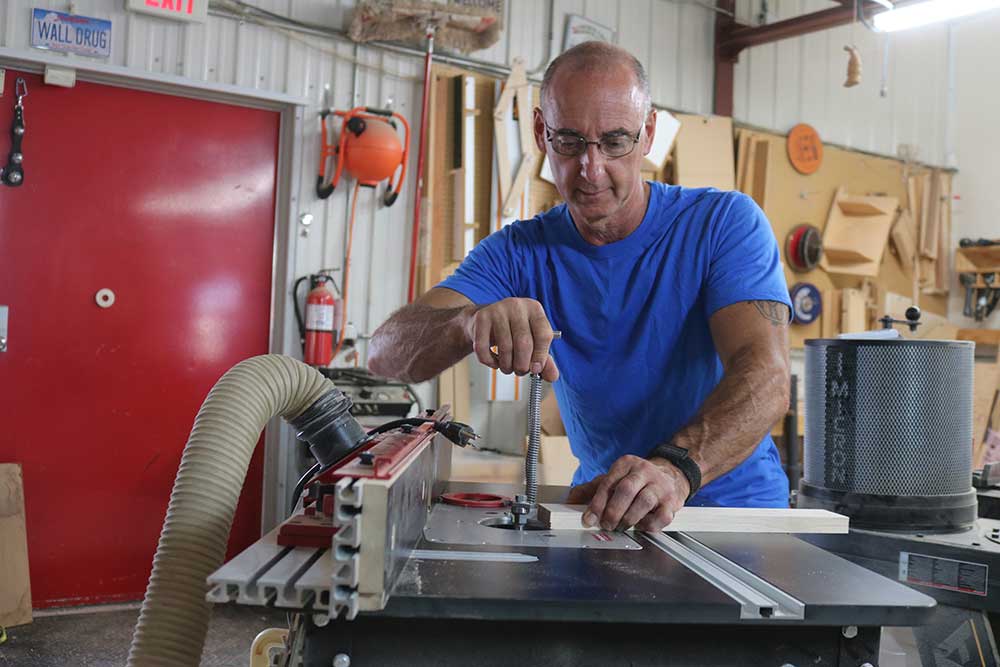
Selecting Table Saw Blades
George VondriskaGeorge Vondriska introduces you to the various types of table saw blades in the line of DeWalt Precision Trim Saw Blades that you can utilize on a table saw for your woodworking projects. He talks about a crosscutting blade with 60-80 teeth in an alternate top bevel pattern that is optimal for end grain and sheet good cuts, a ripping blade with 24-40 teeth with a flat top grind good for ripping stock, and a general purpose 40-tooth blade with an alternating top bevel pattern AND deep gullets that you can use to both rip and crosscut wood.
DeWalt Precision Trim Saw Blade provided by DeWalt. For more information, visit www.dewalt.com.
More videos from Dewalt:
Selecting a Blade for a Slider Miter
There are a lot of blades in the marketplace that you can put on a table saw. But in my experience, we can narrow this down to a selection of three different blades that'll really optimize what your table saw can do. So let's start with crosscutting, and that's gonna take me to this blade right here. Handful of features to point out. One is tooth count.
This is a 60 tooth blade, indicating 60 tooth around the rim of that 10 inch blade. The other thing is the tooth pattern itself. If you looked at this on end, what'd you see is a tooth to my left, tooth to the right, tooth to the left, tooth to the right. That's called an alternating top bevel tooth pattern. What that does for you is it really optimizes the surface finish we can get from the cut.
So this blade, 60 tooth up to an 80 tooth, that's what you'll often see in crosscut with an alternate top bevel does a really nice job of producing a smooth end grain cut and really good cuts in sheet goods. So we can consider this a crosscutting blade, and a sheet stock blade. Really good for veneered materials like plywood. Good cut quality. Now we go to the next blade.
This is a ripping blade. So in the ripping category typically, as we look at this number, we'd be looking at 24 to 40 teeth on rip blade. So when we look up here at the gullets, that's the valley between the teeth, the gullets are quite a bit bigger. What we get from this is a more aggressive cut than we were getting from the crosscut blade. And a good question would be well, if the crosscut blade does so well, if it leaves behind such good cut quality, why don't we use that one all the time?
And the answer is that when you rip a piece of wood, you produce large chips. And I can do a demonstration here to show you, make it real obvious what's happening. When we crosscut wood, like I'm pulling this utility knife across the grain here, you can see there we're getting just these tiny, tiny, tiny shavings. When we rip wood, cutting this direction, look at the big shavings that we get when we go the same direction as the grain. Same thing happens when you're cutting.
