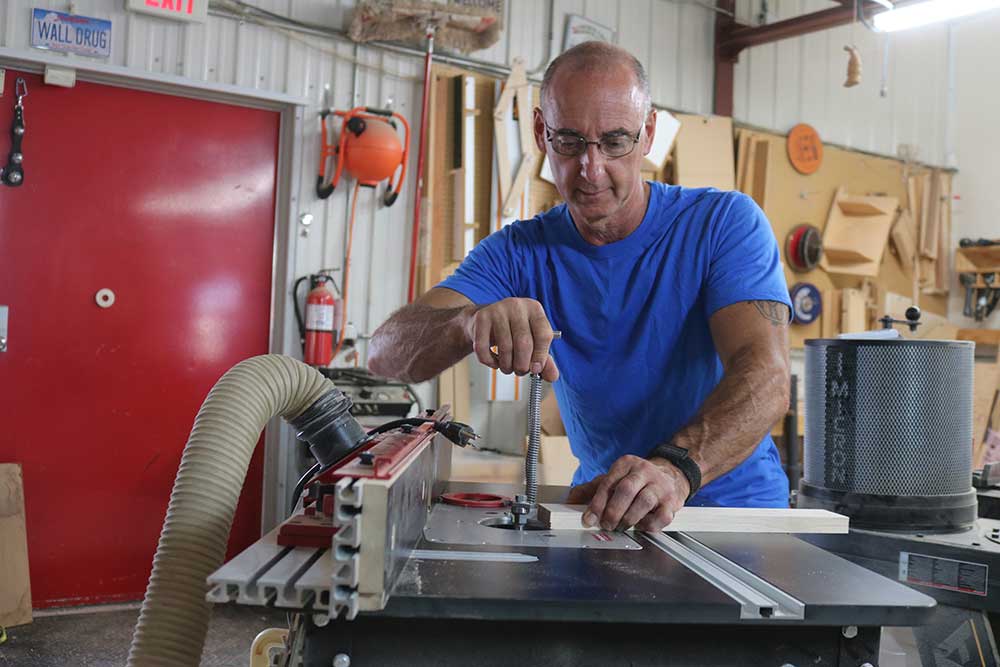
WWGOA LIVE! July 2019
George VondriskaDescription
Special Event – George Vondriska hosted July’s WWGOA LIVE Q&A from the WWGOA headquarters in Minnesota. He was joined by special guest, Charlie Kocourek.
FREE DOWNLOAD: 10 Beautiful Woodworking Projects for the Home
Reference Links:
- Perfect Hinge Mortises on Small Boxes
- Precision Router Base
- Why Do I Need Two Marking Knives?
- Build a Wooden Recipe Box – Great Woodworking Gift Idea
WWGOA LIVE is brought to you by:
Hey, folks. Very happy to sort of virtually see you here today. We're in a new environment. We're doing this live out of a studio rather than my shop. A couple of things are different, of course.
The time is different, more about that in a second. Charlie Kocourek is here. You've seen him do other lives with me and why don't you give us a little of your background, Charlie, in addition to doing other lives for GOA? Well, obviously, I've been doing woodworking for many, many years. I've got my own YouTube channel, Jack Bench Woodworking, I designed adjustable height work bench many years ago.
Which is a very cool product. That's the Jack Bench thing. Yeah, the Jack Bench. So I sell plans for that on my website and I try to stay active in the woodworking community, go out to conferences when I can and meet people and enjoy myself. And you do a lot of stuff, more stuff with veneering than I do, right?
Yeah, I like to do veneering and I do some carving and I wanna get more into more sculptural kind of work. Yeah. Yeah, you stay busy. I do, I do. Charlie and I wanna talk about today is recess, my favorite topic at school.
But no. We would actually wanna do is recess hinges into boxes. That's where we're going with this. So a couple of things. First off, as always with our live sessions, a big thank you to Titebond for underwriting this, which helps keep things free for you.
Also, I'll mention this a couple of times over the time we have here but we've switched times here. That's 11 o'clock in the morning instead of seven o'clock at night. So why don't you, in the comments, you could give us your take on what you prefer. I mean, I guess if you're watching, by default, you're available at 11, right? But let us know until like the 11 o'clock or the seven o'clock p.m.
timeframe better. And then I don't know, should we jump? Sure. You're first. Sure.
So tell us, give us the 10,000-foot view of what your approach is gonna be. So, I've got this box that I made. It's a nice spalted maple box and I'm going to install the hinges on here. And I like to use, I prefer these Brusso hinges for a lot of reasons. Solid brass, right?
They're solid brass. They're machine, they're not stamped. The leaves come together flat without a gap which makes it nicer to install them. Downside is these are really expensive. These are like 30, 35 bucks a pair.
But I do like them. And so that's what I'm gonna do. And when I install the hinges- Let's do, let's jump for just a second, Charlie, and Nate, let's do, you're kind of already there, can you come in? So when I say, we'll get a little camera direction as we go here just to not confuse the audience. But when Charlie says they lay flat, look at that one and then the hinge I'm gonna use is nowhere near as expensive.
This is like a Home Depot hinge. So see the difference there? This is what Charlie's talking about. See the gapicity on this one and how those close. So when I put this one on my box, there's gonna be a little standoff there where it doesn't quite close on the hinge on but Charlie's will get a much better- Well, yeah, and the other option would be if you had this type of hinge to get it to be even close flat, you have to make your mortise deeper than you otherwise would.
But yeah. So I prefer these but they are pretty expensive for just doing a box. I shouldn't say just doing a box 'cause boxes are pretty cool. So, I like to start doing my mortises on the top and that's because later on, we're not gonna get to there but I- The bottom of the top. Well, yes, yes, not the outside, the inside.
