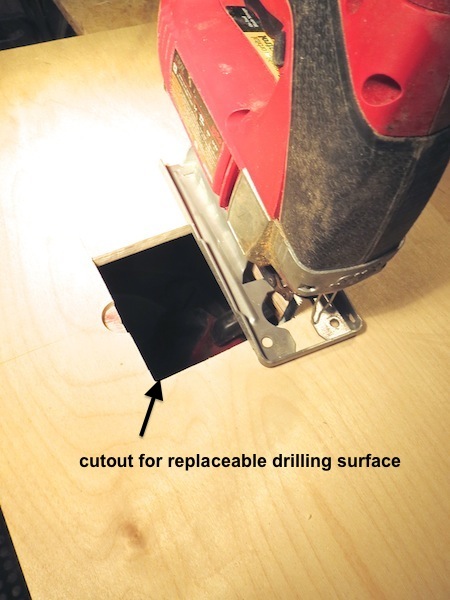
Spread the glue
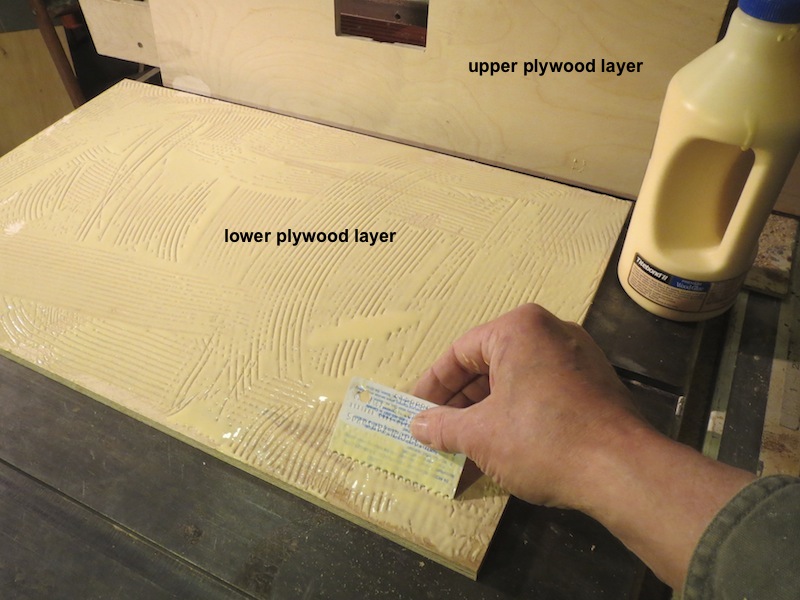
Spread glue over the lower plywood layer of the drill press table. I used an old membership card cut with a pinking shears to help spread the glue evenly.
Pin the halves together before gluing
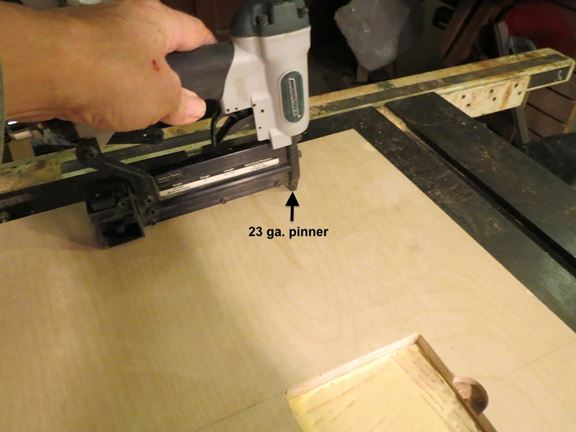
Pin the halves together with a 23-ga. pinner after positioning the panels on your table saw top. The pins will keep the plywood panels from drifting while you pile on weights.
