There is actually no single, authentic, “Arts and Crafts finish,” rather many different schools of thought and technique that comprise the totality of the discipline.
It seems that people are looking for that radiant, reddish chocolatey finish when uncovering an antique Stickley chair at a garage sale. In my research, I found the original Stickley finishes (read, plural!) are carefully guarded secrets.
However, I was able to uncover a series of steps, or schedule, that most experts agree upon. I will be adding my two cents into this muddy world of authentic Arts and Crafts finishing which not only saves time but adds durability. I recommend taking the time to fine tune your own process, as all wood is different, and each of us desires different results when finishing wood.
For this finish how-to I’ll be working on a tabouret table.
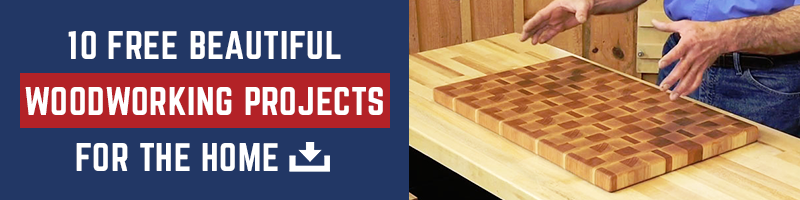
Here is an overview of the different products used. In some ways, this finish can be considered the Holy Grail of finishing techniques. It includes at least four steps that add pigment, color or tone, and requires the use of three different solvents at different stages during the finishing process. Lastly, it requires tons of patience and even a bit of danger. (Say that in hushed tones!) Experts agree that most traditional Arts and Crafts finishes used dye, some type of fuming, an application of shellac (reddish or garnet in tone), and often a gel stain applied at the end to fill the grain a deep brown.
The absolute first step to finishing an Arts and Crafts table is called “raising the grain.” Soak a rag in distilled water and generously apply water to every surface of the disassembled project. The water dries after a day of sitting, leaving behind a layer of expanded wood fibers, which are lightly sanded off. This step is preparation for the next step, where I add dye using a water solvent. The water mixed with the dye can’t swell the fibers of the wood, because the swelling will have already happened.
This is a close look at the wood fibers after “raising the grain.” It is apparent that the grain pops up and has absorbed the water. I gently sand this surface with 220-grit sandpaper to remove the swollen fibers. Avoid vigorous sanding which can expose “un-swollen” fibers deeper in the wood.
Dying the wood is the next step. I measure fifty drops of Trans-Tint “Reddish Brown Dye” into a container (with a top) filled with 2 cups of distilled water. Stir the dye and water to distribute the pigment evenly. Apply the dye with a disposable chip brush, and then gently wipe it off along the grain with a clean rag.
Typically, the density of the color imparted to the wood is a combination of the density of the solution and the time spent soaking on the wood. To get even tone on all the parts, brush the corbels first, and let them sit while applying dye to the top. Afterwards, wipe both the top and corbels. Pre-raising the grain really works. I applied the dye and there was no discernible grain raising. The pigment particles in the dye are microscopic, so they soak deeply into the fibers of the wood and define a base tone for the piece of furniture. I really like dye because the density is easy to fine tune. If the dye is too dark, wipe the surface with a clean rag soaked in water to dilute the pigment. Just the same, an additional application of the same concentration of dye will darken the color.
Fuming is an age-old process for darkening wood. By isolating a piece of furniture in a “tent” with a high concentration of ammonia, the tannins in the wood react with ammonia, creating a dark and rich tone. I make a simple tent out of inexpensive 1×2 furring strips and thick poly sheets. I place the tent is a safe place, where no children or animals might explore.