And I do that because later on, when I do the other half of the other mortise for the bottom, I use double stick tape and it's just easier to mark it if you start with the top. But we're not gonna get there. And so what I'll do is I'll start off and I'll just mark. Well, first thing I did is I marked with pencil hinge side so when I flip this thing around, I'm not accidentally mortising the wrong side of the box. And so, a couple of things about that.
So I think, let's come back to this. Sure. 'Cause I think we have a cool gee whiz factor here, which is you've got a continuous grain thing going here. In its earlier life, this was one, all the way around, it was a piece of wood, right? Correct.
So then, Charlie built the box and then went back and cut it. If you wanna know just more about just general box-making techniques, when you look at the description for this for this video down at the bottom, let me jump in here and tell you exactly what it's called. So I when I do this, I'm looking at my laptop. We've got a link to build a wooden recipe box. And that's a video just about making a box and that also covers this technique of making it all the integral unit or whatever you wanna call it.
You build the whole box and then you go to the table saw. Is that what you do first? Right, Right. You glue the whole thing up, you glue the whole thing together and then you've got a sealed box you can't open. I put on the table saw and there's a few tricks, techniques when you do that but anyway, basically, you cut the top off of there and then you've got- Continuous grain.
Continuous grain, which is very cool. All of that stuff is covered and you can check that out in the build a box video. So that comes back to when Charlie says mark it so he knows where the hinges go. So that he keeps the front the front, the back the back to maintain that- Right, 'cause otherwise, all that effort to make the grain match and then all of a sudden, it wouldn't although that doesn't look horrible. It still looks better like that.
Cool. All right. Sorry to interrupt. No, no, I'm good, thank you. Back to recess.
So anyways, like I said I start with the top and I mark this because sure enough, I would do it on the wrong side otherwise. And the first thing I wanna do when I'm doing this is to locate sideways on here where the hinges are located. I want it here, I want it here. How far out? And I don't get too fancy with this.
I just eyeball it and say well, what looks good? And also that looks good and I'll take my square and I'll loosen my square up. I'll put it there, I seal that, looks pretty good there. With the square up to it, lock my square down. And then I just use an X-Acto knife, I've got a nice handle.
This is just an X-Acto knife I use for marking that. So I'll put my... Turn this around I'm gonna pull that out and we'll bring it back when we need it. Yeah, so I put my a square on here and just put a little mark there and I'll do the same thing on the opposite side, put a mark there. So a couple of cool lessons out of this one is using the square gives, and I'm gonna do the same thing in a little bit on my setup, gives us uniform relationship to the end of the box.
So that's a good trick rather than maybe you're like me, I feel like the more times I read a ruler, the more opportunities I have to screw up. So instead of measuring from the end, he's using the head of the square as a registration point, marking from the end. So consistent layout. And then you're not using a pencil, you're using a knife. Why is that?
And I'm gonna do the same thing. Well, a knife, there's a couple of reasons. First of all, the knife is a thinner line than a pencil so it's more precise. And the other thing is, when I go to route this out, whether you're using a router or a chisel or doing it by hand, either way, you have a line in the wood that is a stop point. And well, in carving, they call it a stop cut.
So, when you get up to there, you're not blowing out the wood beyond that point. It's more distinct than a pencil. Yes, it's more distinct and you get better, you get a cleaner line. Let me feed you a couple of preguntas, a couple of questions here. Sure.
David says, "What makes the hinge worth 35 bucks a pair?" But I think it kind of talked about that. It's a solid brass. That's one thing. Not brass-coated. Yes, it's solid brass.
I said they're machine, they're not stamped so it's just a smoother better operation and they install nicer. And there's no play in this hinge. Like some of these less expensive hinges, you can feel there's quite a bit of wiggle room in the knuckle which you don't have in Brusso, Brusso? Which is- Brusso is how I pronounce it. Okay, Brusso, just in general, it's a great quality hardware company and this is just one thing they make.
Okay, then. Okay, you're caught up. Hit it. Okay, all right. So I've got the sides marked on this and what I'll do is I will mark, then the depth.
And I use, I have this Veritas nice marking gauge. And I just got this. Just so happens I just bought this one. I had a cheaper one, one of the $6 ones you can get here and there. And the only reason I switched initially is because I dropped the cheap one, I ruined the wheel and I couldn't find a replacement wheel.
Well let's hit on this a second. Just lay her on the box. You can grab it easy and give it a give us a profile. So one of the things that's worth mentioning and I'm gonna use, ironically, the same tool on my stuff. This is a cutting gauge, not at marking gauge.
So the difference is that when you look here, there's a knife like wheel right there. And it's like talking about using this knife to do the layout lines. That's gonna incise, it's gonna cut a line into the surface where a marking gauge with a spur tends to kind of bounce along especially when you're going cross grain. This with cross grain cuts and with parallel to the grain cuts is gonna give us a much crisper line and just a better quality, a better way to go. So now, somebody is gonna correct me.
Yes, you can sharpen the spur on a marking gauge to give it a more knife-like tip but it's still not the same as a cutting gauge. This is worth its weight in gold for the quality of layout line that we're about to go get. Right, and what I was going to say too is with that less expensive one that I used to use, I thought well, it's the same thing, it's just you know. No, it's not. This one actually does cut better than the $6 that I had.
It's the adage you get what you pay for or whatever, what's they always, the thing. Cry once and not, I don't know, whatever. Pay a lot of money up front and then you wouldn't be crying your life about the crappy tool you've bought. And this particular one has a micro adjust on it which is a nice feature. It's definitely not a must have feature but it's a nice feature.
So what I'll do though is I wanna see how far in this one to set this. And what you're looking for is the center of the knuckle, the center of the pin on the hinge. And so, the center of that pin should be, should be centered over the back edge of the box. And so what I'll do is I'll take this gauge and I'll adjust this to there and if anything, you'd wanna err, if you're going to err one way or the other, you'd wanna err to have it further out than further in because if it's too far in, your box won't open, it'll bind. But you shoot for the center and that's just what I'll do here.
