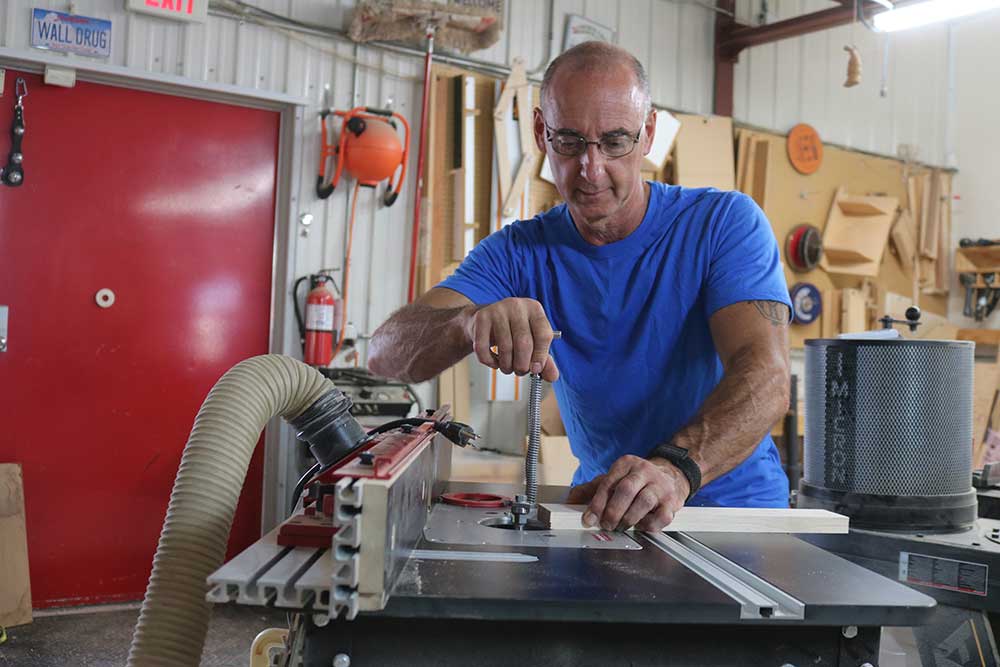
WWGOA LIVE! October 2019
George VondriskaDescription
Fall is the air. For many, that’s the beginning of the woodworking season. Hopefully tonight’s topics will help you with your fall/winter/spring woodworking plans.
1:45 How much should a joint stand proud?
3:50 End grain vs face grain turning
6:03 Tools for bowl turning
9:40 George’s shop wiring
11:55 Can a miter saw live outside?
12:15 Flattening twisted boards
16:00 Cauls on a panel glue up
18:10 Getting a table saw blade square
19:58 Best way to cut plexiglass
20:00 Rail to post for a bed
22:10 Gluing up a large flat panel
24:20 Making a box/stand for a TV
25:18 Kreg router lift questions
26:12 Catskills Mountain Maker Camp
28:00 Planer snipe
29:45 Support on a pocket hole jig
30:48 Lathe: Scraping vs shearing
32:20 Epoxy over shellac?
33:15 November LIVE Event: Jess Crow https://crowcreekdesignsak.com/
34:40 Routing far from a router table fence
37:40 Are router lifts and commercial tables worth the money?
38:50 Working from a hit or miss face
39:50 Routing with a low rpm set up
41:15 Track spacing on George’s bench
43:00 Starter set of CNC bits
44:20 Four way bar clamps
45:20 Using a small drum sander
48:00 Finding a local woodworking club
48:55 Good starter projects
50:05 Finding plans
50:40 Mortise in curved sections
52:00 Specific recommended tool brand
53:40 Materials for CNC
54:15 Applications for different glues
57:20 Cutting balsa wood for Christmas ornaments
58:20 Material for templates
59:00 Drill press table?
59:35 Upcoming scheduling
What gives me the official, and we're officially live. There are little bubbles on my phone. Maybe that's Sam. That's Sam telling me that we're live. So, here we are.
Welcome to the October WWGOA LIVE! First off, thanks to Titebond, where are they, there. For underwriting this and keeping everything free for you. There are a handful of questions already on the site here. So I'm gonna jump right in.
I'm not gonna dilly or dally. We'll jump right in for questions. And let's see what happens here. I'm gonna turn this just a little 'cause I'm gonna sit on the bench. So, here's what we have.
Paul is in Farmer's Branch, Texas. What a great name for a town, Farmer's Branch. I'm trying not to get distracted. I was recently in Texas. My kid was there at a military base and the phone was giving me directions and all the roads are FM something, FM 208.
And I neglected to ask on previous trips to Texas what FM is about, but the phone told me, farm to market. What a great name for a type of road 'cause that's what it really is, was back in the day, right? Farm to market. So FM something in Texas. Anyway, I have a question about laying out joints.
I think I know the answer but would like an answer from someone more knowledgeable. Good luck finding that person, Paul, but I guess I'll take a run at it. In making many joints, like dovetails, box and finger, through-mortise-and-tenon, the pieces are cut with the end of one or both parts left proud, and then they're cut or sanded smooth as a final step. In laying out the joints, how is the extra length for the proud of mount measured and figured into the layout? It depends.
