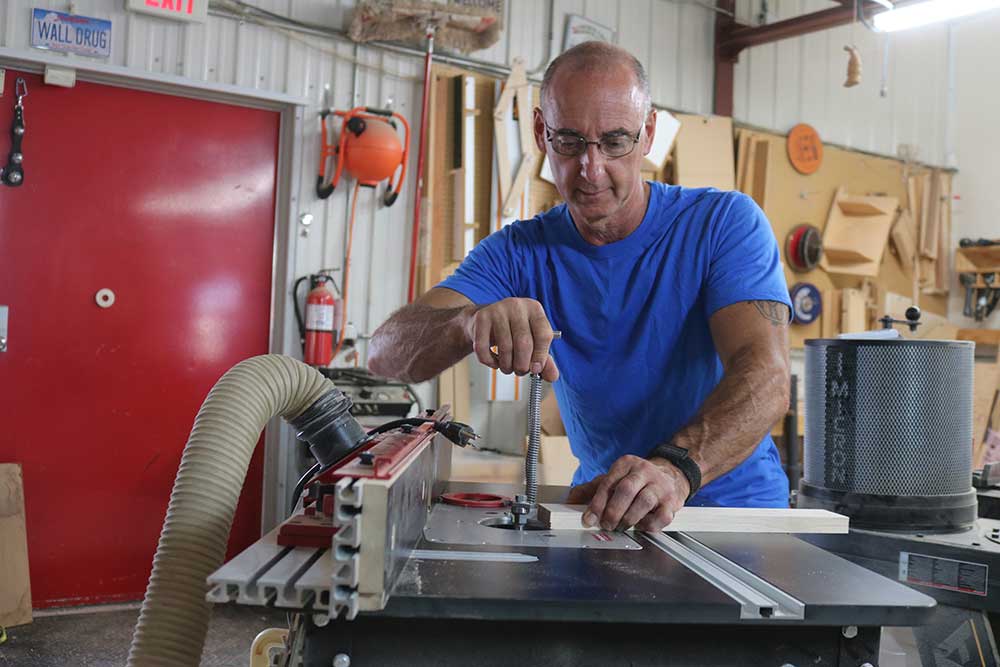
Build a Wall Cabinet, Part 3: Door and Details
George VondriskaDescription
Order of Operations
Even though a cut list is provided, it’s always a good idea to look at your projects and determine the best sequence to follow. On cabinets I build the case first, then cut and build the face frame, then derive the door dimensions. This is all shown in the video.
Making the Door
You can easily make the door on a router table using a tongue and groove router bit set. Follow the formula in the project plan to get your door part sizes. All cabinet door details are provided in the video.
Installing the door with its spring loaded hinges can be a little tricky. The video provides some great tricks to simplify this process.
Screw Cleats and Back
There are just a few details remaining to wrap up the cabinet project. Make and install screw cleats that will allow you to hang the cabinet on a wall. The ¼” thick back doesn’t provide enough strength on its own for this. You have to hang the cabinet using the cleats.
Cut the back to size so it easily fits inside the rabbets cut in the back of the case. It’s easiest if you don’t install the back until after the interior of the case has been completely finished. You can also finish the inside face of the back before installing it.
Make your adjustable shelf, and your cabinet is ready to be put to use.
Build a Wall Cabinet with Kreg Plan Download
Part 1: Build the Case
Part 2: Face Frame
Unlock Your Woodworking Potential!
Sign up for our newsletter for endless woodworking inspiration! Become a member today and gain access to a world of craftsmanship.
We're in video number three of our three part series on how to build a wall cabinet. We've already done the carcass and we did the face frame. In this one we're gonna make the door here on the router table. And we're also gonna just do some additional little details on the cabinet. We're gonna make the door with a tongue and groove router bit set.
Router's unplugged, so we can have a look up close here. With a match set like this it makes it really, really easy to do tongue and groove and the door that we're about to do. This cutter is the end grain cutter, that's gonna leave behind a tongue where it's got the ball bearing in the middle. And then this cutter is the groove cutter. We'll use that on all four of the parts, so that there's a slot, a groove that will receive the panel for the door.
