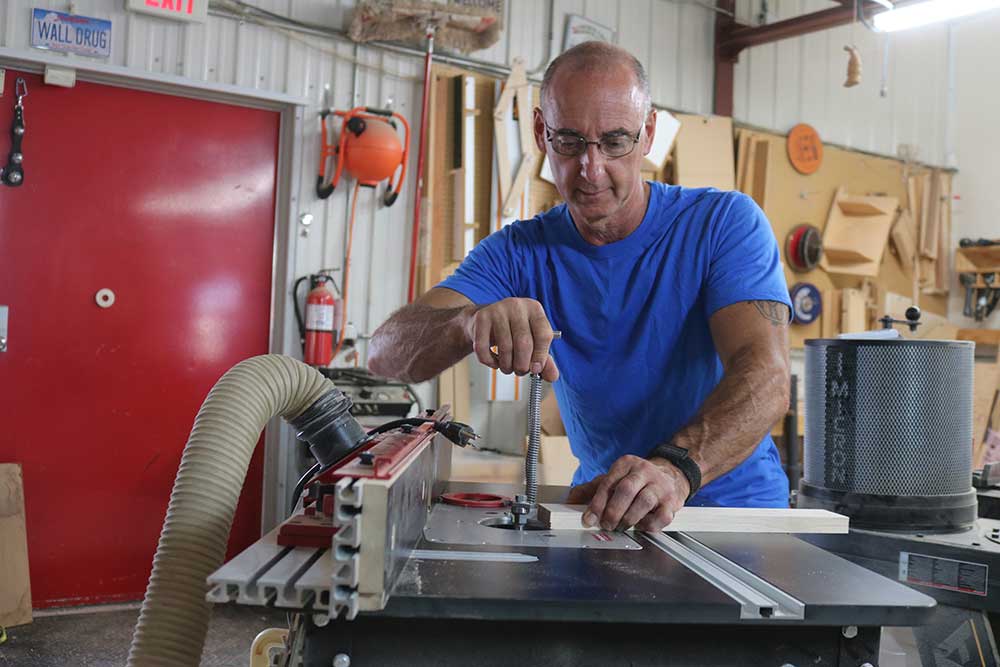
Drawer Making: Session 2: Setting Up and Using a Dovetail Jig
George VondriskaDescription
Here are the ins and outs of setting up and using a half-blind dovetail jig. Lubricating the jig, setting depth of cut, positioning the material, handling the router…each of these must be done correctly for good dovetails. No details are overlooked. We even show you where many woodworkers go wrong when making dovetails.
Before we get into setting up the dovetail jig, I want to give you a general understanding of how these babies work. And again, if your brand of jig is different from my brand of jig, don't sweat it 'cause there are a lot of commonalities between these two. Big thing here that you really need to understand is that when our pieces go in, we're gonna always cut two pieces at the same time in the case of half-blind dovetails. We're not broaching on through dovetails here at all. Whenever you do half-blind dovetails, we're gonna run two pieces at once, and we're gonna talk and talk and talk about this 'cause I want to make sure you get it right.
The horizontal component will always receive the pins and sockets; the vertical component always receives the tails. As a result, your drawer front and or back will always be the piece in the horizontal position; your drawer sides will always be the piece in the vertical position. And we'll talk more as we get going here on positioning and some of the more finite parts of making sure this gets set up. I just want to give you a part of the overview here. One of the things I've found is that a lot of these dovetail jigs have aluminum combs or templates on them, and what can happen over time is they just get kind of rough, and, you know, I can feel on this one that it's a little bit rough.
When I push the router back and forth over the top of it. it catches just a little bit. So a maintenance thing, and even if your dovetail jig is brand new, this isn't a bad idea, is to take a real fine sandpaper, this is a 220 grit self adhesive paper. I'm wrapping it onto a board, not using it by hand, because I want to make sure that it stays nice and flat. I don't want this just on my fingers where I could create an uneven surface.
