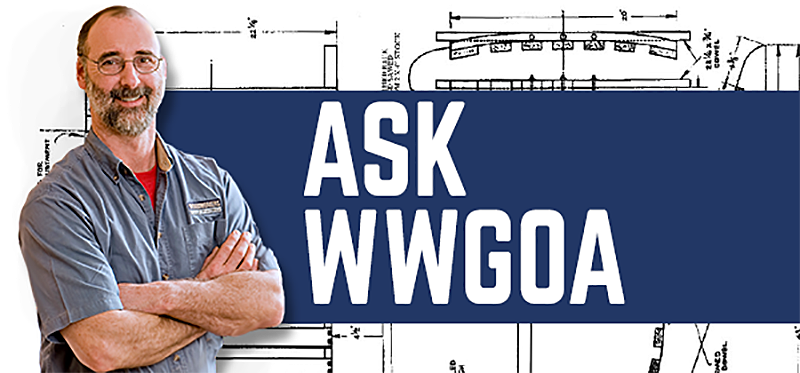
Q: I’m building a jewelry box for my girlfriend for Christmas. I’m looking to flock the inside the drawers, and the inside top half, where necklaces will hang. I’m curious how much setup time I have for the adhesive, if I can spread the adhesive and lay the flocking all at once or if I should do it in sections?
A: The open time will vary depending on the product that you use, as well as the ambient humidity and temperature in your shop. That said, I believe that you should be able to make it in one pass, and I would be uneasy about trying to do it in two phases. You might want to do a simple test on some scrap, and spread some adhesive out and see how long it remains tacky.
Here’s a video on this topic:
You might also be interested in:
Jewelry Box Plans
Glue Tips: Using Denatured Alcohol for a Strong Bond
Methods for Evenly Spreading Glue
Using Contact Adhesive
How to Make a Bandsaw Box
Turning a Small Lidded Box
Cool Upcycled Wood Boxes Using Salvaged Wood
I am building shaker kitchen cabinet doors using solid hickory wood for rails and stiles. The panels are 1/2 inch hickory veneered plywood that has some areas that had knots and they used a dark purplish filler to fill in when plywood was made. I am using clear oil polyurethane and have applied one thin coat with mineral spirit and noticed that some of that filler has lifted or chipped exposing the white ply underneath. How can I darken those areas after applying a coat of poly without using epoxy? Or what would be recommended to fix this?
How do I know when my band saw tires need replaced?
Best way to cut 1/32" X 45 On 3/16" and 1/8" stock all sides?
I just saw your latest Q&A. During which you showed a blue film you used for sign making. What was it and where do you get it?
Learning to make bowls with a router versus my lathe to expand the size and design. The blanks are made laminating wood to create the size needed for the pattern being used. Wondering if it is possible to color a wood green to be used as part of a blank. Example might be a Christmas Tree pattern. Red, brown, white are all possible or close enough with natural wood color. Green is my challenge? Coloring the layer of wood in the lamination after gluing up the blank does not seem workable due to bleeding between layers. Thoughts?
Do you have any blueprints and material list for sheds?
I am a Professional Piano Technician doing research and experiments to come up with a solution to a problem that plagues moving parts in Steinway pianos from the early 1900's. Through research I found that parts had been boiled in paraffin wax to protect against moisture and warping. Unfortunately wool bushings and metal pins holding things together react , develop verdigris like condition and seize up. I believe the paraffin wax is at the core of the problem. I m trying to find a way to detect paraffin wax in the parts and a way to force it out. Attempts with some chemicals have been made but are dangerous and the problem re-appears. I need a non-destructive way to get all of the paraffin out- basically I need to "unboil"
I do woodturning as a hobby and I have what I consider a very large burl from a tree that I cut down in my own yard a year ago due to location issues. Asking for help with the best way to proceed. Thanks in advance. I have pictures but being new I'm not sure how/where to upload.
Would like to build a Mitre saw work bench..can't seem to find anything about this. ..need help..thanks
I have recently purchased a house which has a 2-car garage sized outbuilding, which I'm going to use for my workshop. In the past, I've only ever had small spaces to work in (10x12, 10x15, etc.). The space I have now is obviously much bigger, but I still want to make the most of it so that it "flows" well (lumber storage next to jointer, jointer next to planer, etc.). In my smaller shops, I've always had to have my workbench against a wall so that I was able to move around; this, in turn, made me have to rotate the work piece on the bench to be able to access all 4 sides, and I've gotten used to working like that. With this larger space, however, I can position my workbench so that I can walk around it, which would mean I wouldn't have to rotate the piece - saving time and effort. My question is this: What is your preferred space for your workbench - against a wall or in the center of the floor? Or is it a matter of personal preference balanced against space availability?