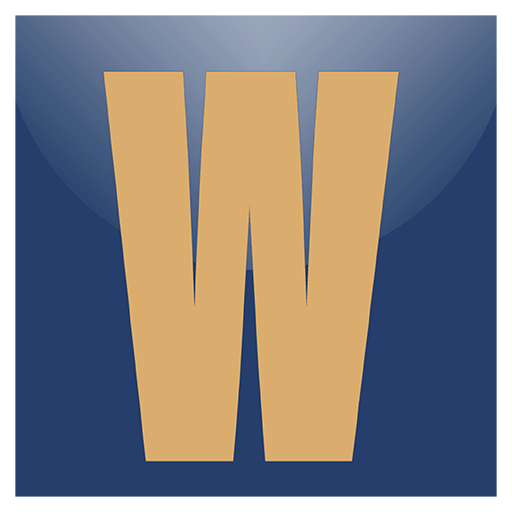
Battle of the Bowls
WWGOA EditorsDescription
The bowl blanks
George had a couple pieces of walnut that had been cut from the same log. Not just walnut, but a couple lovely pieces of walnut crotch. These two pieces could be incredibly beautiful. And, because they were cut from the same log, Rob couldn’t complain about getting a lousy piece.
Turning techniques
Rob and George both scrape and shear, but for this challenge they decided George would shear and Rob would scrape. The means George is using bowl gouges and Rob is using carbide chisels.
Finish
Rob brought an interesting finish along; it’s a CA (cyanoacrylate) glue product. It left an amazing gloss on his bowl. George went with the Mylands Friction Finish that he’s used on many of his turnings.
No, no, no, Rob and I are both avid Bowl Turners. He's been in the shop this week doing some other, you know, important video stuff, but now we're gonna have some fun. We're gonna have the battle battle battle the century. Oh OK. Um So here's what we've got, move your hands so uh to keep everything even, you know, so nobody can complain about being unfairly treated.
These are two pieces of crotch walnut that were book matched cut from the same tree. So they're basically identical, except for me in reverse image, they're identical sister pieces. Um So what we're gonna do is from here, we're just gonna cut loose and he's gonna go do stuff with his and I'm gonna do stuff with mine. And then when we're done, the crew will pick mine as the best, I'm sure. Um So this is just gonna be fun and a chance for you to just kind of watch as we go and see what we do and how we do it.
Part of that is you're scraping right and use all carbide tools and I'm gonna sheer. So I'm gonna be on bowl gouges um for the whole thing. So you'll see two different approaches to technique on that. And other than that, any other smart, I mean, um clever comments. Well, I was gonna say that just because we say we're avid turners doesn't mean that we're professional expert.
I have a lot of things I like doing that. I'm not good at doing and this is another one. All right. I think uh I'm fixing to cut mine round first. So let's see.
You wouldn't wanna be uh what I mean? And you gotta just scream if you need stuff, Rob like, OK, never mind. You're, you're already ahead of me. So, what I'm doing is I, I keep these circles that I fan saw cut. So when I'm gonna do a ball, I can lay that on there and see.
Oh, is that giving me, you know, I wanna optimize the figure. Um That's obviously too much small. That's too much big. So this would give me an idea before I go to the compass of what do I wanna get out of this? And of course, George didn't share anything with me, so I'm here doing it the hard way.
Yeah. But you know, that's all right. I'm not a complainer. Well, I'm not a big complainer. Oh, there we go.
Don Don. It would be fun. All right, Rob is hogging the tools he's in the band saw. So I gotta wait for him to be done. But I'm taking a slightly different approach, which is, here's my circle, but I'm gonna leave.
I want that little live edge to show when I'm done. And as I'm turning, if it's not working out, if it looks weird or it's busting or whatever, I'll just cut this down as I turn to a smaller circle. But I think it'd be kind of cool to leave some of this showing on the outside. What I'm doing. So, this is the first time I've ever used a bandsaw liar.