So what we'll do is Charlie will get it set and then we'll give you a view of exactly what he's talking about and looking for there. Okay, that looks good. Which part of your bifocals are you looking through? Yeah, exactly. I'm looking over the top, I'm not using them at all.
So let's do, so the folks at home can see what you're talking about. Let's give them a shot. Okay. Wherever we need to position this like this and throw your cutting gauge on there so they can see that alignment against that panel. So if you can see that.
Now, give it a little bit of a turn to the... There we go. There we go. Hit it. So if you can see there, that's where I want that hinge to lay on the back of the box.
And so that's where I'm gonna mark my line. Cool. All right. All right. Just need according to precedent.
So I actually skipped a little bit here. Yeah, Mike is telling us buy once, cry once is what- Ah, buy ones, cry once. I like that. So I said I do this line first, I lied. I wanna have some idea how far to mark this line because I don't want a- A blank scoring Yeah, I don't want it to go too far and it's just sloppy, I think.
So what I do is, again, with a knife rather than a pencil, is I'll put the knife back into that cut and then I'll push the hinge up to the knife and so I know that's exactly- That creates a stop. Right up against there. So then, well, let me turn this around so you guys can see. So I put my knife into that cut and pushed the hinge up against it. And then I come on the other side and I'll make another cut.
And then your squarecity here is coming off of having the plate registered off the edge of the box. Yes. That's how we know that we're running- Correct, correct. Right, I mean it's pretty easy to see that the edge of the hinge is flush with the edge of the box. So that's easy to see.
And let me do a commercial timeout. One of the things that I was asked to remind you of and I forgot, is when you look at your computer screen while you're watching this, in the lower right-hand corner, there's a chat box. If you're fixing to ask us questions, don't use that chat box. That doesn't come here. That's not showing up on my computer, it's going to like customer service or someplace in never never land.
So on your screen right below the video, there's a big blue box and there are a bunch of comments on there already. At the bottom of that, there's a blank space in which you can type, hit the Enter key and then it posts. So that what, now, if you're watching on YouTube, none of this is happening. You're not seeing anyone I'm talking about. If you're watching on goa.com, then type your comments in that blank space, hit Enter and then we'll see it.
So don't use the chat box lower right, use that blue box. If you're on YouTube, I am toggling back and forth between YouTube and goa.com to watch for your questions are. Good to know. Good to know. Okay, so now I've got a mark for each side of that hinge and I've sent my gauge to the depth of the hinge and I'll take the wheel and go across here.
And I like to make a nice, deep cut. Okay, and I don't get it perfect because I didn't have the depth of this perfect. I didn't know exactly how long these lines had to be to begin with. So then I'll come back with my knife and my square. Put my knife back in there 'cause these lines aren't long enough now.
And I can see Exactly how far right that line has to go. And I'll do it again. The same thing on this side. Do that again. And now, double check, make sure that good line there.
That little raggedy. Okay, so now, I've got everything, everything is marked. It's pretty hard to see that, I think, on the screen. So the downside, and we run into this on the video stuff all the time. But it's showing it up good.
The downside to Charlie and I using marking knives instead of a pencil is it's harder for you folks to see what we're doing but at the end of the day, this is a much better technique than laying this out with a pencil that starts looking like a crayon line on your work and it's very hard to where your cut points are. Exactly. Let me hit a question on here. "How do you cut the top off without leaving a cut mark," Douglas says. And I'm assuming you mean like saw marks.
Good quality blade. I use a 42 with alternate top bevel when I do this. Do you know what blade you have in the saw? I'm using a rip blade, a regular rip blade. Okay, and then you're gonna do some cleanup.
You're gonna have saw marks and a little bit of sanding on there is what's gonna take care of that. And a good way to stay on that is lay sandpaper on the top of your table saw to flatten and then you're gonna take this whole lid and just . Right. Because you wanna keep all this in plain. If you hit those with a random orbit sander, it's very likely you're gonna round parts over.
So you won't not have marks. But with a good blade, you shouldn't have a lot of marks and sand, I'm using that approach. Yeah, I use that PSA sandpaper on the tables all the time. Pressure-sensitive adhesive, not public service announcement. Correct though.
Okay, so a couple of things here to get started. Oh, well, we want to secure this and George has got these- I got this modification. Yeah, George has got this well on this side now instead of that side. So George brought in these really cool armor hinges. I mean, not hinges.
I think that's a clamp. I think it's a clamp. Anyway. Go figure. George brought in these cool armor hinge clamps.
No, they're clamps and well, these are great. Put them in here and- Self-adjusting- Self-adjusting, lock it down. And no, that's not a good spot. Move it over a little bit. Still lined in the camera.
But- We're not promoting or selling any of these products but- But it's nice. We're doing the work on a Kreg Mobile Project Center, which I also find, I take this when I teach on the road all the time. It's a very versatile thing. I use it as a bench in my shop quite often but it's a great portable work surface to have. Okay, yeah and like George said, we're not selling these products.
I'm just telling you what the ones that I like the ones, that I happened to use and I prefer. And so speaking of products. Yes. You're about to sort of use a router. Sort of a router.
Talk us through- Well, what I have, what I use for- Lay it on your box and Nate will grab it. Okay, all right. So what I have for... That's a better way to, that's good there. So what I have is a Dremel, a Dremel motor and a lot of times, these are handheld.
You'll see them, you can buy them pretty much anywhere. They're not terribly expensive. And I use this with a StewMac router base. They make a base that screws right onto the Dremel and StewMac is a guitar company, luthier. They sell all sorts of things- Not Protestant?
Correct Luthier? Oh, nevermind. That's a different- Luthier. So anyway, so these, I've been using this particular base for years. It's not terribly expensive.
You can buy a lot more expensive ones but this one, I like it, it's accurate and it's easy to see what you're doing and so I like this a lot. Adjusting it, actually adjusting the depth on it is a little cumbersome. I'm not crazy about the way it adjust but it's such a dream to actually use this. So for any light recess, these small hinges. Well, and for guitar work, it's purfling, it's bindings, I built some guitars.
