These no-waste easy-to-build cabinets are a great way to increase the storage in your shop. These modular storage cabinets are designed to be easy to build and install, and to make maximum use of space with a minimum amount of material waste. I replaced four of my cruddy looking old shop storage cabinets with 5 of these great looking new ones (see the before and after photos).Building the cabinets took more time than I anticipated because I covered the exposed plywood edges with solid maple 1/4 thick edging rather than use iron-on wood edge tape. I’ve never been happy with the look and feel of the iron on edging. That’s just me.
Design & Construction Details. There are no door handles! Instead the doors are longer than the height of the cabinet. They overhang 1 at the bottom, and that’s the handle. It’s clean and it works well.The European style concealed hinges are easy to install and adjust. They ‘clip’ to their mounting plates making tool-less mounting and un-mounting a snap! The pneumatic soft close add-on device is nice. I tested it on some of my older cabinets, and I was impressed. No matter how hard you try, the doors will not slam shut. Instead they close slow and soft.
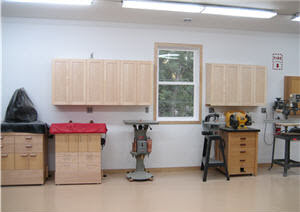
The hinge plates, shelf support pins, and cabinet connector bolts mount in a series of 5-mm dia. holes drilled near the front and rear edges of the sides. I own a dedicated hinge and line-boring machine, and it’s what I use to drill the holes. It’s overkill for a one-person shop, but it does make hinging doors and case construction easier! There are other inexpensive and simpler jig options. You could also lay out the holes and drill them on a drill press using a 5mm brad point drill bit.
As I’m sure you know, 3/4 thick plywood is not 3/4 thick. You’ll need to compensate for this. The finished width of the cabinet is 24. Measure the combined thickness of the 2 sides and adjust the lengths of the top, bottom and shelves accordingly.
The cabinets are ‘hung’ on the wall using wall-mounted ledgers, and cabinet mounted hang strips. The hang strips are fixed to the cabinets with biscuits and glue. The ledgers and cabinets are joined with loose biscuits, no glue. When you hang your cabinets, use 3 screws through the ledgers and hang strips and into wall studs. Each 2′ wide cabinet section needs to be secured to the wall with four screws; two through the hang strip, and two through the ledger. You’ll need to use wall anchors if you a masonry wall with no wall studs.
I have included a cut list of all of the components at the end of this article along with a summary of where I purchased the components I used in my cabinets. Following are the instructions on how to assemble the cabinets.
Make the Cabinet Boxes. Cut the tops, bottoms, sides, and shelves to size (pieces A, B and C). Make the edging strips (E, F and G) slightly wider than the plywood thickness. Cut their lengths 1/2 longer than the edges they will cover.
Photo 1. Glue and clamp the solid wood edging pieces to the exposed plywood edges. I do this using 6. long pieces of masking tape placed 2 apart.
Apply the edging gluing and clamping the solid wood edging pieces to the exposed plywood edges. I like to do this using masking tape (Photo 1).
Photo 2. Sand the edging flush with the plywood faces. Use a belt sander and a 150-grit sanding belt. Squiggly pencil lines drawn across the joint will guide you so you don’t sand too much.
Trim and sand the edging ends flush with the plywood ends. Sand the edging edges flush with the plywood faces. Use a belt sander and 150-grit sanding belt. Making your wood with a squiggly pencil lines will guide you so you don’t sand to much (Photo 2).
Plywood has an A grade face and a B grade face. Put the A faces inward on the cabinet sides that join each other with the connector bolts, and outward where the cabinet sides are finished ends. Put all of the top and bottom pieces A face inward. Label the parts well to avoid confusion.
Photo 3. Layout and cut the #20 biscuit grooves at 1-3/4, 5-7/8, and 10 relative to the front edges of the sides, tops and bottoms.
Layout and cut the biscuit grooves in the sides, tops and bottoms (Photo 3).
Photo 4. Layout and drill the 5mm holes for the hardware. I use my line-boring machine. An inexpensive plastic jig will work fine, it just takes more time.
Get all of the hardware and test it before you go any further. Once you know how it mounts and works, then layout and drill the 5mm holes in the sides (Photo 4). An inexpensive plastic jig will work well for drilling the holes. Drill the holes for the connector bolt sleeves through the sides that join with other sides. Finish sand the inside faces of the sides, tops and bottoms.
Photo 5. Glue and clamp the cabinets together. I use my shop made cabinet square blocks to ensure the assembly is square.
Assemble the cabinet boxes (Photo 5). I use my shop made squaring blocks to help ensure the assembly is square.Make the hang strips and ledgers (H and J). Lay out the biscuit grooves in the hang strips and ledgers. Set your biscuit jointer’s fence to cut the grooves relative to the backs of the hang strips and ledgers, and so 3/16 of wood remains between the fronts of the hang strips and ledgers and the grooves. Test the setup on scrap stock, then cut the biscuit grooves. Set the biscuit jointer aside for now without changing the fence setting.