So, so. Oh, that's how you turn it on while I'm waiting for Mr Noisy over there. I can get my face plate on that won't interfere with the bandsaw work. So I found center just by measuring. I'm eyeballing through there on to that center line.
I like sheet metal screws for putting the face plate on because they have deep threads. So they get a good bite in the wood. So George gave me a drill without any battery power, but that's all right. I'm the first hurdle baby. I, I, you know, I can, I can make this work.
How many screws did you use? Charge? I couldn't describe them. Gave me the wrong size face plate. Did you?
Yeah, I actually checked my, I actually tested my face plate on my, on the, on the lathe. It's just a test run. I'm gonna be smart like Rob and see if it fits first. That's the first time anyone said that I'm gonna be smart. Like Rob.
I kind of liked it. I've never used this lathe before. How important could it be? It's not exactly zero, but I can live with it. Huh.
Like me. It's just slightly eccentric. Right now. When I first met Rob, I was the Tools and new products editor for American Whitaker magazine. He was the editor in chief for Whitaker's Journal and that meeting was probably 20 years ago.
So we were, we crossed paths all the time because we were going to tool shows. Uh We were meeting at events like that and he lives kind of in the area. I'm in western Wisconsin. He's a little bit west of Minneapolis, ST Paul. So geographically, we'd also run into each other that way because we live kind of in the same place, relatively good to do, stop that.
You know, I made it a point. I'm an expert wood worker in a lot of different ways, but I've made it a point of not being an expert wood turner because then it wouldn't be as fun. Well, George and I have known each other for quite a while. And so, and when he suggested we do something together, I suggested something ridiculous, but he thought maybe the bowl challenge would be good. So I was looking forward to it.
I love to turn uh, bowls. I'm not an expert, but it's what I do for fun in the woodshop. So I was aimed, done. Ok, I'll do some more low, low piano. That's a pretty big chunk that came out.
So, when I knew Rob was coming, um, he's gonna be in my shop a couple of days and I like when outside people are here to find something that we can both do together. So, in other cases, we've made stools and other cases, we've made knives. So with Rob, we're both bow turners. So that was a good project where we have a middle ground to meet on and uh, something we could both do. I'm working it.
I gotta get rid of this little guy here. It doesn't look pretty. So the downside to leaving this, that's that chunk, chunk, chunk, chunk, chunk because I'm, I'll never get it perfectly concentric. So I'm always gonna be cutting air a little bit right there. Um But as I get this rounder, I can run it faster and that's gonna help eliminate a lot of that.
Oh, baby. Now we're talking, now, we're talking, it's a really nice lead. Don't you have any higher R PM over there? Dude, I could, I could make it go faster. But, um, but right now I'm just staying, you know, just at 1700 you know, way to the danger zone.
I feel I feel the need poor speed. One of the downsides of the scraping or the shearing is that I think you tend to get some tear out on the end grain. So you need to get in there and touch it really lightly. Oh, I got a flash spot still here. Good thing I saw that.
All right. Still got a flat spot. I think this is, I think this is sharing the end grain a little bit better. At least that's what I'm telling myself. How's it going?
Cowboy? You know, I'm making some progress and I'm making some chips. You're further along than me. I got a flat spot that I'm still working on. Oh, I saw that but, you know, you know, and a soft spot.
Yeah. But, um, so it's a nice shape but I'm, I'm having some trouble with tear out and, um, well, you're scraping, that's the problem. So I gotta do it very gently. That works. Yeah, it's, I like the shape a lot.
So, and now when it comes to up chucking, when it comes to chucking? Are you a bellybutton guy? Are you an Innie or an Audi? Yeah, same for me. So, um, the deal on that is with these four jaw chucks.
You can put a tenant on the bottom and grab an external or you can do a recess on the bottom. My favorite subject at school and then you can expand into that with the jaws. So he and I are both gonna, it sounds like end up with recess. That's right. That's right.
All right. And do you need any tools while I'm distracted? And over here, you know, if you have some 60 grit, sandpaper. I might, I might be, need, need some of that. We'll find, we'll find some.
