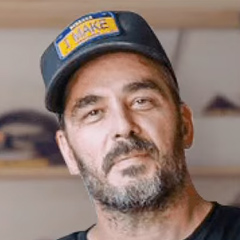
Making a Knife from a Saw Blade
Jimmy DiRestaDescription
Steel quality
The durability of a carbide-tipped saw blade comes from the carbide, not the steel plate. So, the plate isn’t the BEST knife-making material in the world, but it isn’t bad. A file test will tell you a lot about the quality of the metal, and heating and quenching after the knife is made will help a lot. Blades that are not carbide-tipped are most likely made from a higher quality steel.
Cutting and shaping the blade
You can do all the cutting with an angle grinder and cut off wheel. Make shallow and gentle cuts so you don’t snap the cut off wheel. Finalize the shape and polish the knife using flap sander discs on your angle grinder.
Get a handle on it
Use a good hardwood for the handle. If you want to add pins like we did, brazing rod works great. Adhere the handle to the blank with two-part epoxy, let it cure, then shape and seal the handle.
More than knives
This is a fun process and can be used for more than table saw blade knives. You can make other shop-made tools, like a custom shaped scraper. It’d also be fun to get a kid involved and help them make their first knife.
More on knife making
Knife making can go in a lot of directions. My friend, Tom, has been making knives for a long time and is happy to talk about it. I’ve been buying knife blanks for years and making my own handles, including all of my kitchen knives.
Unlock Your Woodworking Potential!
Sign up for our newsletter for endless woodworking inspiration! Become a member today and gain access to a world of craftsmanship.
What you got there? I got a saw blade. What do you got? I got another saw blade. But you know what I see?
What I saw? I see a knife. Oh. I saw a saw blade, but now I see a knife. So what we're gonna do, where we're fixing to go with this is saw blades get to a point, carbide-tipped saw blades get to a point where the carbide has been sharpened so many times it can no longer be sharpened.
And then you might say to yourself, you might say. You might say, "What are you gonna do with this old blade?" So this old blade, this old blade, this old blade are gonna get turned into knives with a few qualifiers, which is we don't know anything about the steel, really. We don't know what kind of steel it is. It may or may not be hardenable. We will do a test.
But, ultimately, what George and I, and potentially you- Don't cut yourself. Oh, I'm sorry. What George, and I, and potentially you at home are gonna learn is how to shape a knife, how to design a knife, and how to, basically, structurally build a knife. Hardening is a different science that we may or may not be able to go into here, but if this is a hard enough material. We're gonna quench 'em because it's gonna look really cool on that camera.
Oh yeah, yeah. So we're gonna quench 'em no matter what. We're gonna quench 'em, we'll see what happens. And we're gonna make wooden handles. We'll do wooden handles.
Which there's also some edge-umacation that'll come out of that. Yeah, there's a lot to making a knife, you know, keeping it sexy, the utility of it, the feel in your hand, there's a lot to it. All right. Switch to this camera. So one of the things you can look for if you wanna do this is if you have like a big sawmill blade.
Saw blade. Those are the ones that I use most. That isn't carbide-tipped, is where I'm going with this. That you probably have a better quality steel throughout the plate- That's right. Than what we have here.
Because the strength, the integrity of the tooth on this, comes from the carbide. Right, on those old sawmill blades, they will harden steel, a tool steel, throughout. Yeah. So anywhere you cut, and plus you also have a much bigger, broader area to cut a knife out of, or even a meat cleaver. Yeah.
Are we, is this a competition? It certainly looks like it. Get stations set up. All we need now is digital clocks behind us, I think. Ticking away.
All right, so- Might amp the anxiety. Next thing we're gonna do is some design work. I know the profile of knife I wanna make. I'm gonna try to ignore Jimmy and not see what he's doing so I don't steal. Jimmy's done this way more than I have.
So I'm gonna, I am gonna steal ideas wherever I can. Plagiarism is a form of flattery. Yep, we don't mind. Okay, I'm leaving for my table. Okay, I'll be over here.
Quit stealing ideas. I'll be at my table. What are you doing? You're doing a David Bowie kind of a style? Yeah, well you know what, I was gonna do like a, they call it a drop-tip Bowie, where the tip drops down like a little bit like that, which I might still do.