If you're, it depends on the application. In many, let's say you're making a box. I don't know, to sit on a dresser or a table, dovetail joints or finger joints. So, if the end grain of each component is projecting past the face of the mate by a 32nd of an inch, and you later cut that off, and so you thought the box was gonna be six by nine but now it's five and 31 30 seconds. Or I guess it would be five and 15 sixteens.
Cause you take a 32nd off each end. I don't think that matters in a case where it's a box it's gonna be a drawer box that has to fit into a very specific opening, then you do have to accommodate that. So then in those cases you are gonna need to say this is how big it needs to be, finished, this is how much projection I'm allowing. And I, when I'm teaching like through dovetails on the band saw, I always just call it a fingernail catch. And in most applications, what that finite amount is, doesn't matter.
But like I said, if you're making something to size, and it has to be specifically sized, you're gonna need to accommodate that. So give it a hard number. And a 32nd of an inch would be fine. And then allow for that when you're sizing the stuff. Brian asks, what are the differences between turning a vessel end grain as opposed to side grain.
In other words, hollowing down the center of a log as opposed to cutting into the side. I'm thinking about cutting and methods of tooling. Well, as a general rule, when one turns bowls, you turn it through the side grain, or vessels, through the side grain not through ingrain. There are a couple of reasons for this. Long grain cuts easier than ingrain.
So lazy wood turner that I am, I'd prefer to cut long grain. More also just from a stability perspective, if when you're working with like, green wood, to turn it ingrain on, that vessel or bowl is gonna be more subject to doing hinky stuff as it dries, long grain bowl would. So as a general rule, we don't do ingrain stuff. Now that being said, I've got a bowl blank at the other end of the shop that is gonna be completely ingrained but I'm stabilizing it with Penta Crow to prevent it from doing hinky stuff once I start turning it into a bowl. Cutting methods, at the end of the day, you can still use your bowl gouges or your carbide chisels, or your scrapers, whatever tool you would use for a long grain bowl, you can use for an ingrain bowl, and you're gonna be okay.
And I think the other part was like ease of cutting or difficulty of cutting. Pretty much a wash there. Ingrain is gonna cut harder. I keep thinking of green wood cause that's primarily what I work with. If you're in kiln dried stuff, ease of use, ingrain will be harder to turn than long grain.
So don't worry about tooling. If you're in green wood, do worry about cracking 'cause ingrain is gonna crack more. And if it's kiln and dried stuff, ingrain will be harder, physically harder, than a long grain bowl. Andrew asks, what kind of tool do you recommend for gouging out a bowl, in terms of scrapers and gouges. Well let's, this is a good visual.
And let me, give me just a sec, to pull things together. Still here. Don't go away. It's the benefit to a wireless mic. Coming right back.
All right. Bowl gouges and bowl scrapers. Let me get one more thing. Hold please. Coming right back, hold please.
All right, here I come. Na, na, na, na, na. Okay. I, on bowls, probably 80% of the time, maybe 90% of the time, I do my work with, don't be rolly polly on me. Don't make me come over there.
I do my work with a bowl gouge. This is a bowl gouge. And then some people go a step further and call that a deep fluted bowl gouge. It looks a little like a spindle gouge, it is not. Do not try to do bowls with a spindle gouge.
So one choice, for shearing bowls is a deep fluted bowl gouge, that's my number one choice for doing bowl work. Alternatively, this is a high-speed steel, round nose scraper. More specifically, it's a one inch scraper, that's the width across the tip. Round 'cause it's round. There are scrapers in different shapes.
So scrapers, when I teach turning to entry-level students, everybody starts with a scraper. It's the easiest way to learn to turn, bowl turning or spindle turning is the scraping technique, but it doesn't provide as good a cut quality. So it's a good way to start, scrapers, but eventually you may wanna graduate to gouges. Now newer in the marketplace are tools like this. This is a carbide tip chisel.
For the most part, carbide tools are all about scraping technique. Some companies do make them in such a way that you can do some amount of shearing with the chisel as well, so, Rhino scrapers or carbide is a great place to start. The benefit to carbide is you don't have to learn to sharpen. And probably 90% of the battle of learning to turn is learning to sharpen, 'cause if your tools ain't sharp, they ain't gonna cut. And it's just gonna be a real struggle to get technique figured out.
So, start with the scraping technique. Once you get the hang of that, if you wanna graduate to the shearing technique, then it would be some form of bowl gouge or deep fluted bowl gouge. Stop it. It be a shame if they fell off 'cause they will land right on the tip, you know how that goes. How many power outlets did you add to the shop?
Where did you put the walls at the floor walls at mid height, oh, or ceiling? How many at 220 versus 110? Oh, I don't know. Long answer. Here's the thing.
I'm in this weird environment 'cause we do so much video in here. So when this place got wired, it was wired with video in mind. In fact I'm looking up 'cause there are, I do have outlets in the ceiling and they're color coded. There are outlets in the ceiling that are not on the same circuit as outlets down here, so that when a studio lights are plugged into them if I turn a tool on, you don't get the dimming effect on the light. I'm in a 3,200 square foot shop.