Use cauls to distribute pressure
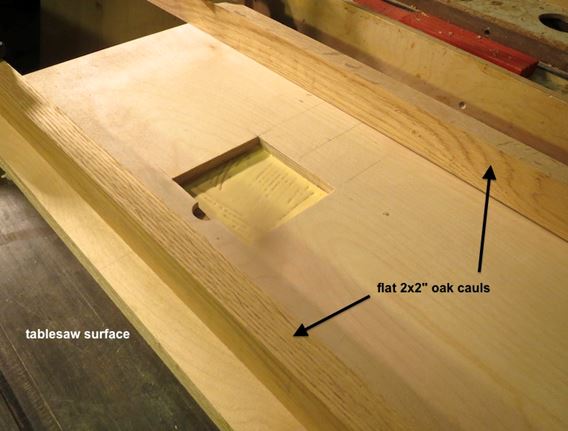
Place straight cauls onto the upper and lower plywood layers so pressure can be placed evenly across the entire surface. Don’t forget to put a later of wax paper or something similar between the plywood and your saw surface so glue squeeze out doesn’t get all over the saw table.
Stack heavy weights
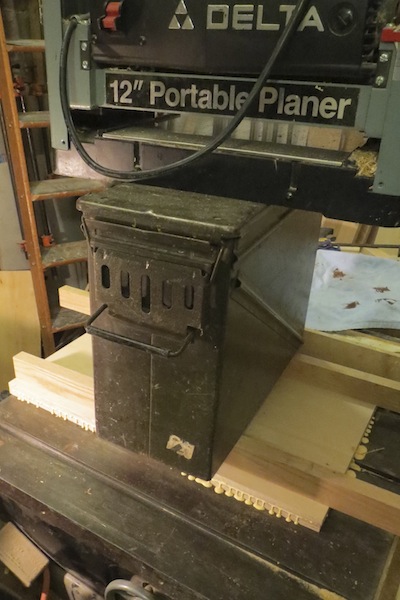
You can see I stacked it pretty high to get enough weight onto the cauls. Use at least 60-pounds of weight, and let it sit for at least three hours.
Scrape away dried glue before it hardens
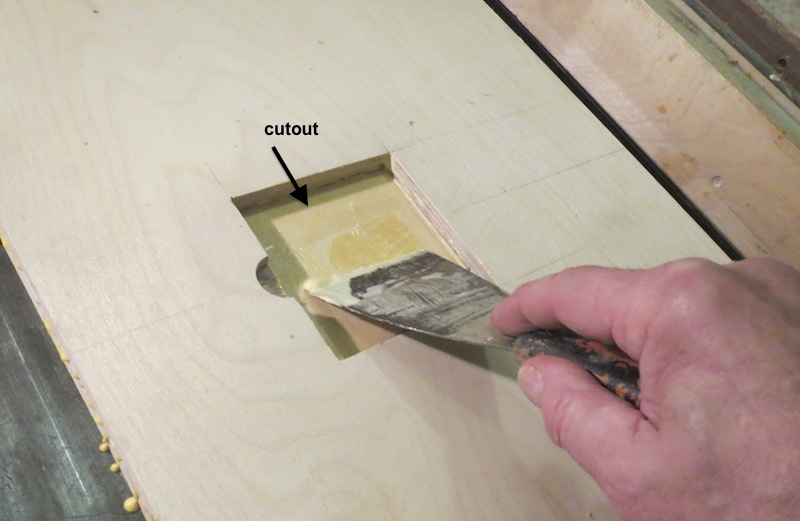
Scrape the glue from cutout before it gets hard. Check the glue frequently for it to be the right consistency for scraping. Too early and it’ll just smear. Too late and it’ll be too hard to remove.