I might do that just for a little added style. But I'm gonna cut this broad shape out and I'm gonna use a cutting disc here on the angle grinder. But I'll stand up when we're ready to go. All right, so I'm gonna do, is it tanto? Do you know?
Am I saying that right? Do you know that style where- Yeah, yeah. It's a very straight blade. Yeah, tanto I think it is. I've always wanted one.
So I'm gonna make one. And part of what I like about it is, because we're cutting with those angle grinders, it's very lineal. You got an easy, straight- Yeah, so. Nice straight. Try and get that little, shallow curve in there.
Across the top? Yeah. Like a little rainbow? Yeah. But the knife, but the blade is straight on those, right?
No, they have like a little bit of like a- Concave, convex. Just a very slight, kind of like a samurai sword. So that's why I brought this because I was anticipating you saying I should introduce a little curve. I'm trying to be flexible like this curve. So when we cut, a couple things.
Oh water. Have some water because one of the things we don't wanna do is overheat the plate, and maybe if it's got some temper in it, take the temper out. So you don't wanna lose your temper. And then the other thing I have on hand is a huge form of water. Fire extinguisher.
We are about to make a bunch of sparks. So it's a good idea to be ready for worst case scenario just in case something really bad happens. I always keep a fire extinguisher anytime I'm doing anything that creates sparks of fire. Even when I weld, I always keep it right nearby. Yeah, I think it's a smart move.
All right, I think we're gonna get noisy. I'm gonna cut. And you want masks on, a mask on, because we're gonna throw a lot of junk. Crews being the divas they are, we had to stop because Terry wanted to switch to slow motion because Jimmy's about to do cool stuff. Ready?
So I think sparks on slow-mo are typically cool, so. So a thing, when you're figuring out your plan and what your knife is gonna look like, keep in mind that we're doing this cutting with a cut-off wheel and an angle grinder. So you're not gonna get in there, it's not like running a scroll saw, you can't get in there and do real sharp turns. But here where I'm trying to do this little uptick on this handle, I can't make that turn with this. But what I can do now is come in, like relief cuts on a band saw, joop, joop, joop, joop, in order to get closer with this so I don't have to do so much grinding or whatever later.
I like that big shape. Yep, I wanted to keep the hole for fun. Just for funsies. I like that. All right, so anyway, I'm sorry I interrupted you, because you did some research.
I did a little research on what this particular metal is inside of a carbide-tipped saw blade. And what that typically is is a low-grade spring steel, typically. So it is good for what we're doing. We can try and harden it. I haven't gotten that far in my research.
We just did the file test and it does file but not as easy as the metal on the vice. It has a varying degree of hardness. It's not- In addition to the sparky spark- Yeah. This is a cool way to get some idea of the metallurgy. See what's hard.
Because the softer it is, the easier it'll file, like pine versus hard maple for a sander. Like, for instance, let's see, the hardest piece of metal right around us now is these tips. You can tell the sound difference too. Yeah. You could hear that grabbing and cutting away.
So this is in between those. Okay. So we're gonna still try the quenching experiment, mostly because I think it's gonna look really cool. We don't know if we're gonna gain anything from it or not. We're a couple steps away from that.
Right now, what we're fixing to do is refine these shapes a whole lot better. We're just using flap sanders on the angle grinders. And we're very intentionally, Jimmy pointed this out when we were off camera a second ago, we're very intentionally sticking with angle grinders for this whole thing, because they're accessible and kind of everybody owns an angle grinder. So we're not using any funky tools here. And I was talking off camera, I am very pleasantly surprised that I didn't snap a cut-off wheel when I did this because of the curve that's here.
And, of course, that cut-off wheel is 4 1/2 inches diameter straight. So it's not really designed to do that. But don't forget that tip of that grinding wheel, like right here, so if we're looking at it at the end, it's only that much of it needs to go through. So you can cut quite a bit of a curve. You don't want to go, the deeper you go in the more flatter you really need to have your curve.
So if you just go in it with the tip of that circle- On a thicker chunk of steel, we couldn't get away with this. Right, well- Like if there was a half inch thick it'd be tough. Right, it would be very tough. What you'd have to do is make your curve really wide to give out clearance for the back of this as it comes around. But baby steps is the key to that to make sure.
Yeah. Now that I've had this in my hand a couple times, because it's set free from the blade, I'm not thrilled about the length of material I left for my handle. So I'm gonna take some away here. The grinder will do that easy. I think I'm gonna shorten my blade by about 3/4 of an inch and add that to the handle.
