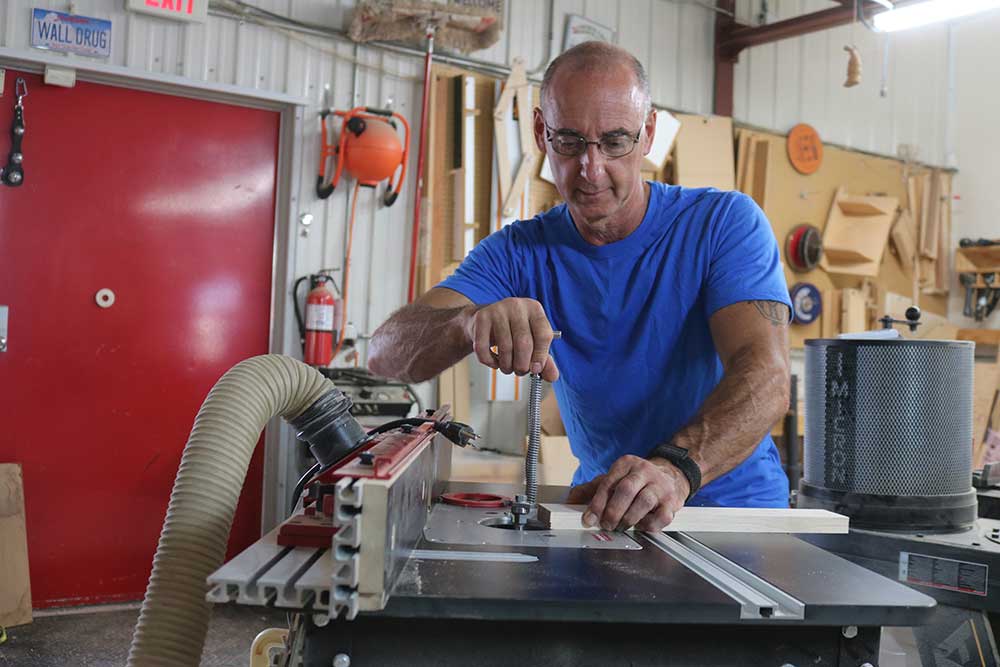
CNC 3D Machine Carving
George VondriskaA wide array of amazing 3D clipart is available. 3D clipart, and the resulting carvings, will add a unique touch to your woodworking projects. If you don’t like sanding (and who does?) make sure you do these carvings with the right bits to ensure the best cut quality.
3D clipart
If you don’t have the artwork you’re looking for in your design software check out Design and Make. A huge assortment of clipart is available there. The clipart used in this video is called Cantering Arabian.
The bits
3D carving is commonly done with two toolpaths, one for roughing and one for finishing. The roughing toolpath removes the bulk of the material, leaving the workpiece looking a little like a tiered cake. The finishing toolpath removes the rest of the waste, leaving the completed image.
The diameter of bit used for the roughing pass varies depending on the size of the carving. Use larger bits for large carvings. A ¼” upcut spiral was used for the roughing toolpath on this project. Similarly, choose the ball nose bit for the finishing toolpath based on the size of the clipart. A ⅛” tapered ball nose bit was used for the finishing pass with a 10% stepover.
The results
With the toolpath correctly set up and the right bits chosen for the project, you’ll find that you have very little sanding to do on the completed carving. The best results come from doing the carving in close grained woods like hard maple, cherry or walnut.
More info
For more information on the router bits you can use for your CNC work check out www.bitsbits.com.
WWGOA has a lot of content that will help you with your CNC router work. Check out the large variety of CNC videos that are available.
One of the things I really like using the CNC for is 3D clip art, like this cantering horse, and a couple of great things come out of this. One is just a level of carving detail that I know I can't carve myself, and two, that level of detail. So when we look at this horse, the mane, the tail, the muscles that are showing up in it, and it's cut into hard maple. So we've got a couple things at play here. One is clip art is really cool.
Another is I don't like sanding. So I really like to use the CNC in a way that I have little, or even better, no sanding to do when this comes off of the router. And that pertains not just to the clip art that we're gonna work on here, but also to the profile toolpath that was done here around the edge when this was cut free from its board. A lot of that comes down to making sure that you're toolpathing correctly, and that you're using the right bit. We're gonna start with a 1/4 inch upcut spiral.
That's gonna do a couple things for us. First, we're gonna do a roughing pass, then we're gonna take that bit out, and it'll come back and do the profile pass. The roughing pass is important. It removes the bulk of the material so that our 1/8 inch tapered ball nose bit can come back and have the opportunity to do that great detail that we were talking about. On the roughing pass, you need to balance the diameter of bit you're using against the size of clip art you're working with.
So if I went with a larger cutter, if I went with the 3/8 diameter end mill, I would get the roughing done more quickly, but it wouldn't get down in the detail the way the 1/4 inch will. So for something this size, this is about eight inches in diameter, the 1/4 inch is a good bit for that. As the artwork gets larger, then the 3/8 might be more appropriate, and of course you can preview toolpath in the software to make sure that you're choosing the best bit for what you're trying to do. And what's neat about this, you can see when we look at the completed or nearly completed roughing toolpath, it's kind of like a tiered cake. It's taken away a lot of the material, but there's enough left there in those steps that now when the 1/8 inch ball nose comes by it can create the detail that we're looking for in the final piece.
Choosing what diameter ball nose bit you're gonna use is very similar to choosing what diameter end mill you're gonna use for the roughing pass. The finer a ball nose we choose, the more detail you can get, but the longer your machine time is gonna be. So again, in the software, the easiest way to approach this is to do a preview toolpath, for instance, with the 1/8 inch ball nose, look at that image, see if it's giving you the detail you're looking for, then substitute in within the software a 1/16 inch ball nose, look at that detail, and then using the software, you can compare the machining times and see, are you willing to spend more time machining in order to get that greater level of detail? The 1/8 inch ball nose I'm using here is stepping over 10%. So it's a pretty long tool path for it to get from one side of an eight inch disc to the other, but that small bit of step over in addition to the great quality cutter that we have is what's giving us the really good cut quality on the material with very little sanding left to do on that completed artwork.
I love this part in the toolpathing, where we've got most of the object cut, and you can really start to see the detail. Look at the mane, look at the tail, that that cutter is producing for us. What a great example of the detail that we can get. This is in hard maple, the detail in the mane and the tail is absolutely beautiful, and honestly, man, very little sanding when this is done, which is a key part of doing CNC work, and that pertains not just to the artwork here, but also I can tell from looking in the edge here that that's a very clean cut that we have on that profile toolpath. So it really comes down to, to get good quality work like this, making sure you're using the right cutters and that your toolpaths are set correctly so that we get this kind of quality of work, this kind of detail, with very, very little time spent cleaning up after the CNC work is done.
Sir. Where can I get a tool path file done from and what would be the charges
What are the optimal feeds and speeds.. I am trying to carve a special forces emblem and I get tear out on the arrows or text details.