Aluminum is fairly soft. Then we just want to stroke across this thing a few times, and that's gonna take out any ridges, and if you've got a dovetail jig that you've had for awhile, and you've never done this, and then you do this little maintenance step and come back and use the jig again, you'll be amazed at how much better it works for you. That's all that that's gonna take. I can feel a lot of that little pitting and high spots and stuff, they're all gone. Now, what we just did is we got that nice and flat.
Like any tool in our shop, we want to make sure that the tools can play nice together, that our router base can very easily move across the top of the tool here. To make that work, I'm gonna use a tool-specific aerosol lubricant for this. Tool-specific is real important. The last thing we want to do with any tool in our shop is introduce any silicone to it. If you do that, you can get silicone on the surface of your material.
You find that out when you go to put finish on. The silicone will basically seal that up, and when you apply a stain or a topcoat, it's not gonna stick. If you've ever had fisheye little kind of bubble spots where finish doesn't take and tiny, tiny tiny little pinpricks in your finish, a lot of times that's caused by silicone residue left in the wood. With this stuff, there's no silicone in it, we'll shake it up to get everything mixed together, and then just spray across the top of that comb, and we're gonna spray the bottom of the router. This is the same stuff I use on my table saw, jointer bandsaw, planer bed, any place where parts are gonna work one against the other or where material is gonna slide across that part.
Now, on my dovetail jig, I'm not concerned about specifically getting it down here or here, because, yes, we're gonna insert material in there, but we're not asking that material to slide back and forth like it does on a jointer or a table saw or a bandsaw table. All I want to do is the comb and the bottom of the router. See how that's started to turn grayish now? That's telling me that it's dry. So what happens is there's a wet aspect of that aerosol, that flashes off, it leaves that lubricant behind.
Take a rag and clean that off, and then buff this out. The alternative to the aerosols for this would be a paste wax, and that's fine as long as it's a paste wax that doesn't have any silicone in it, and generally what that means is you want to stay away from automotive waxes. So what's called a carnauba-based paste wax, look for that on a PDF that accompanies the video, is an alternative to this. Basically, I'm lazy. The aerosol is so much easier to spray out and wipe off than wiping on a paste wax.
I really like the aerosol product. While we're still talking about the jig, we've already touched on this a little bit, but please do make sure that you're using the correct dovetail cutter and correct guide bushing for your dovetail jig. Now, in some cases, some of these jigs, instead of a dovetail bit and a guide bushing, there's a proprietary dovetail cutter that will have a bearing on it, what's called a pattern style dovetail bit. That bearing is then what will ride in and out on the comb. If that's what your jig calls for, that's what you have to use.
The angle on the dovetail cutter is typically specific to the jig, so again, the importance of making sure you got the right bit. With the guide bushings, you can generally tell that you're using the right one if, when you put it into the comb, it doesn't wiggle back and forth. So the fit between the shoulder on the bottom of the guide bushing is usually exactly the same as the space between these fingers. So again, make sure that that's the right diameter for what you're doing. Last thing we want to talk about here is just making sure that this dovetail jig is in a comfortable position for you.
I've watched lots and lots of lots of students cut dovetails in woodworking classes, and one of the things to go wrong is that, as they're cutting the dovetail, sometimes depending on body position, they tip the router like this, and you can imagine if the dovetail bit is sticking out and I tip the router and move forward, it's really gonna mess up our cut. One of the things that helps that a lot is trying to get the top of the jig, the comb, about even with your elbows if you can. In my case, I've got an adjustable height work bench so I was able to pull the bench up so that my dovetail jig ends up just where I want it. If your bench isn't adjustable, the answer might be in a base that you build below the dovetail jig like I've got on this one. In addition to raising the jig, there's drawers on the backside that allow me to store all the stuff I need to go along with this dovetail jig.
So again, the important side of this is the comb about even with your elbows so that when we're running the router, straight in, straight out, straight in, straight out. It just makes it easier to get everything to come out perfectly. Keep those tips in mind about half-blind dovetail jigs. It'll go a long way toward making sure you're using yours correctly. Before we do any kind of cutting or anything on the jig, we're gonna spend some time talking about positioning material, 'cause it's crazy critical that you get this exactly right when the material goes in.
