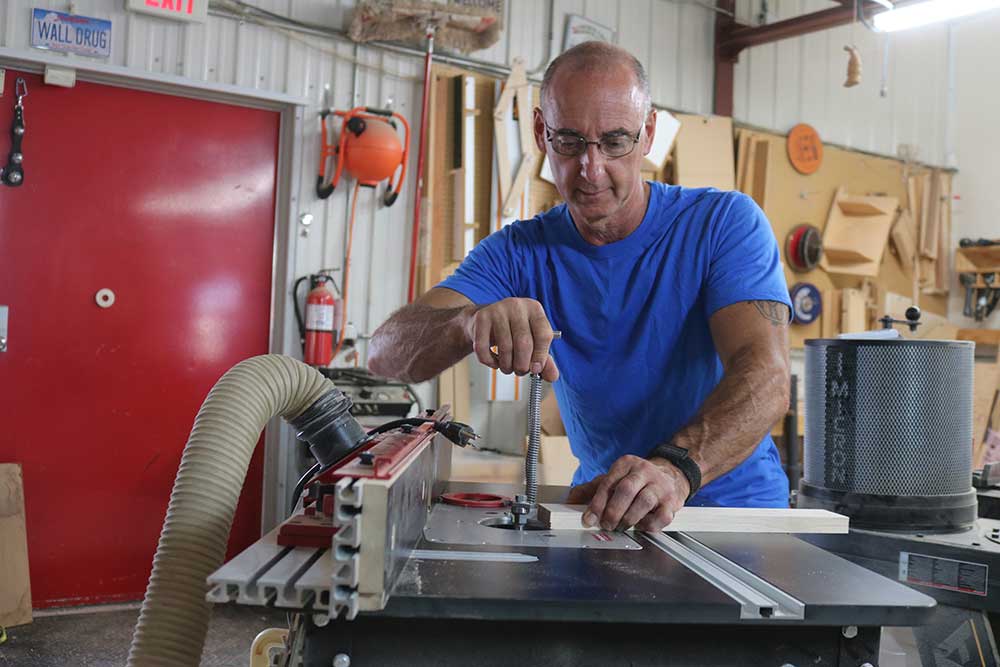
Build An MFT Table
George VondriskaDescription
What will an MFT do?
The multi-function part of the name is exactly what it sounds like. This table is so versatile. Use it to hold stuff in place horizontally and vertically. Routing, sanding, planing…anytime you need an extra pair of hands, an MFT provides it. And, of course, you can use it as a simple work surface.
Table details
I used a pair of adjustable height steel bench ends for my MFT and the stringer that connects them. The table is made from one 4×8 sheet of ¾” MDF.
Dimensions:
Top: ¾” x 32-1/4” x 64-1/2” ¼” deep rabbet all four edges
Narrow rail: ¾” x 4” x 64-1/2” ¼” deep rabbet each end
Wide rail: ¾” x 10-3/4” x 64-1/2” ¼” deep rabbet each end
Sides: ¾” x 10-3/4” x 31-1/4” (Cut to angle to align with rails)
The holes
I used a drill guide and drilled the holes with a 20 mm forstner bit. The holes are 5-3/8” on center and start 2-11/16” from the edge.
The Bessey accessories
Horizontal fixture clamp
Gear clamp with 20 mm peg
Gear track clamp
Threaded track clamp
More info
For more info on Bessey products visit the company’s website.
You need a multi function table in your shop. If you're not familiar with this, um you should be because there's a lot of great stuff going on. Bessie has a number of different products that play nice with the 20 millimeter holes that are in this multifunctional table. So what we're about here is showing you all of the incredible stuff that you can do on the table using the Bessie products. And then I'm also gonna talk you through building one of these so that you can reproduce this and build it in your own shop.
So to get going with this, let's look at how does Bessie's stuff work with? Play nice with this crazy cool table. Let's start with an application where you want lateral pressure on something. It's not uncommon in woodworking that we wanna have our work up against the bench dog. This could be using a hand plane using a sander.
So bench dog that part's easy fits right into that 20 millimeter hole if you need to, you can use the knob from below. So that, that can't lift then with a project like this, got a cutting board with some epoxy on it, the epoxy on the back needs to be sanded and we can get lateral pressure from this clamp. So the way that's gonna work is that right now, that arm is free. When I do this, it pushes the arm out so that get some pressure on our cutting board, little hearing protection. So imagine, I don't know, think of all the things you're doing in your wooing shop using a belt sander using a hand plan or using a random orbit sander using a router.
The times when you don't want to be chasing your work across a bench top, the trapping of your work between the clamp and the dog is a great application of the MFT. We just talked about lateral pressure. Let's talk about vertical pressure. So what a surprise again, we've got a hole down, that'll go in that 20 millimeter hole. Now, if I'm assembling that screw pocket, I can get my material under there.
Bridge the scene, apply some, hold down. And in this particular case, we're getting a bunch of benefits. One is it's holding the wood so you don't have to. The other benefit is that with this pressure right here, we're keeping the face of those pieces flush, which is important for your assembly so that you don't have a bunch of sanding to do later to flush those up. So that covers a little bit of what we can do with vertical pressure.
Let's look at a little bit more, hold down. So this toggle clamp engages with the table. And one of the things I love about this is its self adjust ability. So if I throw that board under there, we're rock out. Now, if I throw another board under there without me changing anything here, we're still solid.
