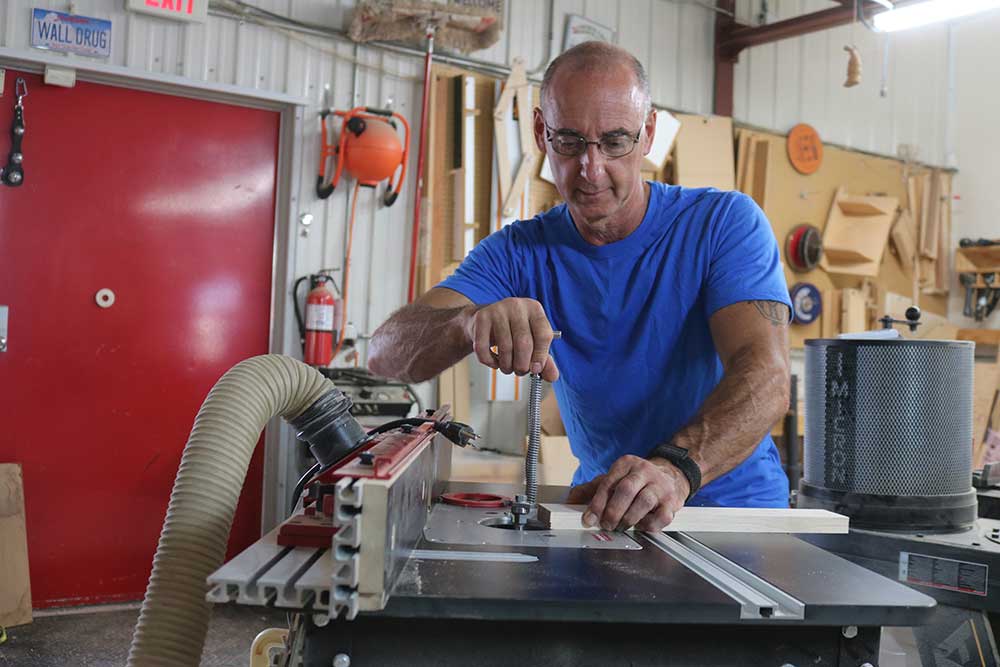
Gluing Up Panels
George VondriskaDescription
Gluing up panels is a must-have skill in woodworking. From tabletops to raised panels, there are plenty of times you’ll need to glue boards edge to edge. Here’s the recipe for making that happen in your shop.
1. Rough Cut to Length
As you crosscut material for the panel leave it 1” – 2” longer than the finished panel needs to be. When cutting up long boards it’s often easiest to cut them with a jig saw. It’s much easier to accurately joint short boards than long boards, so it pays to get them close to their finished length.
2. Joint One Edge of Each Board
The edges must be smooth, straight and square before gluing boards together. If you don’t own a jointer, or need more info on using a jointer, be sure to check out these related articles:
3. Mark the Cut
4. Rip to Width
Note that the jointed edge is against the rip fence. A ripping cut accomplishes a few things for you.
It makes the two edges parallel, which makes clamping easier. If the boards you’re clamping are wedge-shaped they tend to slide past each other when you apply clamp pressure. Wedge-shaped boards also result in a funky shaped panel that can be hard to square up later.
Ripping makes the next round of jointing go faster. If the board has a rough edge it’s faster to straighten it on the table saw than on the jointer.
I shoot for boards that are 4” – 6” wide in my glue ups. The wider a board is, the more prone it is to cupping. That’ll sure mess up making a flat panel. If you want to use a 12” wide board it may seem counter intuitive but what you need to do is cut it down the middle, and then incorporate the two narrower pieces in the glue up.
Your edge to edge glue up should be 1”-2” wider than what is required for the finished panel.
5. Joint the Sawn Edge
Note the position of the pencil mark from the first jointer pass. The face that was against the fence on the first cut is away from the fence on the second cut. Mark the second edge, making the mark near the jointed edge and on the face that was against the fence.
6. Check Your Joints
Lay the boards on a flat surface and slide them together to check the joints. If you’re alternating faces each joint will have an X up on one edge and down on the mating edge.
The joints should easily close with hand pressure. If you have any gaps go back to the jointer for another pass. Excessive glue and clamp pressure do not compensate for lousy joinery.
7. Mark the Faces
Once you’ve worked out the joints and orientation of the boards, make a face mark. A big triangle will show you how the boards go together. You shouldn’t be guessing at this while you’re working with glue and clamps. The bigger the glue up, and the more pieces you’re working with, the more important a face mark becomes.
As I’m working with the boards I go for the best looking face, a function of grain and color. You do not need to alternate growth rings, provided your material has been properly dried.
