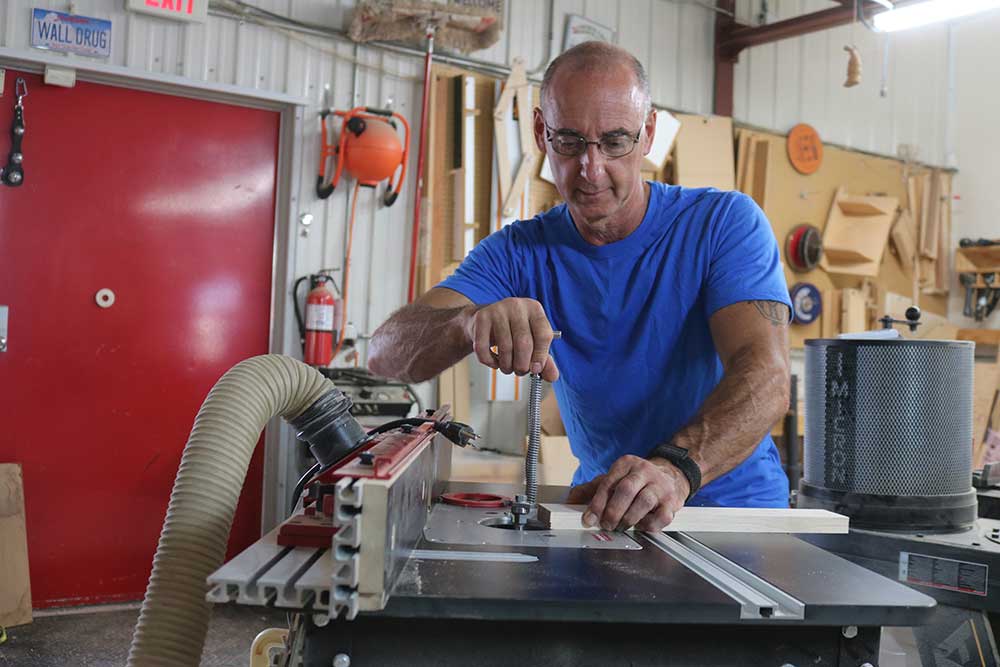
CBN Bench Grinder
George VondriskaDescription
What’s the set up?
CBN wheels are mounted on a low speed (1750 rpm) 8” grinder. Unlike conventional grinding wheels, CBN wheels aren’t likely to explode, so the guards are removed from the grinder. We’ve also equipped the CBN bench grinder with a Kodiak sharpening system. I’m using a 180-grit wheel and a 600-grit wheel.
Benefits of a CBN Bench Grinder
Here’s what you get from CBN wheels:
- Run truer-manufacturing process makes them round, not almost round
- Run cooler-very hard to overheat chisels
- Can use the side of the wheel
- Never need to be dressed
- Never change diameter-important if you’re using sharpening jigs
- Very fine grind
- Can sharpen on the side of the wheel-helpful for skew chisels
- Second in hardness only to diamond
- Longevity: they’ll far outlast a conventional grinding wheel
The Kodiak System
It’s very important to keep a consistent angle and cutting edge on your tools. The Kodiak system makes it very easy to do this. With platforms, mounts and guides for a variety of tools, you’ll be able to keep your chisels very sharp and very consistent.
For More Info
For more information on CBN wheels and the Kodiak system contact Woodturners Wonders via their website or by calling (678) 400-8181.
Want to learn how to put those freshly sharpened lathe chisels to work? We have lots of great information on lathe turning. In addition to lathe work, there’s lots you can learn from WWGOA about working with power tools.
A question I've been getting a lot lately is what's the deal with CBN wheels and sharpening, using them to sharpen? So first off, CBN, cubic boron nitride, manmade material, and we get a lot of stuff going with these wheels. I've got two mounted here on a low RPM grinder. And one of the deals is, let's confront this right away, they are not inexpensive. But this is a good example of cry once when you're buying 'em and then not cry again over the life of the tool.
If you're buying an aluminum oxide wheel for your grinder, in all likelihood, you will replace that wheel over time. Additionally, we get other sharpening benefits out of a CBN. So when we look at the fact that, yes, today, it's more out-of-pocket than an aluminum oxide wheel. However, over the life of my woodworking, I'm never gonna buy another one. Value there.