It auto adjusted. If you go a bunch thicker, you can change this so that it gives you more wiggle room under the clamp pad. And then again, you're gonna get that benefit of it auto adjusting as you go from one thickness to another. So the toggle clamp is another great way to get even more vertical pressure to hold your work in place. A little departure from the way we're using our whole system.
This clamp will go through the whole hook under the table can do this and then this and then this. So now imagine we're routing that edge, we're hand planning a champ for any work that we're doing that we want to be can levered off the table a little bit again, lots of vertical pressure from this and just a different way to get engaged in those 20 millimeter holes. You may have been looking at the table and wondering about the verticals on each side, all of which also have holes in them. Here you go. This is for you in a scenario where we wanna join a couple of boards, we could clamp one horizontally.
Here we could clamp one vertically here and then manipulate them until we get what we want and use that as that, you know, extra pair of hands you've been looking for in your shop when you're trying to fasten parts together and can't quite hold them. The other thing we can do with this vertical surface. Yes. Let's go back to this clamp. If you run into scenarios where you wanna get something up higher, you know, maybe you're in your bifocal years like me and closer is better when you're laying out a joint or something like that, we can use this to elevate the work so that we can get something up high where it's a little bit easier to work on a little bit easier to see taking advantage again of that vertical surface, couple of clamps in there are material secured, other great use of your MFT.
Now that, you know, you have to have one of these tables in your shop. Let's talk through how you can make one for yourself. First off the holes in the whole spacing, the holes are 20 millimeter diameter. I did all those with the Forester bit and those that forester bit is sourced for you. The spacing on the holes for me came from this particular clamp because of its lateral pressure.
So what I did is I mocked up a little piece of scrap with 20 millimeter holes in it. And I did this and I looked at how close to the holes need to be to optimize the travel that I can get from this particular plan. And that's how I got to five and 38 inches for the base of the one that I built, I ordered a steel base and I've got that source for you. So there are a couple different options going on there. One of course, you can build your own base if you want to.
What I like about the steel base, it's adjustable in height. So you can set this to wherever works for you. It's got a horizontal rail on it. And one thing you could do is not get the horizontal rail with the two ends, you could make your own horizontal rail and that would allow you to change the length of this. So the length of my table was dictated by the length of the horizontal rail that came as part of that two ends in a rail set.
So you have some adaptability there. I made the top out of MD F three quarter inch thick MD F. And the first step in that is to work on your layout. The layout like I said is based on five and 38 inches center to center on all these holes at the edge of the sheet. It's half that distance and then the layout picks up the five and 3/8 on center picks up from there.
Once you got the layout done, you're ready for the boring part of this, which is literally boring. You're gonna drill a bunch of holes. Life is gonna be a lot easier to locate the bit on the surface if you take a scratch all and you punch each of those center locations before you start doing the drilling. So the easiest way to make sure you keep these holes perpendicular to the surface is to use a drill guide. If you don't have a drill guide doing this freehand with the Forester bit isn't horrible.
Just make sure you keep the drill perpendicular to the surface of the MD F so that the holes don't end up wonky, they don't end up angled after all the drilling is done, then I sanded the pencil marks off. So I wasn't looking at those forever to make assembly easier and everything a little bit more robust. I cut quarter inch deep rabbits on all four edges of the top and on the two ends of the front and the back, the rabbit is just gonna make it a lot easier to put this together so that the pieces aren't sliding around as you glue and clamp them. I didn't want to put any mechanical fasteners in the top just in case a cutting tool ever penetrates and you don't want to hit a nail or a screw with a router bit or a tracks saw blade as you're using your MFT table. So in order to make that joint, more robust, everything is glued together.
Taking advantage of the rabbits for that as you're cutting the rabbits on your table. So especially on the long edges of the top, if you feel like you're not getting good, hold down from just hand, pressure, add a feather board to the fence to give you a little bit more, hold down to make those tapered sides. I found the easiest way to do that was with the tracks saw. So they're laid out. So that on the wide end of the side, it's the same width as the back of the table.
And on the narrow end of the side, it's the same width as the front of the table. So once I had that laid out to a line, then I could use a track saw to cut those angles when you put this whole thing together. Keep in mind that MD F soaks up a lot of glue. So be generous with the glue, maybe go back and apply a little bit more. If you've got the first round on there, bottom line, just make sure that you've got enough glue on the MD F.
Put the frame together first. It's the easiest way to do this. Get that in clamps. You don't necessarily need to let it completely dry, just leave the clamps on, then put glue on the rabbits on the top and set the top into the frame and then start using clamps, clamps and more clamps, just make sure that you have enough clamps on at this stage that you're closing the front and back and tapered ends against the shoulder of the rabbit and you're pulling the top down so that the front, back and sides are seated into that rabbit to make sure that everything is where it should be. The MFT.
Honestly is something that once it's in your shop, you're gonna find, the more you use it, the more uses you find for it. It's a great assembly table. It's a great sanding table, routing table. And Bessie has done such a nice job of coming up with a really broad array of accessories that work with those 20 millimeter holes. So it's very, very versatile.
It's like the go go gadget workbench of a woodworking shop and really a must have thing.
Do you treat the MDF with anything like oil or poly to give it some durability?
Why not use the Festool interval of 96mm/3.76in?
My choice of words never works.