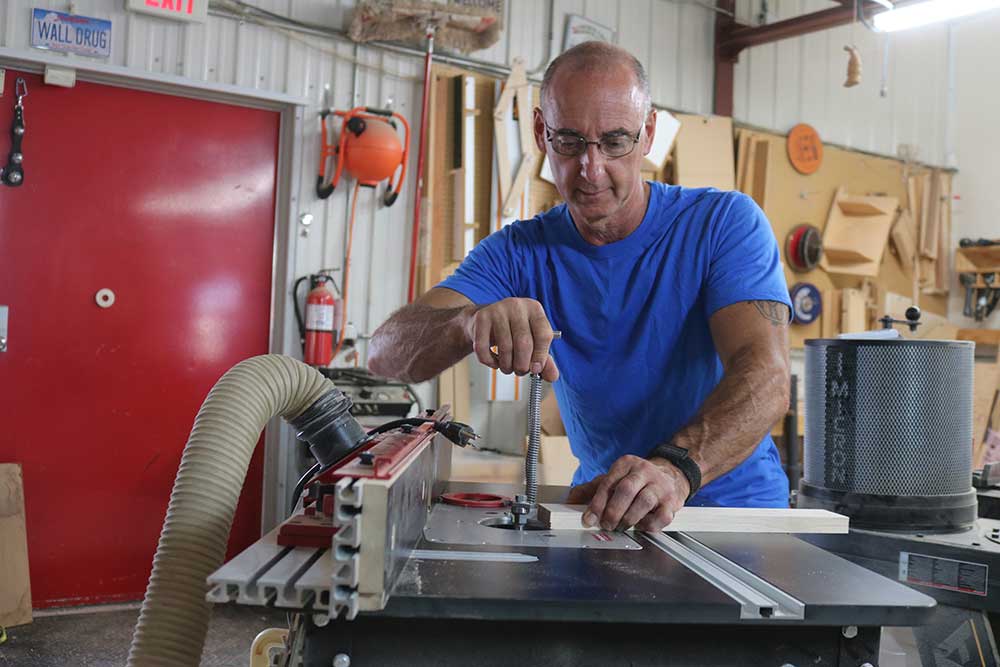
George’s Epoxy Bullet Bowl
George VondriskaDescription
Getting Ready
- – The mold for this project is an inexpensive plastic bowl. The epoxy does release from the bowl, so it can be used over and over.
- – Be sure you’re using the right epoxy. It needs to be an epoxy that’s suitable for deep pours.
- – Clean the casings if you want them shiny. George tumbled his with a brass cleaning product.
- – A pressure pot will eliminate bubbles from the casting.
Pour and Wait
Most epoxies need a lot of cure time before you can put them on the lathe, 5-7 days. Read the epoxy instructions, and don’t push it.
Turning
George toggled between high speed steel and carbide tools to do the turning. The casings really slowed the process down, and their shavings came off so hot he had to put a glove on his left hand. But in the end, the process was similar to any bowl turning project. Just slower. Epoxy projects typically don’t get finish, they get buffed. That was the final step of this project.
Working with Epoxy
If you’d like to try a bowl/epoxy project, but aren’t interested in casings in resin, you might like a wooden bowl with resin accents. We’ve got a lot of great info on incorporating resin into other projects, too.
Here is probably one of the weirdest things I've ever made in my life. It's a bullet bowl. A friend of mine is a real avid shooter. And at some point I had this bubble in my brain. That was, it'd be neat to take advantage of casting resin, take advantage of, I go to the range and I shoot.
Save the empties, put 'em into a mold and I see if I can get a bowl out of it. So here we are. So here's the deal. You may never do this exact thing. In fact, I'm probably never gonna do this again and I'll tell you why, but there were some steps along the way that I think were cool.
And maybe from this process you can extract some stuff that you can use. Why would I never do this again? Well, a couple of reasons, it was crazy labor intensive to do this. Way more labor intensive than turning a wooden bowl. I don't know, if I were doing this to sell, I don't think I could get my money back.
There's about $20 worth of casting resin in this and then an amazing number of empties, to get this mold full so that I could do this. The cutting process was hard. We'll talk more about that in a second. So let me back the truck up and I'll walk you through how this happened. I shoot at a gun range on a regular basis.
So on one of my trips to the gun range I picked up a bunch of empties. And one of the things I liked about not just using my own nine millimeter stuff, but picking up empties, was that it gave me a variety of sizes. When these came back here, they didn't look like this. So the first evolution in the process was how am I going to turn all these things from being dark and gross lookin', to being brassy and shiny. And I was at a different gun store and I found this stuff, which is specifically for polishing cartridges/casings I'm not really sure what those things are called, but for polishing those things.
