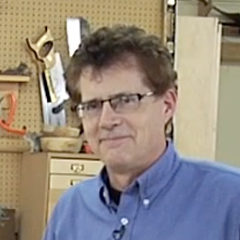
Do I Need a CNC Machine?
Randy JohnsonDescription
CNC machines are all the rage these days. They offer a lot of capabilities, possibly leaving you wondering if you should consider one for your shop. Here’s a great overview of what benchtop CNC machines can do.
I am have a ShopBot CNC in here in my shop for just a couple of months on loan. Checking it out, seeing what it does. And I'm very lucky today because Randy Johnson is here from ShopBot. And we're not doing a ShopBot ad here. What we're talking about is what benchtop CNCs can bring to the average woodworker's shops.
So first thing Randy, thanks for taking the time. Thanks George. You're gone more than your home these days. You got a pretty busy schedule, but thanks for taking the time to come in. And my first question is how do you address when woodworkers gnash their teeth over this isn't woodworking?
How does a CNC machine fit into the average woodworker's shop? Well, that's a great question George. I've got it about a thousand times in every show. And as you know, I started out woodworking in very traditional woodworking. Building Chippendale furniture, and custom cabinets, and the very typical stuff most woodworkers do.
And I got into CNC about five years ago. And what I've found is that it's like any other tool in the shop in the sense that it could extend your capabilities. It's a very capable tool and it does a variety of work. So it's really what you make of it. I mean, here's my deal on this.
I don't think it's any different than owning a table saw that runs on electricity 'cause back in the day people ripped boards by hand. Well, how traditional do you wanna be? Is it okay to use a table saw 'cause they used to rip by hand? Is it okay to use a dovetail jig 'cause they used to cut them all by hand? Is it okay to use a CNC to augment what you can do in your shop?
And I think the answer to all those questions is yes. It is, yes George. It's much like you said. The dovetail jig, the domino jig, the biscuit jig. When that came out, everybody said regular joinery was gonna go away.
But the CNC has some unique capabilities because you're able to program it on the computer to start with. And it's also a very precise machine. It's repeatability is... You can rely on that. Well, speaking of versatile, unique, and precise, you brought some great examples of stuff.
Walk us through just a little bit of the items you brought as examples of what can be done. And I'll tell you what I'd like to hear too is the level of complexity per item here on how hard is it to get the machine to make these pieces? Well, when you get into designing for the CDC, like I said, it all starts with the computer. And we can talk about more in the future, but it basically breaks down into two types of carving. You've got 3D carving such as this raised panel, and then you've got some 2D cuttings such as this little jig, this little toy that I made.
I call this the drill press challenge because it points out the ability of the CNC to cut very precise holes and have them all align. Plus where dowels aren't always a half inch. you can drill the holes to exactly match that. Some of these others. This is sort of a duplication or a simulation of a chip carving from a Swedish-type chip carving.
We have some other carvings which have started out actually on the computer. This is a rosette which I designed in the computer and then carved with the machine. And crazy difficult to... So for me, I think I may be the poster child for this. I've done a little bit of CAD on the computer but not a lot of CAD on the computer.
So is this something that I could with some practice expect to be able to do a month from now or a year from now? What does the programming feel like? There's a bit of a learning curve. If you've used some CAD programs, you're a big step ahead. The big difference for most woodworkers when they get into CNC is going from that CAD design which appears in the computer and then getting their head around how do you take those lines and then decide which router bit to assign to which line, how deep to cut it, how fast to make the machine move?
Once you make those decisions, the computer program outputs a program or a file for the CNC that drives it pretty much automatically. And we're gonna see a little bit of how the computer talks to the CNC as well. Correct. So I'm gonna, this fold thing is crazy cool. That's amazing that that was done.
I'm gonna slide this out, and I wanna bring this in 'cause this is a nice example of in the world of what does CNC bring because of its capability to machine plastic, non-ferrous metals? It'll do aluminum, plastic, foam. Anything but steel pretty much. And this gear was an example used at a education show to show people about gear making for engineers. But there's actually a app like you have a cell phone app.
There's a gear app that you can generate different sized gears automatic Wow, for gearing up. And another plate, you had done kind of a tortoise shell plate. Now riddle me this. So this is very three-dimensional. Did the CNC dome this?
Yes. And produce this? Yeah, so it actually carved the backside first, carved the curve, and then this texture was carved into the curve. One of the things I think is intriguing for me out of this as a business model is that you go through the work to give birth to this the first time. But you mentioned this earlier, the ability for the machine to duplicate this, replicate this seamlessly time after time after time is pretty cool.
If you're looking to sell these, the machine is fully capable of producing one of these or 500 of these just depending on you loading the wood into the CNS. It also has the advantage of CAD which a lot of woodworkers have experienced where you can take a CAD file and you could easily modify it. These files, in the same way you could easily modify them. Make them bigger, make them smaller. Tweak them just a little.
Tweak them up. All right, now you've got a project set up, coasters, right? Yes. Is that the deal? First thing, take us to your laptop.