Ammonia is available in a range of concentration, from the low 1.5% for the homeowner all the way up to 35% from a blueprint supply company. I opted for “Janitorial Strength,” at 10% concentration. Janitorial strength is plenty strong for imparting color, but not nearly as dangerous as the stronger stuff. When using ammonia, I wear a respirator, latex gloves and swim goggles that seal around my eyes, as the fumes can burn your eyes and lungs, and the liquid can burn your skin. I insert the dyed tabouret parts into the tent, isolating the surfaces so they are exposed. After all of the parts are loaded, I pour ammonia into an aluminum pan and insert it into the tent. I seal the tent with duct tape and leave the parts for 72 hours. It is a good idea to check in on your part every 12 hours or so to make sure it isn’t getting too dark.
After 72 hours, I don my protective gear and open the tent to see the results. The darker color is evident in the latter of these two photos. While people often speak of fuming adding a greenish tint to the wood, I find the combination of red dye and fuming make for a very pleasant brown.
Next, I spray a thinned coat of Bulls-Eye Amber shellac onto the parts of the tabouret. I do not sand the fumed parts. I use Bulls-Eye Amber Shellac because it is available at my local hardware store. Liquid shellac has a limited shelf life, so be sure to check the expiration date found on most cans. Bulls-eye Shellac straight out of the can is too dark for my taste. I thin it 50% with denatured alcohol, which makes it much more forgiving and easier to apply with a spray gun.
Don’t be tempted to brush shellac in this instance. I’ve made this mistake before. Shellac dries really fast and is difficult to control. The amber color in the shellac is subtle, but unmistakable. In my mind, it is the essence of “antique”! If the first coat is a little rough, lightly sand with 320 sandpaper and lay another light coat on top of the first for a bit more color and to flatten the first coat. Spirit based stains (which I plan to apply in the next step) don’t bond to surfaces with trace amounts of wax. Bulls Eye Amber Shellac contains wax, so I topcoat this layer with Bullseye “Sealcoat” Dewaxed Shellac. I apply these coats quickly; usually I am done within an hour or so. I let the piece sit overnight for the shellac to begin curing.
When I come in the next day, I am captivated by the table. It is so beautiful, I am inclined to leave it as-is. My goal in woodworking is typically a striking finish, rather than a specific color, but I am also curious to see what additional tone will do for this table. Against my instinct, I forge ahead. I lightly sand the surface with 320 grit sandpaper and then use a vacuum outfitted with a brush to clean the dust from the pores.
Applying Zar “Moorish Teak” stain is a breeze. I wipe a liberal coat of the thick stain onto the entire piece and let it sit for a couple of minutes. When I wipe it most of the stain comes off, but the pores fill, leaving a darker, richer finish. I guess it was worth the risk!
Wiping a protective coat of polyurethane on top of a stained surface is a dangerous proposition. The solvent in the poly can lift pigment from the stain and pull it all over the piece. To avoid this fate, I let the tabouret sit for another day, and then spray a topcoat with Minwax Polyurethane Gloss, which “sets” the stain. While any brand works, I like Minwax aerosol because the nozzle has an adjustable valve that allows me to orient the fan either horizontally or vertically. While the cost is relatively high when using aerosol cans, I often use them for small projects because they save me 15 minutes of clean-up.
Furniture in the 21st century is subjected to much more abuse than in years gone by. People want heirloom quality furniture but are not likely to put down coasters. Rather than risk a finish failure, I put a layer of polyurethane on top of all of the table-tops I make. In ten years of furniture making, I’ve never had a client damage one. I let the sprayed finish dry, and then proceed with 2 thin coats of wipe on poly.
The photos hardly do the piece justice; the depth of tone and clarity of grain and character and are unequalled. I know this finishing approach may seem a bit over the top, and requires a lot of time and steps, but the process is immensely rewarding, each step adding to a rich and “authentic” finish.
