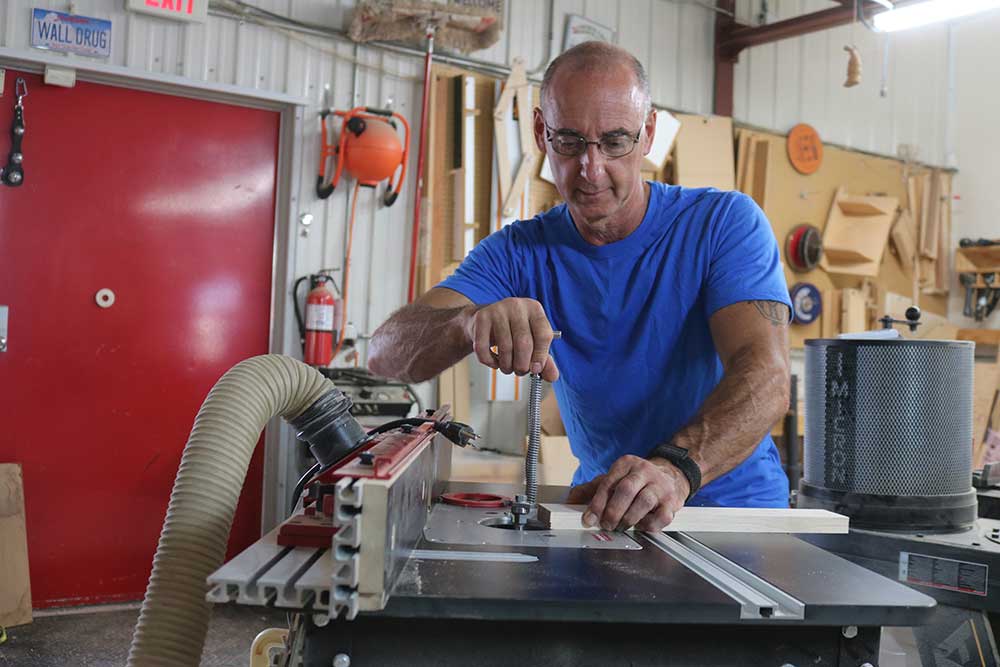
Double-sided Sign on a CNC
George VondriskaDescription
- – Controlling depth of cut so you don’t cut through when you cut both faces
- – Controlling the model position in the project when you’re using 3D clip art
- – Registering correctly when you flip the board so that both faces are identical and identically positioned.
For this project we’ll be using VCarve Pro software, and doing the cutting on a ShopBot benchtop CNC with an ATC, automatic tool changer.
Model position
Within VCarve software you can easily control the position of the model. This is done under the toolpath tab using the Material Setup function. We can use this to make sure that, when cutting from both faces, we don’t cut through, and also to position the 3D carving relative to the text.
Registering both faces
It’s easier than you might think to cut both faces of a double sided sign and make certain they’re correctly registered relative to each other. We’ll do this by pinning the project board to the spoil board. You’ll learn how to create the registration holes in VCarve, and how to take advantage of that when mounting your project board.
Cutting your project
Four bits are required for this project, and it’s hard to beat having an automatic tool changer to take the project from start to finish. No stopping and starting and redoing Z-Zero with each bit change. An ATC provides a very efficient way to cut your project.
More Info
For more information on the ShopBot Desktop Max ATC visit ShopBot’s website or call (866) 466-9939.
One of the great things about sign making on a CNC machine is the ability to do double-sided signs and guarantee that both sides are perfectly registered with each other. With your software, I'm gonna be using VCarve Pro, don't worry about having software that's designed to do two sides. We don't need it for what we're doing here. What this is gonna be all about is a couple of things. One, getting registration from face-to-face, so we know we can flip and flip accurately.
The other is, there's gonna be some 3D clip art on here that I'll show you. And because of the way I'm making the sign, we want to make sure we get that 3D clip art in the right vertical plane. So, let's have a look at VCarve Pro and how we're gonna make this happen. On the screen here, I've got a sign that I already laid out. We're gonna cut this out of a beautiful piece of sapele.
What's going on here is that this line is what will eventually be the outside of the sign. This line is an internal border. What I'm after is getting raised letters, all of this background reliefed, and then this clip art, that cool car, will end up cut into that relief background. So let's talk about that clip art first. And here's the way this is happening.
I've already Toolpathed my letters and this internal border using the VCarve Toolpath. When I did that, I set that to a flat depth of 0.125, that's 1/8 inch. What that means is that from the surface of the wood, the letters here and the border, are gonna stand up 1/8 inch, they're gonna be 1/8 inch proud of that surface. You need to know that number. The reason being, when we come here in Materials Setup and hit this Set button, this part, Model Position in Material, this shaded portion represents that car.
Right now, Gap Above Material, zero, that means that the face of that 3D clip art is even with the top of the board. But what's gonna happen here is we're about to take 1/8 inch of wood off the top of this. So, if I leave it that way we're gonna lose a bunch of detail 'cause the car is up too high. So it's a very simple solution. Right here we know in the previous step when the letter Toolpath was done, we did a flat depth of 1/8 of an inch.
So here, make that 0.125, the exact same flat depth. See what just happened there, it moved that down. This represents the amount of material we're gonna take away here in order to get the clip art to start at that lower level. Now, because we made that change it does a recalculate for us. Now, here's a little keyboard shortcut.
