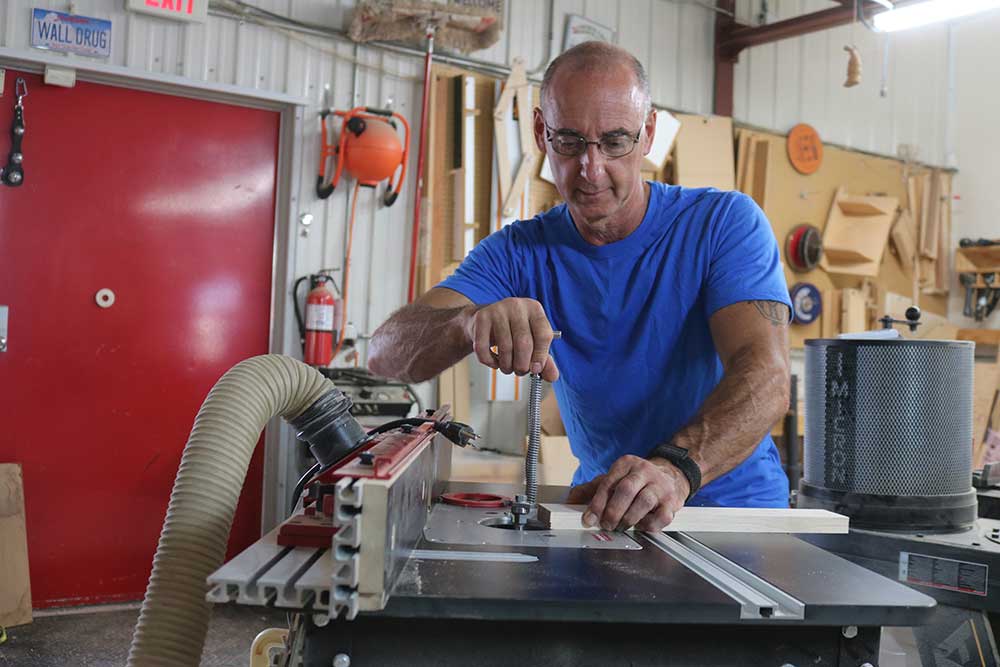
Make Quality Doors Session 2: Making Frames
George VondriskaDescription
Whether you want to make door frames with a reversible bit or two-bit set, we’ve got you covered, taking you through the process start to finish. You’ll need a sled to simplify the end grain cuts on the rails and keep it safe. We’ll show you a shop-made version and a commercially made version.
Before we launch into making coping style joints with a reversible cutter. What I wanna do is talk about some commonalities, things that you're gonna need regardless of how you're doing door joints on the router table. So specifically what I'm talking about here is this sled. I call this a coping sled. What it does is it provides a way for us to very firmly grab the material for when we do the end grain cuts.
So let me grab a chunk of wood. And the way this will work is our material can go into the sled, clamp it in place. This gives us a lot more to hold onto. So it's much safer. Additionally, whenever a router bit exits end grain, we're gonna get chipping.
So because that end grain and this long grain is now up against the backer board of the sled. It's gonna prevent that. These are very simple to make. It's a 1/4 inch hard board base, a cleat back here. That's at least as thick as the material that you're gonna make your doors out of to get full support there.
The toggle clamp to hold that in place. We've got those source for you on a PDF that accompanies the video. Now that's one approach. As you can make this in your shop. If you'd rather buy it, here's another approach.
This is a commercially made version of the same thing offers the same benefits, toggle clamp. Our material goes up against that. Wouldn't support. The wooden support is replaceable. So over time as it gets worn out we can either make or buy a new one.
We've also got these source for you on the PDF that accompanies the video. We're gonna need to know more about these sleds in just a little bit, but not right now. Next thing I wanna do is talk specifically about the reversible rail and style cutter. And when I've taught this in woodworking classes, I always think it's just a little bit confusing because they are called a reversible bits. But of course we can't reverse direction on the collet on a router.
They always run in the same direction. What we're really talking about with reversible is the ability to restack the bits. With a reversible cutter, you're only gonna get one bit. What we can do is make one cut. Then I've already got the nut on top loose so that we can take that off.
