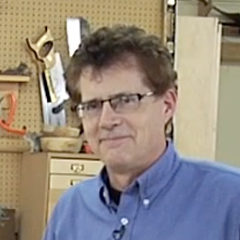
CNC Machine Programming Tips
Randy JohnsonDescription
Are you looking to turn your creative ideas into reality using a benchtop CNC machine? In this video, hosted by Randy Johnson, you’ll learn valuable tricks and techniques to help you streamline bringing your innovative concepts to life with precision and accuracy.
Expert Insights on CNC Programming
Randy Johnson shares his wealth of experience and provides practical knowledge about programming for CNC operations. Whether you’re a beginner or an enthusiast, you’ll find expert advice that will empower you to harness the full potential of your CNC machine.
Unlock Your Woodworking Potential
Sign up for our newsletter for endless woodworking inspiration! Become a member today and gain access to a world of craftsmanship.
We are very lucky in our shop today to have Randy Johnson here and we're lucky despite Randy Johnson being here but Randy Johnson is with shop and he's here to provide us some tips on programming for CNC and workflow for CNC. How to get from the drawing board in your head to where we're actually cutting wood, and Randy are you ready to start us out on your laptop there? I am George. And give us an overview. I will so as you mentioned there's a workflow to it that most woodworkers aren't real familiar with and it boils down to three things.
What is the CAD, which is the drawing part, which most woodworkers are familiar with. And the backend is the cutting, and in between there's something called CAM which is the tool path or the programming. I'm going to walk you through those three steps today George. One of the things to point out is that this is really generic to CNC work in general, not chat bots specific. Absolutely.
This software is real similar from machine to machine. So this is going to help you out no matter which machine you're on. Yeah. There's several different types of software out there as well. The one that I use is a pretty common one and has some pretty neat built-in tools.
I'm going to show you a couple of those today as well George. All right. So it all starts out by doing a job set up which is where you select the size of the board, you can set it whatever size you want based on the size of your machine, the thickness of the board has a couple other settings here also that you set up, simply click okay. And now this white area represents the size of our board which is six by eight inches. From here what one of the neat things about working on CAD and with CNC, you can take a simple drawing.
In this case, I already have a piece of clip art already loaded up. This football, it's a piece of free clip art that I downloaded off the internet. And then there is a tracing tool over in the drawing side, and it has some options. I select the piece of clip art and then I do what's called a preview and you'll notice that we get some lines popping around the edge. Those are vector lines and those are the lines that are going to be used for doing the toolpathing or the cutting.
So tracing is literally tracing. It just defined the outside of each of those clip art lines which eventually become a toolpath. Correct. Okay. And if you have a piece of clip art that's black and white or very bold in color that works better a photograph like you would take with your cell phone doesn't work as well.
So we're going to hit apply, close that. And from here I'm going to do a couple of move to another path that I have here which I already have the football enlarged a little bit. So now here you have eliminated the original clip art and we've isolated only the toolpath, the trace that you did. Correct. Okay.
And because these are what are called vector lines which are based on a group of points and you can see all those dots. Those dots represent nodes in what is called a vector line. And because this is a vector based line you could take that entire shape, select it. And you can enlarge it or shrink it and change the size and it will retain its resolution. So it's kind of cool that from what I've seen so far, I mean, I've worked with similar stuff on photo software, on drying software there's nothing real bizarre happening yet.
If you've done any work with even something like SketchUp or AutoCAD or turbo CAD most of the principles apply. Okay. All right. So we've got the vectors that define the football now what? And I've also created now a square vector around the outside of the football.
At this point, I'm going to add some text and here I can select a whole selection of different fonts simply type something in. And are there fonts available on there a person should stay away from because of too much detail, not enough detail I don't know. Let's say lets gear this towards somebody who's just getting going on this. Are there fonts that are easier to work with than others? Well, the software prefers true type font.
Okay. So it will bring up true type fonts that are on your computer those are the ones that it prefers. Fonts that are really fine in detail, pen fonts. So in this case. So maybe start blocky.
A little bit blocky. So for this lettering, I'm going to pick one of my favorite fonts, which is called David. And I'm going to do it bold and centered I'm going to pick a height of about 0.75. But you can mess with that later, right? You can mess with it later too.
I'm going to click on here, hit apply. And now I have just generally kind of something close to what I want. I can move it over. I can resize it. Sorry, are you happy, Randy, with what you got there?
Well, your name looks a little funny. It does look a little funny. How would you pronounce that George? Yeah, no. Try that one.
Gorge. Go Gorge. There that a little better? Yeah. That's what I get for making that joke at the front half.