Match dado blade depth to your T-track
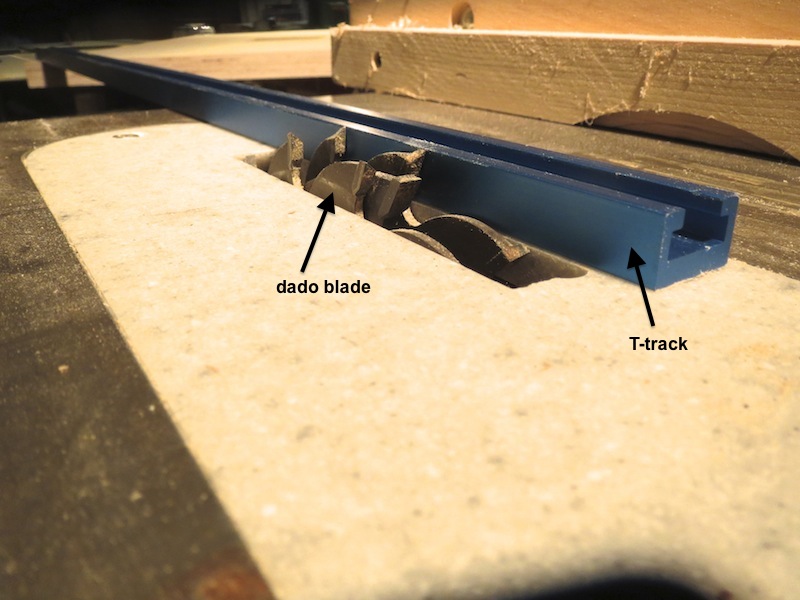
With your table saw unplugged set your dado blade to the height of the T-track. It’s better if the depth is a hair deeper than too shallow. You don’t want the T-track to be above the tabletop at any point.
Dado for the T-tracks
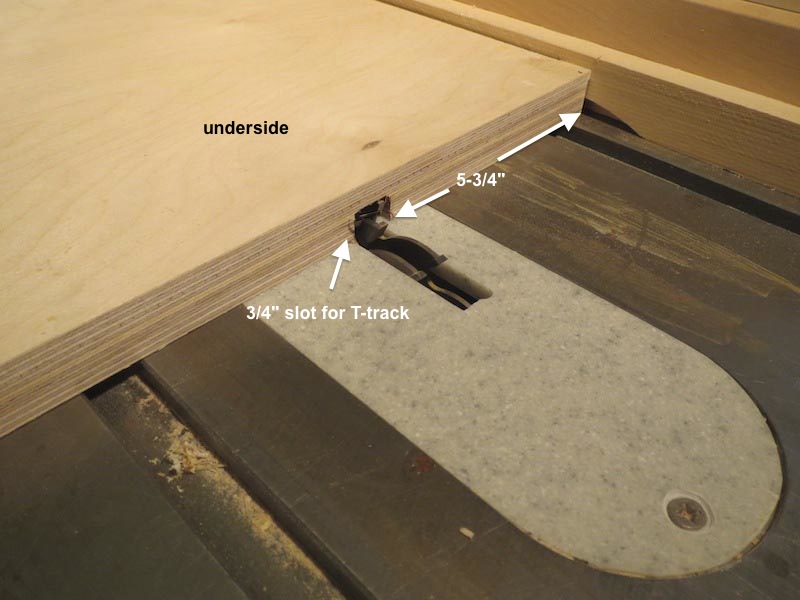
After cutting the glue up to final size (Figure B), set the fence 5-3/4” from the fence and plough your dado. Move the workpiece through slowly and steadily and let the dado blade do the work. Make this cut from both ends, following the lay out in Figure B.