Gonna do that end grain cut first. And what we need to do to get this set up is lower the bit. And what I'm aiming for here for altitude is on this piece I've marked out the tongue position. So I've got two lines equidistant from that face, equidistant from that face. And we're not gonna go straight to project pieces.
We're gonna start with scrap. So approximate the height of the bit. That looks pretty good. Then our other setup related thing is the fence location. There's a ball bearing inside that cutter that I mentioned earlier.
I'm on the ball bearing with my straight edge, bring the fence forward until it hits the straight edge and then lock the fence in place. So bottom line is face of the fence is even with the ball bearing. When you make this cut, you want a backer board so that, a couple of things, that's gonna help prevent this from walking. And this piece is too narrow to feed without a backer board. Additionally, as we go through and exit the cut, that's gonna help prevent chipping on the outfeed side here.
Next step is to check your work and a good way to do that is to gauge it. So if I come in from this face, lock that, and then flip, is it the same? That's what we're looking for, that's our test. When that is the same, then the tongue is centered on our work and we're ready to go. Now, for your door parts.
The formula is in the plan that tells you how to calculate the sizes of your door parts. So have a look at that formula. Don't just go off the cut list, 'cause your cabinet might end up just a tiny bit different than the one that's shown in the plan. So use the formula in order to determine the lengths of your rails and the lengths of your stiles. Once you've got that set, it's a good idea to mark the backs of your rails and the backs of your stiles.
And then when I feed these, to make sure they're consistent, on the feed then I'm always so that it's back face up. At this stage of the game then we can go, zoop, rotate, zoop. It's a lot like the pocket hole discussion, which was make sure you rotate between passes, not flip between passes, 'cause we wanna make sure that the same reference face is down for all our cuts. Even though we've centered the tongue, having the same reference face down all the time is a good way to make sure that the faces of your door parts are gonna be nice and flush. Two cuts on each rail, end grain on each one.
I'm gonna do a bit change and then I'll show you how to get the height of that cutter approximated. And we'll be ready to do our groovy cut. Groove cutter's in. Then, and again, router unplugged, what I did is I raised that cutter until the top of the carbide is even with the top of the tongue that we just produced. Again, do a test cut, but this is gonna get you really, really, really close to being right.
Fence location is the same as we've already done. Face of the fence even with the ball bearing, Then it's good on these long groove cuts to add a feather board and that'll give us hold down pressure right over that cutter, just so that the board doesn't have the opportunity to lift. 'Cause, of course, that would change the relative position of the groove, that would mess us up. That's a piece of scrap. And then our test is this piece just fed like that, face down.
This one X was up, so that was face down. If we flip and bring them together, are they flushed across the face? I have just a little bit of a gapicity right there, not a gap, but a high spot. So I'm gonna make an adjustment in my cutter and then we'll come back and groove all of these pieces when it's right. Next thing, we'll dry fit that frame and I'll show you how to get really accurate dimensions for the panel.
When it comes to measuring and parts sizes and all that stuff, our sequence here is really important. We built the carcass. Didn't do the face frame until the carcass was put together and we extracted the face frame dimensions from the cabinet carcass. Then once the face frame was on, we extracted the door dimensions from the face frame. Then when the door frame is done, now we can figure out how big the panel has to be.
So don't just go through the cut list and cut parts to those sizes, 'cause things change a little bit. We make these little learning opportunities as we go sometimes. So it's better to let one dimension lead to the next the way I've done here. Now, the problem we're up against here is the panel's gotta fit from the bottom of the groove to the bottom of the groove. Really easy way to measure that is you need a ruler that can go inside the groove.
So that end is bottomed out in the groove. I'm gonna make a mark at 10. Then just come back and measure from the other direction, bottom it out in the groove. So 10 plus this number, 13 3/8, 23 3/8, that's my overall length of that panel. Minus 1/16, so it's got a little bit of wiggle room.
We're using plywood, it's not an expansion deal. It just makes it a lot easier to put the door together if the panel isn't exactly the size of the groove to groove distance. Do the same calculation for the width of the panel, cut that to size, and then we can glue the door up. I've got glue on this corner and I'll show you about putting glue on. With that rail and that stile, make a little right angle like that, slide in your panel.