That's a very handy thing to have. Yeah, any kind of inlays. Kind of neat about it is there's nothing wrong with owning a trim router, a flush trim router. A trim router. But what's neat about this too, of course, is you can pull the Dremel out of there and you could sharpen your Forstner bits with it.
So you can take that same motor and it's pretty versatile to use for other stuff. So everything you're about to do, you could do with a trim router as well. You wouldn't wanna do this probably with a horse and a half router. It would just be too big and cumbersome to handle but- Right, you certainly don't have to buy a dedicated Dremel. I like this but like George said, you could use a regular 1/4-inch a trim router and that would be fine too.
So the next thing I would have to do though in this process is to set the depth of the bit on here. And you're currently unplugified. I am unplugified. Well. Fixing to be unplugified.
Now, I'm unplugified. Yeah, that's what we have. So this base has a nice, I don't know if it's machine. It looks like a machine anyways. It's nice and flat and I put this on here and it's not quite flush.
It's easy to feel when it's flushed so I'll loosen up the locks and let me see. Is it your goal to make it perfect? Yes. Okay. Yeah, that is my goal.
I want this to be a perfectly flush. So it's interesting, just if you are interested, Charlie. I'm always interested in this. People are watching from Houston, North Carolina, South Africa which- South Africa. is always interesting to me because I lived there for three years.
I'm scrolling to see if anybody else. Washington, Lake Stevens, Washington. Do you remember the show "Romper Room", you'll be watching- Oh, yeah, yeah. This stuff always reminds me of like at the end, she'd look in the magic mirror and I see David in Lake Stevens. I see Billy in Lake Stevens and whatever.
All right. Stupid cultural reference. Well, yeah. All right, anyway. So, anyway, so now I've got the depth set to the exact thickness of the leafs, leaves, leafs on the hinges.
And so, another cool thing about this StewMac base is you can, it's got a fitting on here that you can hook a hose up and they sell or you can buy it anywhere I suppose but they sell, it's actually an aquarium- Aquarium pump. An aquarium air pump for irrigating aquariums and what it does, you plug it in and it shoots a little puff of air and blows the dust away as you're routing. So otherwise, I would constantly be going, like that. And with this, I shouldn't have to. So, this thing doesn't have a switch on at the pump.
So let's do one thing before you, 'cause we're close to making noise. We're working under studio lights here which you may or may not have in your shot. So the place is very well-lit but show them your light set up 'cause for people who don't have studio lights- Yeah, we happen to be in a studio, the lighting here is outstanding and I shouldn't have any trouble. I think we're getting, our tans are improving. But when I'm at home, I've got to set up and I use, I've got one of these little portable LED lights.
I got this on Amazon. It's about, I don't know 40 bucks, something like that, 40, 50 bucks. And the nice thing about this is it's not tied to a cord. You can get nice led lamps that are courted and that's great but when I'm in my shop in the bench, I'm constantly moving this thing around back and forth here and there, repositioning it and with a cord, it seems like I'm always tripping over it. And so I use this to get a good lighting because it doesn't matter how accurate my lines are, if I can't see them perfectly clearly, then it's a waste.
It's a good form of task lighting. Yeah, good task lighting. It's so important for accuracy. And this is even, maybe just said this, this one is LED. LED battery-operated.
Led battery. Yeah, and then what I do also, I've got, I got a lot of tripods in my shop but I have this tripod here and I just mounted a piece of plywood on it and so, if I wanted to... If I don't always want my lamp on the bench. Sometimes, I needed out here. So I'll just take this and I'll set it out here like this and I'll just- Just tick it on so we could see how bright.
I'll turn it on quickly. And so while that blows out the light but in the camera but as far as being able to see on the work, it's outstanding. So anyway, that's what I do. So happens in this facility right here, I don't need it. In my shop, I do.
So, Ohio, Russia and South Carolina joined us, and Toronto. Oh, well, thank you, yeah. Hey, is there a brand name in Tejas, New York and Nashville. I got to get to Nashville. Is there a brand name on that LED lights?
I don't know if there is or not. This is called a Tacklife but there's dozens of them on Amazon. Google knows. Yeah, Google knows. Google LED battery-operated light.
Yeah, yeah. I just go by the reviews on Amazon. More stars, more likely I'm gonna buy it. So anyway, like I was going to say. So I've got this air pump.
And so I'll plug that in and like I mentioned, it doesn't have a switch so it goes on immediately, starts making noise and then I'll plug in my router. So it's pretty, grab us, Nate, if you would. There's a port here. No, no, no, no, no. I got to find just the right.
There it is. There it is. That hole is where that air is exhausting out right now. So I like that. That's a pretty neat feature to keep your work area clear.
Yeah, it's nice. So getting my eye protection on. And ah, here it is. And what it looks like an 1/8-inch bit. This is an 1/8-inch, yes.
And 1/8-inch is just right for doing these little hinges. And it's the smaller the cutter, the more better because then you're gonna be able to get closer to the inside corners. If we were doing this I mean a 1/4-inch but it wouldn't be practical in a Dremel anyway but if you had a big router bit, just think of the diameter of the cutter, the radius of the cutter. We could only get so close to the corner, you're gonna have that much more work to do. We can't get that router but to cut square corners yet.
That technology, maybe it's common but I don't know. You never know. So everything has got to get squared off with the chisel after. So smaller bit, better control and then you can get closer to the corners. Yeah, yeah.
So, I will just get started here. Just give Nate, there we go. Okay. So, Nate, can I talk over it. Can you hear me okay?
Okay. So, I'll kinda voiceover with Charlie's doing here. It's important to understand that what Charlie's doing here is not cutting to the line. You're just trying to do like broad brush cuts here and eliminate, I don't know, 90% of the waste and final work to the line is gonna done with a hand chisel. So this is detail work but it's not uber detail.
