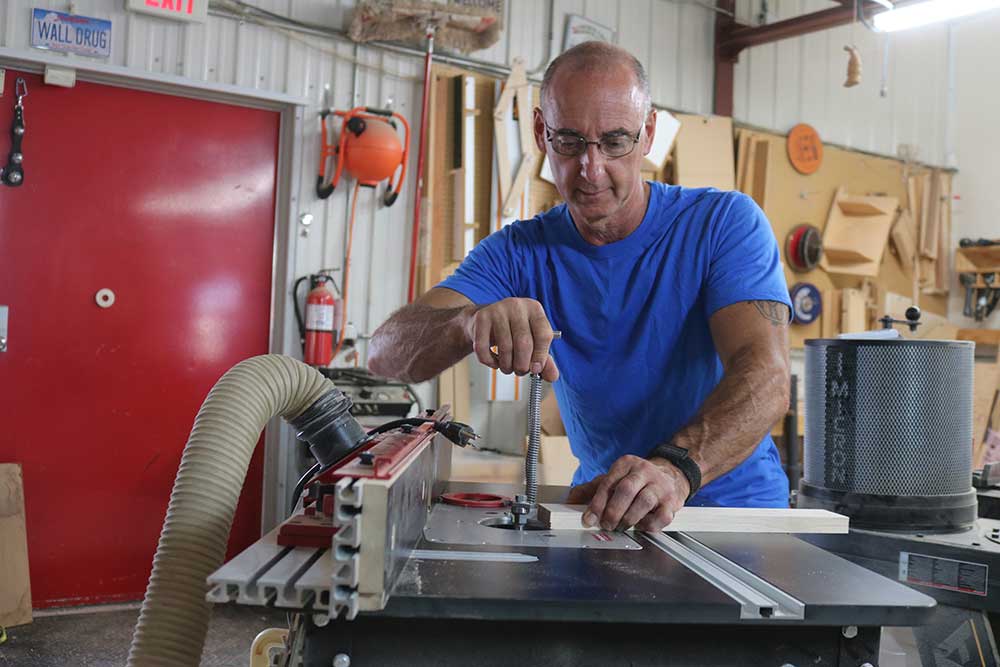
How to Buy Lumber According to Grade
George VondriskaIn this comprehensive video, George will walk you through selecting the suitable lumber for your woodworking projects, ensuring you get the best quality and value for your money.
Lumber Grades
George will explain the various lumber grades, including Select Structural, No. 1 & BTR, No. 2, Construction Grade, No. 3, and Stud Grade lumber, and how they’re defined by strength, appearance, and number of defects.
Lumber Inspection
George will provide practical tips on inspecting and choosing lumber at your local home improvement store or lumberyard. He will discuss the importance of checking for warping, knots, and other imperfections that can impact the quality of your finished project.
Optimizing Lumber Purchases
George will touch on the importance of optimizing your lumber purchases by considering factors such as waste percentage and the potential for reuse in future projects. This will help you make informed decisions and avoid unnecessary expenses.
Following George’s expert advice will give you the knowledge and confidence to buy lumber according to grade, ensuring you get the best materials for your woodworking projects.
Other Lumber Videos
Free Videos:
- Cutting Lumber from Logs
- Milling Lumber: From Rough to Ready
- Plaining Saw Logs into Lumber
- Air Drying Freshly Cut Lumber
Member Videos:
Unlock Your Woodworking Potential!
Sign up for our newsletter for endless woodworking inspiration! Become a member today and gain access to a world of craftsmanship.
I think you brought a banana with you here. Wouldn't we- I brought a couple other boards here. Two of these were already on the bench. We added one to it. This is a two common board, and you can see how crooked it is when I set another board alongside of it.
There's a quite a bit of a, quite a bit of bow in that board. What happens with this board is the reason it has become a two common board, are a few different things, is there are knots on the poorer face but also the amount of bow there starts to limit the size of clear cutting units we get out of here. So again, a board, that's about a four and a half-inch wide board. With a bow that large, you have to take equal, equal loss on both edges. So I'm buying, maybe I'm buying a five-inch wide board, but at the end of the day, in actual use, I'm only gonna get a three and a half-inch wide board or something.
Correct. Yup. Planing this in your shop on a joiner, you're gonna spend all day. You may wanna have your lumber pre-serviced with a straight line rip, which they're gonna clean that one edge up, leave the other end bowed. Another option for this board to get a much higher yield out of it, is to take it and cut it into shorter lengths, prior to straight-lining it.