That's right. You had it coming. All right, so now that we have all of our vectors selected we could leave our CAD side, which is the left side. We go over on the right side, which is commonly called our CAM side or our toolpathing side. And this is the part that is most unfamiliar to most woodworkers, even computer people because this is where we're joining the computer to the machine.
In this case, we're going to select a type of toolpathing which is called V carving. And V carving is a little unique because it actually uses the tip of the V bit in the quarters and I'll show you that in a minute but I'm going to select all the vectors for this drawing and I hit calculate. So step one, you picked the type of cutting you're going to do. Correct. Step two you pick the lines to which you want to apply that style of cutting.
Yeah. So there's actually a couple of other things I should show you here. When we bring this up, we can actually tell it how deep to cut, so in this case, I'm going to cut it 1/8th of an inch deep for a flat depth. And then I'm also going to use what's called a flat area clear and spit. And this case I'm going to select a straight bit for the flat irons clearance bit.
So I actually have two bits a V bit and an end mill bit that I'm going to use to carve this. I kind of thought this was a two-bit operation. Yeah it was. So when I hit calculate, I now actually have two tool paths. This first one that you see here represents the large area clearance that the end mill will be used for, and if we preview that, this is actually how it's going to do the cutting on the machine.
Now this is pretty cool too because we haven't ruined a board yet. We're really seeing, this is where we can start to test the programming that we've done to this point to make sure it's going to define the shape we hope it to define. This simulation is very accurate and I run it for every cut I do. And double-check to make sure I get the results I want. All right.
So now that we've run the large iron clearance bit I'm next going to run the V bit and you can see the blue areas are, that shows where the V bit is going to come up and clean everything out. And as I mentioned earlier something that's unique about V carving is it uses the tip of the bit in the corners so watch as it carves. It's going to come up in the inside of the corners and cut them nice and sharp. And then it goes around the object. Finishing off that V carving and in little areas such as it's working right now where the larger bit couldn't reach it's going to use the tip of the bit and clean up that area.
And that I think too, it's important that you're going to do a tool change in the midst of this but if you wanted to run everything with the V you could it just would take significantly longer because you're taking out tiny, tiny. Just a little bit. Bits of material per pass, rather than what that quarter inch cutter is going to take out so draw toolpath test. I did the last thing we have to do to this one is to inscribe your name. So for this I'm going to use the same bit but we have another option here, as we were looking at this cutting.
The simulation you notice how this area is 1/8th of an inch deeper than the rest of it. So we can actually, for the text we could select that and start that at an eighth of an inch deep. Again, I'm going to select my V bit. Hit calculate and now that blue light represents where the V bit is going to come up. Does the software think you're in the field on the bottom or even with the original surface.
You can see, maybe a little hard to see but it's actually going to cut. It is cutting into At an 1/8 inch deep. Beyond the cut we've already done. Beyond the cut we've already cut. So that way it's going to cut at the bottom of that flat area.
We could see that by previewing it. And here again this is a good example of the power of V carving, because it's bringing that tip of the bit up and give you a nice clean saris of the lettering. So now that that is done I've got to save out the file paths. So the first thing I'm saving out is the straight cutting file path. And I'm going to give that a number and a name, save that.
And since the next two file paths use the same router bit the V cutter. I could save those out together as one toolpath. So is that the line in the sand on saving is as long as the bits the same, even if the operations are different you can save them with each other. Yeah. There's also a setup in here where you can save them all out in one file and it will actually call up and tell you to change the bit.
I usually save them all separately. Just keeps it a little clearer on the subject matter. Okay. So now that those are saved out we could go to the software that controls the machine and I already have the straight bit loaded up in the machine and zeroed out to the surface of the material And the bottom corner And the bottom left hand corner. So your X, Y and Z is already zero.
Right so there's three directions to think about. I'm now going to bring up my cutting file. Now conceivably, you could open the wrong file. Right, I mean, you've got to pay attention here. You could run the V bit accidentally with a quarter inch found share in there.
So there's actually an option here to make sure you've chosen the correct router bit hit secondary preview. Where you bring up and it shows you the cutting path to the extent of your cutting path is what this previous show. So that just is proof that you have the right pass selected. I now have that path already loaded up here. Hit cut again, open and start.
And now it's asking us if the correct tool number which is seven for the straight bit is in, it is, hit okay is the Z zeroed, it is. Now it's reminding me to start the router or the spindle. And the cutting is ready. Okay. So the straight bit is done.