There are a metric simpling plank ton of outlets in here, cause I wired in a lot of outlets. On the walls, all my outlets, which I'm looking at, are four feet up. I don't have any at floor level. I do have outlets I put in the ceiling 'cause I'm a big fan of drop cords. I think I have four drop cords in here.
110 versus 220. I did that on an as-needed basis, or from when in here. I had, I don't know, maybe all I had was a 220 volt planer. Subsequently, I've got 220 volt CNCS, excuse me, a 220 jointer. So I've added 220 volt circuits, as needed, to accommodate those tools.
So I can do that here because everything is surface wired in conduit. So, adding later is not difficult to do. If you're behind walls, if you're in studs. you're gonna have to do a lot more planning to fit. That's the deal.
I would put wire in places where you don't think you're gonna need wire because it's gonna be a lot easier to have it in the wall while it's open than it is after things are closed up. Is it okay to a miter saw on stand outside during winter? If it's covered. Even covered I'd rather not have any tool, I mean, is winter means snow and sleet and rain and stuff, I would much rather not, I'd much rather not do that. Neil asks, what is your approach to flattening twisted boards?
Twisted sister. Let's do this. Let's do it, let's run tools, baby. Let me get, I don't know that I have a twisted board, but certainly I own a board. So let's do, hold please.
I had a piece of poplar earlier today. How about this one? It's such a poplar wood. All right, hang on. Hearing protection, what?
Hearing protection, what? All right. Properly flattening a board, you gotta start with face jointing. Face jointing has nothing to do with your lovely massage. It has to do with using a jointer, like this.
So the benefit, jointers are all about smooth, straight square. That's what jointers do. Square we don't care about, in this application. So when I lay this on here, this board's got a little bit of a cup in it and a little bit of a twist. So, when I put a little bit of down pressure on here, I'm not pushing down so hard that I'm taking the cup the twist out of it, I'm just resting on here, and then I'm gonna propel forward.
Jointers being the way they are, it's gonna make that face flat, kind of like this. That's what I got from moving fast, instead of, so the official ISOtunes thing is you twist them just a little bit, then put them in your ear, and I was being in a hurry. So, I just poked it in my ear. and then it fell out. Gotta do, gotta use tools the right way.
So on that first pass, you could probably hear, it cut then it wasn't cutting, then it cut again. That's 'cause it was bowed in the middle. Once we do a couple of passes, that face, I can tell on the cast iron now, is flat. Next step. This goes to the planer, with the jointed face down on the planer bed.
And we take material off the top that, what the planer excels at is getting those two faces parallel to each other. So twisted board, first step, face jointing, Second step, planer. Bob's your uncle. Na, na, na, na, na, na, na, na. All right.
Laurence says, correct secrets to clamp up using calls, using too much pressure in one direction I think would hinder pressure in the other. So yeah. So calls, let's say we're doing a panel, which I have just glued up, let me go get it. Here's a big flat panel, recently glued up. So I think what he's saying is, if I put calls across here to keep this flat, and then I squeeze those with F clamps or C clamps, if I push down too hard that way, my bar clamps or parallel jaw clamps are gonna have a hard time closing the joint this way.
If I close the joint this way first, and then come down with the calls, especially on a multi-piece glue up, I might not be able to push those pieces back down to level. So like a lot of things in life it's about compromise. You need to, what I would do is get the, I'd get everything setting on the bar clamps or the parallel jaw clamps, and then, get the calls in place and put a little bit of pressure on 'em. And you're gonna be able to tell, are those calls holding everything flat. You're gonna be able to overcome a fair bit of call pressure, with parallel jaw or bar clamp pressure this way.
So I'd get enough pressure on there to get flatness, from the calls, and then start to close the bar clamps and then maybe add a little more pressure to the calls and just keep going back and forth between the two until you're glued up. And honestly it doesn't take, I tell people in class all the time, if your knuckles are turning white while you're tightening clamps you're making stuff way too tight. It doesn't take much to draw good joint closed. So a little bit of pressure in each plane should do it for you. Franklin says, I bought a used table saw and when I cut with it, it's not square, how would I get it to cut square?
Get the owner's manual for it. Surprisingly, large number of owners manuals are available online. Find the owner's manual. See what they say about it. Cut square, it depends on what you mean by that, if you're talking about the blade perpendicular to the table, very frequently, there is the blade is on a trunnion system and that allows it to go to an angle, and then somewhere on that trunnion, there's a bolt that when you go to 45, and then you come back to 90, there's a bolt that tells the trunnion and when to stop.
So by dialing the bolt in, the blade can go further, by dialing it out, the blade stops earlier. So it could be that that bolt is not correctly positioned. You're just gonna have to find the owner's manual and, or poke around on your saw for where that bolt is and then get to it and adjusted accordingly. If you bought, I think he said he bought a used saw, the other thing before I adjust the bolt, I would look at, is it all clean under it? What I've seen sometimes is that what we've got is a bolt head going against the cast iron trunnion, and if a lot of sawdust builds up in there instead of the head of the bolt hitting the cast iron, it's hitting a pad of sawdust.