After one profile is complete, we do this, and this, and this, and this, and this, and this. Get on there. So that with the one cutter by reversing the stack we can cut both profiles. Good news and bad news. The good news is you're gonna save some dough because you're only gonna buy one bit instead of two.
Two bits referring to the match set. We're gonna have a look at in just a little bit here. Downside to this is that for one of our profiles, we're gonna feed all of our pieces good face up. For another one of our profiles, we're gonna feed all of our pieces good face down. That changes the reference face that we're putting down on the router table.
As we get to that part of the operation. I'll talk some more about that but there are some negative aspects of having to flip your pieces over like that. What I'm gonna do is cut the end grain cut first. So that means we go back to our original stack here. This is what your bit should look like, when you're gonna do the end grain cut.
What I'm gonna do with my bit is get this in the collet, tighten that nut on top. And then we can have a look at the specific setup that we want. So we can actually start cutting the joint. I've got the bit in the collet. Router unplugged, holding a wrench on the collet.
I then use the wrench on here to tighten that nut. Make sure that's nice and secure. Now we're very specifically doing the end grain cut first. This is always the case when I do coping style joints. Here's the reason why.
Right now the board that we're gonna cut, it looks like this meaning the edges of the board are still square. We haven't done the long grain cut yet. When the board looks like this, remember we talked about cutting end grain. We might get some chipping. It's very easy to support this board and prevent that chipping because the edges are still square.
Once that long grain profile has been cut, that's a pretty complex profile. It would be difficult to support that to prevent the chipping. So when the board still looks like this, all we have to do is put that in the coping sled to provide some support and we're gonna be good to go. So always end grain cuts before long grain cuts, regardless of what kind of coping style cutters you're using here in the router table. We need to be aware that we're gonna use the sled, cause that affects setting the height of the bit.
The size of the tongue is controlled by the distance from the lower cutter to the upper cutter. Where the ball bearing is, that's the tongue can't change that. What we can change is where this profile shows up in the end grain of this board. That's controlled by the elevation of the cutter. What I'm gonna do is project this out a little from the sled, and then I'm looking at this right here.
I would like the distance from the top of this bit to the top of my board to be about 3/32 of an inch. Just a little bit under an 1/8. I am a little too low in the router table, right there. That's come up a little. One more, a little bit.
Now I'm using a router lift on my table. You can do the same work by simply using a router where you're reaching under the table to make those adjustments. Gonna work exactly the same way. That's one part of our setup. The next part of the setup is incorporating the fence.
Fence set up is gonna be very easy. All we need is a straight edge. And the fence, all we need to do for the fence is get the ball bearing even with the face of the fence. And that is done by bridging the gap in the fence with a straight edge, bring the fence forward. It's easier when you adjust a router fence if you lock one end down.
Then you can pivot on it, block end. In order to make those final adjustments. Bring in our guard. Then when I use the coping sled what I'm gonna do is sled against the fence. Material against the fence, lock that in place.
Now, one of the things that's gonna happen here is that we spin this around, still unplugged. The cutter is gonna cut into our 1/4 inch bottom and remove some material. And I don't want that to happen because I want that sled to maintain contact with the fence. So what I'm gonna do when I make this cut is I'm gonna come in here, then come into the bit. That's gonna allow my sled to contact the out feed side of the fence, then move forward, then lift off, slide off.
So we're not cutting the entire sled front to back. So here's what this is gonna look like. Now let's have a look at that profile and see if we're getting what we want. What we want is to maintain a balance, this and this. In other words, the small lip that we're leaving here at the top of the cut and the shoulder that we're creating at the bottom by raising the bit, this becomes smaller.
The shoulder becomes bigger. Of course, by lowering the bit, just the opposite. This gets thicker, this gets smaller. What we're looking for in that balance is for the lip at the top to be about half as big as the shoulder at the bottom. Now, one of the things that's cool about using our coping sled is that when we made this cut, I did cut into the backer board.
