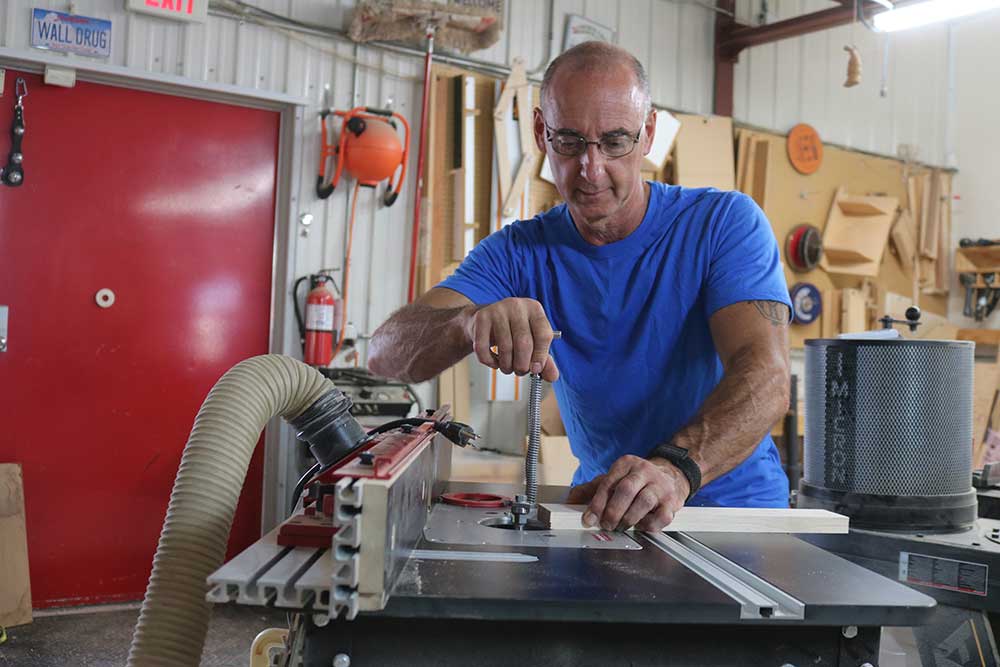
Choosing the Correct Screw Pocket Screw
George VondriskaDescription
When it comes to assembling woodworking projects seamlessly, few methods match the efficiency and durability of screw pockets. However, the success of your woodworking venture heavily relies on the precise selection of screw pocket screws. These screws aren’t mere components; they possess distinct characteristics that render them tailor-made.
Screw Material Matters
Selecting the right screw material is the cornerstone of a robust screw pocket assembly. Stainless steel screws, for instance, offer corrosion resistance, making them an excellent choice for outdoor projects. On the other hand, hardened steel screws provide exceptional strength, ideal for heavy-duty applications. Understanding the nuances of screw material empowers you to choose screws that stand the test of time.
Sizing Up the Situation: Length and Diameter
Screw pocket screws come in various lengths and diameters. Precision in sizing ensures a secure and reliable connection between the joined pieces. Opt for screws that provide ample engagement with the adjoining materials, promoting structural integrity. The versatility of screw pocket screws lies in their adaptability to projects of diverse scales and scopes.
Crucial Thread Considerations
Beyond screw selection, the thread type is a pivotal aspect of screw pocket assembly. Threads determine the grip, stability, and load-bearing capacity of the joint. Navigating the labyrinth of thread choices requires attention to detail and a comprehensive understanding of project requirements.
Fine Threads vs. Coarse Threads
Fine threads offer increased thread engagement, resulting in heightened grip and resistance to loosening. These threads excel in hardwood applications, where the material density demands a secure hold. Conversely, coarse threads are suitable for softer woods and plywood, providing quick and efficient penetration.
Tapping into Self-Tapping Threads
Self-tapping threads simplify the assembly process by creating their path as they’re driven into the material. This reduces the need for pre-drilling, enhancing efficiency. However, matching the thread type with the material is essential to ensure optimal results.
Other Screw Content
If you enjoyed this video tutorial on pickin the perect screw pocket screw,check out these other informative videos on screws. These videos offer a wealth of information and tips to help you improve your woodworking skills and achieve better project results.
Free Videos:
- Using Screw Pockets and Screw Pocket Jigs
- Understanding Different Types of Screws
- What’s the Deal with Screw Pocket Joinery?
- Easy Pocket Hole Joint Assembly
Member Videos:
Unlock Your Woodworking Potential!
Sign up for our newsletter for endless woodworking inspiration! Become a member today and gain access to a world of craftsmanship.
Any idea why Kreg went to the zinc coated screws instead of the black oxide ones?
The other thing that's obvious with the "do not use" screws is that the threads go too far up the shank, inhibiting the drawing of the joint together. Just another reason not to use them. "Friends don't let friends use drywall screws in furniture."
George, I assembled a Hickory table top using pocket holes. One problem I ran into was the screw heads breaking off once they were driven into the adjoining board. I then used a lubricant and although less screw heads broke off , I was still breaking them. I tried an impact driver and also a cordless screwdriver with a clutch with the same results. My question is that with a wood as hard as hickory is there a way to pre drill the adjoining board at the proper angle to match the pocket hole? I plan on using some Ipe lumber on my next project using pocket holes but I'm afraid it may be even more difficult. I used Kreg brand fine thread screws in the hickory table project.. and advise is greatly appreciated and thanks for all the informative videos. Paul G