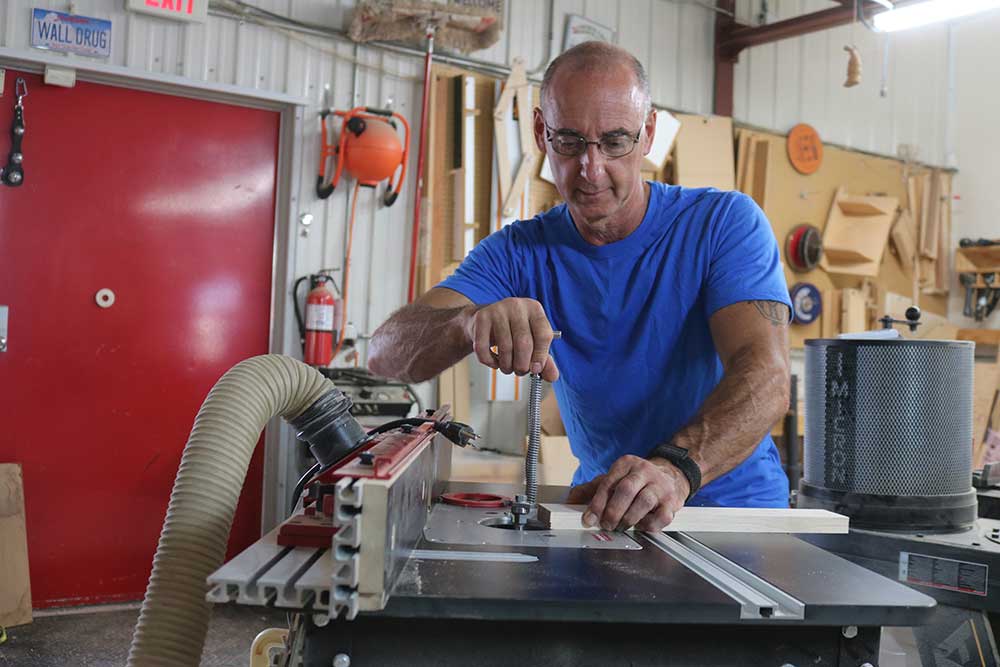
Make an Oval Box and Textured Lid with a CNC
George VondriskaDescription
Making the lid
The lid of our oval box has some great features. It’s domed, and it’s textured. You’ll learn how to create the dome and apply the texture to it. You’ll also see how to cut the exterior shape, and use tabs to hold the lid in place.
The box
Once the lid is complete we’ll transfer the oval that defines the lid to the base to make sure they’re exactly the same size. We’ll use the offset function again to create the wall thickness of the box, and set up the software to excavate the waste out of the box interior, and through cut the exterior, again using tabs.
On to the CNC
We use a unique, but very effective, means of securing our material to the CNC spoil board. With the board set in place you’ll learn how to install router bits and zero the X,Y, and Z axes.
More about CNCs
We cover a lot of information in this video, but we’ve got more information if you’re hungry for more about programming a CNC machine. We can also help you out if simply want to learn more about a benchtop CNC.
You may also like
Here's a really cool CNC project we can make. It's a lid with a textured box and a bunch of stuff is gonna happen here. I'm gonna take the lid off first so we can look at the bottom. Everything is an oval. Now, creating an oval in your shop compared to creating a circle in your shop, little harder to do.
So we're gonna use the software to create the oval. We're gonna hollow out the inside. We're gonna use software to get the exact oval shape of our lid and dome the lid and then apply a texture to that three dimensional dome. All of this will be laid out on our software and then run here on the CNC machine. Here's a complete list of everything you're gonna learn on this video.
We're gonna do our programming, our layout on a piece of software called VCarve. And what's cool is that many, many of these CNC machines use VCarve for the design component. And then you just change what's called the post processor when you send it to your machine. So if you want to make a lidded box like I'm gonna make now you can follow along click by click on your computer and do the layout. So here's where we get started on this.
First thing, like a lot of software items, we're gonna create a new file. So that's over here on the left side. One of my menu items. When I do this, it gives me the opportunity here on the left to choose the dimensions of my material. So we got to know that coming in.
In my case, the width is 11 and the height is six and a half. Now, what does that mean? The width is my X axis, the height is my Y axis. So it's a little backwards from the board that we're working with. The way that we're gonna put the board on the machine is the length of my board is 11.