What does that do for us? Well, the next time we come and set the height of this bit, we now have a gauge block. That'll help us set this up next time. As I adjust the height of the cutter, I can bring my coping sled in until it fits right into the bit. That'll tell me the bit is at the right height.
So here's a lesson out of this. When you're setting this up for the very first time, and you're experimenting with the height of that bit, don't cut all the way through this board and into the sled until you know that the height of the cutter is correct. That way, when the bit height is correct, and we make the cut into the sled. And we do this the next time we use it, that's gonna get us really, really close to having a perfect setup on the first try. Still gonna wanna do test cuts, but that's gonna get us really, really close.
At this stage of the game, what you would do then is with the rails for your doors all the parts that require ingrain cuts, we would go ahead and do this cut so that those are complete before we change bits. Now with our remember one side up one side down idea. With reversible rail and style cutters, when we do the end grain cut it's good face up on our boards. With the long grain cut, it's gonna be good face down. Next thing I'm gonna do is reverse my bits.
Just like I showed you earlier, I'm gonna restack my cutter. Then we'll have a look at making the long grain cut. See how this all comes together. Have a look at that cutter, routers unplugged. Cutters are restack into that configuration that allows me to do the long grain cut.
Next thing we need to do is to control the height of the bit. Now with our end grain cut. We did this, with our long grain cut we're gonna feed good face down. Gotta know that because when we set the height of this bit, the easiest way to do that is to take a long grain piece, flip it over and then align the groove cutter. This part of the bit with the tongue that we have on this part and this profile.
Feeling across the top of the carbide to top of the material. That's not right. Too low. We're gonna try that. Fence position is identical to what we've already done.
Which is face to the fence. Even with the face of the ball bearing. Like I said before, best way to do this is lock one end, back end of my fence is locked. It allows me to pivot and micro adjust like that. We do need something for this that we did not use on the end grain cut, which is feather boards on the router table.
That's gonna help secure our work down. The last thing we want is for these long grain cuts to have the opportunity to lift. That's gonna change the position of the cut and the board and things aren't gonna work out. Little bit of tension. All right, we're ready for a test cut.
Which means we're ready for electricity. You really don't have to feed all the way through. All we need is enough on here to let us have a look at the parts. If you wanna feed all the way through there's nothing wrong with that. Look at the parts means we're gonna take the cut we just made and marry it to the cut we did previously.
And our check is, are we flush across the face, or nearly so. What I like to say here is that I'm looking for a sandable amount. In other words, if these, as I bring them together are just the thickness of a Kleenex. Difference between the two of them, I'm gonna leave them alone. If there's a significant step between these two boards, then we'll adjust them.
Here's the way that's gonna work. If our end grain cut is higher than the long grain cut. If this board is above this board, we have to raise the bit, just the opposite. If the face of this board is below this one we have to lower the bit make that adjustment until we get to that sandable amount. Sandable amount deal is that once the boards are all glued together, I know that if I sand this with a random orbit sander for seconds it's gonna flush them up.
The reason I don't take the time to make it perfect is that I've found from my own work and from teaching hands-on woodworking classes is that we do end up with variations in these end grain cuts. I think it has to do with using the coping sled and how hard you lean on that sled as you're making the cut. If you really hold it down hard it's a slightly different elevation than if you just kind of casually hold it down to the router table. So as you're making a lot of end grain cuts leads to a little bit of variation that shows up here. So making it perfect for this particular piece doesn't mean it's gonna be perfect for another corner.
So get them real close, can be sanded after it's glued together. This is fine just the way it is for my joint. What we would do at this stage of the game then is every board is gonna feed good face down. Get the long grain cut, including the boards that we already have put our end grain cut in. Cause we need to have the long grain profile in all four of our doorframe pieces.
Now the downside of the reversible rail in style. Here's what I've observed is that it can be difficult because we're changing the reference faces from one cut to the other to get these to consistently come out well. And again, from my own woodworking and from observing a lot of students using these cutters, this is the part with the reversible bit where they struggle. And it has to do with the fact that we're good face up for one of the profiles good face down for the other profile. I kind of hate changing those reference faces.