First thing, on a lot of these jigs, the combs can be loosened and raised and lowered. So I'm gonna do that. I'm gonna get this up higher than it needs to be, and then show you how to get that in just the right position. Next thing, to position the verticalosity of that comb, you want to get material that you're gonna work with for your drawer front. So this stuff is the exact same thickness as the drawer front that I'm gonna make.
Slip that into the jig, and then gravity is your friend, just let the comb rest on top of that. Usually what I do is just a finger's worth of pressure, lock that in place, finger's worth of pressure, lock that in place. That registers the altitude of the comb. Now, when the material goes into any half-blind dovetail jig, it's important that you get this just right. On the jig, there'll be a stop of some kind.
We're gonna talk more about these stops later. It's very, very, very important that when I'm working on the left side of the jig, the left edge of our material goes against the stop. The horizontal piece, remember, is our drawer front, so I'm gonna go against the stop, and I'm just gonna leave that to sit there. I'm not worried about forward to back just yet. Vertical piece is always our drawer side.
That's gonna come up. I've still got a stop, a shoulder here. That's gonna go against that shoulder. This comes up until it kisses, not pushes on, that's very important, until it kisses the bottom of the comb. And then I'm gonna lock this in place.
Now, that at this stage, that lock is not gonna be forever. We're still gonna do some micro-adjusting. Looking down from the top, what we can see, there's a gap between the end grain of our horizontal board and the face grain of our vertical board. We need to close that gap. Now, remember how I said your vertical is gonna come up until it kisses the bottom of the comb so we don't want to distort that comb position?
Similarly here, horizontal is gonna come forward until the gap closes. Don't pull on this 'cause we don't want to pull this whole assembly forward, it's possible to do that, we just want to kiss the back. At the same time, remember our stop on this side. We're holding it right to left tight against that stop. Now lock that piece in place.
Now, earlier I said, "We lock this, "but we're probably not done yet." Our final check on this piece is running fingers across the top. This end grain needs to be even with this face grain. That should be accomplished by kissing the bottom of the column. In this case, there's just a tiny discrepancy there. There's just a little fingernail catch.
I'm gonna loosen that vertical piece, bring my vertical up just a little bit, check for flushicity like that. At the same time, pushing right to left, holding this against the stop. Now, before one would do any test cutting, the double-check on this is, looking at through here, I'm checking, is the edge of my board up against the stop? Looking down this way, is the edge of my board up against the stop? Additionally, then, no gap between the end grain and the face grain.
Give it a feel across here. Make sure those are flush. Once we had a router bit set to the right height, we'd be ready to cut a dovetail joint. The more of this you do, the more natural all of this setup is gonna become. It's not gonna take so long as it did now when I'm walking you through it step-by-step.
But the jig can't do its job if you don't get the boards in here correctly. Now, for some of the cutting that we're about to do, we're gonna use the left side of jig; for some of the cutting, we're gonna come over here and use the right side of the jig. Everything over here is a mirror image of what I have over here, and the setup will be exactly the same. So you'll see this happen a bunch of more times yet here on the video, but I want to make sure you've got a good understanding of making sure you're getting your parts and your jig with the correct orientation and the correct engagement between the pieces and between the pieces and the stops. The material is still set up in the dovetail jig, so we're just about ready to try a test cut on this stuff.
A couple of things, the material needs to be the same as what you're gonna make the drawer out of. In this case, we're gonna do our drawer for the video with poplar, and I've got poplar in here for the test cut. The reason for that is that we want to rely on these characteristics being the same as the drawer's characteristics. Here's an example. If I do my test cut in pine but I'm gonna build the drawer out of maple, it's possible that a dovetail that's a little bit too tight will still go together in the pine 'cause those soft fibers will compress.