And we don't need a lot of power on the computer, right? In order to work with the software. No, a typical laptop will handle the software, the two types of software. One is the drawing program and the program for creating the files, and the other program is the one that drives the machine. So what I have at the computer right now is the designs for the three coasters that we're gonna cut shortly.
And having created these line drawings, they're called vectors in the CAD world, I then- And to the vector belong the spoils, right? That's right. I then bring up my tool library and I select a tool. In this case, I'm gonna select a V-bit to create these. And this was the tool library with the different types of tools, say okay.
And I have set up some feeds and speeds. It's called how fast the machine's gonna run. Simply hit calculate, and now I have a three-dimensional view showing blue lines that actually show where the cuttings gonna take place. And this is cool 'cause it gives you such a pretty darn comprehensive look as far as what this is gonna look like in the real world when it's cut out of a chunk of wood. This simulation's very reliable.
What you see is what you get. And it actually simulates the cutting. You can see the order that the cutting is gonna take place in. You can see how many passes it's gonna take and all the details along the way. Yeah, that's very cool.
What's neat about it, once it's done you can actually go in and get an estimate on how long. So we're looking at about three minutes or so to cut these three coasters. And once that's done, you save the file out. Save it to a folder. And now we bring up what's called our machine software, the control software which is actually gonna control the ShopBot.
And before we start running here, one of the things I wanna point out is that Randy and I have intentionally removed this dust shroud that normally lives on the bottom of this piece of acrylic. There's magnets that hold it on. We've taken it off so that you can have a much better opportunity to see the cutting action. We've got another camera mounted actually right on the machine over here. And when the shroud is there of course it shrouds everything.
But when this is on one, it makes dust collection a lot better. Two, just wanted to make sure you know we've intentionally removed that so that you can see what's going on. Now you're ready to fire up, right? I am. And on your end, we can control the speed of the router, the RPM of the router.
Depending on the material, the cutter, and the cut that's happening, you can control the rate of cut, right? Correct. So very fine control that with experience and some help from the CNC manufacturer is gonna help you dial in optimal cut quality for whatever you're doing. Correct. Ready to run?
Ready to run. Hit it! So I select a file, clicked open and click start. And it's gonna ask me if my router bit is in place, if my z-axis is zeroed out? And it's gonna remind me to start the router.
And we're off and running. So this is pretty cool Randy. Go ahead and tap those babies out of there and let's see... We'll have a good look at exactly what they look like. Yeah, that's neat, and this is- That's a nice example of the chip carving type work that you talked about earlier.
Yep. One of the things that I wanna make sure we discuss is that everything we've done here has really been a relief of some kind that we've taken out of the surface. But I know that you can also use the CNC to cut completely through items. Absolutely. So in this case, the MDF on the machine is a waste board that you're gonna cut into, cut into, cut into.
And eventually you'll flatten the top of it again and cut into it some more because when you cut something like this, you are cutting all the way through this to define the shape completely on the CNC, right? Correct, the deck here is typically referred to as a spoil board because it gets spoiled and you plane it down with the large rotor bit, and then you keep using it. And when you get down pretty thin, you glue another one on and you go at it again. So I just again wanna make sure that you understand that you wanna cut an electric guitar body. You could cut the outside shape.
You could punch the holes for the electronics. Everything could be done there on the CNC. In my case with my little learning curve, and again I had a little bit of pre-experience with CAD drawing on the computer but not a lot. In maybe an hour of messing with the software, I was able to lay out signs like this. Now this one's not done.
I let it start. I didn't let it finish. That's why it's still so ridgey like this. But to just lay out the letters, and lay out the oval, and get this sign cooking wasn't really a huge learning curve for me. So it's a long way from some of the three-dimensional stuff that Randy's shown us here, but it wasn't that hard to get to this.
So this is pretty cool, pretty cool. And give us a ballpark range on benchtop CNCs like this under $3, under $10,000, under $6,000. Kind of what's a starting point for a unit like this? Well, if you look at the whole field that's out there right now, you probably have units that are in the couple of thousand dollar range on up from there. For ShopBot, we also have a small tabletop model.
It goes for about 2,800. This if our benchtop model, and then you also get a cabinet making machines which could run into 20 to $40,000 range. Capable of cutting four by eight sheets. Absolutely, for business and manufacturing. Yeah, cool, all right.
Well, thanks for the great overview Thanks George. on CNCs, and what they do, and how they do it.
I have been looking at the low end machines $250 - $800. I figured they will let me learn how to learn how to get an image from idea to a cut piece without pouring a ton of money into it. Also if I would not have time or lose interest I would not be out a lot of dough.
Where is the fun in that? I guess its fine if you want to mass produce products but I take pride in the fact that everything I build is one of a kind and made by me not a program in a robot.
I like the rep's Cheshire cat grin at 2:15 when George asked the "how complex?" That's the greatest drawback with these machines ... software geeks woodworkers aren't. And not many woodworkers under 50 want to spend thousands of man-hours just trying to master the rudimentaries.
personally I love them, I have a bench top model (not shop bot) and it's great allows me to do in minutes things that took hours before