We're gonna solve this problem with the next set of bits that we're gonna look at. So the good news is reversible rail and style can do the job for you. You gotta understand how to restack the bits, how to do the setup. We've just taken you through that. So you can practice this and, or you can have a look at the next set of bits that we're gonna show you.
It makes this work just a little bit easier to do. I've talked about the idea that with the reversible rail in style bit we change reference faces with matched cutters like this. We're gonna keep the good face of your door parts down on the table all the time. Now, all of this stuff that I'm showing you, it's like anything you really need to get out in the shop and practice these skills. So whether it's reversible or the two piece that we're about to do, we really wanna make sure you practice them before you need them for a project.
Here's where we're going with this. We've got two cutters. One of which will only do the end grain cut. The other of which will only do the long grain cut. So we're gonna be doing our door work with a two-bit operation.
One of my favorite woodworking jokes ever. We're always gonna do the end grain cut first. Same reasons I talked about earlier. One thing that can help you if it's a long time between door making operations is here on the steel plate. See how I've written a one there?
Now that steel plate never touches the wood. The carbide does. So that one was put on there, boy, a really long time ago. And it's still there. That is because that's the first bit to go on the router table.
Then when I look at the other cutter, I use the felt tip and I put a two on that one. Second bit to go on the router table. First part of this setup is really gonna be the same because we've got our end grain cutter going in. We're gonna lock that down, set the height just like we did before. Routers unplugged., I'm gonna change things up just a little bit here.
I'm gonna show you an alternative to using the coping sled. And it's something I would say is a little bit more of an advanced approach to making doors. First couple of doors you do I'd like you to still do the coping sled forum. As your experience with this process goes on, then try what I'm showing you here. What I'm showing you here, we're not gonna use the coping sled.
We don't have to compensate for the base of the sled as we set the height of the bit. What I'm gonna do is set the height of this cutter using the same stuff that we talked about earlier which is we wanna locate the profile on the end grain of our board. With many of these two piece sets, what works out really well for a starting position is to make the top of the plate, even with the top of your material. Easier to feel it than it is to see it. Let's try that.
The work with the fence, you've already seen. Lock one end, pivot the other end. So the face of the fence ends up even with the ball bearing. I'm gonna pinch my fence faces in a little bit. I'm gonna narrow up the opening.
And that has to do with the way that we're gonna do this end grain cut. You see that in just a sec. Here's the difference. No coping sled end grain of the material against the fence. Scrap board against the fence.
And these two are gonna go pass the cutter together. So what we're changing here obviously we don't have a toggle clamp. I can't just hold the board. I can't just hold the scrap board. I also have to hold my rail.
So that's where, like I said this is a little bit more of an advanced technique because we don't have the benefit of the toggle clamp but I have made lots and lots of doors this way. Once I got comfortable with the process. Wanna make sure that your scrap board is wide enough that when I have my hand position on this board, I can be well away from the cutter. In other words, if this scrap board is really narrow, I'd have to have my hand in here to keep pressure against that scrap board. That's too close to the bit.
So something about five inches wide is gonna work for ya. Gotta make sure that this end has been cut nice and square so that the board remains perpendicular to the fence. The rail, when we're cutting, What I'm looking for here is the same stuff we talked about earlier. It's just that when we made our cut with the reversible cutter, it was this way. Now we're this way.
So thickness, thickness. We wanna maintain that balance between the two for this cutter. I would say we're in pretty good shape there. Now notice that I only went in partially. Then I backed off.
So I could have a look at the elevation of the cut. Once I know that it's okay then we're ready to feed all the way through that into our scrap piece. These are our end grain cuts. So that operation needs to happen to the end of every rail that you need for all of your doors. Before we change the setup.
One of the things I like to do now that I'm ready for doors is I would bring all of my frame parts to a workbench and mark the backside. And the reason for that is that with these two piece sets, everything feeds good face down. So as I'm doing my door operations that X tells me when it's up that I'm cutting my parts the right way. It's really critical on these rail pieces. Because if I accidentally flip them between cuts we're gonna have a part that you can't use.