Sometimes it's easier to see the shape that you're carving on the back of the bo bowl. Here, it's going up against the white tile. So I can see the, the shape of what parts I want to refine. So it's kind of cool. I'm getting what I want out of this.
There's that live edge and I wanna leave that and I can't decide is that gonna affect my wall thickness? In other words, do I gotta leave the wall so thick. I don't blow through that or maybe I wanna come through it from the inside. I don't see when I get to the inside, but for outside shape, I'm pretty happy, I'm gonna see if I can get a better pass to clean this up. So less sanding my, my shearing is going OK?
Not great, but I'll try to get a clean up pass on this before I san gonna ride the bevel baby. That's way better. Very little sanding there. You can see there's a little bit of a dovetail on this. So I'm shaping the inside of the mortis to so it'll grab that dovetail a little bit better.
80 grit again, trying to get rid of this tear out here using a sandpaper. A really good turner could just scrape it smoothly. That's why I'm standing. If you're wondering if this gets hot enough to burn my fingers. The answer is yes.
Yeah. Ha ha ha. One more time getting very close. So there's my pencil line there. That's the edge of the recess.
And for most chucks they want that to be slightly dovetailed to be angled like this a little bit. So it's undercut there and that will accept the jaws a little more firmly. I think you're doing, I think Rob's doing the same thing. Did you, did you kind of dovetail inside your recess? I did.
I'm surprised you couldn't hear it. Cooing. Yes. All right. Right.
Size could be a little deeper because I'm only maybe halfway on those jaws right now. Some tear out here. The idea behind a ball. You, you can have a foot or you could not have a foot, you can uh shape it however you want. Um I like a couple of, uh, I like to add a couple of shapes because then you can get some dimension when you're looking at it from uh further away shadow lines.
And I like that recess to be just a little bit convex or sorry, concave right in the middle. So I've got a nice flat there. The jaws will make contact with that, but just that little, I don't know, it's a nice touch if somebody turns it over and looks at that and for jaw depth, yeah, we're OK. We want, you want this to bottom out in the recess, not this to bottom out against here. This is the critical spot.
Yep. S word. Gotta do some sanding. I wish my sharing had gone a little better. I should be able to get a better surface finish, but I'm a little out of practice.
So I'm gonna cover a myriad of sins with sanding. You say you've been so sinning over here. Quit looking at my stuff. That's a nice bowl you have there, buddy. Thanks.
Yeah. You know what, you know what it is right now. That's a bold movement. Uh Yeah. Well, I, I have nothing to say and that's unusual.
Yeah. So here I am all by myself in Wisconsin. George asked me here to do some highly technical, you know, hand playing videos. But now here I am turning and George is talking about his bowl movements. Never had it so good dude.
License there as Hemingway said, life is cruel and one must learn to endure it with courage. Do you want a thingy? Huh? A thingy or are you happy with what you're doing there? I think I'm happy.
I mean, I was complaining a few minutes ago about your bowl movement, but now I'm happy. All right, a little bit of sanding. Let's see what we gained. So I'd like to get those tears out. We have a little bit of a time constraint.
So I'll spend a little more time standing on the outside and go from there. Are you gonna want to put, finish on that outside before you spin it around. I am and I brought a secret weapon. All right, in terms of finishing, I've never used it before. So you don't need me to get stuff for you.
No stuff then I don't care what you're doing. Well, yeah, like that's gonna change with the finish. Yeah. So the other thing I'll do when I have some especially bad spots is not run it with the machine running, but just spot sand like that. You know, George, I have a dog.
Were you aware of that? Leroy? Leroy the other day, Leroy ran through my screen door. You know what happened? What happened?
He strained himself. It was terrible. So this is not, the late is not on the disk is causing the ball to turn, which is also kind of a good way to sand this. You get that little bit of motion, putting a rubber glove on, uh, you need anything checked out. You stay on your side of the shop, stay in your lane trying to be helpful.
