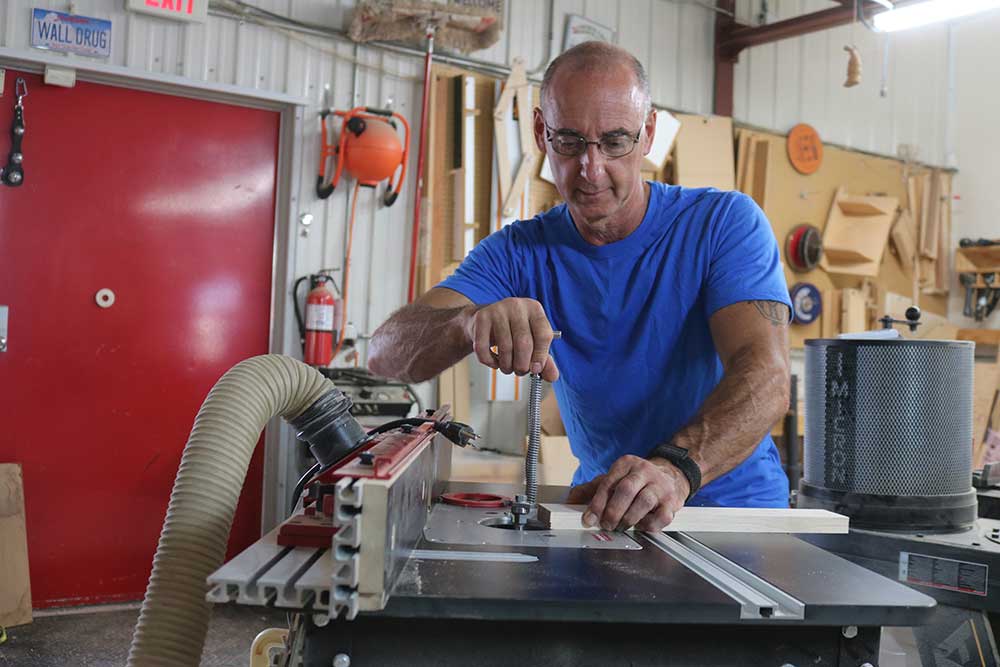
Do Your Own Milling and Save Money
George VondriskaA good hardwood supplier can do lots of operations for you: S2S, surface sanding, gang ripping, making molding, and more. To be an informed consumer you should be aware of what services are available, AND how much each of those services cost. They’re typically priced by the board foot. One way to save some dough on a woodworking project is by doing the milling yourself, provided you have the right tool for the job.
Understanding the Jargon
Let’s get our brains wrapped around what the jargon is all about. S2S means surfaced two sides, which also means milling your material to thickness. You’ll commonly ask for (or do yourself) S2S 13/16, or some other number. The number being the final thickness you want.
Gang rip means getting lots of lineal feet of material ripped to the same width. You’d use this for things like molding and face frames. It’s so much easier to send material through a machine to make this happen than it is to lean over a table saw to make it happen.
Surface sanding is similar to planing, but sanding allows you more flexibility on what you can send through the machine, and often lets you produce thinner stock that a planer would.
Making molding is just what it sounds like. What to put new trim up in your house, or for a customer? If you make your own molding you’re not limited to the species a supplier has on hand, and you can even have custom molding profiles ground for you.
More on Power Tools
If you want to make certain you’re getting the most out of the tools in your shop, have a look at the extensive info we have available on power tools.
More Info
For more information on Woodmaster tools visit their website or call (800) 821-6651.
We all know you can go to hardwood supplier and you can buy hardwood and sheet goods and that kind of stuff but there's a lot of behind the scenes operations you can have done too. And that's what I wanna have a look at, and a couple approaches to this. One is understanding those operations you can pay to have your hardwood supplier do for you, or if you've got the right machine in your shop, you can keep some money in your checkbook and do those operations yourself. So here's what we're gonna look at and define for you. S2S, which is surface two sides.
Gang ripping, which is getting parts cut to a uniform width, a bunch of them all at once, and having moldings made or making them yourself, and then abrasive planing or sanding where we're gonna, instead of a planer head on the machine, we're gonna have a look at having a drum sander on the machine and the benefits that offers. So, like I said, these are things to understand because you may pay by the board foot by asking your hardwood supplier to do it for you, or choose to just invest in a machine that'll do it so you can do all that stuff yourself in your own shop. So here's the deal with surfacing, with planing I have this done ahead of time and generally in four quarter, one inch thick I get my material S2S thirteen-sixteenths. So S2S is when I'm ordering it's good to know the jargon that the hardwood people are looking for. Surface two sides and then the last part of that thirteen-sixteenths that tells them when to stop.