Now you've minimized the amount of bow to 1/3 per piece. So where we have about an inch and a half of bow, now you're down to about a quarter-inch to 3/8 of an inch, on each piece. Well, let's go back and hit on the straight-lining business 'cause I know not everybody's familiar with this. So you're right. If, if I got this in my shop and I needed an eight-foot long board, if I took this baby to the joiner, I'd be there about four years trying to joint that long curve out of there, or I would have to try to rig something on my table saw because I don't, I don't have one good edge to go against the table saw fence.
So I'd have to try to rig a jig, so that I could rip myself an edge onto this. Now on straight line edging, I've seen your machine. It's pretty cool. It's got lasers and the whole thing. So just give us the walk-through on, if your guys were cleaning this board up and they were gonna straight line edge this, what, what happens there?
We basically use a, a multi-bladed saw. We only, we only leave one blade in there with a laser on it. And it shows us exactly where that blade's cutting. We'll take and we will hand-feed in every board, and we will clean up and leave as much as little waste on our floor as possible, so that you end up with the most yield out of your lumber. So the laser's throwin' a line ahead of the blade, onto this board.
Yup. Which lets you predict the cutting path. Correct. So on this board we'd get that lasered to throw basically down. this felt tip line that you put on there.
And once this goes in there, you're not feeding it like you do on a table saw, right? It's conveyed past the blade in a dead straight line. Yeah, it's pulled in and there's a 50 horse motor on our, on our saw. So we can, we can cut anything up to about 12/4 on there. Wow.
And come out with an absolute gluable edge. I know, for me, straight line edging, which you see it represented as SL1E, straight line one edge. I get it done all the time because I find that it saves me. It doesn't cost a lot of money. It doesn't add a lot of price to my order but it saves me so much time in the shop, against handling boards like this that I think it's worth every penny to have 'em done.
Now, the other thing is that, we saw these boards coming off of the tree. We cut them on the saw mill. We cut them on the bandsaw ourselves, and they look like this. Now I know we've got options here too. And we've got a board here as an example.
Let's, let's start with the hit or miss option on the back of this board. Yeah. Here's an example of what you would see when it comes in rough. This board has been through our double-sided planer, and what we do, typically, when we sell or even do additional machining to lumber or make melamines out of it, is we'll take our rough stock, which would look like that piece there. And we'll put it through a planer to get it to a consistent thickness.
We typically will shoot for a 16th under nominal dimension. So if somebody's buying some 4/4 lumber, we will hit and miss it to 15/16. Not every side is gonna be cleaned up though. So here, you can see, this is a, a fairly rough-sided board. All we've done is taken off the high spots along this board.
So we do have a very consistent thickness, but in no means is this cleaned up yet. So I'm placing my order for hardwood and I've got all these options. I need to know how much wood I wanna buy. We've talked about the straight line edging. Then we get to the surfacing business.
So maybe I own a planer, but the benefit of me paying you a little bit of money to do this hit or miss is that, realistically, when the stuff comes from the sawmill, what do you think is the variation from board to board in sawmill logs? Drastic. We, we will see sometimes ends taper up to a half-inch extra on one end, which is even difficult for us to handle. Very typical is eighth to a quarter on varying thickness, board to board. So if I don't have it hit or missed, I get this pile of stuff in my shop that goes from 4/4 to 5/4.
Then when I'm getting to my planing operation, I've gotta maybe isolate out the really fat pieces first, get those planed. So a little bit of extra money to you, and we get the hit or miss. So now I know every piece is about 15/16 of an inch. Correct. Now we can go further than this.
And this is what I usually do. I don't do hit or miss. My stuff comes in like this, which is S2S. So give us, we're a couple steps further down the path here, right? Yeah.
Now typically we will hit and miss, and then we may go back and actually do your surface planing to your desired thickness. So when you place an order, we may have brought it in, in the rough, surface to hit and miss. And then when you place your order, we will ask you what you're looking for, for thickness. You may order it right to 3/4. Some shops order 25, 30 seconds.
It allows them to be able to glue a few pieces and sand a few pieces, and still end up at a 3/4 thickness. Yeah, I like to do, my own recommendation is a 13/16. That way, when it comes in, just like Greg is saying, if you do a glue up, you've got a little bit of material thickness still to work with after the glue up is dry, so that you can surface it down. Additionally, specifically on door work, rail and stile work, that gives you a little bit of extra meat here in the thickness to get your rail and stile cutters placed into the material, a little bit beefier door. So S2S is different from hit or miss, and S2S, you're gonna ask them S2S to what?