The width of my board is six and a half. Now it's also important to come down here and enter the thickness of your material, because when we make our lid we're gonna cut all the way through it. And the machine is gonna need to know exactly how thick it is. So this, Leigh would literally do your best work by measuring the thickness with digital calipers. If it's 1.1, enter 1.1, don't do rounding here.
Tell the machine exactly how thick it is. That gives us a good starting point. The other thing we need to know is this, this X, Y data. This is, if you think back to your high school or middle school math. This is the origin of the product.
Where's the X gonna zero and the Y gonna zero? And for this project I'm gonna choose the center of the piece. Sometimes you might choose lower left, like a real typical graph, X, Y, or center or one of these other spots. But for this project, we're gonna work off this center. What we're looking at now, this big piece of paper, this is the site.
This is my project, this is my board. And here in the middle, zero and zero, this is the center. We're gonna create an oval shape lid. So let's take advantage of what the software is capable of and create an oval. So I've come over here to the menu, draw ellipse and we can do this a couple of different ways.
I can come over onto my board and manually draw the ellipse or I can enter in dimensions that will work for this project. So with X axis of eight, that's actually a pretty good number for what we're doing here. And a height, Y axis of 4.75. That's gonna work pretty well. And then we can create.
Now if for some reason you're not feeling the love on that, you wish had gone a little bit bigger or smaller. We can always click it and we can drag it to be bigger, drag it to be smaller or change our minds altogether and delete. Then let's come back again, create that oval again. The other thing we can control here is where it's centered. So much like when I started with the project, we can pick the spot that we want it to be the zero zero.
So I can go to that lower left point or center. For this, it's gonna work easiest if we stick with the center of the board, be in our layout point of zero, zero, same for the ellipse. So let's go ahead and create that again. Now this is our lid. So what we wanna do next is get the dome shape, go on.
And I'm gonna come down here to the bottom of my menu and pick clip art. And this is really cool. There's a lot of stuff in the can here that we can work with. We're gonna go to Domes. And what happens here, these domes are set up for different thicknesses of material.
We're gonna use this one, the leftmost dome, click, hold your button and just drag that into your workspace. Now that's a little weird, we have a big circle instead of the oval that we want, but we can change that. We can control that. So I'm gonna go back to my drawing, down here on the left. And one of my options is to control the size of my object.
So right here, selected object size. And I'm gonna tell that how big I want it to be. Now, if we're smart, we'll remember the dimensions that we used on our oval and that is eight. And I'm gonna unlink the X and Y. And this is 4.75.
So unlink X and Y, what that would do is, it would keep the two proportional. So if I change this to eight, it'll change this accordingly. In this case, I don't want to do that because I'm creating a custom oval, a custom shape to my particular workspace. Well, let me just go back and do this again. 'Cause I put the number in the wrong spot.
That looks better. Now we want this to remain centered and our work piece. So one way we could do that would be to click it, see how the squares come up around it. Then we can drag it wherever we want it, but let's let the software do some of this work for us. If we'd come back here and look at our menu, we have an option to align objects.
This one centers whatever you've just highlighted completely in your material. So let's click that one. And it puts that oval right smack in the center. Now, when we look at this, my dome is not quite the same size as my oval here. And the reason, even though we entered, manually entered numbers in is the software changed this dome just a little bit.
This is what's called a pixelated form. My oval up here is a vector form. So they don't quite play nice together but they're gonna play nice enough together that things are gonna work out just fine. So I'm gonna pull this a little bit higher until it gets to my oval there. And I'm gonna pull this a little bit lower till it gets to my oval there.
And that's gonna work out just fine. Now I've got my dome in here and I've got this oval, which is gonna help define the exterior of the dome. But one of the things that I can show you on the real cut is that what we need to do is create another oval outside the oval of our lid, of our dome. The reason for that is that when our V cutter comes through here, if we don't create this extra step, this extra area of clearance, this cutter, the V cutter is gonna hit the wood. So we have to add another oval just for the sake of clearing out a little bit more material so there's clearance for the router bit and the collar down the router.
Now this is pretty easy to do. One way we could do it would be, we can click this, copy it, paste it, drag it larger. But again, let's let the software do what the software is good at. I've clicked that oval. So it's pink now, come down here to offset and layout and I'm just gonna create an offset.