Cut the backs (D) to size. Lay the cabinet boxes face down, and set the backs in place loose (no nails). Lay out the hang strip and ledger biscuit grooves in the cabinet tops and bottoms. Move the biscuit jointer’s fence 1/32 closer to its blade, and then cut the biscuit grooves in the cabinet tops and bottoms with the jointer’s fence resting on the cabinet backs. This setup creates a 1/32 space between the cabinet back and wall so it’s easier to hang the cabinets.
Finish sand the shelves, hang strips, ledgers, cabinet backs, and outsides of the cabinet boxes. Glue and clamp the hang strips to the cabinets. Ease all exposed sharp edges. Apply your favorite finish to the shelves, ledgers, cabinet boxes and backs. I used Briwax. Nail the backs in place, and attach the hinge mounting plates.
Make the Doors. The dimensions given for the door stiles and rails (K and L) allow for 1/16 gaps between all doors. At a cabinet finished end, the door outside edge will be setback 1/32 from the cabinet side. Cumulative error in machining setups makes achieving these tolerances impossible. Knowing this, I make my stiles a smidgen wide, and then trim and fit the assembled doors.
Photo 6. Cut the door panel grooves in the stiles and rails. I use my table saw and an 1/8 kerf saw blade with flat topped teeth. I make 2 cuts so the finish groove width matches the panel thickness.
Make the stiles (K) and cut them 1 longer than their finished length. I find it much easier to assemble frame and panel doors starting with the stiles long, and then trimming their lengths after the door frames are assembled. Cut the rails and panels to size (L and M). Cut the stile and rail panel grooves (Photo 6).
Photo 7. Cut the tongues on the rails using a table saw and tenoning jig.
Cut the rail tongues using a table saw and tenoning jig (Photo 7 and 8). Remove shoulder waste using a table saw and miter gauge.
Photo 8. Remove the shoulder waste pieces with a table saw and miter gauge. For safety, I mounted a piece of 1/4 MDF to the top edge of the miter gauge fence and had it extend over the saw blade.
Photo 9. Assemble the doors. Use a slow set glue to give yourself more open time. Use a pipe clamp to pull the rails tight to the plywood panel, and then clamp the stiles to the rails.
Apply a coat of finish to the door panels, and then assemble the doors (photo 9). Use a band saw to trim off the excess stile ends. Sand the ends of the door frames smooth.
Photo 10. Mount the hinges on a pair of doors, and hang those doors on one of the cabinets. This is a rough fitting of the doors. I take the extra time and do this step to make sure the fit is close at this point.
Do an initial mounting of the doors to see where you’re at with the fit (photo 10). If they are grossly wide, then trim them a bit now, but still leave some width to allow for more adjusting when the final fit is done after the cabinets are hung.
Photo 11. Rout a 1/4 roundover on the door edges. Do the top outside edge, and the bottom inside and outside edges. The stop block prevents blowout at the end where the router bit exits.
Rout the top and bottom rounded over door edges (photo 11).
Photo 12. Set the cabinets on the ledger, and secure them to the wall with screws through their hand strips and into wall studs. A 6 long screwdriver tip is helpful for driving the screws straight.
Hang the Cabinets. Lay out a level line on the wall for the ledger, and locate and mark the wall studs. Screw the ledger to the wall. If your wall is not straight, then you will need to loosen the ledger screws a bit to make setting the cabinets easier. Lay out and drill the screw holes through the hang strips. Set the biscuits (no glue) in the ledger. Set an end cabinet on the ledger and over the biscuits. Screw through the hang strip and into a wall studs to secure the cabinet to the wall. Add the other cabinets to complete the ‘run,’ and join them with the connector bolts. Tighten the ledger and hang strip screws if they were loosened.
Hang, adjust and trim to final fit the doors. When you’re done, remove the doors and hinges. Finish sand the doors and apply the finish. Rehang the doors, stick the door bumpers in place, set the shelves, and you’re done.
Cutting List.
Overall Dimensions:
24 wide x 32-1/2 tall x 12-1/2 deep
Material Sources:
I use French cleats to hang cabinets. Easier to hang and adjust left or right as needed.
Good start, looking for floor cabinets too!
For those needing larger photos there are a number of means to accomplish this right at your computer. 1. Right click the photo then click "save image as" and save the photo as a jpeg. Then open it and enlarge it. 2. Right click the the photo and click copy then paste the photo into another program such as word or a graphics program to enlarge it. 3. simply change the the setting in your browser to a higher viewing percentage to view the images at a larger scale. Hope this helps some of you I know good woodworking skills can be more important than computer skills. Seems I'm always having to learn both.
cannot download says its not available
have an idea for the size of the print etc., print out the drawings and whatever else you need, your local library has a copy machine that enlarges, for a minimal cost. hope that helps
will use in shop, having trouble reading cutting list, no excuses, give my tired old eyes a brake. Thanks MZ
Lots of ideas to be culled from this article. I definitely won't be using any hardwoods because of costs and I feel I need to justify all expenses. Also, please move the fire extinguisher, it is blocked by the drill press.
Why do the photo's pop up even smaller than what is on the page, when you click on them to enlarge them. This now happens on all similar articles.
When the church where my Boy Scouts meet remodeled their kitchen, I got a 14' one piece wall cabinet. I mounted it with French cleats since I didn't want to align holes in the cabinets with the wall studs. I had to rent a material lift to install the assembly. It was worth the cost since the cabinet was free.