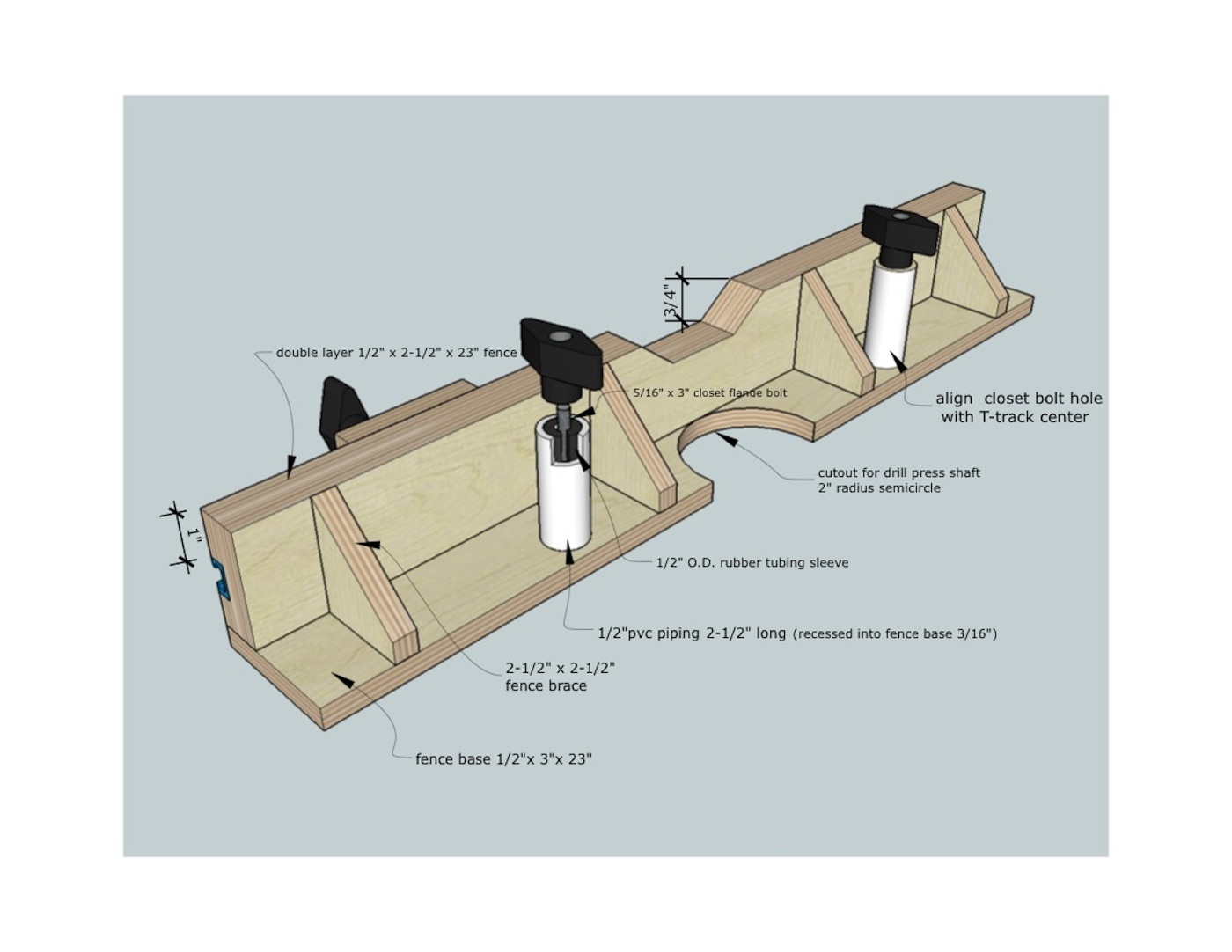
Figure C – Fence Parts and Assembly
Make the warps work for you
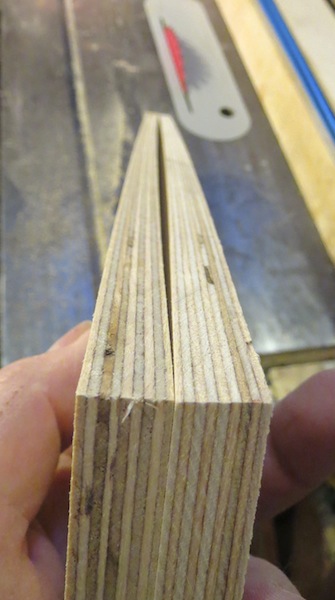
Mate the surfaces for the fence just as you did for the tabletop so any warps oppose each other.