Now I'm going to clean off the surface. Suction. And while we're here looking at the board I want to point out a couple of things. Normally we've got a dust shroud in place here and we've intentionally taken that off to increase the visibility so that you could really see the cutting action. And the other thing is the manner in which the board has fastened to the spoil board to the base here, Randy just used some hot glue on there, which is pretty cool you can't get more low-tech than that couple of dabs creating kind of a fill it on each inside corner to secure that in place.
So this is cool it automatically stopped when it knew what was done with the quarter inch bit, And now you're changing to the V. Yep. That would have changed the V bit. This will cut both the lettering and around the football area. How far does a person have to go in the CNC world to end up with a turret of bits rather than doing these manual changes?
I mean, that's a number of steps up, right? It's a number of steps up and it's the price of a small machine is to add the automatic tool changer. But that's where after a while you get used to combining your cuts, being efficient, picking the order of your cuts. So you get pretty efficient at that. So now that I have that bit installed, the one other step this is where the questions always comes up from people who are new to it is how does the bit know where the top of the material is.
Well most CNC machines have easy zeroing plates such as this. And I bring the bit over the material and lay this on there checking that it has contact and on this set, I add a grounding clip to the Arbor, to the colic, and then I run a little routine called disease iRig routine and the bit will drop down and touch the plate twice. And that will be zeroed out to the surface of the material. The machine then knows how thick the plate is. Yep.
And it's going to compensate for that on its depth cuts that you're ready to probably push the go button. It is. So George, just like before I select cut part I find my next part, which is my 02 file. And everything's in that one Actually I need to double-check. I'm going to just make double checks up to here.
I've got those two, I'm going to save those out. I always say when in doubt, find out. And in this case, finding out means re saving the file. Just to be a hundred percent sure you're about to run the V bit on the V bit patterns. Because after a while you'll end up with a lot of different files your dubrik system your filing system is really important.
And so rather than risk cutting the wrong file. So a tip here might be, maybe you need a folder. Yup. That's specific. This is project number 3-22.
Correct. And you put only these files into that folder. That's correct. So get it to ask me if I have tool number one in the spindle which is the V bit, ask me if the Z is zeroed which it is, and reminding me to turn on the spindle, which is automatic. All right let's clean that off.
Well, oddly enough, that looks suspiciously like the clip art you brought in earlier. It does. A little bit of fuzzing but that's because we're working with wood, right? Yeah. And a stiff bristle brush usually cleans that right out.
Okay. That's good to know. Well, this is cool. This is some great tips that you provided on helping people get programming, to talk from their laptop to the CNC and get it to actually produce what they wanted to produce. Yeah.
And V carvings are a great place to start because as you saw, it's pretty straightforward, pretty simple. And the options are wide open. And people would like this who wouldn't love to have a little sign with their name on it. Exactly, especially if it's spelled right. Thank you, sir.
That's important.
He stated that using a photograph would be more difficult. Is it possible to use a black and white photo and apply that to the carving? Convert to 3-D sort of? Thank You
George, Are you a member of the 4% with us? I noticed the Eagle Scout patch on the wall. Take care Ritchie
Your welcome, George, and any improvements on future videos to help novice Vcarve users would be most appreciated, I'm sure.
George, forgive me, at age 75 I may be dense, but I would like to add-to my last comments regarding your 'Go George' video. I would hope my additional comments would add to the directions given by Randy Johnson and he would assist you by providing more specific/step-by-step directions for the novice to follow. On the initial CAD or Drawing Part, when setting the 'vector' for a clip art, I think it would be beneficial to the novice to see exactly the steps taken on setting-up the bitmap and vector layers (the setup for the text layer is good). Also, to make sure the specific keys or icons are pointed out to use when required. On the tool path side, when the tool path(s) are selected it should be shown how, why and when the separate 'layer' tool paths should be selected, how, why and when each tool is used and how, why and when the different depths are used. Also, it should be pointed out to save each file path separately and to run each file path separately (please note that I am using the Rockler Sharp Pro with the Vectric/Vcarve software). I did notice how you added your spoil board to your machines deck and also how you use hot glue to stabilize the work piece. I'm going right out now to buy the material for my spoil board. And, could you provide the link for the football bitmap so us just starting out can try 'Go George'? Thanks, George, and I appreciate your time in reviewing my comments.
George ... At age 75, I took the plunge and purchased the latest Sharp Pro system and I have to point out, I've viewed a number of tutorial videos that are available on YouTube for my system, but I've found that your tutorial videos have been more positive and direct in teaching what the subject matter is. NOW ... this 'Go George' video is, by far, the BEST that I've seen in providing specific direction(s) on how to perform a CNC operation, such as you provided, and I thank you for your concerns for the novice CNC enthusiasts. I anticipate your future videos.