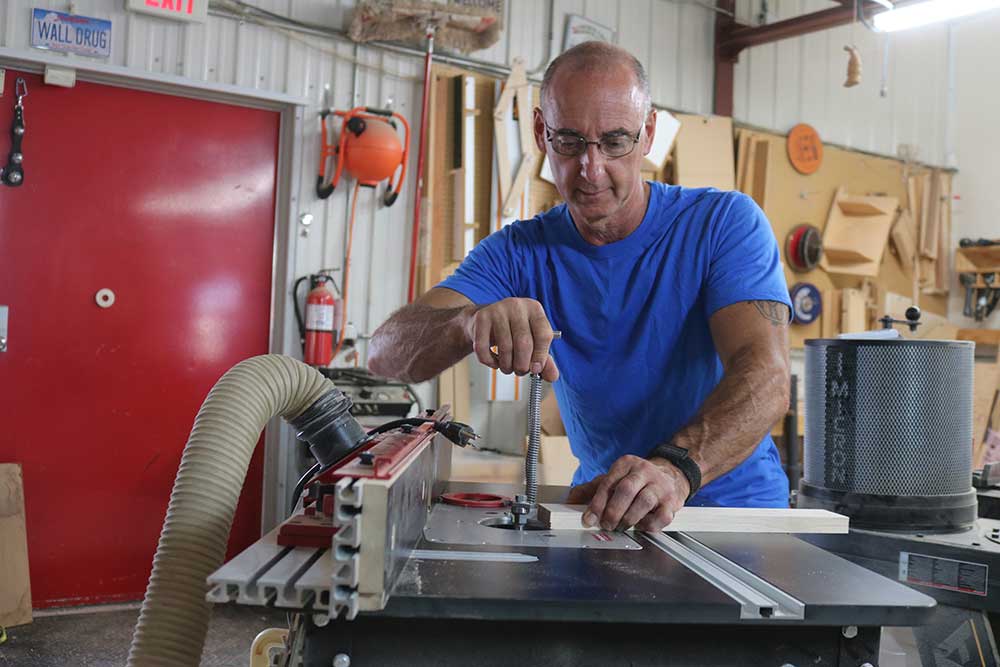
Franklin-Titebond Shop-Made Wooden Try Square: Part 1
George VondriskaDescription
It’s always cool to make projects that improve your shop. And it’s really cool, and fun, to make your own tools for your shop. In this video we teach you to make a wooden try square. Not only is it functional when it’s complete, it also looks great. The project calls for small pieces of wood, so here’s an opportunity to use some of that beautiful scrap you’ve been keeping. This is a two-part project. In Part 1 you’ll learn how to prep the pieces to ensure a perfect fit and easy assembly, and a great trick for capturing the blade in the handle.
Titebond Original Wood Glue, Titebond III Ultimate Wood Glue, and Titebond Instant Adhesive provided by Titebond. For more information, visit www.titebond.com.
More Videos from Titebond:
Franklin-Titebond Shop-Made Wooden Try Square: Part 2
How To Install Crown Molding on Cabinets
How to build a Birdhouse
Adding Accents to Outdoor Products
Calculating Wood Dimensions for Outside Corners
Super Finishing for Turning
Adhere Ceramic Tile to Wood
Create a Crackle Finish on Wood
Glue Squeeze Out that Glows
Unlock Your Woodworking Potential!
Sign up for our newsletter for endless woodworking inspiration! Become a member today and gain access to a world of craftsmanship.