The idea is that these granules go into a tumbler. I don't own a tumbler. So the next evolution was, I went ahead and bought this. Then I got a mixing bucket from a home center, with a lid. And on the bottom of it I put a wooden disc, that would accept the jaws of my four-jaw chuck.
So the way I polished all this stuff, is I made a tumbler. I put this on my lathe and I put the abrasive in there, along with the dirty ones and then put the lid on. And then I ran my lathe that about 50 RPM, ca-chunk, ca-chunk, ca-chunk, ca-chunk, for about an hour. And these came out this shiny. And all I had to do then was filter/sort the brass, the nice stuff from the abrasive.
So that's how I got everything nice and shiny. The next step was to get 'em into a mold. The mold is uber high tech. That is a plastic bowl I bought at Walmart for 50 cents. Now, like I said, you might never do a bullet bowl, but maybe you're interested in casting bowl blanks.
To me, this was an amazing find. I bought a handful of 'em and I figured if I pour the casting resin in there and it sticks, if it doesn't come apart when the resin is cured out, I don't care. This was only 50 cents. So I'll put the whole thing on the lathe. I'll turn that off the outside.
As luck would have it. It does separate from this. So that's not a problem. So here's where we're at. We have a mold, we have clean cartridges/casings, clean brass things.
Going into this process, I've turned resin, I've turned brass. So theoretically, this whole thing is possible. Next step, I put the empties into my mold and positioned them willy-nilly. There was nothing scientific going on there. Mixed up my casting resin.
And I poured the casting resin over the empties and at the same time what I had done, is put a wooden dowel in there. A big piece of Walnut. And that was what I used later to get this turning process started. That's what I grabbed with my four-jaw chuck to start the turning process. Once I had all of that stuff in the mold the next thing was to put it in a pressure pot.
What the pressure pod does is it eliminates the bubbles from the casting resin. It needs to stay in there until the resin is cured. Once I know the resin is cured, open the pressure pot back up, after releasing the pressure, and take everything back out. That got me to a point where I was ready to get the blank onto the lathe. And I went back and forth between carbide chisels and high-speed steel chisels.
And honestly, both of them work equally well. I've got a set of the negative rake carbide and they worked really well for cutting this but also my high-speed steel scraper did just as well. So I started standard turning, scraping process. As I got deeper and deeper into the turning, what I realized is I could smell burning hair from the back of my hand. The brass shavings coming off are really hot.
I don't normally wear a glove when I'm doing bowl turning. However, the brass particulates coming off were so hot, I finally put a glove on and I continued the turning process with that. From there, it was pretty much like turning a regular bowl. It was a slow process because the brass was hard. However, it did effectively cut.
I did sharpen my high-speed steel chisel more frequently than I would've with a wooden bowl but it cut very effectively. Once I had it cut. Then I went through a normal sanding process. And as a last part of that I buffed everything with a buffing wheel. And at this point we still need just a little bit more buffing and this'll end up with a higher gloss than it currently has.
So in the end, I'm glad I made it. My friend Mike is going to really appreciate this. And one of the things in the process here, was in the end, I didn't turn the outside because I really like how these look in their natural environment. Had I started cutting here. This face would have started to look like this face.
And I think it's kind of neat the way they're cut at a cross section here, but I'm glad that I didn't do that on the outside, 'cause I really like how this looks. On the rim I'm gonna leave 'em standing proud, just like they are. My last part of this is, I'm gonna mount this on the lathe like this. Cut that mounting plug off of that side. And then I'll, like I said, take everything to a buffing wheel, with buffing compound, and I'll just buff this thing inside and out.
So net-net I'm happy with my bullet bowl. And it was a idea, that surprisingly, from conception to execution to completion, went better than I thought. No one died. So that was good. And maybe you can steal some ideas from this for a project you're gonna do.
When the blank goes into the pot it it's on the top (rim) of the bowl.. But when it goes onto the lathe, the wood forms a tenon on the bottom.. Puzzled...
George -- That is a very cool bowl. The cross section of the casings on the inside of the bowl is interesting. You've inspired me.
Love the idea, might I recommend the same idea with bullets too. That way your friend can have a Case bowl (brass casings) and a bullet bowl with a mix of caliber bullets of varying types (solid lead, jacketed, hollow point, etc).
"No one died"... classic.