And I wanna leave, I don't wanna build the handle out in this direction past the end of the metal because I think with my handle I wanna leave that showing, the expansion slot, so that you can still tell that came from a table saw blade. What you got? Look at that. Really? Do you get, like- Let me see.
Not so bad. Not so bad at all. Actually, the only criticism I have of what you're working on here is your blade is a little too shallow. Now imagine a hand chisel if it has like a blunted bevel. A short bevel.
Yeah, a short bevel tends to stay duller more often than a long bevel. You can get a nice clean shave. So it's the same thing here. You have a really stunted bevel. You see I brought my bevel back almost to here.
Yep. And I still am not sharp because I wanna make sure that when we quench it we're not super sharp. We don't want to go to that, that's all gonna turn blue. So we wanna leave a little bit of material there before- And one of the things I think happened when the cameras weren't running is we were talking for a second about, as you thin the edge down, you gotta be progressively more careful with the angle grinder. Right, because you're going to heat it up faster.
Because there's less material here. It's easy to blue it because it's so thin. Right. All right, so I can bring my angle back. And I was giving you this little tip here.
I think I was able to smooth this all out, because with the tip of the grinding wheel, it's a dimple. You're putting a dimple and you're trying to move that dimple across and then do it all at the same time. And a way, just like using a planer for wood, or a hand-plane for wood, if you use the file, you could bring that bevel back all clean and evenly. This is a cool setup, you know, if you're primarily a woodworking shop, but every once in a while you do something like this and you don't really want to dedicate a bench space to a metal vice. Yeah, I like this idea.
Just having one available, yeah, that you can clamp it, Jed. And that's a great vice, that's a great pattern-maker vice. Well yeah, so what's cool with this- You could change the shape and direction and everything. When this, when the jaw is loose, it loosens from this so it'll pivot but then you can also do this. Yeah, that is a great vice.
And work in the other direction. So if I wanted to... Trying to think, would that help me now? Maybe, I don't know. But yeah, if you want go in the other plane.
So here's where we're at. We're not sure completely what we have have on the metal, as far as, like, quality metal, hardness of metal. So what Jimmy's experimenting with is an off-cut from the table saw blade and then we're gonna quench it. And the test will be, does that get it harder than what we started with? And the file is gonna help tell us that.
But part of what we're running into here, the ideal way to do this would be in a forge where you can get uniform heat over a really large area. Right. And we're trying it, Jimmy's trying it with torches, and the problem is that tip is ready to go maybe to quench, but the area back here is not. It's hard to keep an even heat here. As soon as he moves away we're- Let's see what it does anyways.
Ready? So in the can is just off-the-shelf vegetable oil, that's what we're quenching in. And there's different stuff going on. There's a lot of metallurgy, there's a lot of chemistry here. You can quench in oil, you can quench in water, you can quench in waste oil.
You can quench in quench-specific liquids. The reason we did vegetable oil and MAPP torches instead of a forge and some weird quenching oil is that everybody's got vegetable oil and a lot of people have this style of torch. Feels like it hardened a little. What say you? Sounds like it hardened a little bit.
Do you hear the difference? Yeah. So that test worked. So you can hear that versus. You have kind of a raspy voice there.
Yeah, it's kind of a higher pitch. I'm making a file joke. I know, I was laughing on the inside. I think I'm very funny. I was laughing on the inside.
Anyway, so what we could do. So what we could do with the knives is try and maintain that red-hot on the edge, so we can go like this just on this edge. And this is much thinner than that, so this will stay redder faster, it'll get redder faster, but it'll also go colder faster. And so we can try and do that and then- And we need to double check on yours. We're full to about here the canola in the can.
Yeah, if we just give it a tilt like that, I'm fully submerged so I'll be able to do that. So we'll just put a chunk of wood in there. So we gotta go one at a time because we can only heat and quench, like, onesie, twosie. It's a little thin, like, in my world of making knives, it's a little flimsy. It's a little thinner than most knives you're working.
This wouldn't be a take-it-in-the-woods and work with it kind of a knife. But, like Jimmy said earlier, is an experience of shaping a blade, working with a blade, putting a handle on a blade, which we're also gonna do. There's a lot of cool stuff going on here. So I think, again, if we were in a plate where it wasn't carbide-tipped, where the whole, the blade was the blade, you'd have a thicker plate to work with. You'd have a thicker knife when you're done.
