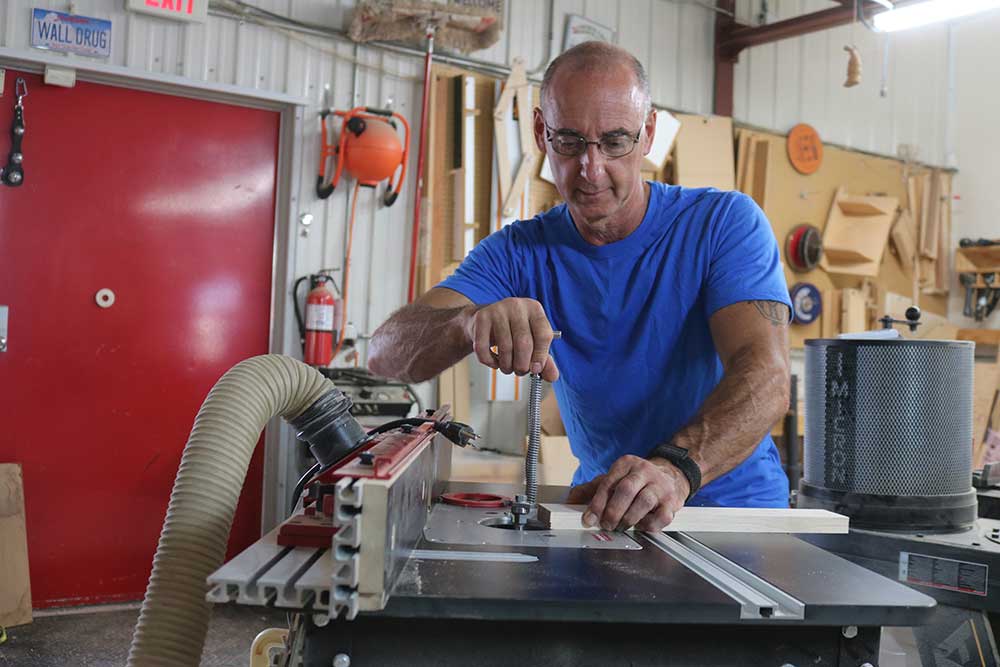
DIY Bottle Opener Handle
George VondriskaDescription
This is such a fun project, and it’s something that lots of people will like. That means it’s a great gift, or it’s something you can make and sell to help monetize your woodworking hobby.
Inlay
One of the distinctive features of the handle is what looks like a very complex inlay. Once the handle is turned, everyone will wonder how you got that stripe into the handle. Don’t sweat it. It’s very easy to do. And we won’t give away the simple secret. Well, except to y
ou.
The opener components
To make the bottle opener, you’ll need a bottle opener kit. These are available from a variety of sources. If you look around the web you’ll find some kits that don’t use a threaded insert like the kit we use in the video does. Kits without an insert are fine. Some sources suggest using a mandrel for the turning. Check with the retailer you get your kit from.
Lathe work
This is a fairly simple spindle turning project. You’ll need a chuck to mount the blank in, and a drill chuck you can mount in your tail stock to drill the hole for the opener kit.
Finish
Have you ever used cyanoacrylate glue as a finish? If not, we’ll show you how. It provides an almost plastic-like finish, which is great for a wooden item that might be touched by wet hands. There are a few tricks to getting a smooth and shiny finish. We’ll pass them along.
More great projects
If turning isn’t your thing you can still make a unique bottle opener. We’ll provide you with all the how-to you need. And when you’re ready to do more than bottle openers, keep us in mind. A little searching on WWGOA.com and you’ll find more woodworking projects.
Isn't this a great gift you could give to the bottle drinkin' buddy in your life? It's a turned handle put onto a bottle opener. It's pretty cool the way this works. The head of that'll unscrew because there's a metal insert inside. So, what we're gonna concentrate on is turning the handle.
Now, the hardware for these you can get from places that sell turning supplies, generally woodworking specialty stores will have these. If you get online and you use Google you'll be able to find all sorts of places that sell bottle openers for which you can make a turned wood handle. Now, one of the things I think that's really cool about this is that stripe. A lotta people look at that and wanna know how you put that in there, thinkin' you did it after the fact. In fact it goes in beforehand.