That's gonna work out just fine. It's gonna do offset outwards and let's go a little bigger than this. Let's go 0.625, that's five eighths on an inch. And now watch what happens when I click on offset, bang. It automatically creates another oval for me.
Now we're to the fun part. We get to actually go to toolpaths, close out of this. And I clicked off my work so that that pink would go away. I wanna click my big oval and I want to click the dome, while I'm doing the dome. While I'm clicking the dome, I'm holding the shift key.
That means now I've got two items selected. Holding the shift key, lets me pick two items. The oval here that defines the perimeter of the dome is not selected. toolpaths, it's real convenient if you hit the pin up here. That's gonna keep that toolpath menu open.
Instead of having it toggle back and forth, between open and closed. And we're gonna come down here and use the 3D roughing. So like you often would in woodworking, we can do a roughing and a finishing pass. The roughing is just like, it sounds, like it's gonna quickly take a lot of material off, not leave a real great surface finish. Then we'll come back and we'll finish this.
So let's go to 3D Roughing. And up here on our tool menu we can choose from a variety of tools. End Mil, that's what we're calling a typical straight router bit or spiral router bit of different diameters. If you have a real small area to excavate, use a small cutter 'cause it's gotta be able to fit in there. If you have a large area to excavate, go to a bigger diameter cutter, for where we're at here, this 0.375 that's three eighths inch is gonna work just fine.
And we have an option here of where we want our excavating, where we want our material removal to end. Model boundary would be the end of our dome but we don't want that remember, we wanna go to that outer oval so that we get this extra area cleaned out. So we go to selected vector, and here in the title I'm gonna change the name of this file, because I want it to be more descriptive. When I get to the machine, I want the file title to help me. I want it to tell me, what bit I'm supposed to be using and what I'm doing.
So I'm gonna call that 38375 roughing. Now this is pretty cool, let's calculate. This is the toolpath we're looking at. What's really cool to check your work, is let's use this part of the menu preview toolpath. That's our router bit excavating, excavating, excavating.
This is gonna give you a visual idea of did we do this right or not? Now this is looking at it from the top down. Let's grab it and turn it. This is the roughing pass. See how it's left these steps kind of like a pyramid.
It created that extra flat at the bottom where we're creating clearance for our V cutter. So this looks good so far. Now on our dome, what we wanna do is finish the dome, but we don't need to do finishing out here in that flat. So we're gonna pick the dome, come back to our finishing pass. Let's finish that dome off.
What we need to do here is check our cutter. Now in this case, generally for this 3D finishing you're not gonna use a bit that straight on the bottom. You wanna use one that's round on the bottom. That's all of our ball nose cutters here. And again, pick the size of the cutter depending on the size of the work you're doing.
So we're gonna go with a half inch, a 0.5. oops, there we go. And I'm gonna change my title. 0.5 finish. Lots of information here.
And what I'm trying to do is give you an overview of future videos. We can drill down further and further with where this can help us, but we're gonna get you quickly here to a point of success. So I'm gonna calculate, preview toolpath, zip, zip, zip. Have a look, see what we've got. There's our dome, ain't that cool?
How that lets you see what you've got. Now, we have a texture on our dome. There's our dome. And we're gonna pick this outer oval as well. Some shift, now that outer oval is pink and our dome is selected.
And one of our options right here is texturing click on Texturing. And once again, we can pick our bit. So here in select, texturing is pretty cool. You gotta try different cutters just to see what they look like. Straight bits, ball nose, B bits.
We're gonna use this 90 degree V bit to do our texturing. And then lots of options that you can play with here. And it changes the parameters. It changes the randomness. We can also change the angle at which we put the texture on.
This is something you need to just experiment with and see how it goes. One of the things that's really important here is we need to project this onto the 3D model. We have to tell the computer that we don't want it to just your straight, across a flat surface. We want it to go down onto that dome. Now again, our name for the file 90 degree and it's texture.
Again, this is our toolpath, those lines let's preview our toolpath. Once we're that far we can rotate. How does that look? If you don't like how it looks, we can undo. We could go back and change those parameters, run it again.
Let's leave that on there, 'cause I'm feeling the love on that, I like it. The only thing we need to do now is cut our lid out. 'Cause we don't wanna leave it attached to that big board, we wanna separate it. Come back to our drawing. Now in this case, what we want, remember the really big oval that was just to create that extra area of excavation.