Too tight in the maple, the exact same fit could cause the maple to crack. So it is really important that we do our test cuts in the same material that we'd be doing the real dovetail in. With my router still unplugged, I've installed my dovetail bit and my guide bushing. Following the instructions in the owner's manual, I set the depth of cut. Now, in my experience, it's hard to get that depth of cut perfectly dialed in, reading this with a ruler and setting it up.
The test cut is gonna tell us everything. The fit between the tails and the sockets will tell us if we're just right, too deep, or too shallow. I'll walk you through all of that. I want to make sure we've got hearing protection ready, 'cause routers are loud. And this is gonna throw a lot of dust this way; great time to have a shop apron on so you don't have snowfall of sawdust all over the front of you.
Now, when we do the cuts, it's gonna be a two-step operation. In the first pass, what I'm gonna do is run the router bit left to right, barely scoring this face. Let me do that first, then I'll talk about why, and then we'll come back and talk about the next cut. In addition to that cutting operation, let's talk about router on, router off. Notice that I set the router on the dovetail jig.
I made sure the bit was not touching the work. I turned it on, made the cut, released the trigger, let it come to a complete stop, then come off the work. So what you don't want to do is turn the router on, then come here, 'cause it's too easy to contact the wood or the comb. Similarly, if it's still spinning when you get to the end and you lift it off, it's possible to hit the material or the comb and you'll ruin either one. Now, let's talk about what I did there.
I scored, I put a shoulder in the face of the material. The reason I did that is that on our next cut, we're gonna enter, exit, enter, exit, enter, exit, and what I've found is that if you don't do this first, in some materials when you make these cuts, you can get chips down the face, especially if you make a drawer out of something like birch or Baltic birch plywood, very, very chippy. Doing this first is a preemptive strike to make sure that any chipping you get can't continue down the face of this board. Next thing, router comes back on here. We'll follow the fingers in and out.
The guide bushing is exactly the same size as the hole in the comb. So we're gonna go in, follow the finger, go in, follow the finger, go in, follow the finger all the way down. We don't have to go left to right when we're in the bottom of the socket on this jig, because the guide bushing and the internal dimension are the same. Couple of things before that material comes out. One, look at the backs of the tails here, and they should be nice and round just like these fingers are nice and round.
As I look at them, on this one, there's a flat spot right there. That tells me that I came out too far, went over, went back in without following that finger. If we notice that now, it's really easy to fix. I can put the router back on here, turn it on, and fix that. If we take the pieces out and then realize it's there, it's gonna be much harder to fix.
If we don't fix it, that tail will not fully insert into the socket. Let me take care of that. Now, before the pieces come out, I want to talk about something we haven't hit on yet, and that is the very intentional offset that's created between these two parts. So when you look at this from up here, you can see that my vertical board, my drawer side, is past the edge of my horizontal board. They're supposed to be that way, because now, the reason I waited until now to point this out, you can see that when I make a socket here, the tail that I cut is adjacent to it.
That's why there has to be an offset. When we fold this joint pack together, this tail goes in that socket, this tail goes in that socket, such that, we were like this, now it's gonna come up and go together like this. Is it gonna go together? That's the question. Clear the decks a little bit so I can work on the bench.
What I'm looking for is some gentle tapping to drive those together, and I can tell by the sound, that's just, there's way too much resistance for that to go together. And if I just keep driving on it, they'll go, but I'm probably gonna crack my pin and socket board. The deal with half-blind dovetails, too tight, too deep. Here's what I mean by that. When the fit between the tails and the sockets is too tight like this one is, the projection of the bit, the bit is sticking out of the router base too much, the bit is set too deep.
This is where this business with the fixed base router and a micro-adjust really pays off. The bit's sticking out too far, routers unplugged. I need to bring the base up to shallow up my depth of cut. How much? Yes, a little.
Tiny, tiny adjustments here, and then we'll sneak up on a good fit on this joint. I'm gonna unlock my router, gonna bring that up, I'm gonna reduce my cut. Now, I am gonna show you a trick once we have a good fitting dovetail that we can do some shortcuts here to get to a good fit faster. All right, now we'll move along a little more quickly here. Material in the horizontal position, material in the vertical position against the stop, kiss the bottom of the comb, lock that, bring this forward up against the stop, make sure it's kissing the back of that piece.
