For the past four summers I have made the trip from my Upper Michigan summer home out east to take classes at the famous WoodenBoat (not a spelling error) School in Brooklin, Maine, which is just a stone’s throw south of Acadia National Park on the Atlantic coast.
I’ve been a woodworker all my life (a shop teacher for the past 32 years), but when I decided to repair a wooden boat we inherited from my wife’s parents, I knew that I was in over my head as soon as I started. One of my best decisions (I found out later) was to not even attempt the repair without further educating myself. After a short search on the internet, I signed up for a wooden boat repair class at WoodenBoat in June of 2011. During those two weeks, we worked on a valuable canoe ($11,000 when new), a historical 1940 Herreshoff 12 ½ sailboat, and a 1945 catboat. My instructor, Greg Bauer, was (and is) an excellent teacher with enough patience to not get too irritated with my million questions. I had such a positive experience taking the class that I have gone back to WoodenBoat every summer since. Here’s a look at my experience at the WoodenBoat School.
The WoodenBoat School is… well… a summer camp for adults who come from every conceivable background with one common interest – wooden boats. I have worked alongside surgeons, lawyers, teachers, college students, high school kids, generals, and company executives, to name a few. Everyone at the school is on equal ground with virtually no egos mucking up the works and the friendly atmosphere is almost surreal. I have made many friendships that continue year after year as the school has an extremely high number of returning students, which is the best indicator of how well the school operates. The director, Rich Hilsinger, has been at the school since 1983 and does a fabulous job of making your experience better than you expected. Mike Moros is in charge of the shop and brings years of practical knowledge as the shop manager and sometimes teacher. I hold Greg Bauer, my first instructor, personally responsible for giving me the wooden boat bug that I just can’t shake. He now spends most of his time managing the working waterfront where students can take a wooden boat (over 30 in the fleet) out for a sail or row after class. I have also taken several classes with the “Grand Poohbah”, Greg Rössell, who has been teaching and working with wooden boats on the Atlantic coast his entire life. He’s the master of the master teachers. All of the instructors go out of their way to make you feel comfortable, no matter what your skill level is. Most classes run one week with a few taking two. Accommodations include an on-campus campground or student housing along with a full service dining hall.
There are many different ways to build a wooden boat, each with its distinct characteristics. One of the most popular classes introduces students to the traditional way of building boats such as carvel – where solid wood planks are custom fitted onto an upside down frame (usually), caulked, then faired out so the hull is smooth.
Lapstrake/clinker style uses solid wood planks overlapped on the hulls like siding on a house. These methods require a large amount of time and patience along with a high level of woodworking competence to successfully complete a project.
There are also many other classes that teach less traditional building methods such as these listed below:
Glued lapstrake is becoming more popular as the quality of solid wood declines. Plywood planks are glued together with epoxy along the laps to form a very rigid hull. The interior of the craft is outfitted in a manner similar to the traditional carvel and lapstrake boats.
Strip-planking – thin, narrow strips of wood are attached to a form then covered in glass cloth saturated with epoxy inside and out. This is popular with many canoe and kayak builders that usually keep the woods natural color with no paint. Since the fiberglass and epoxy are what give the hull its strength, many intricate patterns of wood can be incorporated into the design without undermining the hull’s strength.
Cold forming – basically creating a shaped plywood hull by laying up several layers of veneer with epoxy. It’s a very labor intensive process that’s usually reserved for professional shops but is doable for the amateur who likes to put in thousands of staples and get knee deep in epoxy. The completed shell is a very strong, lightweight, watertight hull that’s very durable but difficult to repair if damaged.