More robust. Don't make a machete out of a table saw blade. It's gonna be too thin. One of the things that intrigues me so much about blacksmithing is reading the color of the metal to know where you're at, and yellow, versus red, versus orange. And then the other, the chemistry or physics that's so cool there is when you get it to a certain temperature, even something that's ferrous metal that's completely magnetic will no longer be magnetic at a certain temperature and then that gives you a clue- Yeah, where you need to be.
about where you're at in the heating process. It's really amazing stuff. Okay, we'll give it a shot. We'll see what happens. Doctor.
It smells like we're making french fries. Or, yeah, popcorn or something. Are you looking for the file test? Yeah. Yeah.
Okay, it may not get hot enough, but- It seems a little harder. Yeah, maybe. Well, could still scratch it. But that doesn't mean that it's not a certain type of Rockwell. Yeah.
You know? Well I'm gonna, I want the experience so I'm gonna go ahead and do the same thing to mine and I have less metal in mine. Yep. So maybe I'll, maybe it'll heat easier. But no matter what, I'm gonna do it.
All right, now, that sound that you had in your ear before. Oh, because I, I think even on a stroke I was cutting before. You feel like you're cutting? No, not, no. Oh okay.
So maybe you got something. I was digging in before. Yeah, so you feel a difference? And I'm pretty much getting nothing now. Yeah, okay then, that's it.
I'm not even, I'm really not even scratching it. Then there you go. Then it worked. Cool. So to get our holes punched here.
Yeah. I would say we'll try this. I'll show you. So this is cool metallurgy, that we're doing the same thing, we're taking it to red hot but it's going in the opposite direction because you're not quenching. It's taking the hardness out of it.
Right? Yep. We're gonna just let it get red hot. Really soak it in that red heat for a couple of, maybe a minute. Get it?
We are through. Are you going bigger? Yeah I wanna give my- I'm gonna use 1/8 inch brazing rod for my pins. Okay. So I wanna have a little more wiggle room to get stuff.
So I read a weird thing once that said, its suggestion to get where you got there, was in a drill press, put the drill bit in upside down and let this end run until it gets uber hot. Oh, that's interesting. Then flip it over and, you know, you're making that happen. Yeah. Then turn it over and let the twist portion drill a hole.
Oh that's really cool. I never heard it. That's a great idea. Yeah, the lower RPM helps a lot. Yeah the low, because, otherwise, if you go too fast, what you're doing is basically generating a lot of friction and you'll dull out your drill bit before you do anything.
We are ready to put handles on these, but do we go back and clean these up again first? Yeah, we could take these to a palm sander and clean them up. That would be a good way to get these nice back to metal. Okay, we're gonna do that. Where are you?
We're gonna do that. There's like 4,000 cameras set up here and I don't know what to do. We're gonna do that polishing step off camera. All we're gonna do is take- It's a palm sander. There it is.
Yeah. What we're gonna do is, go ahead. We're just gonna sand them until they look cooler than they do now. Yeah, if we had a belt grinder, I'd take them to the Scotch-Brite wheel, or if you have Scotch-Brite on an angle grinder, Scotch-Brite would be a perfect opportunity right now to get that all metal back. Okay.
And then we'll come back and we'll handle this. I got my handle prepared. We're using brazing rod as pins, as per your suggestion. And you had this cool, casted up. It's madrone is the wood in there, and then epoxy.
So our blanks are just like each other but different. Mine is madrone and green epoxy. Yours is madrone and red. And we located our holes that we drilled through in the last segment, on the wood, drilled them all the way through the blocks and then cut 'em in half, and then prepared the surface that touches the blade, and then also prepared the area that's gonna be unreachable with the sander. Yeah, because once we're- Glued in.
on there you can't round. And so now we're gonna epoxy in place, let them dry, and then we'll grind what we can up to the inside parts of the blade that are still inside there. And you did a, you took your blade, show that guy, a little further than I did. And I intentionally left mine rough-looking because it's rough, like, it's a handmade knife from a table saw blade. So I kind of, I like that those scratches are still on there.
Yeah, they showed a little bit. They give it kind of a rustic look. You can see 'em here. All right, two-part epoxy. No, nothing hugely earth-shattering here.