Photos By Author
Sources:
Trans-Tint “Reddish Brown” Dye, #27582, www.rockler.com, $21.00, 800-279-4441 Ammonia, Janitorial Strength, available at local Ace Hardware, www.acehardware.com
Zinsser Bulls Eye Sealcoat Shellac, $15.00 for a quart, available at most Home Stores Zar “Moorish Teak” Stain, available at True Value hardware stores, www.truevalue.com
Minwax Gloss Polyurethane in aerosol can, available at most Home Stores
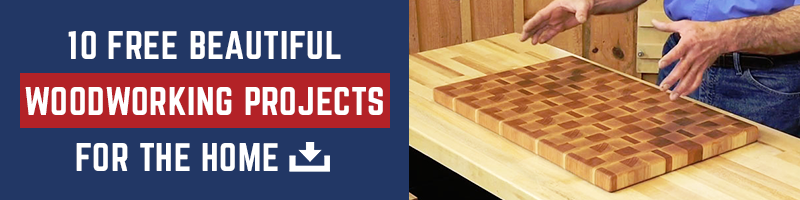
I’m restoring my old house’s woodwork. It’s over 11 y-o. I use a lot of water dye and never see raised grain. I wonder if it’s because it is so old and the resins have hardened? FWIW, I use Moser red mahogany with added purple in water, then re mahogany color in BLO over that. Lastly, same re mahogany in clear shellac at least one coat, applied with ox-bristle brush. I generally go for 4 coats, switching to clear once the color is dark enough. Lastly, 4 applications of SC JOHNSON paste wax with 0000 steel wool. It’s a soft-feeling final finish.
Hi Seth. Its been quite a while since anyone commented, so hopefully I'll get a response. I am assuming that your table was constructed with white oak. I was able to obtain a generous amount of 4/4 red oak. I am wanting to get the chocolate brown look with my projects. In your opinion, will red oak behave similarly to yours? I sure hope so. Thanks for sharing your information.
Hi Tom I'm sorry to hear about your experience fuming! I wonder if you had a higher grade of ammonia than I was able to acquire. Both the concentration and duration affect the darkness, but I have never gotten anywhere near 'black' when fuming. Additioally, oak is a natural material, and perhaps yours had an extraordinary amount of tannin, which is what reacts with the ammonia. I have gotten some tonal differences and usually dye these darker to balance the tones before I move on to the shellac layer. So, in thinking of what I would do in this circumstance, I would probably sand all of the pieces as the fuming works from outside in. Hopefully, this will manage and moderate the density of the color. Then, if you can identify the light and dark sections of wood, I would use dye to darken the very light sections. Lastly, I would thin my shellac with denatured alcohol as the pigment in shellac can be quite deep. As a final hail Mary, I might embrace the dark tone and go all in. There are many examples of very dark Arts and Crafts furniture (see Charles Rennie Mackintosh) that are extraordinarily beautiful. Good luck. Best, Seth
Followed to the t on my first QS A&C couch. After spraying w amber shellac came in next day to my worst nightmare . The piece looked almost black in some sections, mostly I imagine, where the fumes had been strongest and mostly bottom of the legs and underside of the arms. The brackets and caps (I didnt actually mortise the pieces) look ebony. My fault for trying something so new on an important piece. I did lots of testing but it was impossible to know how uneven the fuming would be on such a large piece. Any ideas how I can recover? Have washed the amber shellac down w steel wool 0000 to try to at least get that color off but not really helping
Good grief, Dale. Give Seth a break! He took time to give us some of his experience. There are professionals out there (no names) who won't tell you the time of day. Be happy that someone was willing to help. If you don't like, don't do it. It's that easy. You'd spend thousands making mistakes before you figured out what the folks on this site are giving you. This kind of mud slinging has no place in a forum that's basically free. Just my opinion.
HI Dale- I am not sure what you are referring to. Please elaborate. I do advocate you buy all of your finishing supplies. Thanks for the comment! Best, Seth
This doesn't appear to be any type of informercial to me, Dale. I see an elaborate professional process detailed here with a list of everything that the author used provided as a courtesy to us in case we are curious enough to give it a try. As an example this article actually inspired me to try fuming on a small project, so I went to Ace and bought their ammonia. This was a great tip because the home centers in my area don't carry ammonia that is strong enough for fuming and this stuff does the trick.
wonder what you are selling