So you're, you're gonna ask the buyer to specify S2S to 13/16, 25, 30 seconds, half-inch. If that's what they need. Yup. You can take it down to whatever they want. Yup.
Correct. And the reason we like doing this in two steps are our servicer will take a one-inch thick board, and a 4/4 board in the rough and take it right to this. But you can see, by example, this board, this board here was hit and missed. One side came out perfectly smooth. The other side came out perfectly rough.
When we take it to the next step, to this level, it allows us to take a little extra off one side than the other. To make sure we have two good faces. To make sure you end up, as the end consumer, both good faces. And then just to hit on your straight-lining again, as one more step there. If I had the need for it, I could ask you to straight-line to a specific width.
I could do SL2E, I could straight line two edges, and I could get that lumber taken right down to a specific width also. Correct. Yup. And we can rip one board at a time to a certain width, or we can set up what's called a gang rip, where we could take boards and rip everything two-inch and a half, inch and 5/8, two-inch. And basically, it takes the same amount of time for us to rip a board into six little pieces as one straight line because we just add additional blades there.
Okay. So now, our viewers wanna know where to buy hardwood. So what's your recommendation? How do people find a good hardwood supplier in their area? You know, every area's gonna be a little different.
You can, if you try and do a search on a lumberyard, you're gonna end up with more of your retail box stores, your hardware stores, your major lumberyard centers. You're gonna wanna try and research a hardwood supplier of some kind. But the line in the sand is lumberyard versus hardwood supplier. Yeah. Start there and do an internet search.
Find somebody. If you end up coming up with a, with a mill that's manufacturing lumber, they may not wanna deal with the hobbyist or end consumer, but they may be able to point you to somebody nearby, that they distribute their products to. So make a phone call before you drive up. Yeah. Make a phone call, make a few phone calls.
And you will, you'll be able to find somebody or partner up with somebody to acquire some lumber. Now Greg, when I placed my hardwood order, am I gonna pay as much for a board foot or two as I am for a big 200 or 300 board foot order? Yeah, definitely. You're gonna pay less for the larger order. So if you're gonna go in and just simply order a board or two, it's gonna cost you a little bit more than buying a full pack, half pack, or quarter pack of lumber.
So one of my advice points that I give to woodworkers all the time is, it's real smart to co-op with other woodworkers on your hardwood purchases 'cause there is a significant price difference between a couple board feet and a hundred or 200 board feet. So everybody get together, agree on a specie, buy that, go to somebody's shop, divvy it up, and you're gonna save a lot of money, and get good quality stuff too. Yeah, definitely. And the upper grade woods are available at all distribution points, manufacturers. When you get into some of the lower grade product, you may have a little harder time finding that, but definitely ask, because you may find some very good quality lumber at a very cheap price.
I think a great lesson out of this is number one common, great value, very, very useful, especially for cabinet, furniture work. Admittedly, there are applications where you need big, long, clear pieces, but in all honesty, most woodworking just doesn't demand that kinda stuff. So boy, you can save a lot of money working around the defects. Sure thing. In number one common.
Well, Greg, this has been great information. We've kinda seen it all here. We cut a log on the saw mill. We cut a log on the bandsaw, air drying, kiln drying. You got any final advice for us here, for our viewers, on lumber grading, years of experience in the business?
You know. Tell us what you know. It's, we see a lot of beautiful wood come through our facility every day, low grade. And we're surprised at what you get in every pack of wood. Upper grade, there's certainly expectations made on every board that come through our facility, but finds like this.
You know, it's just, it's neat to see such good quality product come through on what's perceived to be a lower grade lumber. The quality in that lumber and that board is no worse off than any other board that you'll ever buy, as your very best board. So it's a matter of how you use it, how you buy it, and how you trim around your couple of defects. Well, hopefully we gave you some information here you could use. So now instead of just a run-of-the-mill woodworker, you know a little bit more, you're gonna be an educated consumer.
Save some dough on your wood. Happy woodworking.
George I enjoy watching your videos picking up tips and ideas. For purposes of cutting boards that have a large curve or bow -grizzly.com carries a board straightening tool. The cost is only $10 and the few times I’ve used it it seem to work well Chris
I am watching the "How to Buy Lumber According to Grade" unfortunately I am receiving the first three minutes of the video. I understand this is a Free Video, but I am a Premium Member and I am logged on, shouldn't I be getting the complete video. In the past that is how your videos have played. Again, I am logged In.