Like I said, he's not he's not trying to hit right to that score line that he put on the work. How do you feel about that? It looks pretty good. So whilst you were speaking, I was saying you're not trying to get to the line. You're gonna do that with a chisel.
You're leaving some waste there. Right, correct. Then it's pretty neat, we can check Charlie's work to some extent. Oops. By laying the chisel in here.
I think that's a hinge, not a chisel. Yeah. Laying the hinge in here and seeing if he has flushicity across the top. It wouldn't be a bad idea to do this in a piece of scrap before you come to your, Charlie's done this a billion times. So he set the depth, came to the box.
How'd I do, George? Is perfect okay? Perfect is okay. Okay. It would be a good insurance policy to make a similar cut and a piece of scrap.
Check this to make sure that your depth is right before you come to your heirloom box. Mm-hm, yes, yeah, yeah. All right, if you were you, what would you do next? If I were me? Next thing I would do is I would take my chisel and I would clean up these to the line.
Would you like to do that, sir? How about I do that now? All right. And with my eyes, I see better up close without the glasses. Wow.
And I don't use a mallet or anything for this. I just do it by hand. This is a hard maple but even with hard maple, I can do this without- You're really just paring at this point. Yeah, it's not very heavy work. Let me give you a, William says, "Dremel also sells a fan blower attachment that fits on the tool so no tubes.
That does a good job of clearing sawdust." Well that should probably be a good, that would be cool, I haven't seen them. And then John says, "Why not use a small router plane, inexpensive portable and the mortises would already be done. Small Veritas would be perfect." I don't know 'cause it's not a right or wrong. It's just this works for you, I'm gonna cut with hand chisels and maybe Spagnolo would do this with a router plane, I don't know. It's just different strokes for different folks.
Yeah. One of the cool things about woodworking there's eleventy billion ways to do every- How many? Eleventy billion. Wow, cool. And all you have to do is read, nevermind.
So now, Maine and Florida have jumped in. Very cool. Eric thinks that air pump is a brilliant idea. So do I. It's pretty neat.
So a little what, maybe, if you zoom out just a little, Nate, can you get just kind of see Charlie lean in over the chisel like that? If you can back out that much. 'Cause it's just kind of the overall body mechanics here to make this work, I think, are interesting. Because he's not using a chisel. So when he does his- I am using a chisel.
I mean he's not using a mallet. Doing this with an absence of mallet. See how he gets his, he's getting his body weight over the chisel and just pushing down and that's why he doesn't have to, that's why he doesn't have to use a mallet. And I'm guessing the chisel is sharp. Yes, yes chisel was sharp.
When I'm paring, I don't even pare right up to the line initially. I get as close as I can without going to the line 'cause it's easy to go past it. Somebody asked earlier, no segue from what you just said. Are these events archived? And yes, they are.
So I asked about the timeframe which led to somebody asking him about the archive. All of these lives are archived. And if you go upper left-hand corner at wwgoa.com, there's a menu up there. One of the menus is, I'm gonna go look to make sure I get it right. Videos, WWGOA Live and everything is archived under that heading.
Every live we have ever done and it's, I don't know. We're in year something, three, four of doing live streams, so. We were country before country was cool. That's us. All right, I'm getting close.
But I'm gonna talk about this too. Charlie's cutting bevel down. I'm gonna do my work with just a hand chisel and the relationship of the bevel of the chisel to the work is an important part of this. Bevel is in toward the waist side when he's doing that plum, the vertical paring cut. And then when he's doing, when he's trying to just skin waste out of there now, the bevel is down, gives you better control, I think.
And I won't be surprised if when I'm done, when I think I'm done here that I'm not and I'll test it and I might have to make some adjustments with the chisel before I have it completely done. That whole aspect of putting wood back in, we haven't quite mastered. No that's a little- Better to be conservative on taking it outside. There are ways to rip it, there's always ways to fix it but that's another event. And I would say, this is a race that goes to the slow and steady, not the fast 'cause you just wanna, I mean think about how far you are in this box at this point.
Don't screw it up now. Yeah, he just want to take out a little bit of material, do a check, be patient. This is something pediatricians would not be good at. They have very little patients. Let me see- Get it?
Get it? Come on, give me a little chortle. I'm slow, George. I'm really slow. You're just concentrating on your- And I'm getting slower.
You're concentrating on your work so much. Okay, it's a little tight that way. I think this line, I didn't quite get to this line. I can just see that. It's just a, it's not even a sliver but I want it, I want perfect fit.
I don't want any slop in there. See how this looks now. There we go. Oh, that looks like a nice slip in. Just move your pinkies back a little so Nate, there you go.
Okay, and I'm not quite there on the, on these corners. Left to right, you're happy. Yeah, left to right but depth, I'm not quite there. I got to clean up a little bit on these ends to get it clean. And part of what I think is important to watch out for here is he either gotta be plum or slightly undercut this way.
Slightly under cut into the box. You wanna make sure that the top surface here is meeting the edge of the hinge. Right, right. And you wouldn't want that angle to go the other way where it's hitting the bottom of the recess before it hits the top of the recess. Yeah, a little undercut on there is not a problem and you don't want a dig anything drastic but a little bit is not gonna be a problem.
So let me catch up here. Couldn't you use a square chisel on a drill press for this procedure. So like a mortise chisel on a drill press wouldn't really give us what we need here there. Those weren't great for doing mortise. Well, they're okay on a drill press for doing mortises, they're better on a mortise machine for doing mortises.
But they're really designed for going deep, not just the little, we're maybe an 1/8-inch deep here and a mortise chisel wouldn't really be effective for that. John says he would make a jig for a perfect fit which would... If I was doing a bunch of these, I'd maybe make a jig. Well, what I would do is put it on my CNC machine 'cause I like to cheat that way or I'd make a jig that a pattern bit could follow and then- Actually to that point, Brusso, I think they sell templates for their hinges. So if you wanted to do that, I think they actually sell templates.