Check flushicity across the top, needs a micro adjust. That's more better. All right. So very laborious the first time I slowly walked you through that. But once you get used to using the jig, you can see that that's gonna go a lot more quickly to get those parts together and get ready for a cut.
Now, in my first case, what I did is I made the scribe cut, a scoring cut. Then I stopped and talked to you about it and then came back and did the in and out. Normally, I score it and then I just come right back and go into the comb. That's what I'm gonna do here. Visual inspection, back of the tails look good.
Tappy tap inspection, that's better, but that's still too tight. Second verse same as the first. I'm gonna keep going with my setting here. Now, if it's too tight, too deep, then the opposite is also gonna be true. If it's too loose, it's too shallow.
If you find that the fit between the pins and sockets and the tail is looser than you want it to be, then your router bit is not set deeply enough. It's just the opposite problem. Now, as long as we're gonna make another cut, let me talk about some subtleties of what's going on here that I want you to watch for on this one. Yes, we're doing a dovetail with a router and a dovetail jig, and that really simplifies making a dovetail, but the manner in which you run this still takes some practice. I want you as much as possible to make these cuts with your hands, not with your entire upper body.
You've got good control of small movement here. This is more about big movement. Remember, I've seen lots of students cut dovetails with this thing, and one of the things I've noticed is that if you're doing a lot of upper body movement, you're more likely to tip the router. You may have noticed on these first couple of cuts, I'm prone to letting the bottom of my right hand rest on the jig, and then my fingers are pulling the router along. Fingers are good for small movements; shoulders are good for big movements.
So it does take some practice to make sure that we're controlling the router correctly. Big, big thing to avoid is any tipping. Hopefully three is the charm. We're gonna find out in a second here. That's what I like.
Good fit, went in with tapping, I didn't have to pound on it. Again, the material that we're using here is exactly the same as what we're gonna make our drawer out of in a little bit. That's very important. Now, a good question at this point would be, I've talked and talked and talked about these stops, now I can talk about what if I don't hit the stops? What if I make a mistake there?
What the stops do for you is they provide a guarantee that these edges will line up when the joint comes together. If you're missing the stops on one or both pieces, these edges are not gonna align, and, he can say from experience, there's no fix for that. If you have that incorrect when this goes together, there's no way to make it right. So the test cut's telling me that this is a good fit for my dovetail. That's telling me my dovetail bit is the right depth.
Now, I promised you that I'd give you a shortcut for next time. This is a good fit. Drill a hole in this and hang it on the wall somewhere by your dovetail jig. The next time you're gonna use this, instead of measuring the height of your bit, put this in the jig, unplug your router, and set your depth of cut so that the bottom of the dovetail bit is kissing that shoulder that we just cut. The part that we just made becomes a depth gauge for the next time we're gonna use this.
I'd still do test cuts first to make sure that it's right, but this is gonna get you really, really close to having a good fit faster. One of the things that's really cool about half-blind dovetail jigs is that they are not thickness-specific. In other words, when we know that depth is right, whether we're doing drawers in half, 5/8s, or 3/4-inch material, that depth of cut will always be right. So hold onto that board, use it as a gauge block for the next time we're setting a dovetail jig up. That takes care of our test cutting.
We now know that we're good to go to move forward to start working on drawers. Before we can actually cut a drawer, we gotta talk about what you need to do to make sure the drawer parts come out the right size for the opening, and there are some parameters here on the dovetail jig you need to understand to get that to work. Part of what I want to talk about with dimensioning is not to do with the outside dimensions of the drawer box, it's more to do with the layout of the dovetail. So here's what I mean by that. Here's a dovetail gone badly.