All right. As I said, I haven't tried this product before. It's ac A it's AC F finish. Are you covering the bed in my lathe, please? I am.
Thank you. It's a CAA finish and we'll see how it works. It's supposed to stay, it's called fill and finish and it's supposed to stay liquid until I spray it. So will it, I think so. I'm not gonna do this.
Mhm. This is the ultra thin version. They have thicker versions, recipes. I suppose they would be. I thought this might work best for this.
And now comes the magic. We hope completely dry. All right. This is 180. I just did 100.
That's too big a jump. So I'm going to go get a sheet of sandpaper. I'm gonna burnish this. Uh, now with, um, this just this paper towel and then I'll go back and put another, another coat on. Furnishing means rubbing, but really fast.
It's pretty nice. I do want to put one more coat on. See how that works. I can recommend it. And they got your inbound, inbound.
Sometimes when you follow up another code of C A right after you put on the first one. There's enough of that reactant to make it just dry and your rag gets, gets put on, gets glued to the peace. But so far I've avoided that. I like it. Oh, I'm gonna back up a grit.
Hit that again. So we got the bottom down. Got a nice finish on the outside. I'm gonna spin it around. Put a chuck on there.
What are you doing? R I'm I'm chucking it up. I'm up, chucking. You're ready to go on the inside, huh? I am.
I am. I'm an inside man. I, I dovetailed that little mortis. There's a little dovetail on the uh jaws and so now it's in there grabbing on that and I'm gonna tighten it up. So with any luck it stays on the lathe, that's our goal.
All right, it's go time just gonna put a little registration line here to hopefully, uh, align the uh affix where the lip will end. It's my hope to do kind of a closed vessel, but I've hoped a lot of things in my day, we'll find out, gonna get some finish. So I like to put it on with the lathe, not running to make sure I get every spot, but this is a friction finish. So for it to really shine up, it's gonna have to have friction, which means running, running the machine once I have this wet and always with paper towel because because once this is running, if this catches paper towel will tear, a rag, could break my finger. What are you using over there?
It smells like it could get somebody high little friction polish. I think it's pretty heavy on Shellac. I'm trying all these different kinds of scrapers. I got Rockler, I got woodpecker. I got.
What's the other one? Easy, wood, easy wood tools are my favorite. But um, just seeing if there's any difference. All right, little higher R PM and a little polishing. Now, I'm trying to roughly follow the outside curves of the ball on the inside.
We'll see how successful that is. All right, that's ready to come off the spindle. So I'm locking the spindle on that end. It's like an unscrew, don't forget to unlock. Otherwise it's a bad day.
Ok. Just a little bit more scraping and then a lot more sanity and, and I'm looking for short grain tear out. There's a, there's the crotch, uh, wood that comes up here. So the, the ends of those fibers are just straight up and um, sometimes they can be a little challenging to get smooth, especially in this world, someone who isn't, you know, Ernie K over. So when I mess with the speed, I'm looking for the spot where the lathe starts to jump.
I don't want to be there. So I'm, it's the beauty of a variable speed lathe. Like this is, I can just dial up that dial and when it starts to really jump, that's too fast. So like what R PM am I at? I don't know, but I know that at that speed it's not jumping and a little bit faster.
It is, see how we're looking where trouble spots are. There's a trouble spot, although the rim is looking much better than I expected right in here and right in here we have some issues issues. So I'm using just the tip of the chisel out here to establish the wall thickness, got to be real careful if it catches, it's gonna skate and blow the wall. And once I've got that shoulder established and I'm coming around, I can be a little more aggressive. Right.
I'm pretty confident. I'm not in danger of trouble yet, but those are the famous last words of the person that turns their ball into a funnel. Remember we've got that recess at the bottom. So this, well, let me do this and right there in that part of the bowl, it's still that thick. The recess is cut in about 5/16 of an inch.
So I got to allow for that, but there's plenty of meat right there still. You're scaring me, George. That's a noisy, but that's really noisy. So it's kind of cool. You know, you can listen to the ball and know where you're at.
