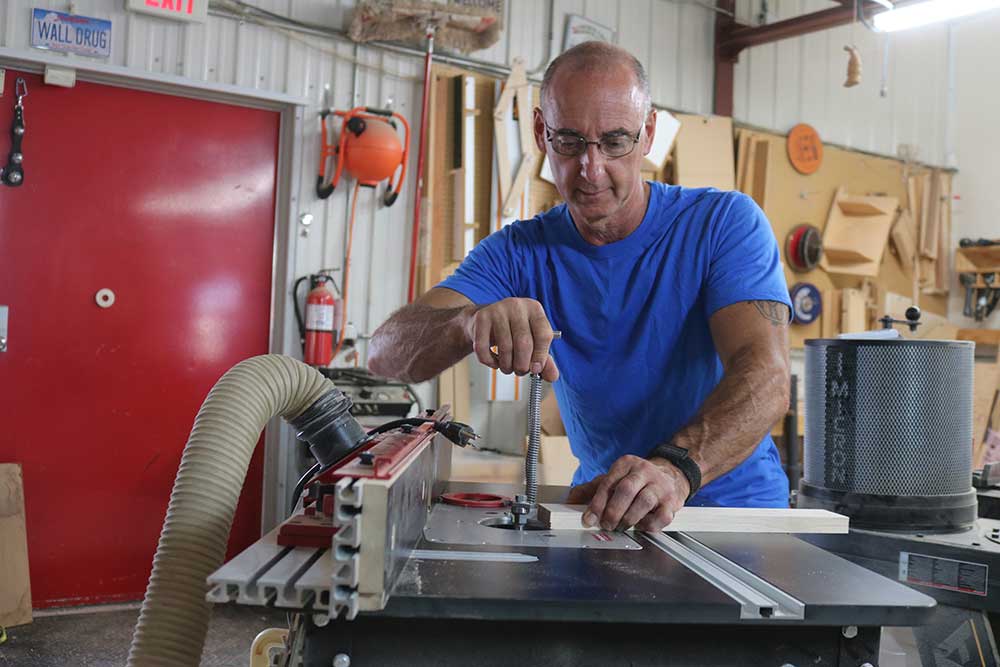
Captive Ring Out of Spindle Turning
George VondriskaThere aren’t many woodworking techniques that will draw more ooh’s and aah’s from your woodworking buddies than a captive ring turned on a spindle. George Vondriska demonstrates the mysterious technique in this clip. A WoodWorkers Guild of America (WWGOA) original video.
Captive rings like this, are something, that I know turners love to do. It provides great bragging rights. I've got this one incorporated into the handle of my shop mallet, and I love showing it, to my woodworking buddies, when they come over. On a smaller scale, I've got a captive ring, on this pen I turned, pretty cool there too. Same process, just a little bit more delicate here.
Let me show you how you make a captive ring, on a spindle turning. The first step, on your turning, once it's been made round, is to form a bead. That bead, is what's gonna become, your captive ring. Once the bead has been formed, the next step, is to reduce the diameter on each side of it. Our goal is to get to a point where we can undercut this.
So, now I'm gonna go from a skew, to a gouge, so that I can get some of the material, on each side of that captive ring, taken away. With this, being hollowed, like it is, now the next step, is to go back to my skew again, and I'll start undercutting, a little bit from each side. You wanna be very conservative with your cuts, so that you don't shatter this bead that we created here. Now, what you want to do with your skew, is you're making these cuts, is listen to it, and you'll hear, as that wall gets thinner and thinner, the pitch go up, and that's gonna give you a clue, that that ring is about to come loose. So now, it's loose on there, but it's still kinda grabbing.
All you need to do, to let it move freely, is reduce the diameter a little bit, of the material underneath it. With the wood underneath cleaned up, now you've got a donut, sitting right in the middle of your spindle turning. Remember, with your captive ring, that once it's cut free, you really can't get sanding or finishing done on this. So, you wanna do that work, right before it pops loose. Now, you know, how to make a captive ring.
Taping adhesive to the spindle under the ring after release, permits sanding of the inner ring surface.
Very cool.does not look difficult
An instructor I had (Bonnie Klien) showed me how to make a small dedicated tool for just this process. It involves grinding down a 1/8th inch allen key. Remove most of the short arm and grind the remainder to a four-sided point. Insert it into a handle and you can create a ring that is only marginally larger than the underlying shaft and is quite clean as well, due to the small size of the tool, which affords easy access to the underside of the ring. Here is an example. https://www.dropbox.com/s/v5la8iu3ao8b2ui/DSCN1701.JPG?dl=0 https://www.dropbox.com/s/0jjuh3x8byqmfie/IMG_0551.JPG?dl=0
How do clean up the inside of the ring?
It would be nice to have a bit more voice-over to describe the details on the skew cuts as you are releasing the ring. In the video it almost looks like you have the long point down but are cutting with the toe, when cutting away from the headstock, but we can't actually see the cut, and the tool positioning seems different when cutting toward the headstock. Also, a tip I saw from another turner is to wrap a piece of sandpaper around the spindle, inside the ring and then carefully sand the inside of the ring to clean it up after it's been turned free.
Now here ya go showing how we do this.