So if you angle it, clean the sawdust out of there, come back, maybe it'll be just right. So you've got a little bit of Sherlock Holmesiness to do there, but I would definitely start probably Googling owner's manual and then manufacturer name and model number of your saw and see if you can find an owner's manual for it. Paul asks, what's the best tool to cut plexiglass? Table saw, with a fine tooth blade. Best way to go.
Bob says, I made a bed, you've made your bed and now you'll sleep in it, Bud, And I want to connect the side rails to the head of the foot board, what type of die set do I need to use to put a thread in the post so I can screw the side rails into it. I'm afraid if I use screws that came with the bracket they would pull out after awhile. What kind of a die set? So I know, Marc Spagnuolo, Wood Whisperer, sells taps for cutting threads, internal threads, in wood. I don't know that that's I feel like this is a pretty small screw.
So one, Bob, go look at Spagnuolo's tap set, see if that's what you want. So look up Wood Whisperer, is Mark, and then, or Wood Whisperer tap and die set and that'll get you there. Google that. Or an alternative is to put thread inserts into the wood. And then you've got a metal, you've got a brass insert, with a internal machine thread on it, and the screws that you're putting in and out of that, are constantly going in and out of the insert rather than in and out of wood, and that'll stand up to the test of time.
I'm not sure in your application, tapping the wood, I'm reading this again. Yeah, I'm not sure threading the post is your best answer in this application. I think a threaded insert, which you can Google that, Rockler sells them, Woodcraft sells them. A threaded insert I think is the way to go. When clamping five by five pieces of wood together how do you keep them from bowing in the middle?
I've been using Bessey parallel clamps. Bessey parallel clamps are a great way to go. If they're still bowing, I would check your edges. If the edges, especially on a five foot panel, if the edges are just a tiny bit out of square, it's like you're making a barrel. So an approach to get help get away from that is when you're at the jointer, Let me get my board.
Wouldn't it actually be beneficial to have a couple of boards, see if we can get a visual here. If I'm gonna go to these two boards together, edge to edge, and even on narrow glue ups I do this all the time, and if this is my face, if this is my front face, then when I go to the jointer, I joint, let me do this, gotta have a better visual here. Need a pencil. So I'm gonna mark 'em. Here's my good face.
Here's my good face. When I joint this one, I'm gonna put the good face against the fence of the jointer, joint that edge. When I edge joint this one, I'm gonna put the back against the jointer. What happens with that is that if the fence on your jointer is just a little bit out of square, then by alternating which face is against the jointer we're creating, I never get it right, through either complimentary or supplementary angles. But the bottom line is, if I joint this edge at 89 and I joint this edge at 91, when they come together they're gonna make a flat glue up.
So if you're using good clamps, my next finger pointing on a bow would be your edges are not square. And a good workaround for that is to alternate which face goes against the fence when you're jointing, so that they compliment each other and stay flat. Kim says, I wanna make a small box for my somebody to elevate her TV that's on her dresser how would you make it? Oh I what tools do you, what kind of material, too many, there's so many variables, Kim. What I would do if I were you is, you know, check, you gotta, you know what tools you own.
And then Pinterest is a great place to start. And just look for designs. Once you have the designs, you can reverse engineer. If I owned nothing but a circ and biscuit jointer versus if I on a table saw on a dado head versus, so there are so many variables there. Blaine, how are you?
Todd World is in Houston, Texas, where I was last summer, doing a little teaching. Guest says I bought a Creed router table. I think maybe it's Kreg, is what he meant, Kreg router table, mounted my router in the Kreg lift, lift does not come to the top of the table, am I supposed to take off the bottom of the router to make it reach the top? Can you tell me what to do to raise the router to the top of the table and make it easier to mount the bits? I would call Kreg, cause I'm not, I've used the Kreg router table, I don't mean to sound snarky about it, but I've used one but I'm not like intimately familiar with how their lift works.
So I would, I'd just call Kreg's customer service and tell 'em that exact question and see what they say A.J. is in from Boston and says it looks like you had a great time in New York. Yes I did. I'll tell you what I'm gonna digress from answering questions, for a second, 'cause this was a really cool thing. I went to an event outside of Albany, New York called Catskills Mountain Maker Camp, and there's a reason why I'm talking about this.
So I taught CNC there for four days. Thanks to ShopBot, they're the ones who sent me out there. It was a great experience. And one of the amazing things is that most of the people that were there attending were in their thirties, maybe, maybe their forties, I was probably the oldest guy there. And so the reason I'm bringing this up is that a lot of times people are gnashing their teeth over no young people to pick a trade, woodworking welding, electricity, electronics, whatever it is, our hobby.
And it's not true. It's just that you don't necessarily see them in the, if you're my age, you don't necessarily see them in the places I normally go to. They, woodworking store cause they order all their stuff online. At this event, it was rampant with young people. And there was woodworking going on, bowl turning, there was a guy there making ax handles from scratch.
There were people with forges set up and they were forging steel, forging iron. It was, it was a really neat event and it was filthy with young people, in a really good way. So I'm just saying you look at Maker Spaces, there are a lot of young people coming in to what we do. And it's very, very, very neat to see. And I did have a blast.
