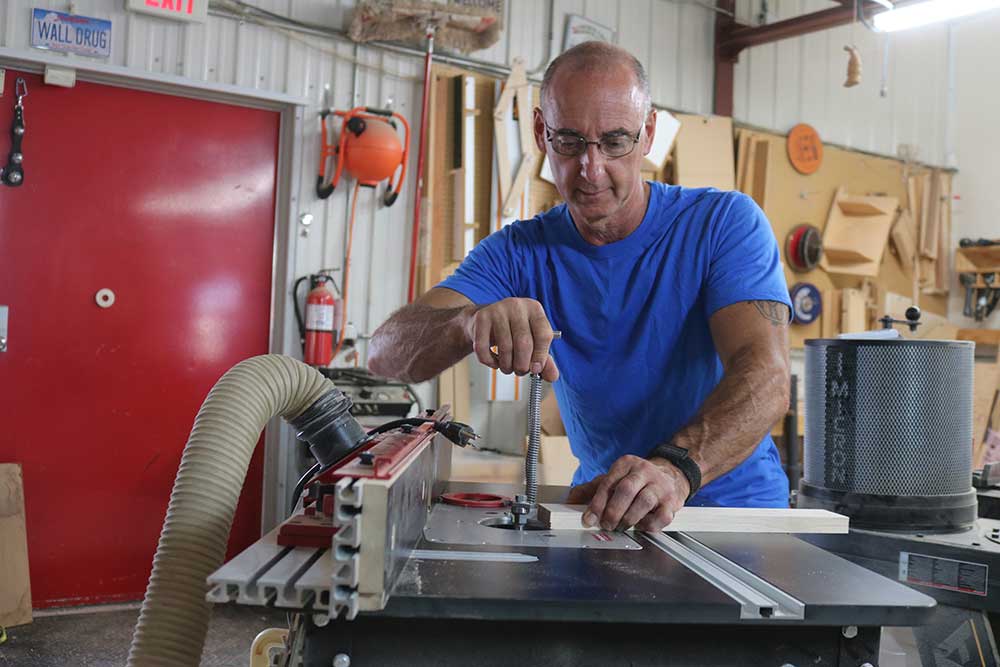
Making a Drawer Lock Joint
George VondriskaDrawer lock joints made using a drawer lock router bit are a GREAT way to put drawers together. Once the setup is right the joint can be cut very fast, and the mechanical interlock the joint provides makes it very strong. What’s not to like? Well, in all honesty the getting the setup just right can be fussy.
Making this work
For a drawer lock joint to fit correctly, the height of the bit AND the fence position must both be perfect. If either one is off, you’ll have a lousy fit, which compromises the joint. Bit height is especially critical. It’s definitely very handy to have a router lift in your table for making these fine height adjustments.
How to get it right
There’s a logical sequence of events involved in getting a drawer lock router bit set up correctly. Start by using the techniques we provide for getting it close. The, through a series of test cuts and tweaks, you’ll fine tune the set up until things are perfect. It’s important to make the test cuts in the same thickness material as you’ll be using for the project.
Controlling tear out
When making drawers one of the cuts will be across the face grain. This can lead to a lot of tear out and chipping on the face. Don’t sweat it, we provide you with a great way to avoid that.
Alternative methods
Drawer locks can also be created on the table saw using a dado head. This is another great way to create lock joints. You should also check out our content on different types of joinery.
More info
For more information on Kreg products visit www.kregtool.com or call (800) 447-8638
Kreg PRS5000 router lift
Drawer lock router bit
A drawer lock bit is a really great way to put drawers together, just in general to put corners together. But I know this is a cutter that makes smoke come out of a lot of woodworkers ears. So let me take you through the setup on this. Once you get the hang of it, it is a really great way to make corners. First thing we'll do is get that bit in the table.
And I got to say, boy is it handy to have a router lift. It's like having an elevator in your router table. And when I can just bring the collet up like this, it sure makes it easy to get bits in and out, of course, with the router unplugged. The router lift is going to pay off as we go through this process because the difference between a good fit and not such a good fit are really small parts of an inch. So the router lift is really going to let us micro adjust.
Now here's our first micro adjust. I've got a line on my board, that's approximately 2/3s the thickness of my material, and that's going to be my starting point for the height of the cutter. Let's go right about there. And what's going to happen is, this is just going to get us close and then test cuts are gonna tell us exactly what we need. With router lifts it's pretty common that a full revolution of the handle is a 16th of an inch of travel.
So it really lets you fine tune things, of course, then a quarter turn is only a 64th of an inch. It's a really good way to finesse stuff together here. Now on the fence location, I'm going to use some setup bars, cause here what I want, is for the tip of that cutter to project half the thickness of my material past the face of the fence. So first step, let's bring those fence faces in just a little bit closer. Now using my bar half-inch stock, I'm going to bring that in until the bit projects a quarter inch past the face of the fence, then lock the fence in place.
Again, test cuts are going to tell us if this is right or wrong. Now with the drawer lock cutter, the way this works is that one of our cuts is made with our material face down on the table. The other cut is made with our material with its face against the fence. So we to do that, we need to simulate the exact same setup. So we need to do that also, as we're doing our test cuts.
Now we can look at the joint and based on symptoms, we can tell what correction we need to make, if any. So when we put this together, it's not going together. In other words, that tongue right there is too big to fit into the groove. Here's a way to think about this, the groove is always the same size because that's made by that part of the cutter. We can reduce the size of the tongue.
Now think about the way this component was cut. It was on the table like this, the tongue needs to be smaller, as a result, my router bit needs to lower. This is where it's really nice to be able to finesse that height with our lift. So let's look at this again and see what it looks like. I'm going to say, we need to lower, boy not much, cause it almost goes together.
