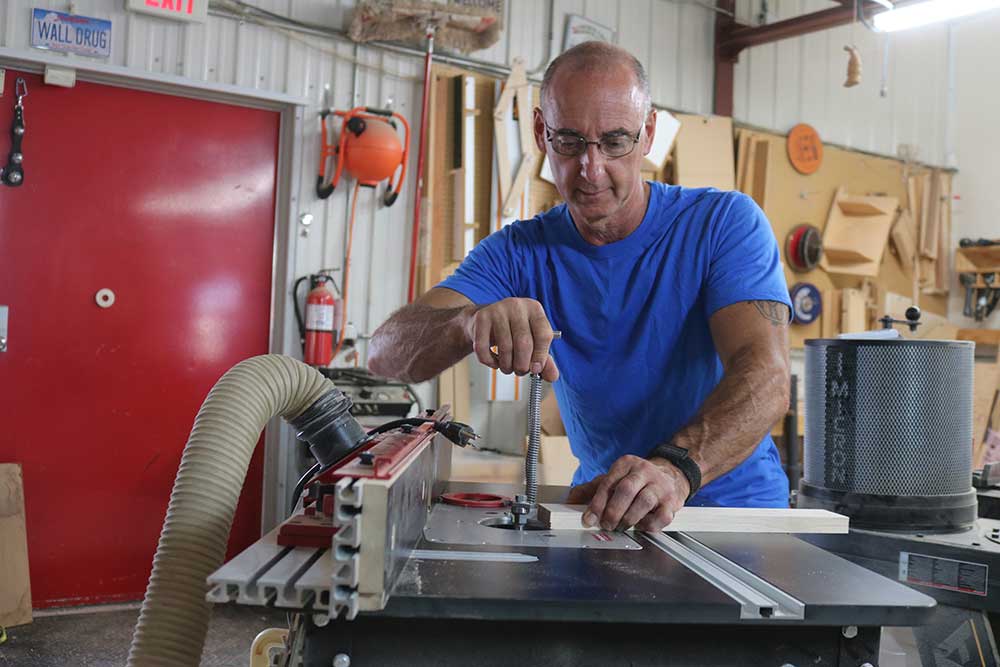
Shopbot Desktop MAX ATC
George VondriskaDescription
What’s an ATC?
ATC stands for automatic tool changer. Instead of the operator manually changing bits for each tool path, the machine does it automatically. The ShopBot Desktop MAX ATC is one of the first CNC routers in its category to add a tool changer. Cool stuff.
How automatic is it?
Once you have the bits installed in the collets (you can use up to six different bits) the software “knows” when to do a tool change, and which tool to grab. Z is set for each bit through an automated function in the control panel and, of course, the XY doesn’t change. So once you push the go button the spindle moves to correct cutter, picks it up and moves off to run the toolpath. Rinse and repeat. When it needs the next bit it automatically returns to the tool dock and grabs it.
What does the system need?
The ShopBot Desktop MAX ATC is a 120-volt tool. You’ll need to connect an air compressor that provides 4 SCFM at 90 psi for the tool changer.
Machine specs
The deck is 24” x 36” with a Z of 3-½”. It includes an air-cooled spindle and cut at up to 4” per second. It uses ER16 collets.
More CNC info
Want to learn to make a project on your CNC? Check out this tutorial that teaches you how to make an oval box with a textured lid.
More info:
For more info on this machine visit the ShopBot website or contact them at (888) 680-4466.
Jimmy and I are at the AWFS show in Las Vegas and let's have a walk through the show and see what amazing stuff we can find to show you. The Desktop Max from Shopbot is not a new tool but there are some features on it that are new and before we get to the features, one of the things that's needed here is the backstory of why Shopbot chose to go in that direction. And, Brian's going to talk about that a little bit first. Well, what we've found is Shopbot Desktop Max has been a huge workhorse in our own production facility. Many of the parts that we use on our other tools are all fabricated using the Desktop Max.
In fact, the Handy Bot, our small portable CNC, is entirely manufactured using just this tool. So, with that in mind we wanted to expand that production capability of the tool and to do that we've added on an automatic tool changer. Part of what this came down to is, you know, you're using it this way so the natural by-product is end users want to have those same capabilities. Exactly. And so, what we've added on is the tool changer that can do six different tools.