Then thicker after you're done with one grit, like I was using 80 grit there. Then the next step up, go pretty fast. All you're doing is removing the previous sandpaper, sanding marks. So it goes much faster, doing a little, we're doing a body fat test today. Yeah.
Yeah, you're doing all right. Oh, well, not according to my wife. So I'm trying to, I'm trying to think, oh, that's gonna take a while. I know that bark inclusion is right there. So I gotta be careful like this is plenty thick.
I normally turn down to a quarter inch wall thickness, but right there that's really thin. So I think I gotta leave all of that, a thicker wall just because of the bark, which is worse than its bite out here because now I've decided I don't want a hole going through. So I think I need to be done. Now, I just need to sweep off the bottom. Now, you can see why George is worried about his LA bed.
You can just tell by that sound. Get it so thin right there. Getting a little heebie Jeebies. Me too and I'm way over here. So my other consideration on this was this chunk, the pith on.
It was a little weak. So I, I had put some epoxy into both of these pieces to stiffen the wood up a little bit. But I think I don't like how thick the bottom is right now. I also don't want this to blow apart into a bazillion pieces. So I think I'm just gonna clean this up and I may actually scrape that to clean it up with a bull gouge.
There's quite a bit of pressure. Um So I don't want to lean on this anymore than I already have. So I'm gonna grab a scraper, clean up that and Incent once again gonna burnish with a paper towel. I then to ST blood. I need to get, I've got uh almost glued my hands together.
Wanna be the first time we got a dry spot or two in here. That's a sharp chisel. Oh That smells and no, it's not the sauerkraut talking. OK? I was gonna say that would be a good Lynyrd Skynyrd song.
You know it smells OK. I got a couple of smooth marks on here. So I've got some 600 grit paper. I'm gonna try to just gently take those off and then I'll reapply. I smoothed that out, but I roughed this edge up all this kind of thing.
Like I say, I'm not expert with the C A finish, but I'm really liking it so far working out for me. Oh, that's cutting nice. Suck a three quarter inch. But remember in that recess is there takes away another 516. I think I'm gonna be done.
Uh done. Well done. Gouging. I got sand a bunch. Um, tool selection.
This is a big surface. Look at the crotch right there, man. Um So this is an inch and a quarter round nose scraper. Could you do it with like a half inch round nose? Yes, but a bigger chisel, it makes it easier to ride over the high spots and level everything out, which is what I'm trying to make happen here.
So I'm gonna suffer from just one more pass syndrome because it's just a little dug right there. I'm gonna see if I can get one good pass down that wall and across the bottom and then I really am gonna be done no matter what. I just don't wanna risk. Where's that inclusion right there? This is like I can't push it back and forth, but that's crazy then right there.
Hm. I have a couple of drips in here. Question. Talking about me. I got three drips in here.
Um, question is, do I try to fix it or do I not? Of course, I do very little cutting pressure. I don't want to flex that wall, but you can hear it's, it's thin, it's chattering just a little and then you can tell the bottom sticker because that chatter sound goes away. Last one. Finish that across the bottom.
Hm. What? So, normally I'm turned into about a quarter inch wall thickness. This is probably half, maybe even five eights across the bottom because I didn't want to lose it. Um, by, I am going to apply some more finish, but I'm gonna do it and a little bit more manageable orientation and then I'll put it back on the and I'll put it back on the lathe and, and burnish it out.
Hey George, I'm Dan. I could put way to Lord it over me. Nice guy could put his nuts in here. Here it is turning, went pretty well, had some challenges with the finish. Um, but I'm happy, I think it's got a nice shape.
It's uh, walnut is spectacular and I'm happy with how it turned out because I gave you the better of the two pieces. Well, I thought I was working with the one that was really pissed, you know, had kids in them anyway, turned out. Ok, you're leaving a trail. That looks pretty cool. You should see it when it's not spinning.
Do I do? I really want to, I'm gonna go get a different form of sandpaper. Ok, because I've got some surf prep, um, foam pads that'll get in here a little more better. I, I didn't bring them out for you because I didn't want you to use them. I get it.