Blaine says, question about my DeWalt planer. It makes a dent at both ends as I run it through. I didn't have a drum sander yet. My next , what do you suggest I do? So DeWalt planer, in category, we would call that a lunchbox planer, or bench top planer, depends on which DeWalt you have.
The 734 has a cutter head lock on it, if you use that while you're planing, it rigidified, it locks up the cutter head, so it can't do this and cause snipe, what you're calling, what you're calling a dent is called snipe. The 735 does not have, and doesn't need a cutter head lock. They've just, it's a more expensive planer, they've got a different system in there. If, for whatever reason, no matter what you do, cutter head lock or not, you're getting sniped, and for that. On Larger stationary planers, there are ways to correct that.
So one thing you can do, there are some common approaches to this. You cut your boards X longer than you need for your finished project 'cause you know you're gonna cut both ends off. If you can always lead and trail with scrap, the scrap leading your cut and trailing your cut, the snipe will happen in the scrap, it won't happen in your target board. So there's two things that you do. Snipe hunting.
On your Kreg pocket hole jig, is there a specific reason you didn't add support to either side of the jig to support the board so it stays flushed to the bottom of the board versus tipping. I, so my pocket hole jig, are you like seeing it hanging in the background, 'cause I think it is. Yeah, it's right there. So I think what's being asked is on this setup, why I don't have any outriggers out here. And the big reason is 99.9% of the time for me my jig is getting used like this.
Rarely if ever gets used like this. So I just, I don't need them. It's not a bad idea. And if you're doing, if you're doing pocket holes and edges, it would be a great idea to add that support. It's just not something I generally use pocket holes for.
Are they called pocket holes or screw pockets? I never know. Carl says for us novices explain shaving and shearing . Oh, maybe scraping and shearing, is that what you mean? So scraping, is if we have this as a lathe chisel and we're doing this spindle, the tool is gonna come in, generally, right on the center axis of the spindle or the bowl, and it's exactly like it sounds, we're scraping the wood fibers much the way you would scrape paint off the side of a house, so it's a very easy process to do.
The downside is, surface finish is okay, but not great. In a sheer cut, it's a whole different approach, and this is not a spindle, this is a bowl gouge, not a spindle gouge, but we can actually lay the bevel of the tool against the work. And it's more like the way a hand plane would remove shavings from the edge of a board rather than the way a paint scraper would remove paint from a surface. So in a shear, we're cutting the wood away, in a scrape, we're scraping the wood away. And that's like, intuitively too, that probably helps you understand the surface finish difference.
Steven is in Port Angeles. I don't know where that is. If I apply sealer such as shellac to oak, walnut, maple or any hardwood, could I then apply a two part epoxy over the shellac? I do not know. I would just, I would call the epoxy company whoever TotalBoat or whoever you got your epoxy from, give them a jingle, lay that all out, I'm just not familiar, with a relationship, compatibility relationship between epoxy and shellac.
Now I'm gonna do a promotion here, 'cause we're talking about epoxy. And I'm gonna mention this again at the end. A couple things, a month from now, like a month from today maybe not quite, I'll get the date. A month from now, the November live is gonna be different. We're gonna have a guest here in the shop.
Jess Crow is from Anchorage, Alaska, but she's gonna be in Wisconsin for a few days. So she's gonna be here for the live and she is gonna do nothing but talk about resin, epoxy, coloring, all the stuff that's related to that. She's got some amazingly beautiful techniques where she mixes resin and puts it on a board. And it you'd swear it's a real ocean wave that washed up on that board. Mirror smooth finishes.
It's a great opportunity. If you're interested in this resin category you need to be here, not in my shop, you need to be participating a month from now when Jess is here, 'cause we're gonna do nothing but resin for an hour. It's gonna be a blast. And she really knows her stuff. She really knows what she's talking about.
If you wanna see her work to get a feel for it, Crow Creek Designs is her business. She's got a webpage and she's Crow Creek designs on Instagram. You can check out what she does. But she'll be here, she will be here for the November live, and it's gonna be fun and interesting, and I am gonna learn a lot about resin. A.J.
says, Showed me how to use a special grind for Halloween, ingrain. Oh, so A.J.'s going back to the ingrain question, and he's got a link there, which is helpful, about sharpening tools specifically for ingrain cuts. Eli says, I wanna add an extension to the back of my very small router table so I can have the bit further from the fence. Is it safe to route that far from the fence? Maybe.
Depends on what you're doing. I mean, here's the thing, never get the work between the fence and an edge forming bit. So let's, I'm looking around to see if we have a clear path. We're actually doing a video shoot today and tomorrow. So I'll show you there's, there goes my panel, there's stuff everywhere.
So like, right there, that light is not normally here. And then if we go in this direction those crazy cool cameras are not my cameras. So let's see if we can find our way to the router table, there's a little bit of video shoot stuff over there, but I wanna make sure, as we talk about this, we understand where we're going. All right, I'm gonna tip you down a little bit. Ignore most of the mess in the background.
Here's what you should never, ever, ever, ever do, I'm unplugging my router. You never want the fence there and feeding the piece in between the fence and a bit, like this. So if that's why you're adding distance back here to do that, that's bad. Don't do that. If what you're trying to do is get more real estate, so you can put a straight cutting bit in the router table and cut dados 10 inches from the edge, as long as the piece you're working on is large enough to prevent it from spinning.