When I have these open and I can only see part of my drawing, if you hit F on your keyboard, it'll fill so that we get the entire drawing within the two columns, the parameters of these other boxes being open. Now, what we're after next is registration so that when we flip this over we know it's gonna be identical on both faces. The way I'm gonna do it is go to my Draw Circle tool. And I want a circle with a diameter of 1/2 inch. And I want that to go at the origin, which is the center of my board.
There's my circle, 1/2 diameter circle, right smack of the origin. What I want to do is move this out to here. And I want to have another one of those out here. And what'll happen when we start Toolpathing is, we're gonna punch a hole all the way through this and into the spoil board, and it acts as a registration pin. So when we change from one face to the other it locks us in place.
Don't click this and drag it. We want to use the software to move it accurately. Gonna click it and highlight it. I'm gonna control-C, copy, control-V, paste. That gives me another circle right over the top of that first one, 'cause eventually I need two.
Then, under Transform Objects, we want to Move Selected Object. And we have two choices here. Absolute, so absolute is, if you think of this as a piece of graph paper, where on that graph paper do we want this thing to move? I find it easier to do Relative. We're currently at zero, zero.
I want to move it straight to the left. In my case, I want to do a negative 16.5, 16-1/2 inch move. Boom. So it moved that circle out to here. Then let's pick that one.
Relative. Now, we want a positive 16.5. Boom. Part of the key is, those numbers off-center have to be exactly the same. And that's when we flip this over and use the pins to relocate this on the spoil board, that's what those holes are gonna do for us.
Looking at this now, I'm gonna do a redo. 16-1/2 is too close to this outer edge. So I'm gonna come back and I'm gonna move those to the 16-3/4. So easy peasy, control-Z, control-Z. I just moved them both back into the middle.
Highlight one. Negative 16.75. Yeah, I like that better. Grab the other one. Positive 16.75.
Then when I Toolpath these, select, hold the shift key, select the other one. I'm doing this work with a 3/8 inch diameter bit, but I'm making a 1/2 diameter hole. So for that I'm using the Pocket Toolpath. My material is about an inch thick, so I want to punch the hole about 1-1/4 deep, I'm at 1.23 I need a little bit of penetration into the spoil board, 'cause that's what's gonna let the registration pins do their thing. From there, calculate.
It's gonna tell me we're going through, which is cool, 'cause we want it to. Reset, and let's look at everything. Preview Toolpath. What do you think? So we've got a couple of things going here.
One thing I want to inspect is, is that clip art where I want it to be? In other words, did starting that clip art at 1/8 inch give me what I want? Yes it did. There are my holes. On my profile cut, I've got tabs in there.
So that that's gonna allow the border to hold that in place while we're doing this. Now, what we're doing in this case is we are using a machine with an automatic tool changer. So, we actually have to run everything twice. We're gonna run the top face, flip it over, run the bottom face. When I do the first series of cuts, we do want to have the registration holes go through.
I don't want to run the outside Toolpath. I don't want to run the profile Toolpath. When we flip it over, now the dowels are holding it in place, so the opposite happens. We don't want to punch the holes that create the registration holes, but we do want to do the profile Toolpath. So just as you're saving your Toolpath, keep track of which one we need to do where.
That's what I'm gonna do next. I'm gonna save my Toolpath to a flash drive. Then we're gonna head for the CNC machine. And we are gonna do sign making magic. Here's what's gonna happen.
I am ready to run. So the CNC is gonna come over. It's gonna do a tool change. So it gets tool number one.. It's gonna punch those registration holes, that's the first Toolpath, so that later when we flip it over, we can do that.
We've got the dust shroud off of there, as always, so that you can see the cool, sexy cuts. That means it's gonna be a little messier than this work normally is. But we want you to be able to see what's going on. So, we're ready. A little dust collection.
Get what we can. You can see how our car came out. Remember, the deal with that was, tell the carving to start at this level, 1/8 of an inch down, so that we get the full depth of cut there. I've got the other screws already out. Now, when you do this, I'm gonna clean my spoil board a little.
And I'm gonna use a screw to clean out my registration holes. Pff-pff. Pff-pff-pff. Pff. Pff-pff-pff.
All right, when we flip, you gotta do this right, or even though we're gonna have registration holes we'll mess this up. It goes end over end, this way. Not edge over edge, this way. And then, 1/2 inch dowels. Same thing on the other end.
And then all I'm gonna do is put the screws back in and press the go button again. Now, remember, in the world of Toolpathing, on this side we are not doing the registration holes 'cause they're already in place. We are doing the Toolpath that's the profile cut to create the outside shape. The internal part, the clearance cut, the letters, and the car, will all be the same. So that's cool and it's locked in place.
Don't forget, the screws are locked in place, doesn't mean we can't, or we don't have to, hold it down. All right, let's see how we did. So, we have tabs, and we have a side. And then, nah-nah-nah-nah-nah-nah-nah, and a side. So, I gotta come back and trim out the bridges, trim out the tabs.
But, two-sided sign, with both sides matching up, which is a wonderful thing. So it's all about using those pins to register you and the table. And remember, also, when we're cutting in like this, how we set the cut distance on the artwork to make sure we were working off of that new surface. So cool process, cool project. Double-sided signs.
Hi George, have been toying about jumping into the CNC world for years but knowing little about the specifics or anyone to mentor me I have not made the plunge (investment) so now I'm that much closer thanks to you.
When doing the first side you could cut the outside but only 1/2 way into the material. when doing the second side also 1/2 deep. I find this gigs me cleaner edges.
What type bits are you using with each tool path?