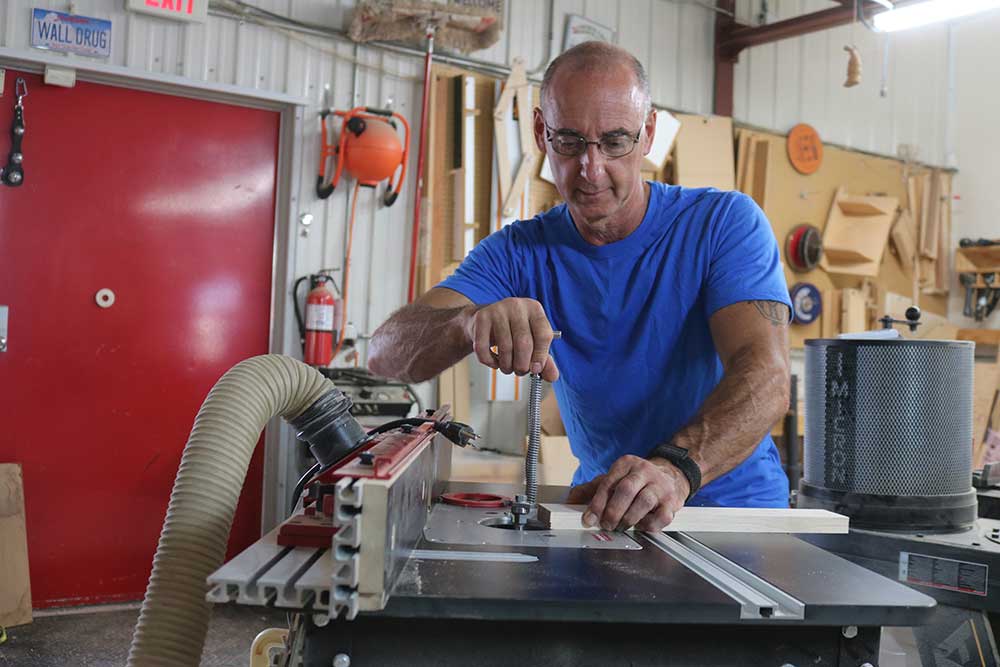
Using a Drum Sander to Sand Complex Profiles
George VondriskaDescription
19-38 Combo Brush/Drum Sander provided by SuperMax. For more information, visit www.supermaxtools.com
More Videos from SuperMax:
Versatility of a Surface Sander
Abrasive Planing and Sanding on the SuperMax Drum Sander
I've got a raised panel door that I put together, and one of the things I need to do after assembly is just a little bit more cleanup with sanding, and this has the opportunity to be kind of a pain 'cause you've got to get into all these nooks and crannies and do your sanding in the bottom of all these profiles. Machines like this can make this a lot easier. Now here's the deal. Looking at this machine, you might figure this is another surface sander that's got a sanding drum in there, but let me show you where it's different. This is pretty cool technology.
It's got fingers in here with abrasive on 'em. I've got one that's out of the machine, so it's easier to see. So here you're looking at the backside. That's the brush. Then on the front of that, there's an abrasive strip.
So you can imagine how this is gonna go. When I run my door through here, this is gonna be able to flex down into the profile, reach right down in there and do that sanding for me, even in complex profiles like this. A couple things going on here that are worth noting. One is that the conveyor itself has variable speed, so we can control the feed rate of the material under the head. Additionally, the head itself is variable speed.
So as we change heads, which is something that we can do with this machine, we're gonna talk more about that in just a little bit, I can also change the RPM to make sure this is dialed into just the right RPM for whatever work we're doing. So here's how this whole thing is gonna come together. Get the head itself turned on, the conveyor turned on. We're gonna feed the door at a diagonal like that. That's gonna facilitate those fingers getting down into these inside corners.
That head, called a flatter head, really did a nice job, even on this open grain red oak, really did a good job of smoothing that out. Now, another application for that same head is something like this. You take that same door and you get a seal coat on it. Next thing we need to do is give that seal coat a light sanding before the top coat goes on. Now what I would normally do then is I would change my abrasive.
I'd go finer. On the machine, the way it works is we take a cap off the end here. This whole array, I'll slide out. The next array with the finer abrasive on it will slide in. Do that all the way around the head.
That's what it takes to change grit. But let's go ahead and run this one through with our existing grit, just to see how that goes. That is very cool how, instead of me taking a piece of sandpaper and doing this to scuff that seal coat all the way around, I can simply send that through. The fingers reach into the profiles. Now to really complete this, what we'd want to do is send it this way.