When you look at the tails on this one: full tail, full tail, tail, tail, tail, tail, then down at the end here, we've got this funky little half tail. When we marry that in to the pin and socket board like this, that means we've also got this odd little cut-out here at the end. My preference, whenever possible, is to get my dovetails to come out so that on the pin and socket board, we've got a half pin on this side then a similarly sized half pin on this side. Then, with our tails, what that means is full tail, full tail, with a little shoulder on each side. That's where we want to end up.
How do we get there? Well, there's a couple it depends. On some dovetail jigs, including this one, this stop is adjustable. On this one, if I loosen this, I can change the position of that stop. What that in turn allows me to do is change the position of my material under the comb within the travel of that stop.
So what that means is that I can get my material where I want it. Using my vertical board, I would bring it into the dovetail jig, position it so that the space from finger to edge on this side and finger to edge on this side is the same, lock that in place, then bring the stop over, lock the stop in place. Now every piece I put in will go in that same position. Controlling the stop for the vertical piece automatically controls it for the horizontal. So I only have to do this once.
Then we'll talk about mirroring this on the other side. Now, on other dovetail jigs, what they do is they might have a stop that's in a fixed position and can't be changed. As a result, when I put my material in, it's gonna fall where it may. It's gonna fall where that stop tells it to fall. If that's the case with your dovetail jig, then to prevent this from happening, we control the width of the board.
So what I mean by that is that on this board, if it were only this wide instead of this wide, we wouldn't have this funky little half tail out here. So what you need to do is do a test cut, if you've got a fixed stop, if you can't change the position of your stop, cut a dovetail, and keep it forever as a gauge, and then what you're gauging is, well, okay, if my drawer is a little over two inches wide, I'm right between those two tails. If I'm three and a 16th inch wide, I'm right between those two tails. If I'm four and a 16th wide, I'm right between those two tails, on and on and on and on. That'll help you determine how wide your parts should be so that you end up with even space, even space on both sides.
If you get into a scenario where you absolutely can't do that, in other words, the drawer box has to be a certain size and you're gonna end up with this as a result, it's not a deal breaker, but it's something that we would rather avoid if we can. That talks about dimensioning relative to the jig. Let's talk about dimensioning just relative to dovetails. We need to know a couple things. Your drawer front, which is right here in my hot little hands, the length of the drawer front will be continuous from left to right for the dimension of your drawer box.
So in other words, if to fit the opening we need a 12-inch-wide drawer, you're gonna make your drawer front 12 inches long. On the sides, they butt into the drawer front, and then there's this little bit of wood right here at the end grain of the tail. So let's say we're using 16-inch drawer sides, and as a result, we want a 16-inch deep drawer. You do not cut your drawer sides to 16 because of the way the sides butt into that small bit of material in the front. What we need to do is know how big that is.
Easiest way to do that is to measure it with digital calipers. This dimension that I'm getting, in this case it's an eighth of an inch, will vary depending on the thickness of your material. So probably, project by project, you're gonna have to, once you have a test cut done, measure this in order to determine the final length of this piece. If you're dovetailing front and back, one of the options I talked about earlier, then we're gonna take this dimension times two, subtract that from the overall length of the drawer, that would give us the length of the side. Gotta do a little bit of math there to make sure that your parts are gonna come out okay.
That takes care of dimensioning the drawer. Now, before we go to the tool, we want to make sure that we have parts identified so that we can tell how the drawer is gonna go together. Much easier to do that here at the workbench than it is to mess around with these parts at the tool and figure out what's what. What I do is lay out the drawer the way it's gonna go together. How's that for a catch?
There we go. Front, front, side, side, then we can start labeling. Now, keep in mind as you put your labels on that the inside of the drawer box is gonna be up in the dovetail jig, and the inside of the drawer box is gonna be facing out in the dovetail jig. So I like to put my labeling on what will be the inside face. So I've got all my parts set up.