The little oval is what defines the outside of our lid. Click on that, come back to our toolpaths. And this one is called our Profile Toolpath and that's gonna cut around the perimeter once again. What a surprise, we can choose what color we choose to use. Now, for convenience I'm gonna go with the same bit that I did my excavating on the 3D work with.
And you'll see where that pays off in just a sec. So three eights diameter cutter. And then as we look at our parameters here we can do all sorts of stuff. We can cut outside the line. We can cut inside the line.
We can cut on the line. We don't want the bit to straddle the line, that's what this would do. And we don't want to go inside, that would make the lid smaller we wanna be on the outside. Now think about your woodworking. Is it easier to ease into your work or plunge and cut?
It's easier to ease in. So let's put ramps into the work and that's gonna help the cutter ramp in more gently when it first starts the cut. Now, as we cut, one of the things we don't wanna do is just playing cut through, because then the lid would fall away from the rest of the material. We're gonna leave what are called tabs. That's gonna hold that in place.
Tabs are here, on the menu. We're gonna add tabs and once we add them here, we can change the distance between them. We can change the number that we're using. And what's also cool. If you look at the drawing itself is that let's say for a particular piece, you didn't think that that was a good location for the tab because maybe you don't like that, it's right there on the end grain.
We can drag it to another spot and we could change the locations of our tabs, the numbers of our tabs, the dimensions of our tabs, whatever you need to do in order to get this to work, for the project that you've got cooking. Now this, it's again a 0.375 cutter and this is our exterior. It's gonna separate the lid from the body of the material. Now I can see from looking at this, I made a mistake. So let's go back and what I'm looking at here is I don't think I sat deeply enough on that cut.
So let's go ahead and preview it. And I will tell if I'm right or not. Yup, so it's not shallow, I mean, it's not deep enough. It's too shallow, it's not cut through. So I'm gonna undo and benefit of being on a computer, double click this piece, and here's the problem.
Our cut depth 0.63, that's a little over half inch. Our material is an inch thick. So the bit wasn't told that cut all the way through. Now, one of the things that is gonna make this machine a little bit faster is remember, we're actually have a lot of that material already excavated away. How much do we already have excavated away?
Let's close this and look at our material set up. The gap below our model is 0.4 inches, just under a half inch. So that tells us how much wood is already gone from above that point, above 0.6 Okay, keep that information in your head. Lets to go back to this cut for a starting depth then instead of zero, that's the top of the board. Let's come down a little bit.
Let's come down to 0.375. We want to cut all the way through. So from that point, we have to continue. That's three eighths of an inch. We got to go another five eighths of an inch which would be 0.65 but we need to cut all the way through.
So let's go a little bit beyond that 0.64 and calculate and preview all toolpath. All right, so let's figure out what's cooking with our final cut through here. I'll cut up the zero. I must have clicked in the wrong spot here. 0.6, what did we say?
0.64 to make sure we were gonna go all the way through. All right, this is good. 'Cause we're getting a warning saying, you're about to cut through your material, this is to help protect you in case that wasn't your intention. How far are we going through? Are we gonna cut too deeply into the bed of the machine, the spoil board, whatever's going on?
So this is fine, this is what we want to do. We want to separate that lid. So that's a good warning, but it doesn't bother us at this point. Let's go back and preview this toolpath. Now we're cooking.
All right, it cut all the way through it left our tabs. This takes care of our lid. Good news. The hardest work is done, the base is a whole lot easier to lay out. So we're gonna come back create a new file and work on the base.
Before we exit the lid file. Let's take advantage of some information here. First, let's look at transferring what we know here to what we're gonna do on the base. Bottom line is, the outside dimensions of the base are exactly the same as the outside dimensions of the lid. That's defined by this oval right there.
That's now pink. So let's take advantage of what computers do for us and let's copy. I'm gonna control C. I'm copying that element and we're gonna use it again and just a little bit. Before we leave here, let's get our toolpaths exported here.
'Cause from here, we got to get them out to the machine. We've got to get rid of the shop bot in order to run them. So first thing I'm gonna do is move my three eighth exterior cut up and you'll see why in just a second. I'm gonna click the roughing cut, click the exterior cut, this thing that looks like an old fashioned floppy disk is my save. Choosing my post processor here.