Stich-and-glue is a process where plywood strakes are wired together, glued with epoxy, wires removed, then more epoxy filleted into the gaps to form a very strong craft. If you want a boat quickly, this is the method for you. There are many, many companies who specialize in CNC produced stitch and glue kits for those who want to build their own boats but don’t have more developed skills or the needed tools required for other methods.
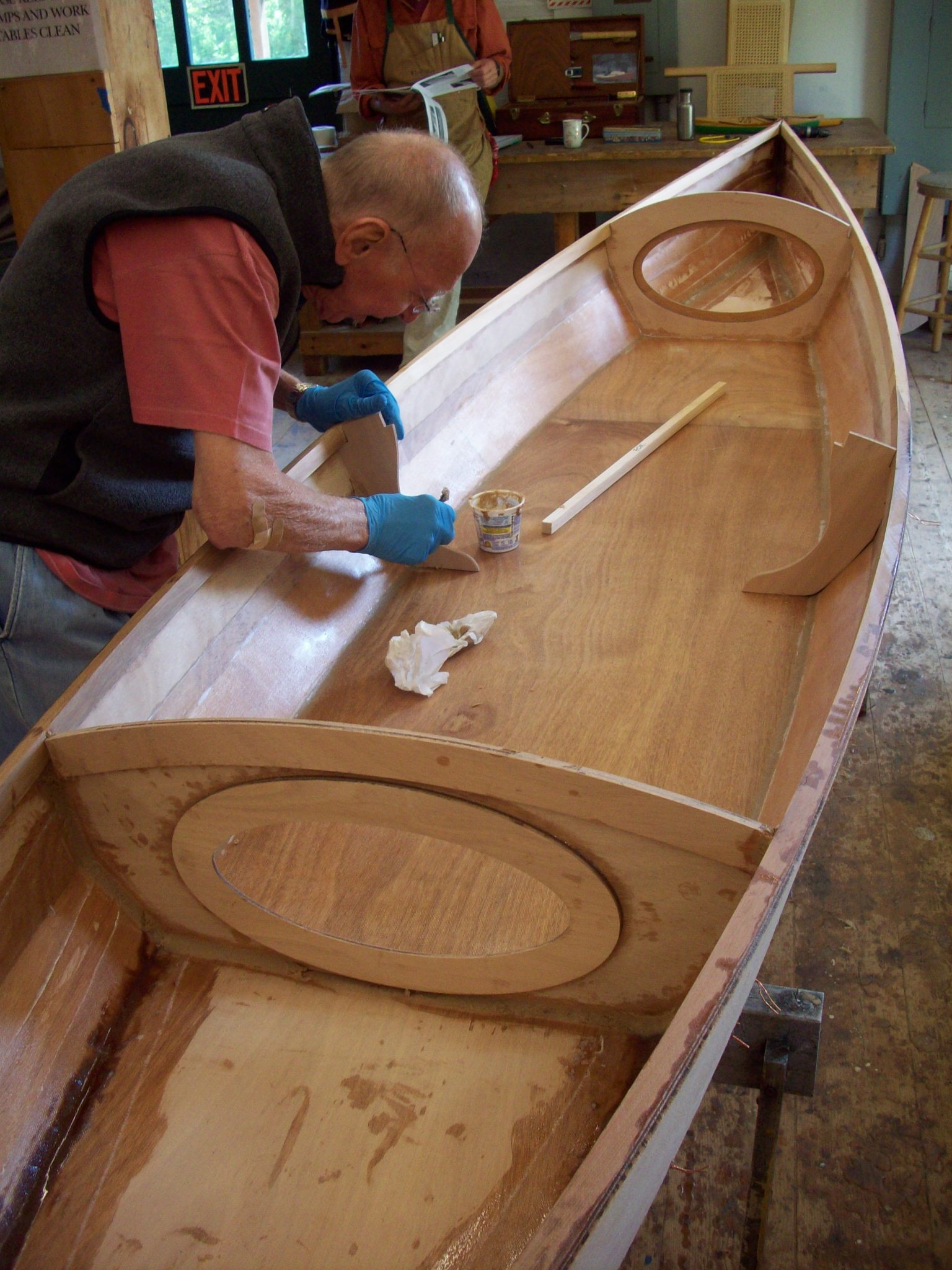
There is also a class in traditional skin-on-frame kayaks where frames are assembled with no mechanical fasteners then covered with a skin of ballistic nylon. I’ve seen many of these kayaks being built under the guidance of Mark Kaufman. You can pick up the finished kayak with one finger but they retain extreme hull durability.
There are also many other classes available at WoodenBoat besides boat building – woodcut art, bronze casting, diesel mechanics, pond yachts, lofting (traditional boat drawings), sailing, coastal camping, oar and spar making to name a few. Check out the school’s website for more information.
After years of woodworking, I found that boats are an entirely different animal. There are no 90° angles on a boat, so proficient use of hand tools is a must. Power tools are used, but many times the quickest, most efficient way to do a process is with a hand tool. Block planes, spoke shaves, chisels, and draw knives are commonly used on many boats. Using my father’s and great grandfather’s tools has been a joy for this power tool junkie. Each time I pick one up I feel that I’m somehow connected to them in a spiritual way as they are no longer with me in a physical sense. I have learned to leave the cheaper quality tools at home in the bottom of the tool box and grab a quality Lie-Nielson (made in nearby Warren, ME) or older Stanleys whenever possible. If you are in need of quality used tools, there are many stores in the area that specialize in that market. I spend way too much time at the used tool emporiums in Liberty, ME, always looking for a usable, older quality tool at good price.
I realize that I kind of sound like a salesman for the school but I’m really just a student who had such a good experience there that I want to pass the word. If you don’t believe me, ask any other person who has attended WoodenBoat and you’ll get the same story. For me, the bottom line is that I learn so much in each class that I want to keep going back to learn more. I have been so enamored with these boats that I’m registered to attend The Great Lakes Boat
Building School in Cedarville, MI, after I retire from teaching this year. My interest at this time is to specialize in historical reproductions and repairing older wooden boats that sailed along northern Lake Michigan and Lake Superior shores.
Epilog – I now (so far) have four wooden boats, all needing my attention. Retirement’s going to be good.
To learn more about WoodenBoat School and view their course offerings, check out their website at www.thewoodenboatschool.com.
I am cold moulding a 30’ 1957 Chris Craft Constellation. The hull is carvel planked and was solid. I chose to cold mould the hull because I live inland and plan to have the boat in and out of the water. I am completing my second layer of 4mm okumi on the bottom side. The port and starboard sides have 2 layers. I am questioning if I should adhere a third layer on the bottom prior to glassing the hull with 6oz cloth. Thoughts.
Just to give you some follow up. I took a course with Greg Bauer again this past summer, first time with him since our first course together. It was interior joined and he did a great job. I am in the middle of building an Adirondack Guideboat from scratch. How has it gone with your new career. We miss you in Brooklin. Robin
I have been watching on You Tube a series on wooden boat construction. This craftsman is building wooden skiff step by step. He is located in Mass. I believe. He has a wonderful NE accent and is very precise with instructions, methods, and especially materials along with their different applications. I have been enamored with his series and cannot wait for the next video to come out. I am retired now for a few years, and if I want to build a boat I had better get going before I get to stoved up to do it. It is a beautiful craft to learn.
Been there. Done that. Going to do it again. Every year as long as I can. A wonder-full place and a wonderful experience.
I always in joyed woodworking,,and boat building..now I'm retired. Looking at it as a hobby
very nice and detailed information , thanks for the education
Wood boat program sounds great! Am starting my first boat project, an Aqua Riva 27'.
Great article! I love working with wood. Not to sound like a heretic, but does anyone know of a similar school for fiberglass boats?
love wooden boats plane on building a glen-l marine boat soon
Looks like a fantastic program for the woodworker boatman