Then I can open them up like this, and I'm gonna label top. And then as I work my way around, this is gonna be joint number one, this will be joint number one, this will be T for top, and I'm not worried about the back corner 'cause we're drawer locking that, T for top, coming over to this corner, joint number two, joint number two, T for top. If you're doing more than one drawer, don't keep using one and two, then use three and four, five and six, seven and eight, so that when we cut those two parts together, they're gonna go back together. On my back one with the drawer lock, I'm simply gonna put an X on here for now indicating that that's the inside face of my piece so we know that later. That labeling is gonna be a great roadmap, you're gonna see it in just a little bit, to help us make sure that we're getting the parts in the dovetail jig exactly the right way.
So that talks about dimensioning, talks about taking advantage of your dovetail jig to make sure the boards are going in there the right way relative to that stop, talks about layout to make sure you're putting them in the dovetail jig the right way, and gets us really close to being able to cut our drawer parts. Before we can actually cut dovetails. We do have to finalize the setup on the stops because on this jig they're adjustable, so I want to make sure that whatever I'm doing on the left side is the same as what's gonna happen on the right. We'll use both sides of the jig. A way to make that happen is to take one of your drawer sides and position it in the jig so that we're getting that spacing that we talked about earlier, which is I have the same distance from finger to edge and finger to edge.
I'm gonna go to my right just a skosh. That looks great. That's the position in which I want to cut this side Take my stop, push it against like I did earlier. Every part I put in subsequently is gonna be exactly in that spot. Now, the question is how do we know that we're gonna get the exact same setup on the other side of the jig?
Easy, easy, easy. What we're gonna do is trace this finger, the first one, trace the left side onto the board, and that gives us that little registration mark. Basically, then, that's the distance from the finger to the stop. So I spin this around, bring it to the other side of the jig. The stop on this side is way out of the way.
Make that line even with the edge of the finger. Bring the stop over. Snug it down. Now, the deal with doing this, what we're buying here is that the top of the boards, which we labeled just a little bit ago, will always go against the stops. Because of the step we just took, the distance from the top to the first, second, third, fourth dovetail will be the same on the left side and the right side.
It's a small step, but it buys you some really nice consistency on laying out your dovetails. In order to cut, we have to look at our parts. And one of the things we know is that the top of the board is always gonna go against the stop. So top against the stop, see how that works out? When we cut number two end on our vertical, on our tailboard, it really needs to go with number two on our pin and socket board.
So that tells us these boards have to go like this. We should always be able to see the marks. We labeled the inside of the drawers. So we should be able to see our layout lines all the time. Top against the stop, top against the stop.
As a refresher here, kiss the bottom of the comb, lock the vertical, bring the horizontal against the back of the vertical, make sure it's against the stop, that it's closed there. I'm just increasing the tension on this hole down here. There we go. No gapicity between end grain and face grain. Check for flush.
That feels great, looks great. A couple of visuals: is T for top against the stop? Yes. Two here, two under the comb, that tells me I'm cutting in the right position. Close there, flush there, should be good to go.
Visual check to make sure everything looks okie and dokie. That's great. The vertical board we're done with for now. The horizontal board is gonna come out. Now we want to cut joint number one.
If I spin it like this so I can cut number one, T for top against the stop, we gotta use the other side of the jig. Roadmap is telling me I'm ready to cut number one. So I gotta find the board with number one, T for top against the stop. Kiss the comb. Bring the horizontal forward, close the gap.
Tight to the stop. Feel for flush. Oh, I got that one right the first time. If we were taking this a step further, if we were dovetailing all four corners, we would have another number on here, T for top against the stop, so that's gonna come back to the other side of the dovetail jig again. As long as you correctly label your pieces, it's gonna make getting them into the jig over here a lot easier.
It's really important to me that you label your parts so that when you get here, you're not fumbling around with the pieces, trying to figure out what goes where. You've got pencil marks on here that make it very easy to follow a roadmap and tell you exactly how those pieces get configured into the jig. I have seen this in my classes all the time. We know once we have a good setup on the dovetail bit that the dovetail is gonna go together, but I know at this stage of the game, people like to see their dovetail go together. So go ahead and tap it in there so you can see the beautiful dovetail you just cut.