Remember I said same software for a lot of these machines but you got to use a post processor that works with your machine. I'm gonna output these to one file. So what's cool about this. Remember I said, there's kind of an economy of movement that'll come from using the same bit. So by choosing these and putting them in the same file, it's gonna run those two files back to back for me.
Save toolpath. I'm on a removable desk, a flash drive here. I like to create a folder just to help keep things organized. So this is our lidded box lid. And within that, we're ready to save that file.
Then we're gonna have our finishing cut, oops, 'cause I forgot to click it here. There we go, now we have our finishing cut. And then our texturing cut. Now everything for the lid is on the flash drive, File, New. Let's save these Now by default, what's gonna happen when we create our new file.
If you look over here on the left side, is it's picking up the same material dimensions from the last project that we entered. All of this is fine. Our material width and length are the same but our thickness is different. The base of our or the thickness of our base is one in a quarter. Instead of one, everything else is just fine.
We're still gonna use the center of our material as our origin. Once again, we've got a big work piece here. Now don't create an oval, just paste an oval. So isn't that cool? We pulled that from the old file into this one.
This then is the outside of our box. Now when I rabbit the lid, I want to use a quarter inch rabbiting bit. So that means this is the outside. I want to create an inside. That's a quarter inch away.
Let's let the computer do what it does. So I'm gonna come down here to my offset. Remember we used this before and in this case I wanna go in. I wanna go in toward the center. So I'm gonna go inwards.
And if I use a quarter inch rabbiting bit, I should make my wall thickness a little less than that so that they're not, the parts aren't so tight, that they won't close. So let's go 0.24. 0.25 would be a quarter and create an offset. There's the inside of my box, pretty cool. Now it's just that little bit of work.
We're already ready for our toolpath. So choose the inside, toolpaths and this we're gonna, let me pin it. So it stays open for us, there we go. We're gonna pocket this out. So pocket cut, now once again, we can choose what kind of cutter we wanna do, we wanna use.
Got a lot of material to use take out, use a big cutter. I'm gonna go with our half inch bit. And then here, we can set the depth of cut. So let's think about this, got an inch and a quarter box. This is currently set for an inch and an eighth depth of cut, that's gonna work out just fine.
Working my way down here. This is a good thing to look at. This raster option would move the bit back and forth in the same direction as the grain of the material. Maybe give you a little bit better surface finish. This is gonna move just like the lines on here, show it.
That's gonna take material out a little bit more quickly. I'm gonna go with the more quick material removal. We can ramp our bit into the work. Just like we talked about before, that'll give it a more gentle entry. And then let's call this what it is.
0.5 is our bit size and where doing the interior of our box. And then calculate and see how that comes out. Preview our toolpath. See how she looks. Now we've hallowed that piece out.
Now we'll come back to our drawing pick the outside of the box and you've already seen this. We're gonna do a profile cut, now smart money, pick the same bit. So we don't have to change cutters and we can run one file right after the other. So I'm gonna go with a half inch bit just like I used on the inside. We wanna cut all the way through so that we can separate the body of the box from the material.
So we're 1.25 material, let's go 1.3. So we cut all the way through and add tabs 'cause again, we don't want it to just fall out of there. So if we add tabs, there they are. And then again, we'll ramp our moves. So it eases into the cut.
This is then is a 0.5 exterior. Calculate, there's our warning again. We're gonna cut all the way through it. Well that's okay, we wanna cut all the way through. Preview our path.
Now, here's a good thing to look at before we save this and go run this. Let's go back and look at our exterior. Think about this. This is a pretty significant cut. So we can come up here and look at, how many passes are we doing this in?
Let's edit those passes. This shows us, here's the thickness of our material. We're currently doing this in four passes of almost three eights of an inch each, 375 would be three eights of an inch. That sounds kind of aggressive to me. So I'm gonna come down to the bottom and I'm gonna increase my number of passes.
So that it's easier on the cutter, easier on the machine. It's gonna do the work a little slower but I'm gonna get a better result. And calculate. So even though we changed it there, nothing changes in the software until we come back down and calculate, we get the warning again. So all it did, there was an increase the number of passes.