So this piece would be a really bad choice for doing that to 'cause it's gonna have a tendency to spin out, cause you're cutting it. If you're talking about large case pieces and you want that additional real estate to put dados in them, you're gonna be okay. Don't use that additional real estate for an edge forming cut, like this. That's very, very, very dangerous. Sam, can you look up the, I think I know the date of the November live when Jess is gonna be here, but I hate to say it and get it wrong.
Can you please look it up for me? Sam is great. Sam is the person behind the curtain who makes all this happen. Everybody needs to say thank you to Sam. Are commercial router tables and lifts worth the money?
Yeah. Maybe to me, maybe not to you, maybe to you, maybe not to me, it depends. A lot of people just like to make everything, whatever they can make in their shop, they like to make. So you could easily apply that to router tables and say, figure out what's best for me and make my own router table. Or you could say a commercially made one is worth every penny.
So it's just, it's more question of, is it worth it to you? I don't own a commer, I own, I have shop made cabinets under my router table, but I bought a router table top, fence, and lift, so to me, yes, it's worth it, but maybe that'd be different for you. Either the same question or a second question about cutting plexi, best way to cut plexi is a table saw. David says I have a tabletop jointer, not good for wide or long boards, so I have my lumberyard joint one face, paid 15 cents a board foot, but they only passed at once through. So entire face was not jointed.
Yeah, it's called hit or miss. First time I had ever had the yard do this. Can I use this space to plane the other face, or did I waste my money? if it's reasonably flat then, sure that could be, that could be your starter face that's then down on the planer. So reasonably flat, you know, it can't still look like a banana.
It's gotta be mostly flat. Dan says, my question is typical router runs. It runs a 10,000 RPM and seems to give satisfactory cuts. How do you think I should manage my routing at 10,000 RPM feed speed cut up? Go, it's like shaper versus router table, Shopsmith versus router table.
You think, you wanna think not in terms of RPM, but in cuts per minute. So when you have a two wing cutter, at 20,000 RPM, you're getting 40,000 cuts per minute. That's part of what gives it good cut quality. You take that same bit and run it at 10,000 RPM. It's gonna cut okay, but not great, 'cause you you're getting only 20,000 cuts per minute.
So you definitely have to lighten up your passes. And, and my Shopsmith experience goes way back. I was working for the company when they came out with the thing that lets you use your router table, like or let's use your Shopsmith like a shaper, really is what it did. And the RPM is really low on that. And shaper, what makes it work is when you use a three wing cutter, or four wing cutter at low RPM that pushes your cuts per minute back up.
So for you, to go back to the question, light passes, slow feed rates. What is the distance between the t tracks and bench dog holes on the bench you are sitting on? Yes, and yes. I don't know, I built it but that was a long time ago, but I own a thing. We can use this to see how long we've been here.
I think I'm very funny. Bench is an eight foot bench. Right there, track to track is 24 inches. So it's one foot in from the end, right? One foot, two foot, and then six more in between.
So yeah, they're one foot in from the end, two feet on center in between. The bench dog holes, I'll give you the number, but I'll give you a qualifier. In this case, the bench dog holes are six inches apart. When you do bench dog holes, though, see if you can see here, what this is really predicated upon is how far does your vice open? So the vice has a certain amount of travel here, and that trolls where you can put your bench dog holes.
If the bench dog holes are 12 inches apart, and this travel is only six, you're gonna run into scenarios where this won't grab your material, 'cause the holes are too far apart. So whatever, come on, whatever this is, this needs to be less than this to make sure, to make sure you can always grab your stock. 20 minutes to Eight, it's going good so far. James says, suggestions on first bits to get for my Shapeoko CNC, already have a quarter inch up cut that came with it. Well, whoops, who left that camera over there?
Where's Jenny? Jenny got a big girl job. Jenny got a great job. She's doing a wonderful, she's doing a wonderful job at her job. I'm very proud of the all three kiddos.
You probably want something for fly cutting. I have a two and a half inch diameter carbide insert cutter, I use for that. And then there's a lot of, it depends, if you wanna do signs, 60 degree V bit, is a wonderful thing for cutting letters. Larger, straight bits, I use a three-eights bit, a lot for when I'm cutting the outside of things to shape. So there's a lot of it depends on what you're gonna do, with your machine, but ball nose cutter is what you use if you're doing 3D work.
So a quarter inch ball nose would be a pretty common size for that. So a quarter-inch ball nose, three eights up cut spiral, and something for fly cutting, a larger diameter bit for fly cutting. And then you can keep going from there and be happy to spend your money. Ivan says when clamping edge to edge, why not use a four way equal pressure clamp? Oh, those ones where the, I used to own a couple of these.
Bars on the top, so as you squeeze from the end, they're also, it's acting as calls from the top and the bottom at the same time. Yeah, sure. Nothing wrong with that. Sometime back you did a video on impact driver drills and recommended we have both. I purchased a new drill and driver.
Cool. That's actually Paul Mayer, did that, did the research on that to the video and the article did a great job on it. I just purchased, purchased a Jet 1020 plus drum sander any tricks for getting best results, sandpaper, grit, feed speed? I don't, I've not used the Jet 1020. On my sander, I'm trying to think.
