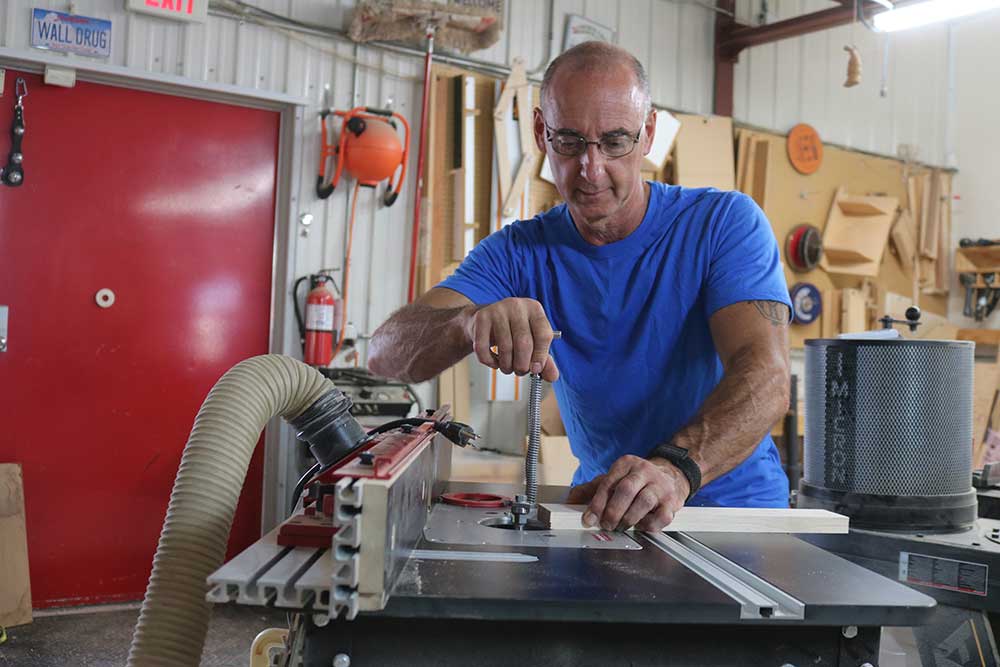
CNC: Leveling an End Grain Cutting Board
George VondriskaPeople love end grain cutting boards. They’re exceptionally beautiful, and because they’re end grain not long grain, they’re very durable and last a long time. However, the same features that make an end grain cutting board durable also make them difficult to level after the final glue-up. A planer might seem like a good solution for this problem, but you shouldn’t run end grain cutting boards through a planer. A CNC router provides a great solution for this problem.
Set up the cut
Using CAD/CAM software like VCarve Pro, create a Pocket Toolpath. Use a light depth of cut, 1/16” works well. In the software, create a rectangle that’s slightly larger than your cutting board. Be sure to ramp the toolpath, 4” works great, so the bit eases into the work.
Secure the board
The entire cutting board surface will be milled, so you can’t use hold down clamps directly on the board. Instead use hold down clamps to secure scrap to your spoilboard, then slide wedges between the scrap and the cutting board to lock it in place. Make sure this arrangement is below the surface of the cutting board so it doesn’t interfere with leveling.
The bit
Any flat-bottomed router bit can be used for this but, like fly cutting your spoilboard, it’ll go faster with a large diameter bit like the cutter used in the video.
Multiple passes
Run the toolpath and see what you get. If, after running the toolpath once, the surface is still irregular, simply rezero the Z axis (don’t change the X and Y origin) and run the toolpath again. Rinse and repeat until the surface is cleaned up. Flip the board over, rezero the Z and do the same thing to the other side.
When you're making an end-grain cutting board, which people love, and man, people pay a lot of money for end-grain cutting boards. When you do that second glue up, where you end up end-grain up on the board, part of the problem is that a lot of times these are just a little bit uneven and you've maybe got some glue beads on there and they can be hard to level out because you made this from hardwood. In this case, this is hickory and maple and walnut and purple heart. So we want a couple of things. We want to have a way to level it out.
And we want to end up with two faces that are parallel to each other. And we don't want to have to do a boatload of sanding. And sanding alone would really lend itself to the faces not being parallel to each other. If you own a CNC machine, the answer is at your fingertips. Here's what we're going to do.
On this cutting board, we're basically going to fly cut it, much the same way you would fly cut your spoil board. I've used a pocket tool path. I created a rectangle that's slightly larger than the size of the board. And I pocket tool pathed it for a 16th of an inch depth of cut. Be sure that you use a ramp on the tool path so that it eases into the work.
Because of the way we're going to cut this, the rectangle is a half inch bigger per side than the cutting board. We can't hold down. We can only hold over. So the way I crack that nut is I've got a hold down on a piece of scrap on this side, then a hold down on a piece of scrap on this side with a shim pushed in there as a wedge to push it over. Same thing, I've got one locked on the far end.
And then on this end, a shim to push that over, to lock this in place. There's not a boatload of lateral cutting pressure on this when you're cutting, but it needs to be secure. Bigger diameter cutter is going to do it faster. This is an inch and an eighth bit. It's going to be just fine.
And I think that's our information at hand. Let's see it go. As always with CNC work, one of the things that's handy about this is while that's doing that, I can be in another part of the shop doing something else. Does a nice job of leveling that out. It's pretty smooth.
Little bit of sanding is going to knock those burns off of there. Next step, flip it over, Z zero to the other side, do the same thing all over again. If you do the first pass, and at a 16th of an inch depth of cut, you complete that, and it's still uneven, all you have to do is zero to this surface, the new surface, and then run the exact same tool path again. And just keep doing that until you're left with a surface that's nice and flat. It makes for such a simple and effective way to level out these end-grain cutting boards.
Is there a way to start the cycle with a perimeter climb cut so you don’t get the splintering?
What speeds and feeds are you using? I have tried slowing down my speed and feed. Rate with mixed results. I wonder if I shouldn’t increase the speed but keep a lower feed rate as well as shallower depth of cut?
I tried this using a 3/4" mortising bit in my router (with a router sled-I don't have a CNC) with a bad result. I just got a 1-1/8" surfacing bit, and tried it out, with a similar (but worse) result. In both cases, I'm left with an uneven surface with grooves and tearing that is a real pain to sand out (I don't have a drum sander). I'm using curly maple, cherry, purple heard and walnut. On my initial pass, I'm going from left to right, and then I come back across from right to left. I'm cutting about 1/32" deep, and taking off about 1/2"-3/4" per pass. Do I need a different router bit?
Why not change your tool path to do a 1/4 inch perimeter pass in a climb cut (clockwise) path? This would eliminate any tear-out. Then switch to your back and forth field levelling passes.
Why is this better than running through a planer? I don’t have a CNC machine. Would a router sled accomplish the same thing?
Noticing the tear out at the end why wouldn't there be a sacrificial strip placed against the sides?