So in the glue world, all we have to do is apply glue to the tongue, spread it. And when I put these together I'm paying careful attention to keeping this long grain flush with this end grain. Then it's simple from there, glue the tongue, glue the tongue, capture everything with the last stile. From there, get your door in clamps, measure diagonals, make adjustments as needed if the door isn't square. While this glue is drying, a couple other details we can do on the cabinet carcass.
Next thing, screw cleats. You can't just run screws to hold this on a wall through the 1/4 inch back and hang it on the 1/4 inch back, 'cause it's gonna pull the back and pull right out of the rabbets. We need something more robust for that. That's what these screw cleats are for. Cut these to size.
And, again, the dimension's in your cut list, but rip them to width, but then transfer the measurement, so that you know you have a good fit inside your case. Now, the reason I went with two pocket holes on this is not for screws, it's to make this a better, easier, one-handed operation. That clamp goes in one pocket hole. Drive a screw in the other one. And you don't have to go back on this application, you really don't have to go back and put a second screw in the other hole.
That other hole really is only there so I can take advantage of this. I'm just checking my face frame there, because I know on this side face frame's just a little high, very easy to fix. And the deal with that is just a piece of plywood that had just a little bit of a crook in it. You could plane in this or you could sand it or you could use a scraper. But work that down flush.
And then one of our last details on that face frame is a 1/4 inch roundover around the edge. Next step, hanging the door. To get the door on the cabinet, first, same 1/4 inch roundover that went on the face frame goes on the edge of the door. Do that. Then look at the plan, locate those hinges on the back of the door, screw those in place.
Now, to get this on the case or on the face frame. The door has got 3/8 overlay per side. So make a mark 3/8 from the face frame edge, 3/8 from the face frame edge. Then I'm gonna do another one up here that I can see. That's gonna show me where the top of the door is.
Part of the deal with these spring-loaded hinges, these self-closing hinges is when you try to install them they can like flex just a little bit and make things just a little bit of a pain. So take a piece of scrap and clamp it onto those pencil lines that you just made. The benefit to that is that that board is gonna put that edge in exactly the right spot. The line here at the top shows me where the door lives in this direction. And then what I can do is grab a scratch awl and my drill and I can flatten the flex out of that hinge, push the door against the stop.
Check my line on top. I gotta hit that one again. There we go. Make a dimple. Same thing at the top.
And then it's a good idea, before you do the rest of the screws, it's a good idea to check your work. Because right now with only one screw in each hinge, if the edge of the door wasn't hitting that pencil line we'd be able to make a little bit of an adjustment by using the second screw for each hinge. Once you know that you hit your line, go ahead and put the second screw in. Then from there, easy peasy. Cut your adjustable shelf to size.
That's gonna fit in there. Cut your back to size. Don't install the back until any finishing that you're gonna do is done. It's a lot easier to finish the cabinet interior when there's no back on it. So take care of all your sanding, all your finishing, then install the back.
You're gonna have a great wall cabinet. You can hang this in your shop. It's great for router bits or drill bits, or it's really just the right size to be an over the toilet cabinet in a bathroom. And learning how to do this from this three video series is really, like I said, opens the door to cabinets, bookcases, vanities, a huge array of different things you can build using these approaches. So hope you enjoyed it, caught all three videos, and have a great wall cabinet like this going in your shop.
These videos are great. George makes everything look easy. I was volunteered by my wife to build an entertainment center for good friends of ours, and although I've done a lot of home carpentry, finish carpentry is not generally my thing. I used these videos and plans as a basis for designing the entertainment center, and it came out great. They are very happy. (I also upgraded my tools significantly; I already had a pretty first-class router, but adding a router table takes it to a completely different level. The track saw, although you can't use it for everything, makes wonderfully smooth and exactly dimensioned cuts).
nice but how do I get the material list and "plans" you keep referring to?
Love it. I always think I need to reinforce glue joinery with brad nails. This video gives me a peace of mind that I can get away with gluing when you use the proper joinery. The Adaptive Cutting System Project Table is a very nice add when mainly using a track saw and skill saw. Now my question is: Normally would you use the table saw over these tools? These tools obviously produce a Great Wall cabinet. However; many of us still wonder if the track saw will replace the need to always have a table saw.
Beautiful presentation. Great tools, also.