Let's do the same thing on our interior. Just to double check, nine passes. Well, that's a lot. We don't need to go quite that many. We're taken off about an eighth per, let's reduce that a seven, just like we did on the outside.
Calculate, we're good to go. I'm gonna save these. We're using the same bit on both of them. Now here's a really important aspect. The machine is gonna cut our part in the order in which these are listed.
You want to do the heavier pass before you do the lighter pass. That means, these are sitting here in the right order. If they're not, you can switch them, like I just did. You can drag them so that they're in a different order. So I want to get the interior excavated before it defaults to the outside.
Output to one file. We have the right post processor for our machine. I'm gonna go back. That's the lidded box lid. I'm gonna create a new folder so I don't mix them up.
And again, even though this only says interior, remember that both of those cuts are captured in that file. That takes care of our work here at VCarve. Here's the cool part. We're gonna go fire up our machine. Now we're ready to bring the work that we designed out here to the machine itself and do some cutting.
I've got my blank for the lid on the machine. We're gonna use Walnut. It's currently not secured. So a couple of jargon things here. This piece of MDF, that's my spoil board.
You can probably see from other areas on here it's already been cut into, that's just fine. But what we need to do is get this so it's gonna stay in place. Here's a great way to do this, hot glue. Now, what I do not want to do, is just simply put dabs a hot glue on the bottom and set this down. 'Cause if I don't get it perfectly made it to the spoil board, I might have high spots and low spots where this is a little bit canted.
What works out nice instead is to use the hot glue, kind of like a cock gun. And I'm unplugging it just to give me some mobility here and I'm gonna run a beat a hot glue on the inside corner here. Same thing on this edge. The far end, the back edge, give that a chance to cool and that's plenty secure for our work. And remember that we're cutting through.
We created tabs for that, so that's just fine. The perimeter is gonna stay in place. The lid will be tabbed to the perimeter. I've already installed bit number one, we're starting with a three eighths diameter cutter. So I've got that bit in the spindle.
You're gonna see big changes as we go here. Installation is just like you would do with a router. But what I need to do now is tell the machine where this piece is. And remember in our layout we decided that the center of the board would be what we're gonna call the origin, the zero, zero of our work. I mark that out, so now I'm gonna open up the right part of my software for the shop bot.
And that's gonna let me jag the head whatever direction I need to in order to get it in the right spot so that we can get it over that X. I can move X and Y, I can also move Z to get it a little closer to the work, to make it easier to tell. Now we've got a little wiggle room around the outside of our material, between the edge of the lid and the perimeter that we've created. So if you miss by a 16th or probably even an eighth of an inch in this case, it's not gonna be a huge deal. But now we need to tell the machine that's where we are.
The option then here on my menu is zero axis. And I'm gonna tell it, that's my X zero and that's my Y zero, that's not my Z zero. What do we do then about Z? I'm gonna raise my head just a little bit. And for Z, we're gonna use, what's called a touch plate.
This is the touch plate. And it's connected electrically to the machine. It goes in between the cutter and the work, and the machine knows how thick that touch plate is. It's pretty cool stuff here. So I'm gonna tell it, I'm gonna tell a software to zero the Z axis.
That's this option right here on the menu. It's gonna ask me, is the touch plate in place? Yes, makes a cool sound. So now the machine and the software know that the top of that work, that's my zero point, this point, we're good to go. We're gonna cut apart.
We're gonna find that file. It's on the flash drive that we brought from the other computer. Lidded box lid, that's what we're working on first. 0.375 roughing. Again, both cuts are in the same file.
Start, then it's gonna ask me one more time. It's bringing the file in. It's gonna ask me to go ahead and start. So here's, what's gonna happen. The first thing I wanna do, I'm gonna back out of this, come back to my ability to move the head up and down.
That doesn't change where the machine thinks my zero is, but it buys me some clearance. So I can put my dust shroud back on. And remember how we did this, cut part. There's our file, 375 roughing. That's the bit that's in there right now.
Open, start, here comes okay. When I click okay, the spindle is gonna start running and the software and the machine are gonna take over from here. So what we were seeing right at the end there, when the spindle was moving up and down, it was leaving the tabs behind. It was cutting the perimeter, lifting, leaving the tab, cutting the perimeter. Next thing we need to do is change cutters.
I told you we were gonna get to see some of that. I gonna turn the spindle itself off, it is a router. So we want to make sure that there's no chance of power going to it. Gonna increase my Z just a little bit. So it's easier to get to.