We need to lower by, I'm going to try a half a turn. The other thing we're looking at is, this component. This edge needs to be out here, flush with, or slightly past this space. That's controlled by our fence position. So we need to move the fence back a little bit.
We need to increase that depth of cut. We need to move the bit down a little bit so that we reduce the size of the tongue. I'm going to just pay attention to my index marks here on the table. Dial that down. And second verse same as the first.
Gonna mark the edges I've already looked at so I don't get confused a little bit when I put parts together again. All right let's have a look. Well I went too far in both directions. So here's the deal, when I put this together now, it's a little bit too loose. The tongue is just a tiny bit too small, I gotta raise my cutter.
I'm going to come back up a quarter turn. When I look at this, this edge is too much past this face. So I took my fence a little bit too far back. So here's what I'm going to do, I'm going to correct my fence, I'm going to raise the cutter, I'm going to make another test cut, and we'll just continue through that test cut process until we get the fit that we need out of these boards. All right, the fit of the tongue is great.
My fence position is still just a tiny bit off. Now, I very intentionally did an end grain cut here cause that's how we're going to do drawers. And I want you to see that because I'm going to show you how to fix that. At this stage of the game, our bit height is correct. So here's what we can do, to eliminate this chipping, we're going to make what's called a zero clearance fence.
Very, very simple to do. What I'm going to do is run the router bit, with the in-feed side of my fence loose, I'm going to push that into the cutter. Now on my depth of cut on my fence location set up, I need to back the fence off just the tiniest little bit. And then let's make that zero clearance fence to eliminate chipping. Now we have the fit that we want.
What I'm looking for is a good fit between the tongue and the groove, a little bit of a lip here because after glue up, I'll trim that off and make it look like I made it perfect right from the start. Now that we know that the fit is good we're ready to run all our drawer box pieces. Here's the thing to keep in mind, when you do this part pay attention to which component is which and what happens is that, as we run these parts, we want to pay attention to which are our drawer sides and which are the drawers front and back. So the way that the joint interlocks, it'll always be the drawer sides that feed vertically and the drawer front and back will feed horizontal. I really love the way that the drawer lock comes together.
Not only do we get mechanical grab between the components but we also get additional glue surface. And you can see that once we get the setup right, boy is it a fast way to make corners. It is very beneficial to have a router lift you can use for this because of that micro adjust that we need to do to get the height of the cutter, just right. So check out, drill lock cutters. It's really a great way to make boxes.
Once you've got the bit height and table positions dialed in, you should make your cut into a piece of scrap and then label and save it. Next time you need to make the cuts again in same-sized material you can re-set the bit and fence until it fits perfectly into your saved reference cut.
Great video! I avoid changing the fence position and the bit height at the same times. I record the bit heights and fence positions for these drawer lock cuts (as well as other common cuts) in a log book. It is based on the thickness of the front and sides. I measure from the fence to the miter gauge slot in metric. Using a magnifying glass, I can adjust the fence position easily by 1/2 mm. For these types of cuts, I use a designated, one-piece, sacrificial fence that I C-clamp to my regular fence. That prevents the tendency for the sides to rotate into the bit where the regular fence sides separate when routing a work piece vertically instead of flat on the router table. To make a sacrificial fence, clamp a suitable piece of 3/4 or 1/2 inch mdf to your fence with the fence placed behind the bit, start the router and pull the mdf fence towards you into the bit until it comes all the way through. You can easily re-use that mdf for the drawer lock bit next time. Exact fit over the bit next time is not required. You just want to have the area of the fence above the bit closed. I do not recommend chewing up your regular fence to do this. Yes, you can make new ones, but that requires a T-slot bit, 2 perfectly identical pieces for the sides and good bit alignment. It's an unnecessary pain. The sacrificial fence works well whenever you need to route a piece vertically. That and other useful templates should be saved and available. For the non-professional, like me, it is very useful to keep a log book of your projects. That way, should you decide to repeat them, you will be able to see how you build it the last time and you will also be less likely to repeat the same mistakes. The first few pages of my log book have router bit/fence settings for various cuts. To obtain consistent results, always measure with the same ruler.
For the Baltic birch plywood I see you use, does the shortness of the joint cause a problem with the layers shearing off? I have experienced That little nub is susceptible to breaking off and hence the joint does not hold... any suggestions on how to either reinforce or keep from shearing off?
Avoiding tear out on birch ply drawer sides
I think it's important to mention that in changing one thing you affect the other. In other words changing the fence position moves the groove to position the side correctly, but it also changes how it cuts the tongue, so it compounds the adjustment. Also, changing the bit height not only adjusts the tongue thickness, but it changes where the groove lands on the front, effectively shortening or lengthening the entire drawer box. Maybe just a little and maybe well within the adjustment of your drawer slides, but it's something to consider. All that said this is a great video! It's a tricky joint to get right even with a setup block.
I've tried creating blind dovetails on the 1/2" baltic birch George used with mixed results. I was using my Leigh RTJ400. They did not recommend using plywood. He used a zero clearance fence to avoid chipping. Is there something equivalent I could do when cutting my dovetails. Dovetails can look so nice when using baltic birch when it works. Thanks!
What router table are you using?
While your on the subject demonstrate the lock miter bit which is even more fidgety to dial in, accordingly highly recommend using a router lift with a bit height locking feature.
I would 1st start with a sacrificial fence mounted and then make my adjustments. I would never purposely cut into my Kreg fence! That really surprised me!
Instead of cutting into my router fence, couldn't I use a backer board?