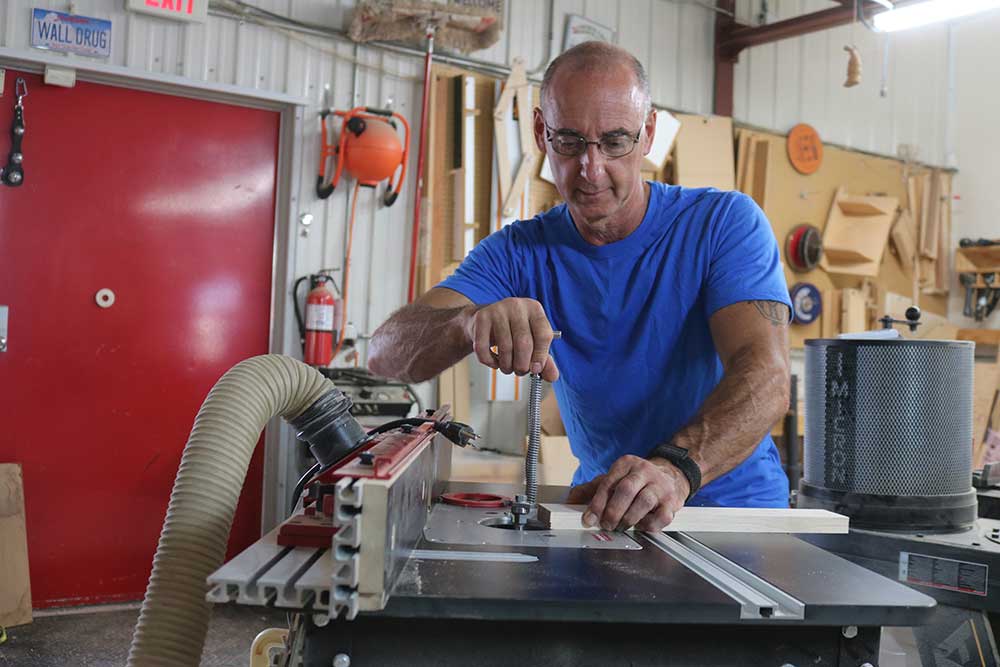
CNC: Flattening Cookies
George VondriskaDescription
The Problem
Chainsaw cuts made to create the cookie probably won’t be perfectly parallel to each other. Even if they are, chainsaw chains don’t provide the kind of surface you’ll want to incorporate into your projects. If you own a CNC router, you can use it as a CNC cookie cutter. This is a great way to get two surfaces parallel and smooth enough for sanding.
The Bit
You can use nearly any flat bottomed router bit to do the work, but a spoilboard router bit is definitely the best way to go. They typically have a large diameter so can remove a lot of material quickly, and are specifically designed to leave behind a good surface.
Freehand CNC Cutting
Did you know you can use many CNC routers “freehand.” Instead of creating a toolpath you can use the fob to control the spindle or router position, guiding it across the surface. This is how we’ll get started, and it provides a great way to eliminate high spots on your cookie.
More About Cookies
If you don’t own a chainsaw, but want to make log cookies, check out how to do this on a bandsaw. One problem with log cookies is getting them to dry without cracking. There is a chemical treatment you can do to stabilize them. No CNC in your shop (yet)? You can also flatten cookies with a hand-held router and shop-made jig.
In the world of prevalent questions that we get at WWGOA, people asking about working with cookies, making cookies, is a really, really common one. And by cookies, what I mean is, they're doing cross-sections from a log and there's a lot involved here, and we've got a lot of information on the site about this. But, what I wanna talk about here is if you've got a CNC machine, you can use that to get the cookie nice and level. And this is one of the challenges is, you cut the stuff with a chain saw, and I don't know about you, but I have a hard time cutting stuff dead straight and getting the two faces parallel. And, of course, then you've got the crummy finish that comes off a chainsaw.
So what we're gonna do is throw this on the CNC and basically we're gonna fly cut the surface, but we're gonna do some freehand cutting there. I'll show you that in a little bit. I'm gonna show you the mount for it here 'cause it'll be easier to see than at the machine. What I did is I took some scrap MDF and I traced the log onto it like that. When this goes on the bed of the machine, I'll position it.
And then I'm just gonna push these up against the edge, clamp 'em, and do that from each of the four sides. And there's not gonna be any uplift on this. So all I'm really worried about is holding it laterally. So with a couple of hold downs on each of these corners, on each of these blocks, we'll be able to keep that in place so that this isn't sliding sideways while we're cutting on it. I'm gonna get this on the machine and then a cookie cutter from there.