Clamp the parts to a flat surface
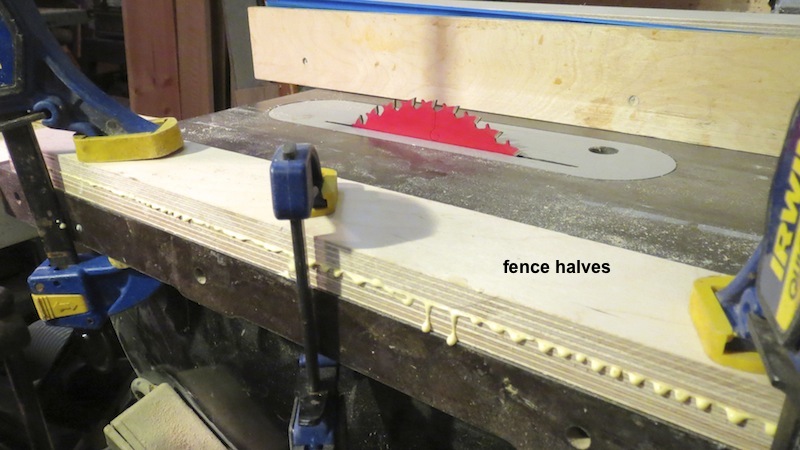
Clamp the fence halves to the top of your table saw in order to keep them perfectly flat. It’s best to cut the pieces oversize slightly and then trim them to size once the glue has dried.
Use a drum sander to smooth curves
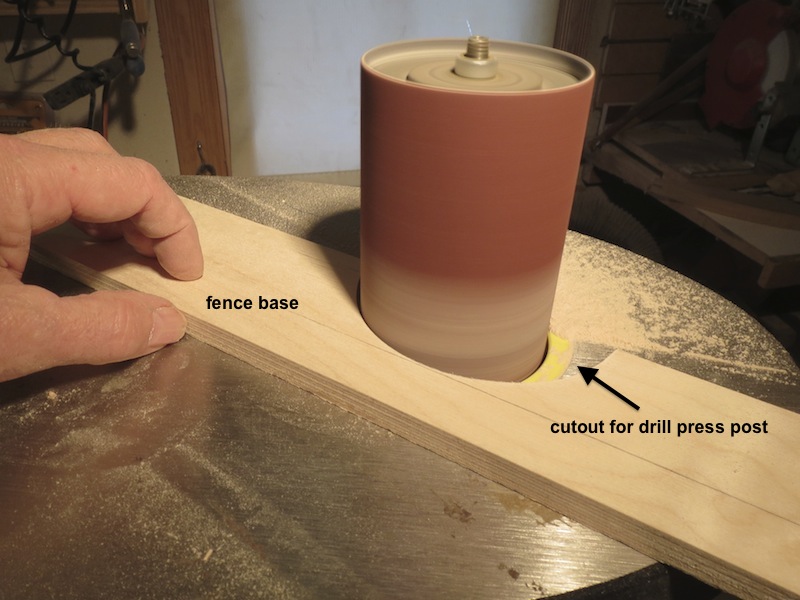
Cut the lower fence base to size and then cut the semicircle in the rear. The 2-in. radius semicircle makes it easy to remove the fence portion of the drill press fixture while it remains mounted to the drill press platen.