Don't change the setting. Send it this way. That makes sure it gets everything coming and going, so you get into all the nooks and crannies. Now, just think about it for a second. This isn't the only complex profile that probably goes through your shop.
You've got moldings, you've got trim. Whether you make 'em yourself or you buy 'em, they commonly come with mill marks on 'em. Before you install that, you want to get all the mill marks out. The same deal. We can send those molding pieces through here.
The fingers will reach into the molding, do a nice job of sanding, so all those mill marks go away. Now, let me show you something else that's pretty darn cool. Veneer on plywood gets thinner, it seems like, on a daily basis. So you take a sander to this, it's pretty darn easy to go through the veneer. If we sent it through a conventional drum sander, real easy to go through the veneer 'cause you probably have high and low spots.
If we have a machine like this that'll flex to the profile, we can even send veneered materials, like this plywood, through the flatter sander. Watch this. How's that for cool. Instead of carefully, meticulously hand sanding all these plywood panels to make sure you don't go through the veneer, we can send 'em through the sander. And if you could reach through your television or monitor and do a feeler meter on here, you'd be able to tell just how smooth it made that oak veneer.
So another great application for this head, but we want to save some time here so we can look at other heads on this machine and the other things they can do for ya. I've put a new head on the machine. Now we've got a wire wheel on here. This adds a whole new dimension, literally three-dimensional, to what we're doing here. Changing the head, there's a bearing on this end, there's a bearing on that end, a couple of bolts in each one.
Loosen the bolts. Take those out. Do the head swap. You're good to go. Now, this is gonna do some different work for us.
If you work with barn board or you've wanted to work with barn board, sometimes when it comes into your shop, it's just a mess. A lot of times, the way people clean that up is with a wire brush, whish, whish, whish, whish, whish. We're effectively doing the same thing here, under power. So we can send this material through under that wire wheel. Get it cleaned up and we're sending all the schmutz that comes off up into the dust collector, helping keep your shop nice and clean.
So let's send this one through and have a look at what it looks like on the outfeed side. With the wire wheel set up, think about what's going on here. We've got those stiff fingers, those wires, reaching down into the material here. So there's a lot of variables. We can, of course, change the RPM of the head.
We can change the speed on the conveyor. We can change our depth of penetration. All of that's gonna affect the outcome that we get here. But you can see on this one, already, it's a lot cleaner than it was when it came in. As I feel it, I can really feel the texture difference.
Now, texture difference is what we want to talk about next. All woods have, hardwood and softwood in that one piece, so I'm not talking about different categories of material, but here in the striping of this material, there are parts that are softer than others. So if we run this under the wire wheel, it's a little bit like it's sneaking up on a sandblasting effect. It's gonna kind of leave the hard parts alone. Those bristles are gonna reach down into the softer parts and relieve them from the material, leaving us with a pretty cool three-dimensional effect.
So let's run this one, have a look at what it looks like on the outfeed side. Now if you were standing here in the shop with me and could do this, you'd be able to feel the texture difference that that wire brush created. It's really cool. It's very three-dimensional. You might not be able to feel it and might not be able to quite see it, but let me do something that's gonna help accentuate that color.
I've got another piece of cedar here, and what adding color is gonna do is really make the grain differences pop for us. This cedar is just flat, wasn't wire wheeled at all. So apply a little stain, wipe off a little stain, and we've got just a nice flat surface. On this one that we did wire wheel, it even reacts differently as I'm putting the stain on. And the stain really helps accentuate the three-dimensional effect that we're getting by sending that through the wire wheel.
That's pretty cool stuff. So, combination machines like this are out there in the marketplace. Now, in addition to what I've shown you here today, this will also take a nylon head, which is capable of de-fuzzing, and a conventional sanding drum head that you can put abrasive on so that you can do conventional sanding like you would with any other surface sander. So, a lot of capabilities here can really offer a lot of different things to your shop. You've seen a bunch of 'em happen here today.
It's a machine that's definitely worth checking out for your workshop.
Do you happen to know what other manufacturers make a combination drum sander besides SuperMax?
We are a large cabinet door Refinishing company. Will this machine with the flatter head sand down and possibly off old finish to allow us to reprime and refinish the old doors? Trying to have time and money from orbital and hand sanding!
I noticed that you have Delta controller on a Super Max drum sander. Does Delta make Super Max?