Okay. I've never used them, I've never bought them but I have seen them on their site. And on a onesy twosy basis, I would do this, I would do exactly what Charlie's doing. But if I were doing a lot of boxes, I'd take the time to jig it. So I'm pretty happy with that.
Let me hold. Yeah, no. Take it off the clamp and see if I can get the camera to- Show your good work. Show my good work. Oh, cut my finger.
All right, it's not screwed in there but- But it's not screwed up either. And it's not screwed up. And you see, this is spalted maple and spalted maple has got, it's hard maple but it's spalt maple and so there are some release soft punky areas and if you see right here, the wood is a little darker right here and that was one of the areas is punky. And so when I when I drew my line, I got a little bit of a rough cut and so that's why that isn't absolutely perfect but I'm quite happy with it. No, it looks good.
And it'd be pleased, and Rico says, "What a great fit." Oh, thank you, Rico. So let me revisit a couple of things and then we'll look at chisels on this other box. Sure. One, well, if you're wondering why Charlie and I keep doing this, that's because there's a monitor right here. So we need to see what you see so that we know we're getting everything right.
That's why we keep looking down. Two, big thank you to Titebond for sponsoring these live events which keeps them free for you. So thanks Titebond for that. Three, if you're watching this on wwgoa.com and you wanna communicate with us, there's a box in the lower right-hand corner of the screen that says chat. Don't use that.
That goes to customer service and then like Paul Meyer and I get questions, we see those later, we answer those questions. If you wanna be communicating with us live, on that main screen for wwgoa.com, right under the video, there's a big blue box and at the bottom of that blue box, there's a blank box and if you type in there and hit the Enter key, it'll post your question and then we'll see it. If you're watching on YouTube, I am toggling back and forth between the tabs to see. Braxton is watching. Braxton.
He says, "Great job, Charlie." My bud! Hey, Braxton. Viva Las Vegas, we're all gonna be there. Yeah. We.
Are you going this year? No, no. So let me just look at a couple of questions here and make sure we're caught up and then I'll bring that stuff up. Chief something, says, I've enjoyed learning a lot from you, especially proper gluing techniques. So that's good.
Thank you. Yeah. Annapolis, Maryland, Joplin, Missouri, something in ciroic, or no, what's Russian writing called? I can't read it. Okay.
All right. Clear the decks. Clear the decks. All right, so here's my deal. To provide just a little bit different look, I'm gonna do everything with a hand chisel.
Ooh! My box is walnut, approach was the same at the starting point which was this box was made as one big piece. And then went to the table saw, cut the lid off just like we already talked about. I'm gonna move fast on some of this 'cause Charlie has already talked about it and we have some overlap on our technique. Starting with setting the distance in from the outside.
You've already seen Charlie do this. I prefer to do it with a layout tool than a pencil. I'm using a marking knife. Let's hit on this for just a second. I've got two marking knives here.
The difference to your- Square? I got it. The difference between marking knives and utility knife is when I do this and this and this. This will be like a great challenge just 'cause it will be hard to actually see this in detail. The marking knives are beveled one face flat on the back.
A utility blade is beveled both faces. So what Charlie was doing when he used this utility knife was making a point of getting that bevel against the layout tool or against the hinge. With a marking knife, because it's got a flat face, when I do this, it gives me the opportunity to very accurately trace that edge 'cause it's flat on the side. So two marking knives 'cause you generally need a left and a right. And if you look down in the description of the video, we've got a link for more information on the benefits of why we need a left and a right marking knife.
However, that being said, layout tool. So things are consistent. Trace it. And all the same reasons Charlie talked about, that gives me a nice crisp line rather than doing this with a pencil. Easiest way to find the other side is to get the chisel on here.
Now, watch, I'm gonna switch marking knives 'cause this one's flat that side. So just like Charlie said, if I put that in the incised line, slide until I kiss it, now, I have to go back to marking knife number one 'cause that's flat on the left side. Trace. Now, if you wanna make this uber simple, one way to do this is to simply fold the hinge onto that edge and trace here. So what Charlie did is he kept that knuckle centered, which we put it in here.
Part of this is so that I can do a recess and not go all the way through because I wanna show you how to do a recess. I'm gonna fold it and the whole knuckle is gonna be on the outside of the box like that. And then like this. And when I'm doing this, when I'm tracing like this, my first pass is light and then I'll push progressively harder once I've got that first path created. Any questions there, Charlie?
Yeah, yeah. Let me see. Michael asked if we could just use a corner. A corner chisel, I think, he means and knock those, hitting it up like that. Yeah, so I almost brought a cornering chisel but at the scale of it is way too big for what we're doing here.
It's really designed for hinges, I'm pointing to a door. Hinges on a door mortising, more so than the scale. And I don't know if they make those in a way, way smaller scale. I don't think they do and the, I prefer using just the straight chisel than a corner chisel. One of the reasons is because corner chisels are kind of hard to sharpen.
You gotta be pretty good with sharpening. I mean I can do it, there's no doubt about it. But it it's really so easy and I can get just as accurate with a flat chisel as I could with the corner chisel. And I'm just happy- And part of what predicates the use of the coroner chisel is that, again, it's typically a passage door or an entry door and there are jigs, Porter-Cable makes one that are specifically like entry door hinge routing jigs. So when you route that, you're routing to a template.
And the length of mortise you've routed and the depth of mortise you've routed are perfect. It's just that you've got round corners instead of square corners. So that squaring chisel can go right up against those cut edges and you snap it down and you're finished. With Charlie's approach here of doing that free hand route and cutting to the line, you still got to go in there with the chisel 'cause you got to get back to the line which you would have to do before the corner chisel went in there anyway. So it's just in this application, it's not really the right tool for the job.
