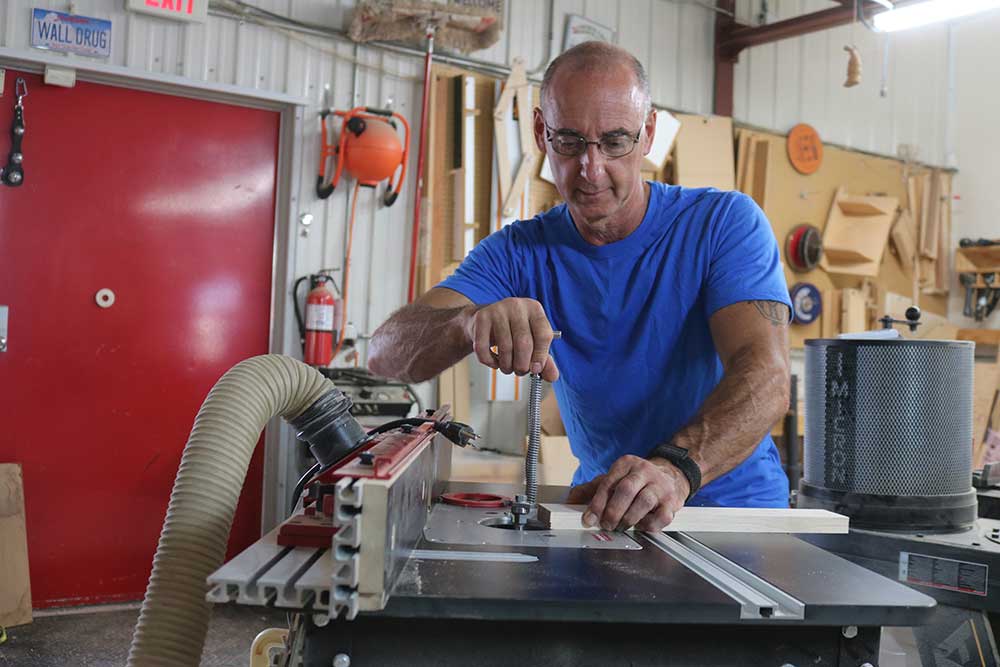
Air Drying Wood Slabs
George VondriskaLogs are cut and converted to lumber while the log is still wet, commonly referred to as green, and the material needs to be dried before it can be used in your shop. Air drying wood slabs is a really low tech way to dry lumber.
Prep
Before stacking the green wood paint the end grain to seal it. End grain is very porous and, if it hasn’t been sealed, moisture can escape from the end grain too quickly, causing the wood to crack. You can use left over latex paint or end grain sealer for this.
Moisture content
MC (moisture content) is expressed as a percentage. 30% MC (not at all unlikely for a freshly cut log) means 30% of the log’s weight is made up of water, 70% is made up of wood. Air drying typically brings MC down to 12-14%. Final moisture content shouldn’t be guessed at. If you’re going to dry wood, you really need to own a moisture meter.
Making the stack
Air needs to be able to flow over each board and throughout the stack. Use stickers to provide space between each layer so you have good airflow. Some woods, like maple, are more susceptible to stains from stickers than others. The safest way to avoid staining is to make the stickers from the same material as you are air drying. Stickers should be spaced about every 16”, and should align with each other vertically to prevent sagging.
Timing
A rule of thumb for air drying wood slabs is to allow one year per inch of thickness. Some environments may demand more time. Use a moisture meter to check the material.
Check out this great article for more insight on air drying wood.
I have been cutting some slabs... On my chainsaw-based sawmill, and the next step with them is to be really, really, really patient, because I'm gonna air dry these slabs. So let's talk about that process. Air drying means I'm gonna stack 'em up and I'm gonna forget I own 'em for probably two years, 'cause these are all about two inches thick. General rule of thumb is a year per inch of thickness.
Some people, depending on where you live, will say a year per inch plus a year. The answer, to get that really figured out, is you got to own a moisture meter. So when I meter these and they get to a point where they're probably gonna be somewhere around 12 or 13%, so you hit 13%, and it's 13% this month, next month, the following month, in other words, it doesn't change, you've got 'em as dry as they're gonna be. But in an air drying process, that takes a while. Comparatively, kiln drying is really fast.
That could be as short as three or four weeks instead of a couple of years. One of the benefits to air drying is it's really low-tech. I put 'em on a pallet, I stack 'em up, we'll talk more about that, and I just forget I own 'em. As far as keeping the pile dry, different people have different solutions to this. Here, we're inside a building.
An alternative is, put a sheet of plywood over the top, or maybe some old metal roofing, just something so that if it's gonna live outside, it can shed water a little bit. Even a tarp is okay for that, but don't drape the tarp down the side. We just want, like, a roof. We went a little rain cover on the top. This is a pretty perfect environment.