It's hard. George is very competitive. Yeah. What can I say? I can still hear you.
Quit talking about me. Do just be, did you find your foam pads? Yes, sir. All right, I'm gonna foam home right now. Foam foam home.
Watch your fingers. It can get hot. You know how I know, gotta burn my finger. I'm pretty sure I know how, you know, I read it once in the Woodworkers journal and then saw it on Woodworker Guild of America. So if it's in those two places gotta be true.
Absolute gospel. Although both of them employ some sketchy guys about what grit are you gonna stand up to? 2 22 21? Whatever it takes, right, Mr Mom, this is 240. Um, I do wanna go, I'm gonna go to 320 on the inside here because that crotch is so crazy.
Cool. And that's gonna help that. Um, is that, is that a technical term? And then, uh, I'll throw some finish on there. So I'm caught a few.
Yeah, there's a big crack right here that just wants to come apart. Said we were hearing, here's some of there's some woodworking, a SMR right there for some. I was, I was thinking like the vulgar boatman. We need a, like a sanding song. Oh, boy.
Oh. Why? Living for thrills, baby? It would be like, 000, my fingers are in danger. The ball is getting stranger.
What you do with all that money, Rob. What money is that money your mom gave you for singing lessons. I went out and played in the, uh, in the stock market, you know? All right. What's the worst that could happen?
Do you want me to make a list or you just wanna just kind of let it, let it, let it fly. Ok, bye. All right. So just trying to be helpful. Check it up.
Oh, that's looking good. Now, eggs. This, the boards are important and you did some, you did paper towels or something, right? Your paper towels and a cloth because you don't want the schmutz ending up all over the bed of the machine. A couple of drops right there.
So, thank you. I just see if you were gonna notice that and I'll call it out or just leave me hanging. All right, I'm gonna run it and buff. It looks gorgeous. Thanks.
I like it. Last step. Furnish. You're living right on the edge there, brother. In fact, that's where the crack is on the edge.
No, no, no, no, no, no. Whoa. Nice. Crotch George. Thank you, sir.
Yep. Don't hear that often. Understandably. Hm. That's enough.
That looks nice. Thanks. You got some purples going on in here. That's pretty cool. Well, and part of what we got going here is this is air dried wood, not kiln dried wood.
So, for people who aren't familiar with that walnut cherry, if you air dry them, not kiln dry, I mean, you really get a whole different beast, whole different color pattern. They'll steam those, they'll steam it in order to get even drying. But lots of times that makes it a lot, a lot less dramatic. Yeah. And I think that, well, especially when you start to see the purples.
A lot of that is in the, uh, air dried stuff, but the finish on yours, I'm gonna have to get that product. That's, well, I had some challenges. I think I can do it much better the next time. But, you know, you live and you learn. You nice boy, you got a lot of compound curves going, which is not easy to execute.
I mean, it's easy to cut pain in the butt to sand and you did a great job sanding that stuff smooth. I, I kind of wanted it to curve in here more. Have a clothes but you know what? It's perfect. Now, you, you did a great job taking away everything that did not look like a bowl.
Exactly. Exactly. Um, well, I like on this. So that was part of my goal was to leave the little live edge thing going there. I'm gonna have to hit this.
I'm gonna spray that with some Rattle can Lacquer just because it's, I can't get the turning finish in there. So I'll hit that with rattle can. But, yeah, other than that, I did it, I think we both did a great job of, uh, capitalizing on that. The crotch that was in that wal nut happy. I'm happy.
All right. Well, thanks for playing along. It was, are we making the crew pick a winner? Recognizing we're making them, making them all that stuff up? I can tell you that.
All right, we're not gonna make the crew pick a winner, but thanks Rob. This was very cool. It was good. It was fun.
Share tips, start a discussion or ask other students a question. If you have a question for the instructor, please click here.
Already a member? Sign in
No Responses to “Battle of the Bowls”