That's a good point about that corner chisel there. Mortising hinges on an entry door or a passage door would be good. Down to New Orleans, says hello. John says, "Paul Sellers has got a lot of good articles on using a router plane." Yeah, Paul Sellers is a great guy. I like his stuff.
Nick, RSA, he likes what we're doing here. And Kevin says, "You can pinch the wings of the hinge in a vice to get them close tighter." Oh, okay, yeah. That could work. You could modify. I suppose you could.
I can see that. I suppose you could. And quick tip I've found from using the marking knife. I think he means he likes what you said. Oh, okay.
Now, depth to cut. Now, we're gonna do is I'm gonna use a cutting gauge just like Charlie did because I wanted to be just like Charlie when I grow up. I'm setting that to the thickness of the leaf. So cutting wheel on the marking gauge and the cutting gauge. Setting that to the thickness of the leaf.
Let me get it, and then I'll show you again. Here we go. That in turn then gets transferred to the box where I had my layout. Now just like Charlie did, I need to know where to stop and where to start. So, gonna use my square.
And I'm gonna get into that incised cut. So as I come along, I can feel right there, the marking knife drop into it. Bring the square to that point. Just make a little downward stroke. Feel the knife drop into that cut.
Again, it's another, like Charlie mentioned, it's another benefit of doing this with a marking knife is now you can use that, you can create those stopping points like that. Now, there's two lines on there. Probably difficult for you to see but I can see them pretty clearly. I'm gonna drag. It's kind of a drag.
And give myself depth. The complete layout then is thickness of the leaf, it's there. And then the size of the hinge at rectangle there on the top of the box or the bottom of the top. All right, a little bit of clampicity. Gonna try to leave this on your side so it's easy for you to see.
So, what he was saying, that last Dinrat is what he was trying to say about the marking knife is the bevel gets wider, the deeper you go so if you start with the appropriate knife to start the line then remove the piece and switch to the opposite bevel, you don't create a larger mortise. And that's- Okay. Yeah. Sure, I buy that. Now, here's what I'm gonna do.
I am gonna use a mallet. Okay. And what I wanna do is just give these lines a little bit more definition. And this is where, again, having the cut lines on here, the marking knife lines. See if you can hear this.
A little click. When I'm pulling the chisel back, that's the tip of the chisel falling into that marking knife line. That tells me that that's where that chisel needs to go. Bevel is on the waste side. Flat is on the keeper side.
Little rappy-tappy-tap-tap. Finish it to the corner. And you don't wanna go crazy with this because we are driving a wedge into this. And if I go deeper than I need to, it's possible that it's pushing the back of the chisel too far into the keeper side. Similar to the point that Dinrat made.
Yep. And then big long line across the back. So I'm gonna go, I think I have a wider, yeah. I'm gonna go to a wider chisel. Let it fall into that cut line.
Beautiful chisels by the way. They are pretty nice. I got these when I started doing guitars. These are Lie-Nielsen chisels. Those are nice.
And there's so much detail work on guitars that you need good chisels for. Let's just then click on the YouTube and see if there's anything there we got to pick up. Okay. How far were you before? It was Braxton.
Oh, yeah, I'm sure it is hot down there, Braxton. I'll find out next week. Sizing is fine. How do you recover if you go a little too deep? That's a good question.
If you're doing a little too deep, then you can fill it in with, I don't know, put a piece of paper in there, a little- A little bit of veneer. Preferably, yes, I was gonna say a little piece of veneer is probably best. There are always ways that you can repair your mistakes. Well almost always. It's amazing with as many mistakes as I've made over the years, I've gotten pretty good at fixing them.
So yes, a little piece of veneer under there, a little sliver of something. You can fix it. I think we're set. Okay. All right.
With the chisel now, like Charlie, I'm not gonna use a mallet and bevel is down. A little bit of pressure from my thumb. I'm really just wiggling, I'm carving, I'm paring away at this. We'll see if the walnut lets me do this without a mallet. And what we want right there, I hit that distinct stopping point, which is the spot where I had tapped the chiseled down in there just a little bit deeper.
Little overshot. And one of the things I'm doing, see that wiggle? Of the chisel, not me, is that's helping me kind of walk this forward so that I'm not trying to do a full width pass all at one time. When I do this and then this and then this and then this, that's helping me get that little paring go on. And of course, all we have to do is I'm starting in about the middle and going in this direction.
And I try to get that end finished. There. Then at some point, gonna get this going this way. So we got to work from the center out. Here, I think I have a little bit sharper chisel now than I had in that bigger one.
That's the peel I'm looking for. Yeah, it looks like it's working a little better. And this is just gonna be a case of kind of rinse and repeat. I'm gonna very carefully work. Now see how a fair bit of pressure here but when I get close to that end, I'm really backing off on my pressure because if this just goes bloo!
I'm gonna take a big skin off right there. And I don't wanna do that. There, this is what that deeper cut is letting us do. See how that just flakes up right at that stop point. Pressing down pretty good with my left thumb, I'm dominant right hand.
Stupidly dominant right hand. So I'm pushing on the chisel with my right hand, down pressure with my left thumb. We have a little bit of a recess there. And just frequent checks and we're looking for flush so I've got a ways to go. Anything?
Comment about you're wiggling, I think, from Jim. Similar to the angle cut you would make for a knife before sawing. Would you advise same for help avoiding the overshoot I just saw? Use a sharp chisel right from the start would help the overshoot you just saw. Yes.
I grabbed all of these chisels and thought they were all in good shape but that one was a little duller than I wanted. So gone way more better with this one. All right, so I'm gonna keep doing this but it's gonna get boring 'cause we're just doing more and more and more of the same. What else, Charlie? Any other hinge recess information you wanna pass along or other questions we wanna grab?
Ah, well, we got a question here. What type of wood was the bottom of the first box? That was some spalted maple that I was able to find locally here in Minneapolis. And it's beautiful. Really glad that I got some of that.