And then, two, benefits that we get just from using CBN wheels. And we'll talk about that. And I heard somebody say a great thing once, which is, we're gonna look at sharpening lathe chisels, "So when you've got a really expensive bowl gouge, "why are you sharpening a really expensive bowl gouge "on a really marginal grinding wheel?" It's a great point. And that really stuck with me. Here's what goes on with a CBN wheel.
One thing you notice here on the grinder, there's no shrouds on it. With conventional grinding wheels, one of the things they can do is fracture, so everything is significantly guarded. With the CBN wheels, we don't have that issue. Additionally, I have been told from an early age, machine shop when I was 12 years old, that you should never grind on the side of a wheel, and that's correct if you're using a conventional grinding wheel because that can cause fracture. With the CBN wheels, we can use the side of the wheel.
This is a great benefit when we're grinding anything that's got a flat surface to it, and instead of trying to bring it here, we can bring it here and take advantage of that nice flat side. So, benefit right there. They can't fracture and they allow us to use the side of the wheel for flat tools like that. Another thing, if you've got a low RPM grinder now, with conventional wheels in it, maybe when you run it there's just a little bit of vibration to it. It's hard to get conventional wheels perfectly round.
The manner in which these wheels are manufactured makes it easy to get 'em round. So we're, right out of the box here, we're running with way less vibration than a conventional grinding wheel. That's a cool thing. Speaking of cool things, CBN wheels also grind cooler than a conventional wheel. So as long as you're not being overly aggressive when you use these babies, the idea of overheating the tip of your tool is almost nonexistent.
You pretty much can't do it. The other thing that's cool is that these aren't gonna change diameter over time. We don't have to dress these wheels. So when I get a jig set up and we rely on distance from jig to grinding wheel for a specific operation, that distance is gonna be uniform forever because we don't have to dress 'em. By not dressing, we're not changing the diameter.
So that consistency is really, really important. And here's the thing. When I'm teaching people to turn, one of the things I harp on a lot is you gotta keep your chisel sharp, you gotta sharpen 'em the same way every time. If you change the dynamic of the cutting tip on your chisel, it's gonna change your body dynamic when you're using it. And when you're learning to turn, that's introducing a factor that's not good.
Why introduce another variable? So the more consistent we can keep the cutting edges, the better off we're gonna be. A lot of great attributes here. Now on this setup, I am running a 180 on this side, a 600 on this side. Now 180 might sound fine but, not sound fine, but as opposed to coarse.
So what we find with CBN wheels is that, because of the way they cut, instead of having a 60-grit on this side for shaping operations, I can have an 80, a 180 here that gets me to a finer finish right away, and I can transition from that right to the 600 to get me closer to the finish line on my cutting edge. So, there's a really different dynamic, a very positive dynamic going on with these CBN wheels. Now, in addition to the wheels, here's the other thing I want to talk about is a cool system. Specifically, This is a Kodiak system from Woodturners Wonders. And what I like about it is, man, it really makes getting a good cutting edge on your tools repeatable and pretty darn bulletproof, and as I just mentioned, consistency is really, really important on those cutting edges.
So let me swap a couple things around here, and we're gonna jump right into look at sharpening a bowl gouge and what that entails. My favorable gouge ready to have its edge refreshed. To get a little understanding of the system here, the grinder is sitting on a support platform. That platform will accept devices like this or the table I had on there previously. While this is still out, one of the things to look at is it's got numbers on it.
That's gonna play for us in just a second. Also, there's a pocket right here. In just a second, I'm gonna use this pocket to control the projection of my bowl gouge. One of the things that comes with the system is a chart, and depending on what kind of grind you're trying to achieve, we use the numbers over here to get that grind. So, I'm gonna put this in.
I want a B2. Slide that in, engage in the 2, lock that. Now remember that pocket I showed ya? I'm gonna put my bowl gouge into this holder, project into that pocket, lock this, and that gives me a consistent cantilever here. Remember I mentioned earlier, these wheels don't change in diameter.
So that's why this will always work. This will always work. Then, this goes in here. I'm gonna put my chisel in the B position which just means I'm racking it up on this holder, here or here, A or B. And then from there, just roll on the wheel.
If you're used to using a conventional grinding wheel, one of the things you might be looking at is saying where the heck are the sparks? That's it, baby. I mean, that's the extent of sparks you saw here is what we get. So remember, we've got that attribute here of we're running cooler? Also, way less sparks, which we just proved.