They'll end up against a wall over here instead of in the middle of the room, but the environment is nice because there's a lot of air flow in here, there's a roof over the top, so they're not gonna get rained on, they're not in full sun. We want 'em to dry, but we want 'em to dry slowly. Drying stuff too fast is part of what leads to cracking, and then also a lot of internal stress. You might've run into wood with internal stress if you've bought home center lumber and you rip it on the table saw and it does all sorts of funky stuff. We don't want that here.
So if it's gonna sit outside, that's okay. A lot of people will put a tarp over the top layer of it, or a sheet of plywood, or a piece of metal roofing, and that's just to help deflect the rain a little bit, so that can work. Now in this category of drying but drying slowly, couple things there. Notice that on a lot of these pieces, the bark is still on. If the bark stays on, like this stuff did when you cut it, leave it on.
That acts as a skin that helps inhibit the drying process a little bit. On the end grain, they're all a really pretty shade of green. Who cares that they're green? That's just leftover latex paint that I had. And I put that on the end, ' cause end grain looks like a bunch of pipes, like a bunch of soda straws.
And what that paint on the end is gonna is slow the rate at which moisture can leave the end grain. So it's another important aspect about slowing that drying process down. Now, when you stack them, you don't want face to face to face, 'cause we have to have air flow. So that's the deal with these things, which are called stickers. Couple of things are important about the stickers.
They need to be something that plays nice with the stuff that you've stacked. This is maple, the bottom pile is maple. Maple in particular seems to be subject to sticker shock, which is if you use the wrong specie for stickering, it can stay in the material and stain it pretty deep, and you have to plane a lot of wood off to get the sticker stains out. So in this case, I've used birch veneer plywood, which tends to be a good benign middle ground for stickers, non-reactive to most species, but it's a good thing to double-check with your pile. Make sure your stickers are compatible.
One good way to do that is, all of these had slab wood that came off the top. If you cut the slab wood into stickers, you know you're safe, because if the log was maple and you cut the stickers from the same maple, they're gonna be okay. The other thing that's important about the stickers is that they line up with each other. Lot of weight here, or to a lot of way down there compared to up here. So if the stickers aren't lined up with each other, especially on four quarter lumber, it's possible that we introduce a deflection.
We're gonna put a bow in it, just like bending a piece of wood while it's wet, and then when it dries, it's still got the bend in it. Same thing can happen here. So having the stickers one over the other is gonna keep that load vertical, vertically aligned, so that the parts stay as straight as possible. In all honesty, with this eight quarter stack, I've overdone it a little bit on stickers. I've got 'em every 16 inches, and on thick stuff like this every 20 or 24 would have been okay, but too many stickers is better than not enough.
And what does plywood cost? So I'd rather have extra stickers in here than not enough stickers. They're on a pallet. The substrate that you set them on, that's important, 'cause it needs to be nice and straight, nice and flat. Again, otherwise you can introduce a twist or a bow or a cup to the pieces if the thing down here is kerflooey, and you'll end up with a whole pile that's kerflooey.
The ratchet strap I was messing with when we started, that's gonna do a couple things. When my friend Charlie comes in and moves this and pushes it against the wall with a forklift, that's gonna help keep the pile together so nothing bad happens. Additionally, you can put weight on the top to help keep this thing weighted down so the very top pieces stay nice and flat, or you can put ratchet straps on and they have that same net effect. So a lot of different ways to approach this. Bottom line, what I like about it is it's low tech, so this isn't costing me a dime to do.
Downside is you're gonna wait a really long time to get the usable material out of this. But as long as you keep that pipeline full, then as time goes on, you'll always have material ready that's been air dried. So simple process, but make sure you do it right so the lumber that comes off the pile is stuff you can use.
Would it be better to maybe put stickers under the straps to prevent bleeding?
I understand what you meant about the cost of using plywood for the stickers but, have you checked the prices of plywood lately? Good article. I had not thought about using the offcut scrap as stickers of even the ratchet straps for the needed pressure.
Truly enjoy your tips and tutorials. I always gain something new or I'm reminded. I have currently purchased a WoodMizer portable Saw Mill so I have been studying up on the drying process. Grey info on the process but I really had to laugh out loud when you were describing stickers made from plywood, " how much does plywood cost anyway?" ! Well let me tell ya.... Thanks again for the info you guys put out there !!
Although it may seem obvious to many it won't be to all and that is one minor oversight in the video. You did it but you didn't say to make sure the ratchet straps are aligned with the stickers. Dave out
How long do you have between the time the slab is sliced, to stacking it up for drying? I'm assuming, as quick as possible, but what if it's in a area where you can't retrieve it all or some other reason for not being able to stack it immediately.
Would you do anything different if you were trying a soft wood like Western red cedar or ponderosa pine?