I've got one part in the bucket already. We'll do a little of this. I have denatured alcohol nearby so that if you get epoxy someplace you don't want it, denatured alcohol will take that off. So- You have to get a wipe in there. Yeah, as, if the epoxy cures up in this inside corner right there, it's gonna be horrific to get that out later.
Yeah, you're don't wanna stretch your blade trying to get that off. It's easier to clean that out. And then because we don't have glovies on, if we have a little epoxy on our fingers, the denatured alcohol will take it off of there too. So we will come back after the glue is dry. We're gonna come back, shape the handles just a little bit.
After the commercial break. After the commercial break. And I would like to get, finish the edge on here. And then, I don't know, whatever we can do to kind of see how they cut. Like we could bring a block of cheese, and a box of pepperoni or something.
Yeah, that would be good. That'd be kind of cool. Yours will cut the cheese. Mine will cut the pepperoni. Okay.
Careful. Use the rest of that to make a river table. Okay, I overmixed. I didn't wanna run out. I heard river tables are in.
I didn't know if you were an excessive gluer. All right, we're gonna watch glue dry. We're actually gonna go and eat pot roast and have dinner, and we're not gonna watch glue dry, but we're gonna come back later and finish this. In a world. In a world where pot roast is king.
I don't know. In order to shape the handle, the first thing I'm doing is putting masking tape on the blade so I don't cut myself there, and use a pair of nippers to get those brass pins as close as I can to the wood. I like starting on this 12 inch sanding disc because it's very aggressive and it's gonna let me hog a lot of wood off really fast. I like to start on the big broad flat belt this way I like to keep everything in one plane and I can start to develop a series of facets. And as I develop a series of facets, I start making them closer and closer together till they begin to become round.
For me, went from the disc to the belt. I think I've got, like, 80 grit paper on the disc and 120 on the belt. So I'm roughing out on the disc. And then, in the end, doing the same thing as Jimmy. I'm rolling the handle over, and over, and over again on the belt to try to get that smoothed out.
But it doesn't let me get to the inside curve on the bottom of my handle. So to get to the inside curve on the bottom of the handle, we use this bench-top oscillating spindle sander, does a great job at removing any material on an inside curve. And then there we both started rolling the corners over too. And again it's, we're both gonna end up with a bunch of facets here and eventually just keep leveling, leveling. The facets get smaller and smaller, which eventually turns them into a curve.
So yeah, we're starting to shape the handle with rolling it, and then just keep feeling it in your hand. It's very subjective for where you want to end up. It's just gotta feel good in your hand. The reason I like to do the facets on opposite sides as I go, is so that I could see where I am as far as making one side symmetrical to the other. If I do a series of facets, I could see exactly how they're mirrored on the opposite side of the the handle.
And once I feel satisfied that I removed enough material, I begin to roll those facets into the round shape knowing that I'm relatively close, as far as a mirror image goes, from one side of the handle to the other. Using this oscillating spindle sander, I could really get in close and start eliminating some of those facets and rolling over any of those little sharp edges that I could feel with the palm of my hand. I'm very comfortable shaping with a file, which is something I often always reach for first. So I did as much removal as I can on all the sanding devices and now I'm just gonna blend everything with the file. And for the finer finish, I'll go to the random orbit sander before I then go to the flat disc.
The random orbit sander can be a little hard to handle on a small knife handle like this. But, you know, creative for me, holding the sander in my lap and then using it upside down is a good way for me to manage that. And the flap disc that Jimmy's using, that flutter sander, is, man, talk about blending your facets together. Ready to be finished, dude? Let's finish.
Or Scandinavian, or- Come on, I'll just go into it. So we're ready for our finish. I see you like to use oil and vinegar. I prefer vinegarette. Balsamic is my favorite.
This is a mix, I've been doing this for a long time. One third linseed oil, one third mineral spirits, one third shellac, one third something else. No, that wouldn't work. Hold on a second. This is one third, one third, one third.
Yeah, and it's, I mean, they're one third by volume. Wonder what high school you went to. They are. We haven't even talked about my chemistry degree yet, have we? So they are, but why they settle out like that, I don't know.
But to be serious, one third boiled linseed oil, one third shellac, one third mineral spirits. I use it on lathe turnings frequently. So shake it up, baby. What one third is this, by the way? I don't know.