But you don't really have to do that, but there's a nice feeling of reward out of that. That takes care of cutting our front dovetails here on our half-blind dovetail jig. They really look great and they fit great. Sometimes, you know, the best laid plans of mice and men and dovetail jigs don't quite work out. So I want to talk about a couple things I've observed in myself and in my students about where things can go kerflooey here.
Turning the clock back a little bit to setup, let's talk about this, which is the face of this board, the tailboard, meeting the end grain of the pin and socket board. If you tap these together and that goes on and on and on and on, and the end grain is sticking away past the face grain, we can fix that. Or you tap these together and you find that this didn't go in far enough like this, we can fix that. Let's have a look at the dovetail jig. You might have to read the owner's manual.
On this particular one, the way that it works is that the front-to-back position of the comb can be controlled by loosening this knob and then turning this knurled knob behind this bracket. If I turn this clockwise, it's gonna move this big knurled knob that way. That lets this comb go deeper into the jig. That would allow me to cut deeper sockets. So if we have this problem, which is the face is above the end grain, we gotta go deeper.
If we have the opposite problem, which is we seat it in too far, then we'd want to back out that knurled knob on both sides and bring this forward. Now, again, your jig, your owner's manual, you're gonna have to have a look and see what that adjustment is, but there's gonna be some way to control that front-to-back travel. Now, from an operator perspective, couple things. I've seen people come to the jig and do this board placement opposite of what we should do, which would be, I got my comb down a little too tight, there we go, instead of doing my vertical board with my horizontal kissing the back of it, I've seen people do horizontal board out, vertical up kissing the bottom of the horizontal. That ain't gonna fly.
When we cut this dovetail, we're gonna cut really deep sockets into this board. You're not gonna even touch this one. No fixing that. So keep in mind the sequence in which the boards go together. A very, very common one is for people to get so hung up on this alignment, which is very important, that they forget about making sure that they're tight to the stops over here.
I talked about this earlier. If you miss the stops, when you put your dovetail together later, the edges of your boards are not gonna align. There's no fix for that. So our double-check here, mentioned earlier, is to make sure that once this is right, we also make sure we're seated against that stop. That provides this overlap we have out here on this corner, which provides our alignment that we're gonna have on both corners when they come together.
Another very common one is when the dovetail is being handled on here, I'm sorry, when the router is being handled on here, that that router gets tipped like this as you're making the cut. And you can imagine, because of the shape of that dovetail bit, if I'm in the board and that rocks up, I'm gonna pull that wider part of the dovetail cutter up through the material, and I'm gonna ruin the dovetail. This all comes back to me talking about body position, hand position, controlling this router with your hands and fingers, not with your whole upper body, so that we keep that router base nice and flat on the jig and stay away from that tipping. Another big one I've seen is having that router still spinning when this gets lifted off the dovetail jig. If you do that, carbide is gonna win over aluminum or plastic.
You're gonna cut into that comb, and you're gonna have to replace it, because any mistakes, any bobbles you have in the comb will telegraph into your dovetail. Another big one, and I mentioned this earlier, coming out too far means then when you do this rounding leaving material on the outside of the tail, which prevents it from seeding into the socket. That's an easy one to fix as long as you notice it while the material is still in the jig. Those are some of the most common problems I've seen. Hope you won't have them.
But remember that, yes, we're simplifying the whole dovetailing process by using a dovetail jig. However, like anything else, this still takes practice. I can buy a really, really good guitar, and it's not gonna make me a better guitar player just owning a good guitar. Just owning a good dovetail jig and a good router isn't gonna make you a better dovetailer. It makes it easier, but you still gotta get on here and practice all the stuff I talked about to make sure that you're setting this up correctly and using it correctly.
That takes care of the dovetail information that we need for dovetailing our lifetime drawers.
Share tips, start a discussion or ask other students a question. If you have a question for the instructor, please click here.
Already a member? Sign in
No Responses to “Drawer Making: Session 2: Setting Up and Using a Dovetail Jig”