I know that people love making stuff to improve their shop. It's a great way to take advantage of your woodworking skills. How's this for a cool project to improve your shop? You can make your own try square from hardwood scrap that you have laying around. It's simple process I'm gonna take you through. Now, be sure to look for part one and part two of this series to get you through all the steps, start to finish. Here's what you're gonna do to get rolling on this. We have to prep a couple pieces, and there are a few things that are real important. We want parts for the handle that are one quarter by one and a half, and if you make a piece that's about 18 inches long, you'll have plenty of wood to work with. For the blade, we're gonna make a piece that's a quarter inch thick, one a three quarter wide, and we only need this to finish out at eight inches. But, it's a little easier to work with if you start with a piece that's a little bit longer. Now, here's the critical thing, this'll make sense when we put everything together. These parts need to be exactly the same thickness. 'Cause what we're doing here is we're using kind of a bridal joint type assembly. The way that we're gonna make that happen is with layers of wood, so when we put these layer together, in order for the blade to slip into the joint, that has to be exactly the same thickness as that center layer. So, when you make up your parts, make sure they're exactly the same thickness. Hit this one more time. One and a half wide or the handle pieces, one and three quarter wide for the blade. So, get those parts set, and what I'm gonna do is I'm gonna get these cut to length, we'll come back and talk about what those lengths are, and look at the assembly step. I've got my parts cut to length, and here's what those lengths are. The center piece of the handle, the one that eventually the blade is gonna go up against is cut to four and a half inches long, the two outer pieces are cut to six inches long. Now, we're gonna use a couple different glues in this process, conventional yellow glue is fine for the step that we're doing here. I'm gonna butter up both sides of this center piece. Wax paper on my bench, so I don't get glue all over it. And, when you put this together, what you want to do... You know, sometimes parts can slip a little bit when you're gluing them. So, make sure that the edges stay nice and flush, and the end grain stays reasonably flush. Doesn't have to be absolutely perfect, but it's nice if it's pretty darn close. Just gentle pressure on that first on for now, 'till I get the second one on. Making sure I'm registered, I'm flush across the top. And then, you can see how we have that gap there that the blade is gonna slip into a little bit later. Now, that's gonna dry, so we'll set that aside. And, let's talk about the blade for a sec. I've got this cut to eight inches, there's nothing magical about that. It can go a little longer, it can go a little shorter, the one I'm showing you here is cut at eight. I wanna get this decorative scallop cut out at the end of it. Now, really that looks nice, you don't have to do this, it doesn't serve any huge purpose with the square when we're done, but it does kind of lighten up the look of the whole tool. I'm gonna lay that out with this really fancy layout tool, otherwise known as a soup can in it's first life. Just like that. Band saw or scroll saw, cut and sand to the line to get that all cleaned up. Now, one of the things I want to point out about this while we're here is this is a great spot to take advantage of some cool looking pieces of wood you have laying around the shop. 'Cause the pieces we need are so tiny. So, it's a great way to use up some pretty scrap, like the sapele handle I'm using here, and the figured maple that I'm using for the blade. Now, let's do one more thing, while that glue is drying. We're gonna pin everything together when we're done with non-coated brass brazing rod. You can get this from welding suppliers, you can get it from hardware stores. What we want to do is drive and glue this into a hole. We're gonna use CA glue for that. In order for that glue to have some tooth on the rod, it's a real good idea to abrade it just a little bit. So, just 220 grit sandpaper, run that over the outside edge of that rod. That'll put some scratch marks in it, which is what we want. And then, the other thing we can do while we're waiting for that handle to dry is get our pins cut to length. Overall width or thickness on that handle is three quarters of an inch. So, if you cut your pins a little bit over an inch, that'll give you some extra that will trim off later. And, side cutters will do a great job with this. Now, second verse same as the first, we want four of these pins, so keep going with that step. Once, you've got a pin, it's gonna be easier to engage it in the hole that we're gonna put it into. If you dome or pointify the end just a little bit, so that instead of the end being square, it's kind of tapered, and that's gonna make it easier to start in the hole that we'll drill in the handle. So, get that far. That's gonna complete us here on part one of this process, don't forget to come back and look for part two, so that you can see how to finish up your shop-made try square.
When I click on the video, nothing happens, except the title shows.
it's a lot easier to dome the pens before cutting it off the main peace of stock