So as a result, when we make ripping cuts, we have to have these big gullets, the big valleys between the teeth, in order to carry the chips away. If you try to do a ripping operation with a crosscut blade, you're likely to overheat the blade. If it overheats real badly, it'll distort, and it's no good to you at all. So again, ripping blades 24 to 40 teeth. Commonly, they're a flat top grind on these teeth, meaning as we look at this straight on, that tooth is just plain flat.
Now at the end of my run here, I've got a 40 tooth blade. If you're looking for a blade that you're saying, "I just would like to get one blade on my saw," and instead of a dedicated rip and a dedicated crosscut, want to leave that one blade on there all the time, this would be the way to go. It's got a tooth count that'll let you both rip and crosscut an alternate top bevel tooth pattern. That's gonna go back to providing that really nice quality of cut on the edge of your material. So that's a good general purpose blade for you.
Now another thing that we should point out before we get any of these blades onto the table saw is this whole idea about standard kerf, thin kerf. So here's the deal, kerf is the word for the slot that the saw blade makes through your material. It refers to the amount of waste being taken out every time you make a cut. If we go to a thin kerf blade, what's cool about that is that your saw doesn't have to work as hard to power the blade through the cut. So one thing it's gonna let you do is go to thicker stock without worrying about bogging your saw down when you make those cuts.
So thin kerf is a great way to go. Again, optimizes the power that's available from your saw. Next thing I'm gonna do here, get each of these blades onto my table saw, and that'll be a good opportunity to show you just what kind of cut quality we're talking about from each of these saw blades. I've got the 60 tooth cross cut blade on here, a piece of red oak set up. Let's see what kind of cut we get on the end grain of this oak.
All right, nice and smooth there. In fact, it's pretty darn shiny. Now remember, that 60 tooth blade, that should be dual purpose for us. So we're talking about crosscutting. We're also talking about using that blade for sheet stock like this oak veneered plywood.
So now I'm gonna bring the fence into position. And we'll see how it does on the veneer on this plywood. Remember that with man-made materials we don't want to take this back to the jointer because the glue inside there is abrasive to a jointer. So what that means is that we're relying on the cut quality off of that blade to give us a really good, smooth edge here. So couple things, smooth edge, pretty chip free on that oak veneer.
So those are the two applications for that 60 tooth. Next thing, let's get that 24 tooth rip blade on here, and see how she does on a rip cut. Now, I've got the 24 tooth rip blade in there. I've got a piece of the solid, that same piece of red oak ready to go here. So we'll get the fence positioned, and do a test cut in this red oak.
Now with a nice aggressive rip blade like that, we get a nice, fast cut. Couple of saw marks on here. Doesn't surprise me at all. Trip to the joiner is gonna clean those right up. Now a good question would be could I cut sheet goods, and could I crosscut with my rip blade.
The answer is yes, but it's really not what they're designed to do. You really want to stick to these ripping cuts with these. You wouldn't be real happy with the cut quality you get from a ripping blade on crosscut or sheet goods. Next thing, that general purpose 40 tooth alternate top bevel. And we'll see how that blade does.
Now we can have a look at that 40 tooth alternate top bevel blade crosscut first. Let's see how it does on end grain and red oak. Pretty nice cut quality there. Again, we've got a nice, shiny, burnished surface there, which shows us that that end grain's pretty smooth. Now remember, that 40 tooth is all about having a general purpose blade on the saw so that we don't have to toggle back and forth between dedicated blades.
So let's see how we do now on a rip in the red oak. This is a nice example of what tooth count and tooth geometry can do for you. We went from the 24 tooth rip to a 40 tooth blade here, so our surface finish is a little bit nicer. Plus we went from a flat top grind, to an alternate top bevel here. So real nice edge quality off of that.
Last test, another piece of red oak veneered plywood. Of course on plywood, cutting in the same direction as the grain is easy. Let's see how it does on a crosscut. So again, we're checking on quality of edge cut, chipping across the veneer. Looks pretty good.
So let's wrap this whole thing up. You have a bunch of choices here. One way to go would be dedicated blades, something like a 60 to 80 tooth alternate top bevel. That's gonna handle your crosscut and sheet goods. 24 to 40 tooth, that'd be a dedicated rip blade.
Or something like a 40 tooth alternate top bevel, great general purpose blade you could just leave on the table saw all the time. All of those blades can offer you the benefit of thin kerf so that your saw doesn't have to work as hard when you're pushing material across the blade. So get out there, do some shopping, pick out the blades that are gonna work best for you and your table saw.
What about pitch angle on blades and triple chip grinds? Both are not mentioned in video. Also what do you think of combination blades?
Good eyes Wayne. I played it back and you are correct.
George, on the Red Oak Cross Cut at 8:40 in the video you stack the just cut pcs and show us the edge that was not cut by the 40 tooth blade.