Don't hold my feet to the fire on details, details, details. Dries very fast. Beautiful. It's gonna be a little bit glossy. Hit it up?
Hit it. There you go, I'll hit you up. Don't get it on my hand, trying to stay clean. Oh baby, look at that. That's the good stuff right there.
Look at that. Wow. I didn't even realize what color this thing was supposed to be until I see it now. Which reminds me of my dad's workshop. Because of the shellac?
Or was that a- No because of the smell. I know, but, or the linseed oil, also, has such a strong, identifiable- Probably the shellac. I think it's the shellac. This and a little Hank Williams playing in the background, take me right back to 10 years old. Oh we could do that.
Okay, we're gonna let finish dry. Look at how beautiful that looks, wow. It really came out. And then we'll, we're gonna do a, then we're gonna do a knife test. Cut test.
See if this will cut. What do you think? I think they both came out really nice. If this is gonna be a first knife project for somebody at home, you could see how accessible this really is. Yeah, and that accessible word is what I really like about this.
And people end up with old saw blades, like we talked about at the beginning, they don't know what to do with them and not a lot of specialized tools here. Would you like to try yours on the sausage, as you mentioned, I dunno, some time ago. Let's give it a shot. Oh, look at that. We could have spent a little bit more time sharpening them, but it's not bad.
We gotta cut it up for the whole crew. I could have spent more time cleaning mine. I'm leaving a little residue on the cheese. But I'm sure it'll be fine. In the world of things I've ingested in my shop, I think metal grindings are probably pretty low on that.
I'll tell you how it tastes. Is it cheesy? It's Wisconsin cheese, baby. I love the, the blade polish gives it a nice . It's good.
Local? Bought it at the grocery store just five miles up the road. You bet. Yeah. So always buy local.
All right. Parting wisdom for people who wanna do this at home, don't overheat when you're cutting, it's a big deal. Don't necessarily have to quench, right? Not really. But I think the most important thing of all is just give it a try.
Worst thing that can happen is you fail and you just cut into another saw blade. Well, that seems to be everyone's biggest problem is just getting started. Yeah. They talk about it. They worry about it.
Paralysis through analysis. "What if I don't do it right? "What if I break this?" Just get started. You won't know until you do it. And then when you make your first one, your next one will be better.
And then your third one will be better than that one, and so on. That's how you get good at anything. It's a cool project. I think we did a really good job. It's a very accessible project for the average shop guy.
Not too complicated, made from found materials, for the most part. Reduce, reuse, recycle. That's it, yeah. I think, and if we weren't stopping, and talking, and messing around, and talking to cameras- We'd be done quickly. This would go really fast.
Really fast. I mean this is like an afternoon project, easy. A hundred percent, yeah. And I know one of the things you talk about a lot is don't let fear of failure, or whatever else, stop you from experimenting. Yeah.
I mean, clearly, this is, like, metal working, not woodworking, but part of the reason we threw it in to the video is because it's cool. And then, you know, every once in a while, as a woodworker, you might want to make, use this type of technology to make your own scraper, or anything. You know, you might wanna make a scraper that fits an alcove or something specific. So it's all basically the same type of work. And I think the most important thing of any of this is just get started.
So many people get tied up in worrying, "What if, what if, what if, what if?" Just get started. Then you answer all those questions. You have a reference point. Your next project will be better than this one, and the third one will be better than the second one, and so on. And that's how you build your skills.
Yeah, this was fun. How do you like the Wisconsin cheese? It's really good. I love it. All right, knife making.
That was cool. Knife from a saw blade. Success. Success.
This is a great shop guy or shop girl project. 😊
A nice overview on making blades from a sawblade. I have made several Plane (hand plane) irons from old saw blades before. The one thing that surprised me with this video was that they didn't finish the heat treating of the blades. After the quench the blades should have been put into an oven. The temp brought up to 400 degrees F and held there for an hour. Then allow to cool to room temperature. This secondary process keeps the blades from being brittle and lessens the chances of the cracking or chipping if dropped.
A very good overview of making your own knife from a saw blade. In 1981 I made a chef's knife from a big "buzz saw" blade and it is still in use today. While at Stout in the late 70's the Metals Instructor, Hank Thomas had a class that included knife making and we were able to use all of the furnaces and equipment that the metallurgy classes used so we could really control the quality of our knives. Great video! Cal Fischer 1980 Stout grad.