Get your dado depth just right
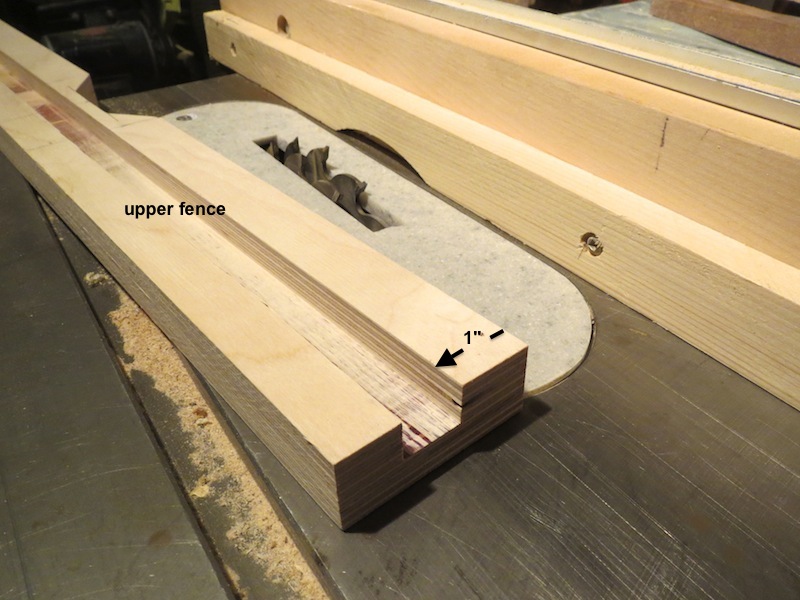
Trim the upper fence to size and then plough a dado for the T-track. Next, glue and clamp the upper fence to the lower fence.
Cut braces to reinforce the fence
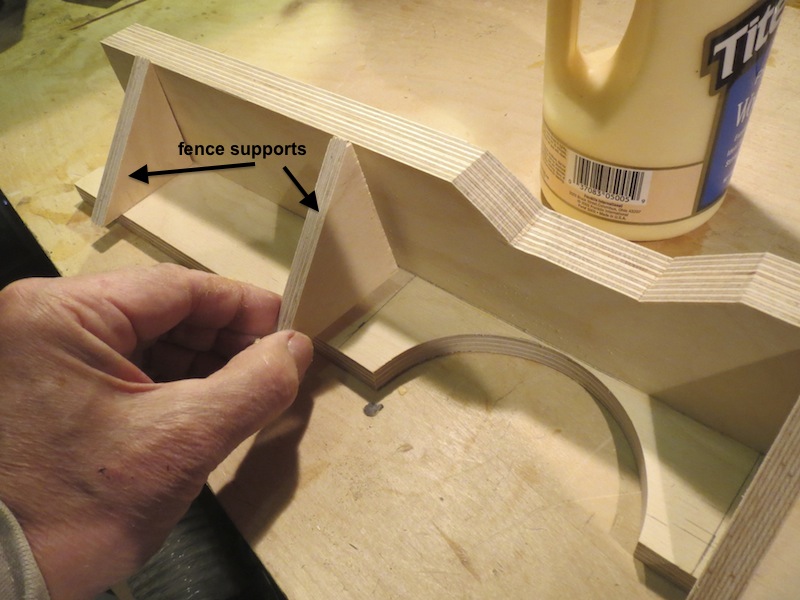
Cut 2-1/2”x 2-1/2” triangular fence supports from the left over ½” plywood. Glue and pin them in place. Set the assembly aside to dry. The outer supports are placed 1-1/2” from the ends of the fence and the inner supports are 8-1/2” from the edge. After the glue is dry use a hand saw to trim the overhanging points off the fence supports.
Use a centerpunch to mark holes

Mark the holes for the mounting screws into the T-track. The holes should be located every three inches along the T-track. Start in the center of each length and work your way along to each end.
Drill and countersink holes into the metal track
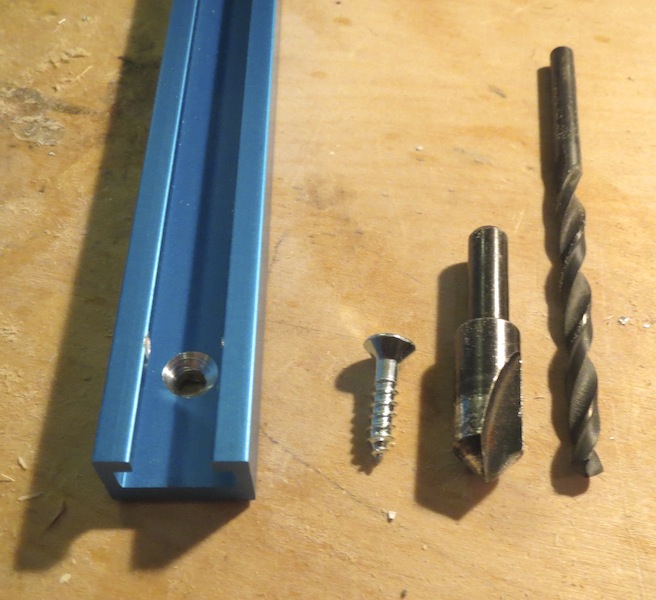
Drill the T-track with a 3/16” drill bit followed by a 3/8” countersink bit. Use #8 x 5/8” flat head screws.
