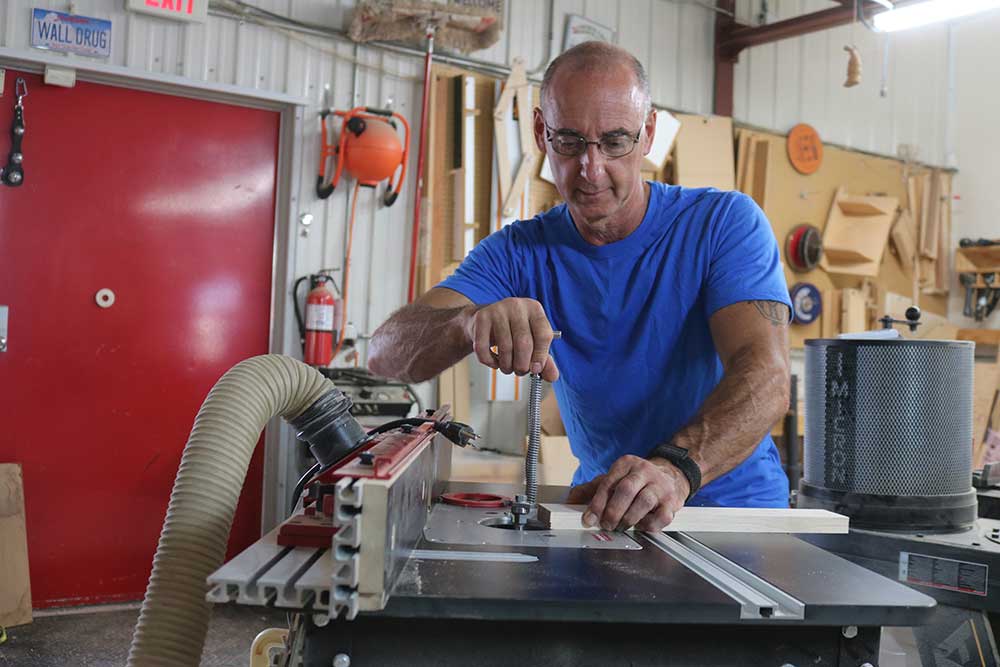
Veneering 101
George VondriskaDescription
Veneering can be intimidating, and many woodworkers shy away from it. However, if you can follow some simple steps, you’ll find that you can produce great results without a lot of trial and error. There are a few key topics covered here to help you get started:
Pick the right substrate. We’ll cover the role of the substrate, and the ideal material to use.
Do the same thing on both sides. One of the mistakes that many first-timers make is to apply veneer to only one side of the substrate, which results in a warped piece. Applying veneer to both sides will reduce the change of problems by stabilizing the panel.
Use the right glue and applicator. There are so many glue choices available today. For the type of application shown here, George recommends this glue and this applicator.
Apply the right pressure. While you might be tempted to apply maximum pressure right away as you apply a veneer, that can lead to problems. We’ll cover the best approach that can apply the veneer so that it lays down flat and stays that way.
After you’ve mastered the art of veneering, use your new skill to make one of your next woodworking projects.
The benefit to getting some mastery of veneering is that you can make MD F look like this Birds Eye Maple figured Walnut Mozambique. So here's what I want to do with this first thing it's important to understand is I am not a huge master of an earring, but I know enough about this to pass it along to you and help you not make some mistakes that I made along the way. One of the things that's really, really important is a substrate. We're gonna talk about that. It's also really important how you apply the veneer.
It's kind of twice as much as you think you need to do. It's gonna make more sense in a second. So substrate MD F medium density fiberboard works really well for veneer because MD F tends to be very, very, very flat and not just flat in this direction, it's flat, but also a flat face veneer is really thin. So if there are knots or whatever in this, and I put a veneer on here and I clamp it in place that stuff can telegraph through the veneer. So having a nice flat plain of a surface on both faces of the MD F is really, really helpful when you're veneering.
The other thing that I learned when I put this chessboard together is that this, what's called figured Mozambique is the name of that specie. The reason that's on the back is in part it looks cool, but mostly because it stabilizes the material. Here's an example of this has a lovely piece of zebra wood on this face. It's got nothing on the back. When you look down it like this, there's this huge bow in this piece and that's because this is, this is just like I say this about finishing all the time.
Whatever you do to one face you gotta do to the other face or the wood is not stable. So same here, if you veneer one face and you don't veneer the other face, then you're likely to get this. So here's what we need to do. Get all our ducks in a row, which is we're gonna do this up on blocks, that's gonna make it easier to clamp. In addition to what we're the substrate that we're using.
We need clamping calls. We need a way once that veneer is on there to get pressure all across the surface and hold everything nice and flat times two because we're doing two faces. So the other part of doing two faces is you gotta do them both. At the same time, you can't glue one face, let it sit overnight, then come back and glue the other face because it's gonna start to react. So we're ready for glue, but we need to talk about glue.
You can do this with just standard off the shelf like type on original, but you're gonna be better off with type on three. And the reason is it's got more solids in it. So one of the things that can happen is that a glue that doesn't have a lot of solids can telegraph through the veneer. And that's gonna show up. Probably when you start to put, finish on.
There are veneer specific glues out there type on makes one that's called Cold Press veneer glue. Um If you don't have, it type on three is really accessible and it offers, like I said, some of the same level of solids and suspension that the Cold Press veneer glue has. So we want a good uniform code of this and I think I'm gonna correct myself. I think I said zebra would, when I picked up that other piece that's also figured Mozambique on that one. It's not zebra with.
I don't want you, you know, pointing my mistakes out to me later in the comments. Just there's our figured Walnut. Now we want to call on here. But if I do this, there's a good chance I'm gonna make a big sandwich out of this. I'm gonna glue everything together.
So we need wax paper first, then the call, then we flip checking my edges to make sure they're aligned and then we just repeat the process some more of that figured Mozambique. So, what I'm doing there, I'm making sure there aren't any little thingies in there. If there's a wood chip and I do this same, that wood chip is gonna telegraph. If there's a wood chip here and I put a call on top, I'm gonna press that chip into the surface and I'm gonna leave a dimple behind. So, cleanliness is good when you're putting all this together.
And I'm intentionally moving fast because look at that veneer already, see how just from that little bit of access to the glue that's soaking up moisture and it's starting to cup a little bit. So I don't want that to get away from me. It's another nice thing about type on three. It's got pretty good open time. So it gives you some opportunity to work here and then clamp clamp clamp.
I'm intentionally being gentle with pressure there because sometimes if from spot number one, if you gorilla grip this and wrench on it, that can make everything shift a little bit. So just enough pressure to hold that in place, get another clamp on there. Now we can do a little more, a little more. Now, we can really snug it down, that's gonna take care of getting that whole thing set up. Give that plenty of opportunity to dry.
We don't have a lot of airflow here because we've got the maner, then the wax paper, then the calls. So what I usually do is let this sit overnight. Then when I open this up where normally in a glue up overnight would be plenty of time to start working with that. In the case of this veneer, I'm gonna let it sit a while longer because I want it to have exposure to open air so it can dry just a little bit more. You probably feel it when tomorrow morning you take that wax paper off, the veneer is still gonna feel a little wet from the glue.
So let that sit a while longer until that goes away. Follow those tips for a veneer recipe and this is gonna be a good start on you doing your first veneer project and getting stuff more right than I did on my first veneer project.
Share tips, start a discussion or ask other students a question. If you have a question for the instructor, please click here.
Already a member? Sign in
No Responses to “Veneering 101”