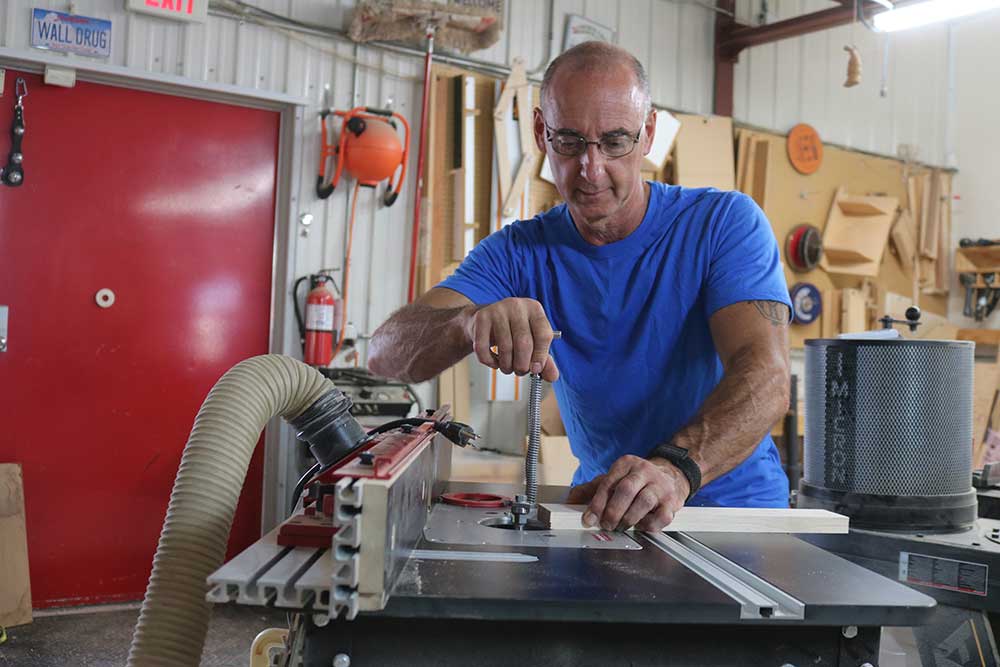
3 Useful Raised Panel Router Bits
George VondriskaDescription
When it comes to making raised panels for doors, it’s hard to beat the work that can be accomplished by raised panel router bits. You’ve got choices; vertical panel raiser, horizontal panel raiser, or horizontal panel raiser with back cutter. Your selection could be based on your woodworking project, or on what type of router table set-up you have. Here’s some buying advice that will help you choose the panel bit that’s right for you.
Tooling
Raised panel router bits must be used in a router table. In addition to learning about the different styles of bits, this video instruction from WoodWorkers Guild of America provides great info on what it takes to set them up, helping you learn how to use a router table. Your bit selection can be limited by how large (or small) a router you use in your router table, and we’ll provide the info you need to determine which of these bits your router can handle.
The Ever-Versatile Router Table
Raised panel router bits aren’t, of course, the only thing your router table can do. A router table is one of the most versatile tools in the shop, stressing the importance of learning how to use a router table properly.
There are a variety of ways to do raised panels here on the router table. So let me give you a quick overview of some different bits that are available. We'll start with this guy. This is what's called a vertical panel razor. What we'll do when we're ready to use this is get it in the router collet, and then oddly enough, all of our panels are gonna feed past this vertically.
We're gonna control the depth of cut and our final dimensioning by controlling the position of the fence. Big advantage to these is that we don't have to worry with this cutter about having a large horsepower or high amperage router in the table that has variable speed. I'm gonna talk more about that in a second. One of the disadvantages to this is that we can only do rectangular panels. We can't do an arch top panel and of the three that we're gonna talk about, I find that this one has got the least good cut quality coming off the router bit.
Big advantage though is that we don't have to have the high horsepower, low RPM router in the machine. Another style is a horizontal panel raising router bit, maximum diameter for these cutters is usually about 3 1/2 inches. When we go to these larger diameter bits, we have to have a router that's capable of running at a lower RPM. In other words, we got to have variable speed. Additionally, you're gonna want a router in your table that's at least 12 amp.
That's about 2 1/4 horsepower, 15 amp, three horsepower is better. With these cutters, what I usually do is position the fence so that it's even with the ball bearing and the bit. And then I control my depth of cut and my final dimensioning by slowly raising the bit through a series of passes. So making progressive passes, taking off more and more material, until the panel looks the way I want it to look. With both of these cutters, as you work on the front of the panel, what you're gonna have to control is either the fence position or in this case, the height of the bit to leave just the right tongue or edge on the edge of the panel so it fits into the groove you formed in your doorframe.
On this cutter, this is a horizontal panel razor. It's still 3 1/2 inches in diameter with a back cutter. The distance from the upper cutter to the lower leaves in between exactly the amount we need, typically a 1/4 inch to fit into the groove that we make on the door frame. So with this one, I don't have to worry about the height of the bit or the position of the fence to control that fit. It's gonna be automatic coming off of the cutter really regardless of the thickness of the panel.
So for me, I find that this one is the easiest way to produce a panel that's a great fit for my frame. If we go back and look at what we've got here with our vertical panel raiser, again, I would use this if I had that lower horsepower, lower amperage fixed RPM router. If I do have variable speed, higher amperage router, I would go to one of these two. For my own woodworking, honestly, I can't see why I would use this. The absence of the back cutter means you have to control the height of the bit in order to achieve that perfect fit, where with this cutter, it's gonna automatically happen for you.
So as you might be able to tell from this, for me, I'm a big advocate of using the horizontal panel razors with back cutter because of all the advantages I've talked about there. End of the day, all three of these in your router table provide great ways to do raised panels.
This would have been much more useful and instructive if a practical demonstration showing the achieved patterns was shown.
Great information about the router bits but next time please show a finished cut of each of the router bits.