8. Prep Your Clamps
If you’re using pipe clamps made up with black pipe, put masking tape on the pipe. If you don’t, glue squeeze out can loosen up the black coating and allow it to migrate into your panel. It can take A LOT of sanding or planing to remove those black marks.
9. Apply Glue
Using a glue brush spread a uniform film of glue. You only need to apply glue to one edge in each joint.
What about biscuits, dowels or some other joiner? No need, as far as strength goes. With good joinery, the joint will be stronger than the surrounding wood. Need proof? Check out this video. On large glue ups you may want to add biscuits, or something similar, simply to help keep the faces aligned so you don’t have to work so hard to level the panel as you’re clamping it up.
10. How Much Glue?
Put on glue like you’d put on paint. Go for a uniform coating that is opaque enough that you can barely see through it to the wood below.
11. Clamp the Panel
Use an equal number of pipe clamps above and below the panel. Having clamps above and below the panel, with equal pressure on all the clamps, helps keep the panel flat. The pipe clamps on top were made using galvanized pipe, instead of black, so masking tape isn’t required.
Don’t over tighten. As soon as you see the joint close, you’re done with clamp pressure. No need for clamp pads because the panel is oversized and the edges will get cut off later.
12. Check Alignment
As you tighten the clamps you’ll need to manipulate the boards to make sure the faces are aligned. Near the end of the panel you can bridge the seam with a small clamp. As you tighten this clamp it will pull the faces into alignment.
13. Don’t Wipe the Squeeze Out
Wiping wet glue with a damp rag just pushes the glue around and makes an even bigger mess. Allow the glue to dry until it’s rubbery, about 10-15 minutes, and slice it off with a chisel. If you don’t wait long enough it’ll be too wet and make a big mess. If you wait too long it’ll get too hard and you won’t be able to cut it off. Check the squeeze out frequently to see if it’s hit the right consistency yet. When it’s ready it’ll peel easily.
14. Make Glue Ups Easier
If you want to simplify gluing up panels, consider upgrading to parallel jaw clamps. There’s no need to put masking tape on the beam and, because the jaws are parallel to each other, there’s no need to clamp from below and above. You’ll find parallel jaw clamps at woodworking specialty stores, from a variety of manufacturers. A warning, these clamps aren’t inexpensive, but they make clamping panels (and doors) so much easier, they’re worth the price.
Why Alternate Faces on the Jointer?
When setting up the jointer your goal is to make the fence perfectly perpendicular to the table. That’s a great goal, but it doesn’t always happen. If the fence is off a little you’ll joint a slight angle onto the edges of your pieces.
In this picture the jointed boards are lying on a table with the face that was against the fence down on both boards. You can see that because of the angled edge the joint won’t close unless I rock one of the boards up off the table. That’s fine if you’re making a barrel, but no good for panels.
These are the same two boards, with one board flipped over. Now the angled edges produced by the jointer complement each other, allowing the glue up to be flat.
If you know that your jointer fence is perfectly perpendicular you can ignore this aspect of the panel sequence.
Photos by Author
Premium Membership
Unlock exclusive member content from our industry experts.
- 24/7 Access to Premium Woodworking Videos, Projects, and Tips
- Step-by-Step Instructional Demos, Plans, and Tutorials
- 50% Off Video Downloads Purchased in the Woodworkers Guild of America Shop
- 2 Printable Woodworking Plans
Unlock exclusive member content from our industry experts.
- 24/7 Access to Premium Woodworking Videos, Projects, and Tips
- Step-by-Step Instructional Demos, Plans, and Tutorials
- 50% Off Video Downloads Purchased in the Woodworkers Guild of America Shop
- 2 Full-Length Video Downloads to Watch Offline
- 2 Printable Woodworking Plans
Gold Membership
$370 Value
Get everything included in Premium plus exclusive Gold Membership benefits.
- 24/7 Access to Premium Woodworking Videos, Projects, and Tips
- Step-by-Step Instructional Demos, Plans, and Tutorials
- 8 Full-Length Video Downloads to Watch Offline
- 3 Full-Length Woodworking Classes to Keep for Life
- 7 Printable Woodworking Plans
- Discounts on Purchase-to-Own Content in the Woodworkers Guild of America Shop
- Access to Ask the Expert Program
- Exclusive GOLD LIVE Streaming Events
It is mentionned in the Description tab : "You do not need to alternate growth rings, provided your material has been properly dried". The thing I do not get is this : in my mind, even if the material has been properly dried, the fact that my shop is not climate controlled (temperature, %RH), the material will gain in humidity if the humidity rate in my shop is higher than the one of the material (provided the material stays longer enough in the shop, that is almost always the case). So the orientation of the growth rings would make a difference. Thank you explaining me why it not as I think of it!