This part of our story. We're right where we were before which is we're ready to take that bit out. Change to the long grain cutter, go through that set up. So that we can get groovy with our doorframes here. So let me do some setup change here and we'll come back and look at that setup.
You've seen a lot of this stuff before, cause we just did it with the reversible bit, but here we go again. I've got the second cutter in the table. That's my long grain bit or outer unplugged. This is my end grain bit. We're gonna set the height of the bit until the groove cutter is even with the top of the tongue.
Then guess how we're gonna position the fence. To make the face of the fence, even with the ball bearing. What am I missing? Cutter board. Sometimes there's little quizzes along the way.
And what are we looking for? A sandable amount, same story here. If the alignment isn't here, we need to adjust the height of that bit like I talked about earlier until we have that sandable amount across these two faces. Between the two cutter sets, reversible and two piece the overall process is the same. The benefit that I feel we get from the two piece set, is that because everything feeds face down.
It's easier to get good alignment across the face of our pieces. We do wanna make sure that doorframe parts are all the same thickness, but if for some reason there's a little bit of variation in them. When we use a two piece set that variation would all show up on the back of the door, not the front. Because the way that we set this up, we're referencing off that good face, the front face all the time. I do find it's a little bit easier to get good results from the two piece set than from a single reversible.
I wanna talk about another aspect of the long grain cut before we end this part. And that is the way that I'm using this push stick. In the case of my test pieces here, that test piece is pretty short. but it's not uncommon especially with styles for a door, styles being the vertical components. It's not uncommon that styles are contacting the cutter.
While a portion of the material is still cantilevered off the table. Gotta be really careful about that because if you press down on this end of that piece it'll lift up on that end of that piece. And it's gonna mess the position of your profile up within the thickness of the board. So I'm very intentionally feeding this with my push stick horizontal, not vertical. Even on these short boards, it's a good habit to be in.
And certainly when my board is projecting off the table, wanna make sure that I'm using that horizontal pressure not vertical pressure. Not uncommon question is could I put another feather board here in the table to keep pressure this way right in front of the bit? You sure could. For me, I find that it then interferes with me being able to get my push stick through here. And if interferes means I have to stop, reposition, restart, that's gonna show up in a little burn in your cut.
So if you wanna experiment with feather board and see how that goes for ya, that's fine. But I find that by maintaining that horizontal pressure, it allows me to feed in one fluid motion pass the bit that makes it easier to get good quality cuts still providing the pressure I need to keep the material against the fence. I do wanna do one more long grain cut to talk you through hand position because that's really, really important. So let me grab one long style and we'll have a look at one more cut here before we leave this point. There's a ballet that has to happen with your hands to successfully pull off making these doors.
The feather boards do help us a lot, but these hands got to do some stuff. The cantilever board idea, I've already talked about that. Right hand is gonna control the push stick horizontally to make sure we feed uniform. I really wanna talk about your left hand and what's gonna happen here. Really important to never allow your hand to pass immediately over any cutter.
Router table, table saw, doesn't matter what you're using. I wanna leap frog past the bit. So what I wanna do here is feed correctly with the feather board. My left hand on this longer board is gonna maintain pressure up here. When I start to move forward, and I get to the bit I'm gonna keep this pressure on the in-feed side of the fence.
As the push stick catches up, I'm gonna leap frog past the bit, engage with my board again, maintain that pressure on the outfield side. Always keeping the board moving forward. Cause if we stall out, you're gonna get a burn or a mark. So watch for that hand position and work on that in your own shop to make sure that in one fluid motion, we've got this going past the cutter and we're staying safe by never having hand pressure immediately in front of the bit. Like I was saying earlier, all this stuff takes some practice.
So what I really want you to do is get out in the shop, work on setting up these bits, regardless of what style you have. Do some practice pieces, do some practice doors. So that before you need this for a project, you know you've mastered these skills and you'll be able to quickly move through this and work on the router table here.
Share tips, start a discussion or ask other students a question. If you have a question for the instructor, please click here.
Already a member? Sign in
No Responses to “Make Quality Doors Session 2: Making Frames”