So you can use a ball nose bit, v nose bit, a straight bit and all of that can be changed automatically during your cut without you having to change any bits at all. And, this will speed up your production process. It'll allow you to do more detailed cuts and I think that it's going to speed up our production process by a lot. And, I'm looking forward to getting them in use in our shop. And if you've been using a CNC today, and I've been using them a lot, it is going in there and manually changing from cutter to cutter is a thing, you know, you gotta, you got to keep track of when the tool path ends, get the new bid in there, start the next tool path, and you're constantly cycling back and forth.
So, an automatic tool changer is really something you often see only on larger machines, so the addition to this one is great. The other feature on typically bigger machines is? A vacuum hold down. So, like on our larger tools where we offer big blowers that can hold down sheets of material, we now offer a vacuum deck for our Desktop Max and desktop tools. So, you can throw a sheet of plastic on there, a sheet of metal, a sheet of wood, turn on the vacuum, hold it down, do all your cutting without having to bolt it down, jig it up or anything like that.
That's how we do all of our production. They're all general vacuum hold down throw our sheets on and get our parts made. What it's a huge change. It's really a game changer for this machine and exciting news for me. The next step is getting one of these in my shop and I'm going to get the opportunity to mess with it a little bit, right?
Yep. I'm really looking forward to seeing what you make with it. Excellent. It was great hearing about the features of the ATC from Shopbot and now we get the opportunity to run it in my shop which is going to be really exciting. So here's the deal, ATC, automatic tool changer.
One of the things I really like in woodworking is watching industry on a big scale and seeing that stuff trickle down to where mere mortals like us have access to it. This is one of those examples. Tool changers have been present on CNC machines for a really really long time. Present on desktop machines? Not so much.
So what is this all about? What happens is that when we're running a part, a toolpath, whatever it is that we're creating on a CNC machine, it's not uncommon that takes a number of bits to get one job done. Two, three, four, five six different cutters to get the look that we want. In the absence of an automatic tool changer you, I, am the automatic tool changer which is the machine does a tool path, it comes to a stop, I manually change the bit, I re-zero my Z, we go again. Next cutter, next cutter, next cutter rinse and repeat.
Automatic tool changer, It's just what it sounds like. The machine is going to take that operation over for us so that we don't have to manually do those changes. Here's an overview of how this works. There's a bay of sockets on this end of the machine in those sockets are collets. Standard collets like you're probably already familiar with whether you have a CNC or not.
The difference is that on top of the collet this socket will go up into my spindle automatically. It's an air driven system, pressured air. So what'll happen is the spindle will come over grab this whatever spindle it needs whatever bit it needs for that operation. It's going to do that automatically. Once they're loaded, these look like this.
So what we can do, is fill these bays with commonly used cutters and, as we go from toolpath to toolpath, the machine is going to automatically make the changes that it needs to make. I've saved my toolpath onto a flash drive and I'm loading that into the laptop or the FAB, whatever drives your machine, just like I normally would in this case, a laptop. The system knows that I'm about to run a bunch of bits back to back. So within the software I've identified bit number one, two, three, four in my toolpath. When we get to the machine then, what we need to do is zero those bits out, so we can tell the software to pick up a cutter, bring it to a touch plate, do the z-zero, and it'll do that over and over again for each bit we're choosing to use.
Well, what we'll do is we'll start the tool path. The machine will automatically go to bit number one. It'll run that tool path. Once that tool path is complete, it'll cycle over grab bit number two, on and on through the cycles through all the tool paths, until all the work on our project is complete. I'll tell you what.
A CNC is a wonderful shop helper. No matter what it shows up every day, it knows how to read a tape measure, you can go do other stuff while the CNC is running. With the addition of a tool changer, so that, it can just continuously go through every tool path in your work. It's an even better helper. I just am so amazed watching it automatically do those changes.
So that's the deal with an automatic tool changer ATC and really can add a lot of value to your CNC machine.
Share tips, start a discussion or ask other students a question. If you have a question for the instructor, please click here.
Already a member? Sign in
No Responses to “Shopbot Desktop MAX ATC”