It was a nice piece. Yeah. What else could we be talking about? Well. As far as for hinge, mortises.
One thing I'll mention about those Brusso hinges and this is, I said, we're not trying to sell these and I'll tell you why. Well, not why but I'll tell you one thing. As expensive as they are, the screws that they provide with them, I don't like and I don't use them. I actually go and I buy screws separately to use with those hinges. It blows my mind that they give these uber fabulously high quality hinges and they give you these cheap Phillips head screws.
So what is it you've run into why? Well, they're smaller. They're a small shank and their Phillips head. And this gets into, this gets into some of the ridiculous, really, but the traditional way is to use a slotted head screw for your hardware on boxes and- Why is that? Really?
Yeah, oh, absolutely. Oh, absolutely. And if you get into trying to show your work at shows or any competitions, the judges, many, many, many of the judges will ding you for using Phillips head screws as opposed to slotted screws. So they don't know any cordless tools? Apparently not.
Well, it gets even more ridiculous than that. Some of the judges will ding you if the slotted head screws aren't, if you don't clock the screw heads, which if you don't what clocking the screw heads in means, what that means is the direction that the slots on the screws are all perfectly lined in the same direction so they all be, for example, parallel with the back of the box. Well, I will confess when I do electrical work, I make a point of making all of the slots on boxes vertical when I put electrical box, when I put cover plates, face plates on electrical boxes, so. I guess if they're wrapping you for slotted instead of Phillips, the fact that the directions aren't all the same is not much of a surprise. Yeah, so it's just sort of a trivia question for most people and for a few people, if you're actually out in competitions showing your work and exhibitions or shows, yeah, yeah, some people really take that seriously.
All right I'm pretty good on the one end. Tell me what kind of clamp you're using. So this is an Armor, A-R-M-O-R, self-adjusting clamp. And they make a number and this is their backstop as well. Is in the 3/4 dog holes and the clamp is in the 3/4 dog holes, so.
I really liked these clamps. They're nice. Well, I did count how many I brought. So if I'm missing anything when I leave, I'm gonna know. Just, I'm telling you.
Well, whatever you counted is wrong, George. Everybody knows you can't count. I use my toes. All right. Fernando in Arizona, he says, he's liking what we're doing here.
Good. All right, why don't you hit back to- And hi from Phil in the UK. Go back to the other site. All right. So flush across the top, where we wanna be.
Yes, it is some nice walnut, maples, he likes that walnut. Are the slots on the old screws narrower than the slots in the new screws? I can't say. I can't say. Maybe.
Bottom line, that recess is done. Let me I'll flip around, Nate, and then we'll come off of that. I got to keep a finger on it or it falls out of there. Watch across the top in the recess. Net-net, what this exercise does is it shows us that you don't have to have a router, you don't have to have the Dremel base.
You can do this all with hand tools. In the real world, if I were doing this in my shop, I'd be doing it exactly the same way Charlie just did. I would rough it out with a router and then I'd come back and finish it with a hand chisel and that would get me more consistent results. Again, there's eleventy billion ways to do stuff. So what works for one person doesn't make it imperative for everybody.
This is one way to do hinges, this is one way to do hinges and everybody else has- Yeah. Some people really liked to do things by hand and I get it, I get it. You got the noise, you got the dust from power tools and there's a certain satisfaction from doing it by hand, that tactile feeling of doing it. I get it. But like George, I get more consistent, cleaner results using the power tools and that's my first choice.
All right. Yeah. Hit us on the main page one more time. All right, see how it works. We're about wrapping up here.
So if you've got any last- I got it. With the hinge installation, are you, do you lay the hinge on both pieces to line them up or do you do this freehand also? Ah, you're talking about the top and the bottom. I don't do that free hand. What I would do is I would have, is that square still here?
Anyway, I would take the square, the same. So I would- He used to lay it out on the first go around. So for the bottom of my box, I would take the same square. This happened to be George's but I would I would mark the sides the same way as I did to begin with. And I'd put the hinge on and mark the sides again the same way did on the top.
Well. Yeah. Two ways of doing it. I'm thinking of different boxes. With a square box like this, I would do it just what I just said.
I would mark it the same and I would cut it the same. I've done other boxes that are elliptical or odd-shaped and in that case, you say it's hard to do it that way. And in that case, I will use a double face tape and I'll put, I'll install the hinge on the one side and I'll use and I'll put double face tape on it. In the approximate hinge location. Is that what you're doing?
You're picking up the hinge. No, it's exact. So what I do is... Let me get this other side. And you could do it with a square box.
I was thinking something different earlier 'cause I just did an elliptical box. But I would actually install the hinges on the top here. I would actually install the hinges, screw them in. And then I would put double face tape on the face of 'em and then I would line the box up perfectly the way I want it. Press that tape down as hard as I could and then what I would do is I would very carefully open that box up without disturbing the tape and I would mark the other side.
And like I said, that is if I have an odd-shaped box or something. On a square box like this- It would work here but it's not- It would work but it's not- Not necessary. It's not necessary. You can get perfectly great accuracy using your marking tools, your layout tools. Okay, that's a good, the double faced tape on a hinge leaf is a great idea.
Yeah. Yeah, and it works well. All right. Let's check the other site here. Back to GOA.
I think we're there. Very good. All right. Well, again, thanks to Titebond for underwriting this and keeping us going. Thanks to you for coming in.
Hey, thanks for having me here, George. It was a approach and I love that little StewMac base I haven't heard. Might be one in my future. Maybe, huh, maybe. Yeah, they're nice.
And thanks to you, folks, for tuning in and we- Phillips head screws did not exist in the 1930s. Yeah. How did they build cars at the Ford factory? No, they weren't, nevermind. All right.
Go ahead, George. All right. Thanks, folks, for tuning in and we will see you whenever this happens next. Yeah, thanks a lot.
Phillips head screws did not exist until the early 1930s