So, we're gonna do a couple things. In order to make a blank large enough, first step we're gonna just glue up some walnut here. Now because, when you're handlin' bottles they might be a little bit wet and your hands might get wet, I'm gonna go with a waterproof glue for this application. So, this is a glue that you know, we could really rely on no matter how wet this handle gets, the glue is gonna stick together. So when you do your blank make sure that you get the glue uniformly spread, and the pieces have gone through a planer so I know they're nice and flat and I'm gonna get good glue joints in each of the layers.
Flush up my ends. All right, so that's step one. That glue is gonna dry and it's gonna give us somethin' that looks like this. There's my three plies, I got some squeeze out. I then took this to the band saw and I made this gentle curve cut.
That's just a freehand thing. We wanna do a couple things here. One, I don't want the curve to get so sharp that the part I put in there is gonna have a chance to crack 'cause the curve is too sharp. So that's a function of how thin this material is. For the inlay material you can use veneer that you can also get from woodworking specialty stores.
The other thing that's real important is that this is right off the band saw. Don't do any sanding on these pieces 'cause if you do you might sand this one more than this one and then they're not gonna come back together. So the saw marks really don't become an issue. To help with the saw marks I use a 10 tooth per inch blade to keep that cut as smooth as possible inside there. Now same deal, I'm gonna stick with that waterproof glue to make sure that our blank, even if it's exposed to moisture drippin' off of the soda bottle, that it's gonna hold up.
You wanna have your veneer piece just ever so slightly bigger, longer than the blank itself, because the curve is gonna take up some of its length. Make sure your ends are flush. That's gonna force the curve to align with itself. All right, then we're gonna watch glue dry. Thankfully, this one's already done.
So glue is dry on this one. What I'm gonna do is get this all cleaned up, get this little bit of excess off here, square off the ends and we'll be ready for the turning step. Now what's gonna be real cool with this is when the turning is complete we're actually gonna use a glue to help provide a nice, durable surface on here, same reason as usin' the waterproof glue to make sure that even when your hands are a little bit wet that finish is gonna hold up. So next step for us is gonna be the lathe where we'll be able to do some turnin'. What I've done so far is got the turning blank in a chuck here on the lathe, and what a beautiful chunk of walnut that is.
It's really gonna pop under the finish and it's gonna look great with that accent stripe in it. Now, you're gonna have to pay attention to the particular mechanism that you get from your supplier. Here's how this bottle opener works. It's got this threaded insert. That's of course, gonna end up in the handle.
And then the bottle opener itself will screw into that. So what'll happen is we're at a point where we can drill for this insert and again, in this case the way it works is, we're gonna drill a hole, and then it's set up for an Allen wrench to go in here and we'll be able to drive the insert in. I have a piece of tape on my drill bit to indicate my final depth of cut, and as far as turning goes, what I've done up to this point is simply rounded this and just got the corners off of it. So we can get this out of the way. Get this a little closer to our work.
Well, that was boring. Now that's done. So out with that. And now we're just gonna get back to some old fashioned turning. I'm gonna get my insert in place.
And to give you the big picture, here's what's gonna happen. I've got a mandrel that'll thread into this. So, I'm gonna do a little bit of finish turning on this. I wanna get my shape a little more refined. Then, we're gonna turn this around altogether and with this mounted on the head stock end we'll be able to finish off the handle, sand it, and that's when we'll get the finish on.
So, I'm not ready to do that yet. I wanna do a little bit more shape refinement, like I said. So I'm gonna let my cone center go right into that insert and take away everything that doesn't look like a bottle opener handle. Now one of the things you wanna pay attention to is knowin' when to quit, because what we'd like to do is have the diameter of that wood equal to or a little bit bigger than the bottle opener. You can see here, I've still got quite a ways to go.
So one of the things I'm gonna do is just trace. That's gonna give me an indicator on the end grade of how far I don't wanna go. In other words, I don't wanna cut beyond that pencil line. I don't want this diameter to get smaller than that part of the bottle opener. I am just thrilled with the look of this walnut.
