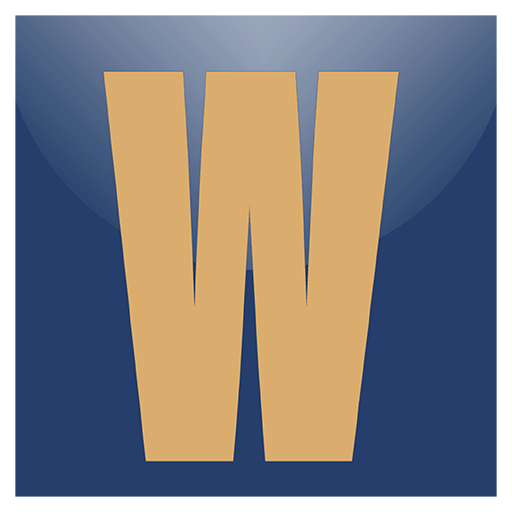
How to Make Wood Plugs
WWGOA EditorsDescription
Drilling the screw holes
Getting this process right starts with correctly drilling for the screws. Use a countersink set that, in one step, drills the correct hole for the screw AND leaves a hole that a plug can fit into.
Cloak of invisibility
Use a screw plug cutter to cut the plugs from the same material you’re using for your project. If you’re careful, the plugs will be nearly invisible. Or, use a contrasting material and make the plug decorative.
Shearing the plugs
Yep, you could sand the plugs flush but you’ll save time, and it’s really rewarding, to use a sharp chisel and trim the plugs close before doing any sanding. If the chisel work doesn’t go well and you end up with an Oops, don’t sweat it. We’ll show you how to fix that.
Can we plug pocket holes?
If you’re using pocket hole joinery on your projects we can apply a similar idea. Hiding pocket holes with plugs is easy to do, and you can make custom plugs to add decorative details. You just need to know how to make wood plugs for those specific holes.
Other joinery methods
There are so many ways to put wood together. With such a huge array of joints and joinery available, we’re happy to provide you with the how-to you need to add joints to your woodworking arsenal.
Lot's of bad advice in this video. Maybe this works for this guy but it looks like he makes a lot more work for himself than necessary. I screw and plug a lot of my work so here's some advice, for what it's worth... -Don't make wafer-thin plugs. You need a substantial amount of the plug below the surface so it's less easily removed and so it holds strong when being flushed to the piece. Try to have a plug at least 3/8" in length and at least 1/4" below the surface. -Don't use a countersink bit to bore a hole when you plan on plugging. This will bevel the top of your hole making it difficult for a plug to sit properly. Instead, use a regular drill bit to make a straight, cylindrical hole so the plug will appear seamless when flush cut to the surface. -Don't use a hammer and chisel to flush the plugs to the rest of the piece. As you see in the video the wood fibers of the plug rip out below the surface and he has to remove the plug. I'm surprised he didn't offer an alternative to the hammer/chisel method because it clearly failed him. It's much easier to use a flush cut saw to remove the bulk of the plug then sand the rest flush. There's two videos on this site titled "CUTTING PLUGS AND USING PLUG CUTTERS" and "TRIMMING SCREW PLUGS" where George shows a different way of approaching this. I suggest you watch those instead of this one.
How do you get the newly cut plugs out of the wood you drilled them from?
Might want to show how a small Japanese saw can give even better, quicker results than a chisel. Done right, sometimes they barely need sanding.
I have 3 different types of plug cutters I have the prong type like you used and the solid type never could get them to work right HELPPPPPPPPPPPPPP.