I've got the cookie mounted to the CNC, obviously, and here's what I'm gonna do. Right now, there are a couple of things. It's a little bit high. It's a little bit high for my Z and there's a lot more wood to take off here than there is here. So I have created a toolpath that'll do this work for me.
And I'll talk more about that when we get to that point. But to start out, I'm gonna just rough this out by controlling it manually with the fob. And if you're not aware that you can do this, you should be. I can, of course, turn the spindle on and off. So I'm gonna turn the spindle on and then we move it in the X and the Y all the time in order to manipulate it and get it where we want it to be in order to zero our X and Y.
You can control the rate of that movement. And your fob might be a little bit different than mine, but this information is there somewhere. So here on mine, high/low, when I click that it moves at a faster rate. Low, slower rate. And I want it at that slower rate for what I'm about to do.
So this is simple. I'm gonna turn on the spindle. I'm gonna use the X and Y buttons in order to move this direction and knock this high spot down. And I'm gonna run the dust collector. I don't have the shroud on there 'cause then you can't see the cool stuff that's happening here.
So we'll get a little bit of pickup, but we're gonna make a big mess too, because the dust shroud itself isn't on there. Big cutter, so make sure you check the RPM on your machine before you fire up, 'cause we wanna run this at a low RPM with such a big diameter bit. So here's what I'm learning. This high spot is a little bit more than this cutter likes to take off. And part of the reason is that that particular cutter doesn't have a lot of side cutters.
It's primarily designed as a fly cutter to cut on the bottom. So what I'm gonna do, to help the section, I'm gonna grab an electric hand plane and come back and we'll we'll knock some of this high spot down with the plane to eliminate some of that waste. And then we'll come back and wrap up with that bit. So part of what I did here is at this point when I shut this off, I didn't change the Z on that. So that cutter is still at this height.
And then we can come back and just resume what we're doing with the freehand, then go to the toolpath. Gonna be right back with a plane. Way more better. Now we just go back to doing what we were doing. And a good question would be, I've got an electric hand plane, why not do the whole cookie with that?
And you could, but the challenge would be getting it dead flat. It's hard to regulate that. It's hard for me anyway to regulate that and get the surface perfectly flat, and then when we flip it, to get the other face parallel. So that's where the CNC or a handheld router jig, or something like that, really shines for this stuff. Way better!
Way easier on the cutter. Now that that's close, what I'm gonna do, is zero my XY, zero my Z. And I'm just gonna zero the Z manually, not off a touch pad, and then I'll run the toolpath off of my flash drive. I've got the toolpath set up as though this was a 23 1/2 inch diameter circle. I'm using a pocket cut, 3/16 of an inch per pass, and that'll come in and just fly cut this whole thing nice and flat.
It's gonna take a couple passes to get it perfectly flat but we'll get there. Pocket toolpath, 3/16 of an inch per pass. And I think we are ready to cut away. Looks pretty good. What an improvement over what we had.
Now, a couple things we were talking about the bark on here. In all likelihood the bark's gonna come off. That's kind of a crapshoot.` It depends on the wood. It depends on when it was cut, how long it sat in the sun, but this bark is not gonna stay stuck. Surface finish on here.
This is, it looks like there are little ridges there from the router bit, but they're not, in my experience, just a little bit of work with a random orbit sander is gonna take these marks off. This'll be dead flat. What we did here is once it was done with cut number one, I zeroed it again to the new surface, and then just ran the same toolpath all over again. Took another 3/16 off and that's where we are now. What needs to happen next is I'll flip this over, do the same thing to the other side.
That'll get the other face nice and smooth and even more critical, I think, they'll be parallel to each other. I'll probably just put hairpin legs on the bottom of this. So having those two faces parallel is a big deal. End of the day, if you've got a CNC machine and you've got access to cookies like this, this is a really nice way to level 'em. And I think it's pretty neat, that freehand CNC work at the beginning, to just go specifically after the high spots, I think is a good thing to know about.
So you can move this along a little faster. There's no sense running the whole toolpath when we really just needed to concentrate on that one spot. So, happy with this cookie and happy with how it went and how it came out and also really happy to have the dust shroud back on there for the rest of the cuts.
Share tips, start a discussion or ask other students a question. If you have a question for the instructor, please click here.
Already a member? Sign in
No Responses to “CNC: Flattening Cookies”