Use flange bolts for T-track knobs
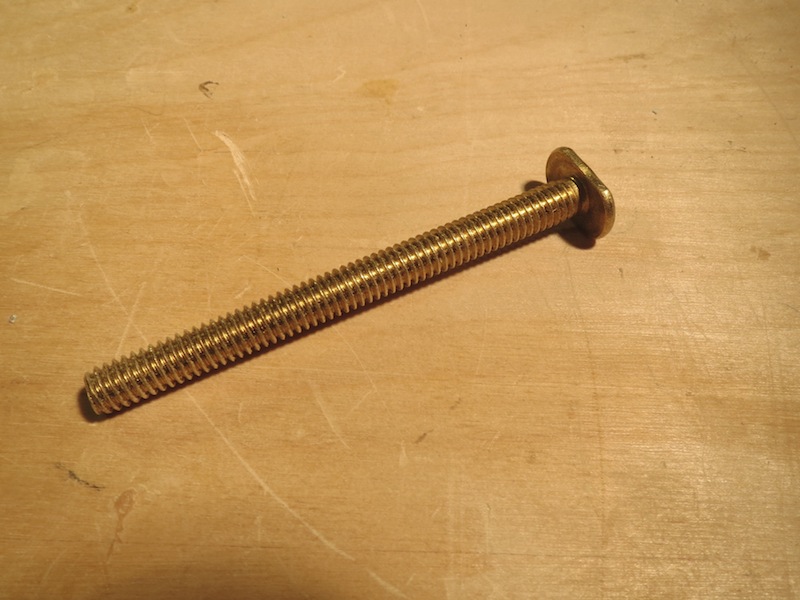
5/16” closet flange bolts are made for fastening your toilet to the closet flange on the bath floor but they work great for T-tracks. I used these 3” long bolts for the fence clamps. They fit into the track and then are sleeved with some ½” tubing to fit into the PVC piping. The piping lifts the knobs of the fence clamping knobs so they’re easy to reach. See Figure C for details. You can cut these to length by threading on a nut, clamping them in a vise and then cut to length with a hacksaw. Simply back the nut over the cut end to restore the threads.
Set up the fence locks
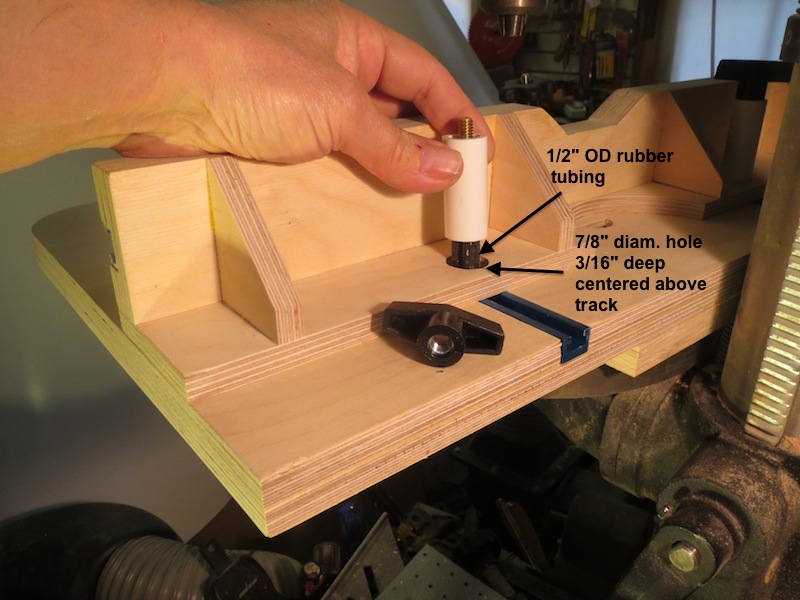
Drill 7/8” diameter recess holes for the fence clamps, 3/16” deep and centered 7/8” from the back edge of the fence base. Be sure to locate the hole center 6-1/8” from the side edge of the fence or directly above the center of the T-track. Drill 5/16” diameter holes for the t-bolts. The ½” OD rubber tubing keeps the bolt centered inside the pvc tubing.