All right, another setup change, and then we'll jump right back on this wheel again and show ya another sharpening. When it comes to sharpen the skew, it's nice, I like to have a long, flat bevel there, which in this case we can take advantage of having the side of a wheel that we can work on. Now, some of the stuff that we're looking at here, these are accessories that you can add to the system. So, this accessory is gonna allow me to get the skew here, run it on the side, skew here, run it on the side, and this stand is available in different angles depending on what you want to do with your skew. But here's the way this baby works.
One thing, I just came off the grinding wheel, and that edge is not hot. Really important that we have consistency on our cutting angles. This has given us that consistency here on the skew. Now while the table's on, let's look at a couple of other things. For something like a roughing gouge, what I'll do is simply angle this table, and once the wheel comes to a stop, I can set that up and show you walking through our roughing gouge.
Doesn't get much easier than that. That takes care of our roughing gouge. Now similarly, a scraper. Set the table at the right angle and we can simply roll that scraper back and forth across the wheel like that. Let me show you something on this other wheel that's a cool thing to take advantage of with your scrapers.
The difference between the two, different grit, obviously, but this wheel has also got round edges. So when my table is here, the other way I can sharpen a scraper is to come in, sweep up the rounded corner, sweep up the rounded corner. So we have a couple different approaches that we can use on round nose scrapers like this one, depending on which wheel you're on and what approach you want to take with your cutting tip. Now something like a parting tool, we can do this a couple ways. We have a flat side on the wheel.
We can come in like this and take advantage of that flat side on the wheel in order to work on that, work on that, brrp, brrp. On a parting tool, I actually like it to be a little bit hollow ground. So for me, on this wheel with a parting tool, I would simply do this. If you're not comfortable doing that free hand, you could take advantage of the table and get established at the right angle to let the table do that for ya. The other thing we should have a look at is what about just your conventional pocket knife?
This is really easy peasy. This is free hand stuff. And last thing for us to take a peek at is conventional bench chisels. Gonna let that come to a stop and get that system set up so I can show it to you. With this accessory on, now we can hit a conventional bench chisel.
From there, a little bit of work on a whetstone, and we're gonna have a great cutting edge on this. Spindle gouges are gonna get approached the same way our bowl gouge did, which is pick the angle that you want, do the settings like we talked about earlier, and then just roll it back and forth across the wheel. So, a lot going on here. One is just understanding the CBN technology and recognizing that, upfront costs versus longterm costs, there's a lot of value here. And then, in addition to that, the ease of sharpening that the Kodiak system adds here.
And I think, when it comes to lathe turning especially, sharpening is probably 60% of the skill of lathe turning 'cause if your tools aren't sharp, they're not gonna work for ya. So big scheme of things, the marriage of the CBN wheels to the Kodiak system here really brings a lot of value and a lot of ease of keeping your tools keen, keeping 'em sharp to your shop.
Your wheels appear to have about 1" grinding surface on the sides. Woodturner Wonders website says theirs is about 1/4". What is the source of your wheels ?
With such a minimum of sparks is it still advisable not to connect the grinder to dust collection ??? I hate the metal dust in the air and collecting around the grinder. Of course I vacuum it up after grinding.
Not true about CBN wheels lasting a lifetime, the 120 grit one I bought from Ron Brown's Best lasted less than a year before the particle coating wore off,yea he replaced it but not before a lot of back and forth and having to pay an additional $35 in shipping.
I disagree about removing the guards. Those sparks are hot pieces of metal. Having been a professional cutter grinder for 27 years, I know the value of the safety guards. CBN wheels do wear, just not as fast as aluminum oxide wheels. Don't kid yourself about CBN wheels not blowing up. A defect in the wheel or the metal backing can cause the wheel to break apart. Safety first!!
What brand of CBN grinding wheel did you use in demonstration?
Cost of that system is not that bad, Over a good qulity bench grinder, also it's a complete system. Even the wheels alone are not that bad. You can spend more then that on your irons Unless you go with carbide incert tools. And if you have any experience in metalworking you can make your own. And as a former machinest I'd be tempted to try that. The nice thing about carbide it a tougher material will hold an edge dosnt need to be sharpened and wont hold heat.not that I'd pick one up after cutting with one. New incerts cost 1.50 to 12 bucks each and have 3 to 6 sides. Carbide cuts more holds up better holds its shape cuts even the hardest woods and will hold an edge. They were ment to cut metals wood is butter for a hot knife to them.