You know, my go-to grit for most of my work is 120, as my starting point. And I take stuff up, I end at 180, and then I random orbit sand from there. Feed speed, I'll tell you what I'm guilty of. I have SuperMax, a SuperMax product in my shop and it's variable speed. If I feed stuff too quickly, if I feed it too fast, it automatically slows itself down until it's at the right feed rate for that load.
So I'm basically guilty of running stuff fast all the time, if you go at a slower feed rate you're gonna get a better surface finish. It's kind of back to the same cuts per minute idea. That drum is turning at a fixed rate. So if you're passing your wood under it more slowly the sandpaper has more time to do its thing. So Lawrence goes on to say, I have both impact driver and drill.
I find the impact driver has tremendous torque, will often strip screw heads. Yep. Are there different type drivers for woodworkers or would it be my technique? You just have to be careful. If you, if you're, you know, a lot of times on an impact driver, I was just driving pocket screws today, and I won't necessarily use the impact driver until it bottoms out.
I'm kind of goosin' it. You know, I run it full bore until it gets, the head gets close to contact with the material and then I kinda to finish it so that I'm not snapping off a screw head or stripping it out, so. I'm trying to think, I don't think I have ever seen an impact driver with a clutch the way a drill has a clutch. So it's more about just being careful using it. Carl says eReplacementparts.com is good for owner's manual.
How do I find woodworkers in Springfield, MO. I would Google, like woodworking club, Woodworking Guild for your city. And then if there's a retail store, I can't think off the top of my head, if Woodcraft or Rockefeller has a store there, if you can find woodworking retail stores go to the store see if there's a bulletin board up, see if they have clubs or groups that meet in their store. I know here in the twin cities, Rockefeller has a CNC group that meets in their store. I don't know if they have other clubs or not.
But anyway, just use Google to start with and just Google woodworking clubs. And then also check in at retail stores to see. A good starting project for a beginning woodworker. It depends. Here's, here's the deal, with this.
And I, other people who do what I do, which is videos and articles and teach and that kind of stuff I've heard pretty much all of them provide this same answer, which is, I can't tell you, what's a good starter project for you. You need to tell you that. 'Cause if I say you should make this box and you have zero interest in owning that box that project is gonna stink for you to do. You're gonna hate it. What you need to do is look around at things that interest you, maybe you would like a case for a handgun, maybe you would like a box to put a special watch in, maybe you would like a, I don't know what, a cutting board.
So based on your needs and your wants, pick something that's important to you, and then you're gonna be invested in I wanna learn how to cut this joint, 'cause that's how the watch box goes together. I wanna learn how to flatten wood, 'cause that's what this cutting board needs, I wanna learn. So it will be way more compelling for you than for me to tell you. So I, every time I'm asked that question, which is frequent, I give that same answer. That's a good starting project.
New to woodworking, not comfortable making my own plans. Neither am I. Any recommendation for good inexpensive plans to make that Well, same answer, just keep looking around for things that are important to you and use those plans to make what you wanna make. So it's very parallel to what I just said. What's a good way to cut a mortise to us into the end of a lowering board.
I'm connecting a long style, to a curve doorframe section, where the drawing board, mortise and tenon, but I'm not sure how to cut a mortise in the ingrain of the curb section. I would cut it before you cut the curve, that'll make your life easiest, so you're working with square stock. And then I think that the common approach for loose tenon jointery, where you're cutting into the end of a board is to do that with a router, a plunge router, and you have to jig it all up. Everything has to be rock solid, so that when you go into that ingrain, ingrain is difficult to cut. If you're not jig solidly, it's gonna make the router bit jump around.
It's gonna be really bad, so. I would look for shop made jigs for loose tenon jointery. It wouldn't, and see what you find there. And plunge router would probably be a great way to go. Now, that being said, you could look at, I'm not sure if you're, Oh, you said it's draw board.
So it is traditional mortise and tenon. So yeah, I would lean toward a router but you're gonna have to make a shop made jig to support it. Timothy says, watching your videos, I see you use lots of different tools, do you have a specific favorite brand you'd recommend for tools, such as table saw, drill press, planer. Table saw, SawStop. That one's easy.
Save your pennies, get a SawStop if you can. It's a really, really, really, really really good saw, that also has a brake technology on it. And other stuff drill press and planer, tool tests are great. We, Woodworkers Guild, doesn't do tool tests, but Wood Magazine still does. I'm trying to think who else, Fine Woodworking, maybe.
But I would look for, generally when they do those tool tests, they'll say we wanna test all the jointers that cost $500 to $800. All the drill presses that cost $200 to $600, whatever it is, they pick a price point. So then you can match your budget to that tool test and see those are objective results that they're providing. And that's a great way to find the best tool in a category. Oh, back to the snipe, I put a small amount of pressure on the board, John says, at the end of the run through the DeWalt planer the stocks sniping most of the time.
So yeah, maybe a little uplift at the end. I'm planning on buying a CNC soon. Are there particular woods or other material you prefer to work with? Not anything in particular. Depends on what I'm doing.