Mounts the assembled drill press jig to your drill press.
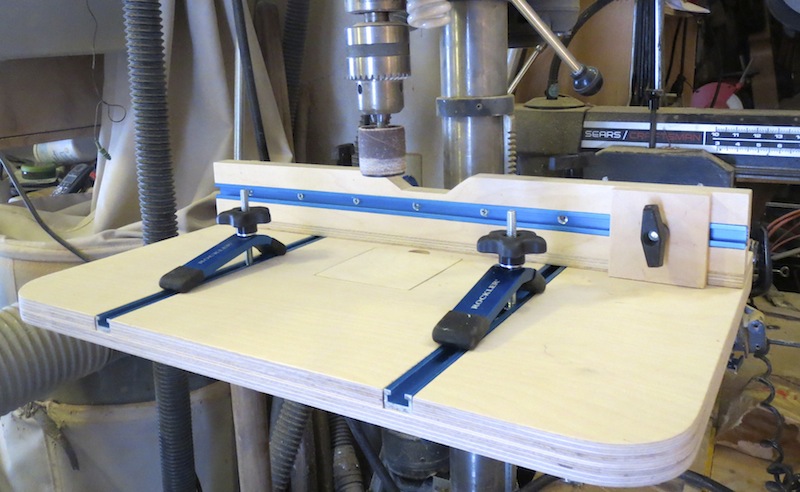
Use lag screws or hanger bolts to mount the fixture to your drill press. I first bolted a scrap of 3/4” x 12” x 12” plywood to my drill press table, then screwed my fixture to the plywood scrap. It’s solid and I don’t think I’ll be removing it any time soon. As a woodworker, why would I?
Sources
Hold Down Clamp #35283
Universal T-track #22104 (1pc)
Universal T-track #26420 (1pc)
1-800-279.4441
T knobs #972 (3pcs)
1-888-512-9069
Is there a disadvantage to having a round replaceable cut out as opposed to a square cut out?
Thank you very much for this plan, have just about finished mine and am very happy with it, again thank you for sharing
Offer any designs for a benchtop drill press! Neat plan! Thanks
Looks simple enough to construct. Just purchased new DP and need a table and looking forward to putting this together.
I'm sure that I'm reading this wrong. on page 3/49 it says to mark the4 center and the mark the cutout for the replacable drilling square. how far in do you put the finger hole?
I can't seem to find the link to download these plans
Nice job thanks
Can not load half of the images, especially the ones with the overall measurements. Would be great to have actual plans to download.
I really liked your plans for the table but I had to downsize considerably as my bench top drill press is not very big. I ended up with a 9x9 table & a 2 inch tall fence. I located 2 tracks for the fence & clamps to share. The fence also has a track for a stop block to ride in. One idea I would share concerns the stand-off posts for the fence tightening knobs. Instead of using steel or plastic tubing, & rubber hose, etc., I cut 2 lengths off an old broom handle & carefully drilled them on center for a 17/64 hole. This avoided tubing & pipe, etc. Washers on either end of the wood dowels protect the soft wood.(Don't tell the wife about her broom, please?)
looks great I will jump on it quick like a bunny