Pop this bid out, get the right collar, 'cause we're gonna a smaller shank and get our new bid in. Quarter inch collar, just like a standard router or a round ball cutter. Very similar, it really is, it's a core box bit. That's doing this work for us here. And let's think about what we got going here.
We have an X and Y zero and we have a Z zero. Nothing we've done is changed our X and Y zero. That's still the same. It's over that mark that we created but we've changed our Z because maybe this bit is sticking out further or less far than the bit we had in previously. So I gonna bring my bit, a little bit closer.
And then once again, use our touch plate. It is important that the touch plate is on a original zero surface. That's the top of the wood, not down here on one of these lower tiers. And then zero R Z. Raise everything up so I can get my dust shroud back on and we're ready for our next cut.
Here on my software, cut part, find it. It's the 0.5, it's the half inch, finishing cut. And remember to turn your spindle back on and we can hit okay and we're gonna run. That's pretty cool. Now, surface finish that we achieved off that ball.
I'm not too worried about it, because we're gonna come back and we're gonna texture that whole thing. So we can control that. Remember I said about the software, that there's all sorts of different stuff that you can do. We're just trying to give you a preliminary at this point. Spindle is shut off, we're done with this bit.
Gonna go back to a half inch shank cutter? So change collars. And you know where we're going next. We're gonna check our Z. We're gonna touch off the touch plate again.
We're gonna bring up this particular file and we're gonna do our texturing. Now, I can't go here for my Z anymore because I've lowered this beyond the original zero point. So we got to get back over here to where wood is as yet uncut, about there. Get a little closer to our work. Get back up so I have a dust shroud, spindle back on, press the go button.
And again, as I go now to cut apart, find that file, 90 degree texture helps me keep things straight. Start and okay. Pretty cool, let's get that head out of the way. And there is the textured lid for our box. Now with our hot glue, what you can do is, use a utility knife and slice, work your way around all four corners.
Don't try to just pull it up 'cause you'll take a lot of MDF with it. That's pretty nice looking beautiful piece of wood with the grain and the texture, really looks cool. Now with the wood, with the hot glue on it, that doesn't bother me. 'Cause this whole frame is gonna come off of there. With the MDF, use a sharp chisel.
And if you have any excess, you can slice that off the surface. Now these are called spoil boards. Eventually we're gonna get so much junk and so cuts on here that we do what's called fly cutting and we resurface this whole board. So that little bit of glue doesn't bother me. Here's what I'm gonna do.
We still have to cut our base. So I'm gonna get the base hot glued in place. I'm gonna recenter, I got to change my cutters. We're gonna do that base with a half inch bit. I'll take care of all that work.
Then when you come back, we'll be ready to run. New board in place, inch and a quarter thick. I centered, I zeroed my X and my Y over that mark. I then, I also zeroed my Z down to the surface using the touch plate. Next step, call up the right file here.
And remember these files are gonna run back to back, because we put them both in the same file. So they're gonna run one right after the other. That's the lid again, let's look here for the bottom. I've already got the spindle turned on, so we're good to go. Lets jag that head out of the way.
So you can see what we've got. There's the base of our box. I'm gonna do the same thing I did before. Here's a utility knife to cut that loose of the MDF. And I'm gonna do a little bit of bandsaw and Rotter table work and we'll come back and have a look at our box.
Here's our box. Now what I did was went to the bandsaw and I cut the tabs on the bottom of the box. I left the tabs sticking out a little bit. So I cut them proud on the bandsaw then go to a sander and sand the tabs off. The lid then I took to a router table and with a quarter inch rabbiting bit, cut that rabbit.
Remember how we programmed this? We have a just under a quarter inch wall thickness, making those two parts go together. Now, for those of you who are probably gonna ask, could we have done this work on the CNC? And the answer is yes. It's just another step in registration.
And we want to start with baby steps to get to this point. But yes, we could have done this, created the rabbit, done this created the dome and the texture. It's all possible on the CNC. So a lot of information here, but watch that programming click-by-click. You can do that along with us on your computer.
And that takes you through the steps that we used to create a textured lidded box.
This is a great video, thank you for explaining it in detail. I am new to CNC and needed soming just like this! You explained V-Carve as well. Thank you!