So how thick do you want it to come to you? An alternative is to pick a different number S2S seven-eighths, or what is also called hit or miss. When the material goes through a planer on a hit or miss what they're really doing is just making sure that everything that's coming out of the backside is the same size. And basically they're just gonna barely skin your stack to make sure everything is uniform thickness but it's still gonna be pretty thick, pretty close to four quarters, six quarters, eight quarters when you get it into your shop. So there are a variety of operations that are available.
So currently on this machine, the planer head is in there and I've got a lovely piece of rough sawn oak which is actually a side story, a pretty cool piece of wood. This was actually a wall stud in a house that belongs to a friend of mine. The people that built the house, moved into town from a farm and they machined a lot of their own wood. You can see the saw mill marks, circ saw mark still on this. And it's pretty neat that at one point they were making their own house studs out of oak from their farm.
All right, let's do a little S2S on this baby. Dust collection works better when you remember to turn the dust collector on. Pretty, pretty piece of wood. A pretty amazing looking piece of wood. So again, with S2S you're...
when am I done is gonna be defined by what you tell them to do. Hit or miss or give them a specific number this way the lumber is gonna come to you with the rough sawn off. Wow, that's a pretty face and just about ready to go to work. Next, let's have a look at the gang ripping operation and the benefits that offers you. Hood off so we can see inside.
Planar head is out. Other shaft is in, and on that shaft, we can put saw blades. The saw blades can be positioned wherever you need them in order to get the dimensions that you're trying to produce. There's a fence here that the material rides against. So what's neat about this is really you'll see it in just a second.
Once we start the material on this side, of course it's gonna auto feed under those cutters come out this side, cut to the correct width. So it's a really easy way, think about leaning over a table saw and producing face frame material for instance. A really easy way to send stuff through a machine like this and get lots and lots and lots of uniform dimension parts out the other side looking kind of like this. What a super simple and fast and really a very safe way to make miles and miles and miles of face frame material, or base molding or other kinds of molding. And it's really a great thing to be able to take advantage of that gang rip operation.
Next, let's have a look at custom moldings. Here's where I'm at with this. Planer head is out. Obviously gang rip is out. Molding head is in, along with another fence rail so that as the material feeds under this the material is actually bound between those two runners.
And that's what gets it to feed in just the right spot under the molding head. Now, where are we going with this? Why would we do this? Well, depending on the species you wanna work with you can't always get commercially made moldings that you want. So either from your hardwood supplier or in your own shop, you could make moldings let's say you're making a cabinet out of butter nut and you want a piece of crown molding or cold molding to go with that in butternut.
You really can't walk into a store and buy butternut molding. So, an opportunity to make your own. So I get the hood put back together here and then we can run this profile. Pretty cool, I still can't get over shoving a square board in one side and getting a molded board out the other side. It's pretty neat.
Last thing here, abrasive planing, or just plane drum sanding. And another swap here and we'll have a look at that. Molding head out, sanding head in. So sanding a brace of planing. What's the deal with that?
Well, one thing is we can run stuff through a sander that you can't necessarily run through a planer. A good example would be an ingrained cutting board. On a commercial basis, if you've got any kind of man-made material you're looking to get surface, we're better off doing that in a sander than a planer. So it just provides another option for getting stuff surface. And as we go to finer and finer grits, of course in the sander, we're getting closer and closer to the finishing step and not having to spend so much time with a random orbit sander to get things ready for finish.
To revisit our topic here, stuff you can get done at your hardwood supplier, surfacing commonly called S2S, surface two sides. Gang ripping where we can very easily cut lots and lots and lots of parts to uniform width. Making moldings and abrasive planing or drum sanding on the machine and the benefits that that offer. So I mentioned earlier, one thing here is understanding all that stuff. So if you're talking to a hardwood supplier you're walking the walk, talking the talk and then you're gonna pay them by the board foot to have that done or having the right machine in your shop where you can keep a little Ching in your pocket for other stuff by doing those operations yourself.
What is the name of this tool?
What type of milling machine is that?
When milling a crown molding, I guess that you would start with the back side to remove the two angled corners and still retain a smooth back surface to allow for the proper milling of the front surface? Or, am I over simplifying this. Please elaborate.
Curious as to how the boards are held against the fence during the gang rip feature.