It's really cool. All right, I'm gonna take things apart and flip 'em around and then we'll come back and wrap up with just a little bit more turning, sanding and finishing. Alrighty, let me get you up to speed with where I'm at here. I've got the mandrel that I showed you earlier in a drill chuck on the head stock end, so that let me turn everything around. The mandrel goes into the insert, which is inside the handle.
I'm still supporting this end so that as I sand I can be a little bit more aggressive than I would be able to be if this were unsupported. I'm just about to a point where I'm ready to part that off over there. I am gonna take this up one more level of sanding. I'm gonna take it to 280. Then we'll be ready to do one more cut here in the middle I'll show 'ya and some parting on the end, then it'll be ready for finishing.
The reason I hold off on that until the sanding is done is 'cause I don't want the sanding to then take away the detail of what I just created. So, I will come back now with my 280, clean that up just a little bit more, then I'm gonna part down here on the end. To come back to this tool, if you're lookin' at that and thinkin', boy, that looks like an Allen wrench, you're right. It's an Allen wrench I turned into a lathe chisel, works really great for this detail work. All right, now we're ready for the really cool part, just in case this hasn't been cool enough for you yet.
I'm gonna lower the rpms on the lathe. I want it to run about 600 rpm for the finish. Gonna get a paper towel there on the bed of the lathe to protect the bed. We're gonna do the finishing with cyanoacrylate, or CA glue. I'm gonna use a medium viscosity of that.
What's gonna happen is we're gonna get a paper towel on here, run a bead kind of along the edge of the towel and the edge of the turning, at that low rpm apply it like you would a finish, but don't over work it. We wanna just get it on there, let it alone, let it dry, scuff it, do a second coat. If you keep messin' with it, it could start to dry and grab your paper towel and the paper towel will stick to the turning and you're gonna have to sand all that off. So it's not a friction polish like you might have otherwise used on a lathe. It's a finish that we're just gonna put on, and like I said, leave it alone.
The real beauty of this is the incredibly durable coating that we get from it. So again, in an application like this we are probably gonna touch that with a wet hand. It's really gonna hold up. Got some rubber gloves on, rpm is way down there. So, paper towel, and then I'm just gonna kinda shoot a bead of that glue along the paper towel, let that contact the turning, work it down into my coves alongside the bead there.
And that's as much as we're gonna do for now. I let this get dry and now I'm back to my 280 grit sandpaper and I just wanna give that a little bit of a scuff, smooth out any imperfections, like my imperfections. Then we'll get one more coat on there and that'll be done. Let's just stop so you can have a look at what she looks like right now. I've got sanding scratches that could build up a finish on there.
All right, it's lookin' good. So I'm gonna lower my rpm again. Same protocol, paper towel, glue, one more coat. We'll let this dry. I need a fresh paper towel.
So, the reason I switched there is that paper towel was kinda sticky, not sticky, but hard from my previous application and we want this nice and soft and pliable, otherwise it's gonna leave marks in the finish. So, frequent change on that paper towel. So we'll get some finish on here, like I was sayin', let this coat dry and then come back one more time and have a look at our finished bottle opener. That takes care of our process of turnin' a beautiful handle for our bottle opener. And, thanks to the waterproof glue that we put the layers together with and then this beautiful layer of CA glue that we sealed the outside with, even if your hands are a little bit damp that product is gonna hold up really, really well.
I love how that walnut looks. I love the accent stripe that's in there with the walnut. So now, after that dusty work on the lathe, if only I had somethin' here I could open with my bottle opener. That takes care of this project. See you next time.
Why use 3 plies of 1/2" instead of 2 3/4" Liked the video.
Where do I find plans for turned bottle opener ?
I have used CA as a finish for pens and some bottle openers, as well as for a couple of small bowls. A word of caution: Using CA for larger projects such as this releases fumes that are highly irritating, causing a dry cough that persists for several days (don't ask me how I know). Repeated exposure may result in sensitization in some people. Good ventilation is absolutely essential.
Can you polish the ca glue finish or will the friction perhaps make it a mess ?
What is the lathe you are using?