Paint grade stuff, MDF is great. It's cheap and machines like a dream, but I've also cut plexiglass, brass, aluminum , building foam, maple, cherry, Walnut, all the usual suspects, suspects. So yeah, I don't have a favorite, It just depends on where you're going, and what you wanna do. Hello from Canada. When do you use CA glue versus contact, versus epoxy, versus white or yellow?
Wow, broad question. None of those have similar applications. Let's see, we have six minutes left. I'll give this a minute. Let me go back and hit on the glues.
Starting at the bottom of the list, white and yellow glue are gonna be for porous materials, like wood. Long-standing bonds, they're gonna hold up very, very well. Backing up, epoxy has gap filling. It's the only glue in this list that is gap filling. So if you have two materials that didn't quite come together, as well as they could have, epoxy can take care of that.
It's the only one here that is in fact gap filling. Epoxy is completely waterproof, so if it's gotta live outside, epoxy will resolve that. That being said, it's messy to work with, hard to clean up. Contact Cement is primarily only used for plastic laminate. Some people use it for veneering as well.
And it's a unique animal in that it gets applied to both surfaces and allowed to dry, then you put them together. Way different application than yellow glue or epoxy. CA, cyanoacrylate, the crazy glue of the woodworking world. Really good, 'cause it dries fast. It can fill voids to some extent.
I commonly use it to repair a little cracks and voids and issues I have in bowls I'm making. So, there you have it, big thing with CA glue is it sets up in a heartbeat. So it's a great, that instant bond is a very great thing. Yeah, so we'll go from there. Maybe that was even less than a minute.
Suggestions, set up a shared Google calendar. Yeah, maybe I can bounce that off of the powers that be. There are, you know, at the end of the day, I'm a content creator is I really am. And then there's a whole other, up side, and that's not what I mean, there's a whole office that does stuff like, managing that kind of idea, but it's a good idea. So Sam kicked in here, the November live where, Jess Crow, will be here all the way from Anchorage, 4,000 miles away, is November 7th, 7:00 PM be here or be square.
She's gonna talk resin the whole time, and she knows her stuff. Bob says, you're in Wisconsin, why on earth would a person be a Packer backer? I'm not, I never watched sports. I'll qualify that, if the rugby game came on TV, I would maybe watch it. But I, it's pretty safe to say never sit and watch sports.
John says, what would be the best use to cut blocks of balsa wood into shapes as Christmas ornaments. Scroll saw, probably would be good for that. Paul says, sound is cutting out. So. Yeah, so Sam says sometimes, it's when I'm moving around.
So the deal is I have a lav mic here and then there's a sender here. So maybe I need to be more gentle with the sender, so it doesn't do that. I will do that next time. All right, we're down to like the last waning minutes here. What would use, use, what would maybe you use, for a template for accuracy, vertical perfection and drill bit router bit mechanisms for bench dog holes in a new top.
I drilled these with a drill. So I use, if you wanna do it with a template, you, Baltic Birch plywood would be great. And that's a Baltic Birch multiply plywood is great for templates. DeWalt used to sell an impact driver with three speeds to control. Okay, our last question here.
I purchased a Shop Fox isolating drill press, do you have any brand preferences for drill press table? Ever use a drill press clamp? Woodpeckers drill press table is a very nice product. I own it. I haven't put it on my new drill press yet.
There's just a logistical thing with the way the handle comes around to move the table up and down. It bumps the aftermarket table, but it's a really cool product. Ever is a drill press clamp? Yep. For holding down big pieces, drill press clamp is great.
Okay, couple things. November 7th, we've talked about that, Jess Crow is gonna be here and she's gonna talk for an hour and be able to answer your questions and show you some really cool techniques. I'm sorry. A week from tomorrow, I will be in Hickory, North Carolina. That's the Klingspor Woodworking Extravaganza.
I've got a really neat demo set up for that event. I'm gonna make a cabinet. Working through all the vendor's booths to make that cabinet. So Klingspor Woodworking Extravaganza, a week from today, it's a two day event. Friday and Saturday, I believe that's the 25th and 26th of October in Hickory, North Carolina.
The week after that, Saturday, I'm gonna be at the Salem New Hampshire Rockefeller store, logs to lumber and check with the store for timing on that. I don't wanna give a time, 'cause I'm gonna get it wrong. Salem, New Hampshire. And then I think I'm actually done teaching on the road for a little bit. So thanks everybody for tuning in.
And we will see you November 7th for the resin extravaganza with Jess Crow. It's gonna be a lot of fun. See you later.
The man in Springfield MO ck wood turners of SW missouri for turning club, I am not aware of a woodworking club at this time.
What is the best way to cut out a cup holder in a cheese board / cutting board?
I'm 64 years old and just starting woodworking. Have already purchased a number of videos, sets. I'm excited...thank you for everything!!
What is a good way to cut a mortise into the end of a long board? I'm connecting a long stile to a curved door frame section with a draw-bore mortise and tenon but am not sure how to cut a mortise into the end grain of the curved section.
I have been trying to use the carbide tools for turning but it keeps catching. what might I be doing wrong? my regular turning tools don't catch as much.
What is the best tip for someone staring to use a jointer to take off the same amount of material off all along a surface?